Microwave/Microtrace PCB Manufacturer. Advanced high speed and high frequency material PCB, we offer Microwave/Microtrace PCB from 2 layer to 50 layers.
In today’s digital era, PCB (Printed Circuit Board) has become the core component of almost all electronic devices. In terms of wireless communications, radio frequency technology and high-frequency microwave applications, the development of Microwave/Microtrace PCB manufacturing technology is particularly important. This article will give you an in-depth understanding of PCB definition, design, materials, manufacturing processes, application areas, advantages, and answers to your frequently asked questions.
What is Microwave/Microtrace PCB?
Microwave/Microtrace PCB is a printed circuit board (PCB) designed for high-frequency microwave applications. Compared with traditional PCBs, microwave/Microtrace PCBs are more stringent in design and manufacturing to ensure stable and reliable performance in high-frequency microwave environments.
First, a Microwave/Microtrace PCB is a basic component that connects electronic components together. It secures electronic components to an insulating plate through a series of conductive pathways. These conductive paths usually use high-precision circuit design to ensure the stability and accuracy of signal transmission in high-frequency microwave environments.
Microwave/Microtrace PCB manufacturing technology has high precision and requirements. During the manufacturing process, special high-frequency dielectric materials such as polytetrafluoroethylene (PTFE) need to be used to ensure low loss and stability in high-frequency microwave environments. In addition, chemical processing, imaging technology and processing equipment in the manufacturing process require high precision and specialization.
In terms of design, microwave/Microtrace PCB needs to take into account the particularities of high-frequency microwave signals. Cabling, layout, and impedance matching all need to be optimized based on specific application requirements to ensure performance in high-frequency microwave environments.
Microwave/Microtrace PCBs are widely used in many high-frequency microwave applications, including communications, radar, satellites, and medical equipment. Their superior performance makes them the first choice for these critical applications.
In summary, Microwave/Microtrace PCB is a printed circuit board designed specifically for high-frequency microwave applications, with strict design and manufacturing requirements to ensure stable, reliable performance in high-frequency microwave environments.
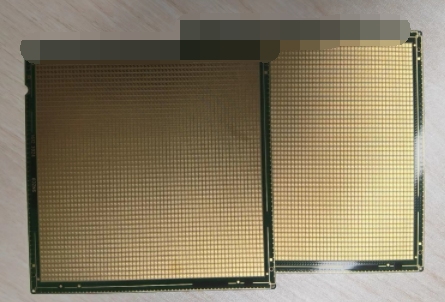
Microwave/Microtrace PCB
Microwave/Microtrace PCB design Reference Guide.
The key to Microwave/Microtrace PCB manufacturing is design. In high-frequency microwave applications, proper design is key to ensuring stable signal transmission and excellent impedance matching. From wiring to layout, the particularities of microwave and high-frequency signals need to be taken into consideration. Here are some important design guidelines to help you succeed in the design process.
High frequency signal transmission line design
When designing high-frequency signal transmission lines, special attention needs to be paid to the length, width and shape of the signal transmission path. In order to reduce the loss and crosstalk of transmission lines, the transmission path should be shortened as much as possible and the continuity and uniformity of the path should be maintained. In addition, choosing the appropriate material and plate thickness is also an important factor in ensuring signal transmission quality.
Impedance matching
In Microwave/Microtrace PCB design, impedance matching is critical. Good impedance matching can ensure the stability and reliability of signals during transmission. With proper wiring and path design, optimal impedance matching can be achieved. In addition, verification of impedance matching using simulation tools and test methods is also an essential step.
Signal layer layout
During the PCB layout process, the layout of the signal layers should be reasonably arranged to minimize interference and crosstalk between signals. In high-frequency microwave applications, the layout of the signal layer must take into account the speed and frequency of signal transmission to avoid signal path crossover and mutual interference. By using appropriate interlayer stacking and lead layout, the mutual influence between signal layers can be effectively reduced.
Ground wire design
Good ground design is critical to Microwave/Microtrace PCB performance. During the PCB design process, the layout and connection method of the ground wire should be fully considered to ensure the shortest distance and minimum resistance between the ground wire and the signal wire. By adopting distributed ground wire design and good grounding planning, crosstalk and interference in ground loops can be effectively reduced.
Simulation and testing
After the design is completed, simulation and testing must be performed to verify the performance and reliability of the design. By using professional simulation tools and test equipment, the signal transmission characteristics, impedance matching and interference conditions of the PCB can be comprehensively analyzed and evaluated. By continuously optimizing and adjusting the design, you can ensure that the final PCB design meets the requirements of high-frequency microwave applications.
What material is used in Microwave/Microtrace PCB?
The materials used in the manufacture of Microwave/Microtrace PCBs are critical as these materials directly affect the performance and stability of the PCB. In high-frequency microwave applications, choosing the right material is crucial to ensure the stability of signal transmission.
First, high-frequency dielectric materials are one of the key components in Microwave/Microtrace PCB manufacturing. Among them, PTFE (polytetrafluoroethylene) is a commonly used high-frequency dielectric material that is favored for its low dielectric constant and low loss. PTFE has excellent insulation properties, allowing it to maintain stable signal transmission in high-frequency environments, while also effectively reducing signal loss.
Secondly, FR-4 is another common PCB material that is also widely used in the manufacturing of Microwave/Microtrace PCBs. FR-4 material has good mechanical and thermal properties and is suitable for general electronic applications. However, in high-frequency microwave applications, the performance of FR-4 may not be sufficient, so it often needs to be optimized in combination with other high-frequency dielectric materials.
Additionally, special conductive materials are an integral part of Microwave/Microtrace PCB manufacturing. These conductive materials usually have excellent conductive properties and stability, ensuring efficient signal transmission in PCBs. In high-frequency microwave applications, the selection of conductive materials should take into account their impedance matching and signal transmission characteristics in high-frequency environments.
In general, the materials used in Microwave/Microtrace PCB manufacturing include high-frequency dielectric materials such as PTFE and FR-4, as well as special conductive materials. These materials have excellent properties to ensure stable performance and low loss of PCBs in high-frequency microwave environments. By selecting appropriate materials and combining professional design and manufacturing technology, high-performance, high-reliability Microwave/Microtrace PCB manufacturing can be achieved to meet the needs of various high-frequency microwave applications.
What size are Microwave/Microtrace PCB?
Microwave/Microtrace PCB dimensions often depend on the needs of the specific application. Microwave/Microtrace PCB manufacturing technology provides high flexibility in design and can realize complex circuit and tiny size designs. Compared with traditional PCB manufacturing technology, Microwave/Microtrace PCB manufacturing technology is more suitable for applications requiring high-density layout and high performance.
One of the keys to Microwave/Microtrace PCB manufacturing technology is its ability to achieve micro-sized designs. Since high-frequency microwave applications often require higher integration and more compact designs, Microwave/Microtrace PCBs can meet these requirements. They enable smaller line widths and spacing, as well as higher line density, enabling more functionality in a limited space.
In actual applications, Microwave/Microtrace PCB dimensions can vary significantly. Some applications may require a very small PCB to fit within a tight device interior, while other applications may require a larger PCB size to accommodate more components or connectors. Whether small or large, Microwave/Microtrace PCBs can be custom designed to meet specific needs to ensure optimal performance and fit.
In addition, Microwave/Microtrace PCB manufacturing technology also enables multi-layer designs, further increasing PCB density and performance. By arranging wiring and components on multiple levels, more complex functions can be implemented and signal transmission and power management can be isolated, thereby improving overall system stability and reliability.
Overall, Microwave/Microtrace PCB manufacturing technology can meet a variety of size requirements, from tiny to larger sizes, and designs of all complexity. Whether you are pursuing high-performance, high-density micro devices, or systems requiring larger size and more complex functions, Microwave/Microtrace PCB can provide flexible solutions to meet the needs of different applications.
The Manufacturer Process of Microwave/Microtrace PCB.
The manufacturing process of Microwave/Microtrace PCB is a highly complex and precise project, involving the coordination of multiple links and professional technologies. First, the process begins with the design phase, where engineers design the board layout, routing, and device placement based on specific application needs and performance requirements. At this stage, the particularities of microwave and high-frequency signals need to be considered in depth to ensure the stability of signal transmission and the accuracy of impedance matching.
Next comes one of the key steps in the manufacturing process, chemical processing. This step mainly involves the precise processing of PCB materials to ensure the quality and performance of the board. In Microwave/Microtrace PCB manufacturing, commonly used high-frequency dielectric materials such as PTFE require special chemical treatment to ensure their stability and reliability in high-frequency environments. In addition, chemical processing also includes the preparation and surface treatment of conductive layers to improve the conductivity and corrosion resistance of circuit boards.
After chemical processing is completed, imaging technology becomes another important link in the manufacturing process. Imaging technology is mainly used for pattern preparation and processing control of PCB, including processes such as photolithography and etching. Through imaging technology, engineers can achieve high-precision processing of PCB wiring, circuits and devices to ensure that the geometry and size of the circuit board meet the design requirements.
Finally, the final step in the manufacturing process is final machining and assembly using high-precision machining equipment. At this stage, the PCB will be cut to final size and undergo necessary surface treatment and finished product inspection. Through strict quality control and professional technical support, it is ensured that Microwave/Microtrace PCB can meet the highest quality standards and performance requirements in every aspect of the manufacturing process.
To sum up, the manufacturing process of Microwave/Microtrace PCB is a complex project that combines chemical processing, imaging technology and high-precision processing equipment. Through strict quality control and professional technical support, we ensure that every aspect of PCB from design to finished product can meet high standards of quality and performance requirements.
The Application area of Microwave/Microtrace PCB.
Microwave/Microtrace PCB manufacturing technology is widely used across many fields, and its high-frequency characteristics and stability provide excellent solutions for many critical applications.
In the field of communications, Microwave/Microtrace PCB is widely used in the construction of wireless communications infrastructure. Whether it is a mobile communication base station, communication satellite or microwave communication equipment, high-performance PCB is required to ensure the stability and reliability of signal transmission. The excellent characteristics of Microwave/Microtrace PCB enable it to cope with complex communication environments and provide users with a high-speed and efficient communication experience.
Radar technology is another key area in which Microwave/Microtrace PCBs play a vital role. Radar systems have extremely high requirements for signal processing and analysis, and the high-frequency characteristics and low transmission loss of Microwave/Microtrace PCB ensure the accuracy and sensitivity of the radar system. From military defense to weather monitoring, radar technology plays an irreplaceable role in various fields, and the application of Microwave/Microtrace PCB provides a solid foundation for it.
Satellite communications are an important part of modern communications technology, and Microwave/Microtrace PCBs play a key role in satellite systems. Satellite communication systems need to withstand extreme environmental conditions, and the high reliability and stable performance of Microwave/Microtrace PCBs make them ideal for satellite systems. Whether it is an earth observation satellite or a communication satellite, it is inseparable from the support of high-performance PCB technology.
The medical equipment industry is also one of the important application areas of Microwave/Microtrace PCB. From medical imaging equipment to life support systems, modern medical equipment increasingly requires high-precision, high-reliability electronic systems. The high-frequency characteristics and stable performance of Microwave/Microtrace PCB ensure the accuracy and reliability of medical equipment during diagnosis and treatment, providing strong technical support for medical staff.
To sum up, the wide application of Microwave/Microtrace PCB manufacturing technology in communications, radar, satellites, medical equipment and other fields demonstrates its important position and irreplaceable role in the field of high-frequency microwave technology. With the continuous development and innovation of technology, Microwave/Microtrace PCB will continue to provide strong support and power for the development of various industries.
What are the advantages of Microwave/Microtrace PCB?
Microwave/Microtrace PCB manufacturing technology has many advantages over traditional circuit boards, which make it outstanding in the high-frequency microwave field.
First, Microwave/Microtrace PCBs have lower transmission losses. In the process of high-frequency microwave signal transmission, transmission loss is an important consideration. Microwave/Microtrace PCB uses high-frequency dielectric materials and precise design and manufacturing processes to effectively reduce energy loss during signal transmission, thereby ensuring signal stability and reliability.
Secondly, Microwave/Microtrace PCB has better impedance matching capabilities. In the field of high-frequency microwaves, impedance matching has a particularly important impact on signal transmission. Microwave/Microtrace PCB manufacturing technology enables more precise impedance control, ensuring signals are well matched between different components, thereby improving system performance and efficiency.
Additionally, Microwave/Microtrace PCBs have higher frequency response. High frequency microwave applications require fast and accurate response to frequency changes, and Microwave/Microtrace PCBs are designed and manufactured to meet this need. Its superior frequency response characteristics make it widely used in wireless communications, radar, satellite and other fields.
Finally, Microwave/Microtrace PCBs offer greater reliability. High-frequency microwave systems have extremely high requirements on the stability and reliability of PCBs. Any small fault may lead to system performance degradation or even complete failure. Microwave/Microtrace PCB manufacturing technology uses high-quality materials and strict manufacturing processes to ensure the stability and reliability of the PCB, allowing it to operate stably for a long time in harsh environments.
To sum up, Microwave/Microtrace PCB manufacturing technology has lower transmission loss, better impedance matching, higher frequency response and higher reliability than traditional circuit boards. These advantages make it the first choice in the high-frequency microwave field, providing electronic equipment manufacturers with more reliable and high-performance solutions.
FAQ
What is the design process for Microwave/Microtrace PCB?
The design process of Microwave/Microtrace PCB is different from traditional PCB and requires more professional design skills and tool support. The design process usually includes circuit design, layout design, wiring design, simulation and verification. During the design process, factors such as the transmission characteristics of high-frequency signals, impedance matching, and electromagnetic compatibility need to be taken into consideration to ensure the stability and reliability of the design. At the same time, it is necessary to work closely with the manufacturer to understand its process capabilities and requirements to ensure the manufacturability and producibility of the design.
What frequency ranges are Microwave/Microtrace PCBs suitable for?
Microwave/Microtrace PCBs are designed for high frequency microwave applications and are suitable for a wide frequency range. Typically, they can cover frequency ranges from a few hundred megahertz (MHz) to tens of gigahertz (GHz). This makes them widely used in wireless communications, radar, satellite communications and other fields.
What is the manufacturing lead time for Microwave/Microtrace PCB?
Microwave/Microtrace PCB manufacturing cycle times vary based on design and requirements. Generally speaking, it usually takes a few days to a few weeks from design confirmation to delivery of the finished product. During this time, multiple aspects such as design review, sample production, process debugging, and production need to be considered to ensure the quality and performance of the final product.
How important is impedance matching for Microwave/Microtrace PCBs?
Impedance matching is critical in Microwave/Microtrace PCB design. Since high-frequency microwave signals have more stringent requirements for circuit boards, good impedance matching can ensure stable signal transmission and minimal signal loss. Therefore, impedance matching needs to be considered during the design stage and corresponding measures must be taken to optimize the performance of the circuit board.