Microtrace RF Substrates Manufacturer.Microtrace RF Substrates Manufacturer specializes in the production of high-performance RF substrates for advanced electronic applications. Their state-of-the-art materials ensure superior signal integrity and reliability, catering to industries such as telecommunications, aerospace, and defense. With a focus on innovation and quality, Microtrace delivers customized solutions to meet the specific needs of its global clientele, ensuring optimal performance and efficiency in critical systems.
As electronic devices become increasingly complex, Microtrace RF Substrates have attracted much attention as a key factor in high-performance PCB design. This article will deeply explore the importance and application of Microtrace RF Substrates in the PCB industry, analyze its outstanding performance in high-frequency signal transmission, low dielectric loss and excellent signal integrity, as well as its application in communications, radar, satellite communications, etc. wide range of applications in the field.
What are Microtrace RF Substrates?
Microtrace RF Substrates is a high-performance radio frequency substrate material. Its excellent electrical properties and signal transmission performance make it an indispensable key component in the modern electronic field. This substrate is manufactured using advanced micro-nano technology. Through precise process and material selection, it achieves stable signal transmission at high frequencies and is widely used in various radio frequency applications.
As a high-performance material, Microtrace RF Substrates have many compelling features. First, it has low dielectric loss, which can effectively reduce signal attenuation, thereby improving system sensitivity and performance. Secondly, Microtrace RF Substrates have excellent high-frequency performance and can achieve stable signal transmission in the microwave frequency band. They are suitable for various radio frequency and microwave applications, such as communications, radar, satellite communications, etc. In addition, Microtrace RF Substrates provide excellent signal integrity and noise rejection, helping to improve system reliability and performance.
The manufacturing process of Microtrace RF Substrates is key to their excellent performance. Through advanced micro-nano technology, the manufacturing process of Microtrace RF Substrates covers precise material selection, substrate preparation, metallization and micro-fabrication processes. Precise control of these processes ensures high quality and stability of substrates, thereby meeting stringent performance requirements.
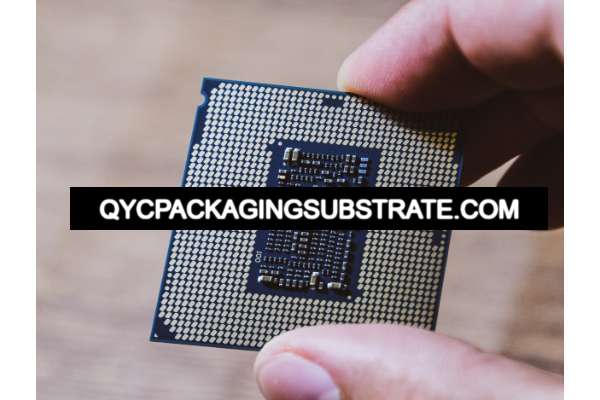
Microtrace RF Substrates Manufacturer
In practical applications, Microtrace RF Substrates are widely used in various radio frequency and microwave equipment. From communications systems to radio equipment, from radar systems to satellite communications, Microtrace RF Substrates play a key role. Its high performance and reliability make it the substrate material of choice for various RF and microwave applications, providing solid support for performance improvement and innovation in electronic devices.
In summary, Microtrace RF Substrates, as a high-performance radio frequency substrate material, is of great significance in the field of modern electronics. Through its excellent electrical characteristics and signal transmission performance, Microtrace RF Substrates will continue to promote the development of the PCB industry and provide critical support for the realization of various RF and microwave applications.
Microtrace RF Substrates design Reference Guide.
Microtrace RF Substrates is the core of high-performance PCB design, and its design process requires careful consideration of multiple key factors. The following is a reference guide for Microtrace RF Substrates designs to help you optimize your PCB design for optimal performance and reliability.
Electrical Characteristics Analysis
In the design process of Microtrace RF Substrates, electrical characteristics analysis needs to be performed first, including dielectric constant, dielectric loss, signal transmission speed, etc. Understanding the electrical properties of the substrate helps select appropriate materials and manufacturing processes to ensure design requirements are met.
RF characteristics optimization
Microtrace RF Substrates are mainly used for radio frequency and microwave applications, so the optimization of radio frequency characteristics needs to be considered during the design process. This includes signal transmission matching, impedance matching, signal integrity and noise suppression to ensure that the system can operate stably at high frequencies.
Material selection
Selecting the appropriate substrate material is critical to Microtrace RF Substrates design. Commonly used materials include ceramics, polyimides, and specialty fiberglass composites, each with specific electrical and mechanical properties that need to be selected based on specific application needs.
Thermal management
Thermal management is an important consideration in Microtrace RF Substrates design. In the case of high-frequency signal transmission and high power density, large amounts of heat may be generated, affecting the stability and reliability of the system. Therefore, effective heat dissipation measures, such as heat sinks, heat sinks, etc., need to be taken to ensure that the substrate operates stably within the operating temperature range.
Printed circuit board layout
In Microtrace RF Substrates design, the layout of the printed circuit board (PCB) has a huge impact on system performance and EMI/EMC (electromagnetic interference/compatibility). Reasonable layout can minimize signal crossover and electromagnetic interference, and improve the anti-interference ability and stability of the system.
Consider manufacturing processes
Finally, the feasibility and cost-effectiveness of the manufacturing process need to be considered in Microtrace RF Substrates design. A reasonable design should be compatible with existing manufacturing processes and enable efficient mass production to ensure product quality and stability.
In short, the design of Microtrace RF Substrates is a complex and critical process that requires comprehensive consideration of electrical characteristics, radio frequency characteristics, material selection, thermal management, layout and manufacturing processes. By following the above guidelines, you can optimize your PCB design, achieve optimal performance and reliability, and drive growth and innovation in electronic devices.
What material is used in Microtrace RF Substrates?
Microtrace RF Substrates utilize a range of high performance materials to ensure they perform exceptionally well in RF and microwave applications. Main materials include:
High frequency dielectric materials
Microtrace RF Substrates use special high-frequency dielectric materials with excellent dielectric properties and stable dielectric constant. These materials are usually zirconium oxide, boron nitride, fluoride, etc., which have low loss, high dielectric constant and excellent high-frequency performance, and can maintain stable signal transmission in the microwave frequency band.
Conductive metal layer
The surface of Microtrace RF Substrates is covered with a conductive metal layer, usually copper, silver or gold. These metal layers are used to create conductive paths and connectors to ensure good signal transmission and grounding performance. Metal layer selection and preparation processes are critical to the performance of Microtrace RF Substrates and require precise control to achieve high-quality electrical connections.
Substrate material
The substrate material of Microtrace RF Substrates usually uses high-strength, low dielectric loss substrate materials, such as polytetrafluoroethylene (PTFE), polyimide (PI), etc. These materials have excellent high temperature resistance and chemical stability, making them suitable for use in a variety of harsh working environments.
Ceramic material
In some high-temperature, high-frequency applications, Microtrace RF Substrates may use ceramic substrate materials, such as alumina ceramics or boron nitride ceramics. These materials have excellent high-temperature stability and dielectric properties, allowing them to maintain stable performance in extreme environments.
Polymer composite materials
Microtrace RF Substrates can also use polymer composite materials as substrate materials, such as polyimide glass cloth (FR4), polyimide glass fiber (G-10), polytetrafluoroethylene glass fiber (PTFE-Glass), etc. . These composites have good mechanical strength and chemical stability, making them suitable for most RF and microwave applications.
By carefully selecting and optimizing these materials, Microtrace RF Substrates are able to achieve excellent RF performance and stability, meeting the requirements of a variety of high-frequency circuits and microwave systems. The advantages of its material composition and preparation process make it one of the indispensable key components in modern electronic equipment.
What size are Microtrace RF Substrates?
Microtrace RF Substrates is a radio frequency substrate material that is crucial in PCB design, and its wide application in the electronics field makes it important to understand its size specifications. While Microtrace RF Substrates can vary in size depending on the requirements of a specific application, generally they come in a certain range of standard sizes.
The size of Microtrace RF Substrates is usually determined by their application area and required performance. In general, the size of these substrates can range from a few millimeters to tens of centimeters. For example, in mobile communication devices or wireless sensor networks, Microtrace RF Substrates may need to be very small in size to fit into compact device designs. In contrast, in radar systems or satellite communications equipment, these substrates may be larger to accommodate complex circuits and components.
Typically, the size of Microtrace RF Substrates is limited by the manufacturing process, as substrate consistency and stability need to be taken into consideration during the manufacturing process. However, as manufacturing technology continues to advance, more and more manufacturers are able to provide customized sizes of Microtrace RF Substrates to meet the specific needs of different customers.
In addition to length and width, the thickness of Microtrace RF Substrates is also critical. The thickness of the substrate directly affects its electrical properties and mechanical stability and therefore must be precisely controlled according to the requirements of the specific application. Typically, the thickness of Microtrace RF Substrates can vary from tens to hundreds of microns, depending on the required dielectric properties and mechanical strength.
Overall, Microtrace RF Substrates are available in a wide range of sizes and can be customized to meet the requirements of a specific application. Whether used in mobile communications equipment, radar systems or satellite communications equipment, Microtrace RF Substrates provide superior performance and reliability, becoming a key factor in achieving high-performance PCB designs.
The Manufacturer Process of Microtrace RF Substrates.
The manufacturing process of Microtrace RF Substrates uses advanced micro-nano technology, which is a key link in achieving high-performance PCB design. This process involves multiple precision steps to ensure the substrate maintains consistent performance and reliability in high frequency and microwave applications.
First, the manufacturing of Microtrace RF Substrates starts with material selection. For different application requirements, it is crucial to select high-quality substrate materials. High-performance dielectric materials such as ceramics, polyimides, and special polymer composites are typically used. These materials have excellent dielectric properties and thermal stability, enabling stable signal transmission at high frequencies.
Next is the preparation process of the substrate. During the preparation process, it is necessary to ensure that the flatness and surface roughness of the substrate surface meet the design requirements. Through precise machining and polishing processes, the surface of the substrate is smooth and uniform, which is conducive to subsequent metallization and micro-processing.
Metalization is one of the key steps in the manufacturing process of Microtrace RF Substrates. By coating conductive materials, such as copper, silver or gold, on the surface of the substrate, a conductive layer is formed to provide good conductive properties for circuit connections. This process requires highly precise control to ensure that the conductive layer has a uniform thickness, a smooth surface, and good adhesion to the substrate material.
Micromachining is the final step in the manufacturing process of Microtrace RF Substrates. In this step, advanced micro-nano processing technology is used to precisely process and pattern the conductive layer to realize the wiring of the circuit and the installation of electronic components. This includes chemical etching, photolithography, thin film deposition and other processes to ensure the accuracy and stability of circuit connections.
Through the above precision manufacturing process, Microtrace RF Substrates ensures the high quality and stability of the substrate and meets strict performance requirements. Its excellent electrical properties and signal transmission performance make it the substrate material of choice for various RF and microwave applications. As technology continues to advance, Microtrace RF Substrates will continue to promote the development of the PCB industry and provide solid support for performance improvement and innovation in electronic devices.
The Application area of Microtrace RF Substrates.
Microtrace RF Substrates is an excellent radio frequency substrate material that has been widely used in communications, radio, radar, satellite communications, wireless sensor networks and other fields. Its superior performance and reliability make it the substrate material of choice for a variety of RF and microwave devices.
In the field of communications, Microtrace RF Substrates are widely used in wireless communication equipment, such as mobile phones, wireless routers, base stations and satellite communication systems. Its excellent electrical characteristics and signal transmission performance ensure the stability and reliability of communication equipment, enabling it to achieve efficient data transmission in different communication environments.
In the radio field, Microtrace RF Substrates are used to design and manufacture various types of RF circuits and microwave systems, including radios, televisions, radars and antennas. Its low loss and high frequency performance ensure the excellent performance of radio equipment, enabling it to maintain stable operation in complex electromagnetic environments.
In the field of radar, Microtrace RF Substrates are used in the design and manufacture of various types of radar systems, including civilian and military radars. Its excellent signal integrity and noise suppression capabilities ensure the high performance and reliability of the radar system, enabling it to accurately detect and track targets.
In the field of satellite communications, Microtrace RF Substrates are used to manufacture radio frequency modules and antenna systems for satellite communications equipment. Its high performance and reliability ensure that satellite communication equipment achieves stable communication connections in different satellite orbits and communication frequency bands, providing support for data transmission worldwide.
In the field of wireless sensor networks, Microtrace RF Substrates are widely used in the design and manufacture of various types of wireless sensor nodes and data acquisition systems. Its excellent electrical characteristics and signal transmission performance enable reliable data transmission and remote monitoring under complex environmental conditions, providing support for smart cities, smart transportation, smart agriculture and other fields.
In short, Microtrace RF Substrates has become the preferred substrate material for various radio frequency and microwave equipment due to its excellent performance and reliability, providing important support for the development and innovation of modern electronic technology.
What are the advantages of Microtrace RF Substrates?
Microtrace RF Substrates is a high-performance radio frequency substrate material whose unique advantages make it ideal for designing high-frequency circuits and microwave systems.
First, Microtrace RF Substrates feature low dielectric loss. Due to the optimization of its material structure and manufacturing process, this substrate can reduce energy loss during signal transmission, thereby reducing signal attenuation. Low dielectric loss can not only improve the sensitivity and performance of the system, but also extend the distance of signal transmission, making it excellent in applications such as long-distance communication and high-speed data transmission.
Second, Microtrace RF Substrates have excellent high-frequency performance. In high-frequency environments, the stability and reliability of signal transmission are crucial. Microtrace RF Substrates, with its excellent electrical characteristics, achieves stable signal transmission in the high frequency range and is not susceptible to external interference. This makes it widely used in RF and microwave applications, including wireless communications, radar systems, satellite communications and more.
In addition, Microtrace RF Substrates also have excellent signal integrity and noise suppression capabilities. Through precise material selection and manufacturing processes, this substrate can effectively suppress noise and interference generated during signal transmission, ensuring the purity and stability of the signal. Excellent signal integrity can not only improve the reliability of the system, but also reduce the bit error rate and improve the accuracy and stability of data transmission.
In summary, Microtrace RF Substrates are an ideal choice for designing high-performance PCBs due to their low dielectric loss, high frequency performance and excellent signal integrity. In the ever-evolving electronics industry, Microtrace RF Substrates will continue to play an important role in promoting the advancement of radio frequency and microwave technologies and providing key support for performance improvement and innovation in electronic devices.
FAQ
What are the advantages of Microtrace RF Substrates over traditional substrate materials?
Microtrace RF Substrates have excellent electrical characteristics and signal transmission performance. Compared with traditional substrate materials, they have lower dielectric loss, higher dielectric constant and more stable high-frequency performance. This enables it to achieve better performance when designing high-frequency circuits and microwave systems.
What RF and microwave applications are Microtrace RF Substrates suitable for?
Microtrace RF Substrates are widely used in communications, radio, radar, satellite communications, wireless sensor networks and other fields. It can be used to manufacture RF and microwave equipment such as antennas, RF filters, power amplifiers, and microwave integrated circuits.
What is the manufacturing process of Microtrace RF Substrates?
The manufacturing process of Microtrace RF Substrates uses advanced micro-nano technology, including precise material selection, substrate preparation, metallization and microfabrication processes. During the manufacturing process, process parameters and environmental conditions need to be strictly controlled to ensure the high quality and stability of the substrate.
Microtrace RF Substrates What issues should we pay attention to when designing high-frequency circuits?
When designing high-frequency circuits, special attention needs to be paid to issues such as signal integrity, matching network design, and electromagnetic interference suppression. In addition, the thermal conductivity properties and heat dissipation design of the substrate material also need to be considered to ensure that the system can maintain stable performance under high-frequency operation.