Military circuit board Manufacturer. High speed and high frequency material PCBs, and Military packaging substrate Manufacturer. Advanced production process.
In the field of modern warfare and defense systems, the role of military circuit boards is crucial. These complex electronic components are the basis for advanced weapons, communications systems, and surveillance equipment used by armed forces around the world. In this comprehensive guide, we dive into the complexities of military circuit board manufacturing, revealing the processes, materials, and key considerations that shape this critical aspect of military technology.
What is a military circuit board?
Military circuit boards, referred to as PCB (Printed Circuit Board), play a vital role in modern warfare and national defense systems. They are electronic devices specifically designed for military applications that integrate individual functional modules onto a single circuit board by printing circuits, connectors and other electronic components on the surface. This integrated design enables military circuit boards to operate stably and reliably in extreme environments while providing high performance and efficiency.
In the modern military field, military circuit boards have a wide range of applications. First, they are core components of advanced weapons systems. For example, weapons platforms such as missiles, fighter jets, tanks, and ships rely on a variety of complex electronic systems for control, navigation, and communication. Military circuit boards play a key role in these systems, ensuring efficient connection and coordination between various sensors, control devices and weapon systems.
Secondly, military circuit boards are also an important part of communication systems. Modern militaries rely on efficient communications networks for command, control, and intelligence exchange. Military circuit boards play a key role in communication equipment, ensuring data transmission speed, stability and security, while adapting to various complex communication environments and conditions.
In addition, military circuit boards are also widely used in surveillance and intelligence collection equipment. The acquisition and analysis of military intelligence is critical to formulating strategies and taking action, and modern surveillance equipment and intelligence collection systems rely on advanced electronic technology to track, identify and analyze targets. Military circuit boards provide efficient and reliable electronic support for these surveillance devices by integrating components such as various sensors, signal processors, and data storage.
To sum up, military circuit boards play an irreplaceable role in the modern military field. They are not only core components of advanced weapons, communication systems and surveillance equipment, but also an important guarantee for national security and national defense interests. Therefore, the design, manufacturing and application of military circuit boards must be extremely careful and professional to ensure their reliability, stability and performance under various extreme conditions.
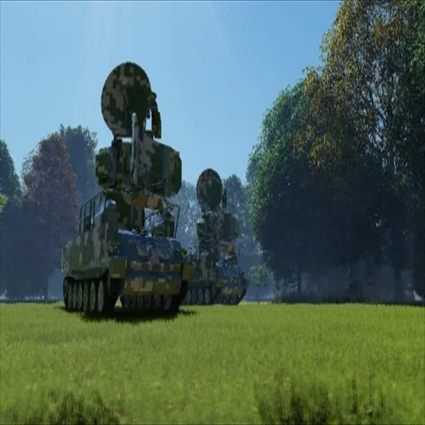
Military circuit board
What is the design of military circuit boards?
The design of military circuit boards is a complex and sophisticated process that requires multiple steps and the use of advanced technologies to ensure that the stringent requirements of military applications are met. Below we’ll cover the general steps for designing a military circuit board and how to ensure it meets military standards during the design process.
First, the process of designing a military circuit board usually begins with requirements analysis and specification definition. At this stage, the design team works with the military or related agencies to clarify key information such as the circuit board’s functional requirements, performance indicators, and working environment conditions. This information will provide important guidance for subsequent design work.
Next, the design team will design the circuit schematic. At this stage, the designer will draw a schematic diagram of the circuit based on the requirements and specifications, and determine the structure, functional modules, and connection relationships of each component of the circuit. This step requires designers to have solid circuit knowledge and the ability to skillfully use relevant design software.
This is followed by PCB layout design. At this stage, the designer will design the PCB layout based on the circuit schematic diagram and determine the location and wiring path of each component on the circuit board. In layout design, designers need to consider factors such as the size, layering, heat dissipation, and signal transmission of the circuit board to ensure the performance and reliability of the circuit board.
After completing the PCB layout design, the design team will conduct the wiring design of the circuit board. At this stage, designers will draw specific wiring paths based on the layout design, connect various components, and plan the signal layer and power layer. The wiring design needs to consider requirements such as signal integrity, electromagnetic compatibility, and the EMC (electromagnetic compatibility) characteristics of the circuit board.
Finally, the design team will conduct board simulation and verification. At this stage, designers will use simulation tools to perform performance analysis and verification of the designed circuit board to ensure that it meets the stringent requirements of military applications. At the same time, the design team will also conduct prototype production and testing, and conduct actual verification and debugging of the circuit board to further improve its performance and reliability.
During the design process, the design team needs to pay close attention to military standards and specifications, such as MIL-STD-810G and MIL-PRF-31032, etc., to ensure that the circuit board design meets the requirements of the military. At the same time, the design team also needs to maintain close communication with the military or relevant agencies to understand and adapt to changes in their needs in a timely manner to ensure that the designed circuit boards can achieve the expected results in actual applications.
To sum up, designing military circuit boards is a complex and meticulous process. It requires the design team to have solid circuit knowledge and technical capabilities, and to work closely with the military or related agencies to ensure that the circuit boards can meet the strict requirements of military applications. Require.
What is the manufacturing process of military circuit boards?
The manufacturing of military circuit boards is a complex and sophisticated process that requires multiple critical steps to ensure that the final product meets strict quality and performance standards. The following are the main manufacturing steps from raw material selection to final inspection:
Raw material selection: The first step in manufacturing military circuit boards is choosing the right raw materials. Commonly used substrate materials include FR-4 fiberglass reinforced epoxy, polyimide (PI), and polytetrafluoroethylene (PTFE). These materials must have high temperature resistance, corrosion resistance and mechanical strength to meet the harsh environmental requirements of military applications.
Circuit board design: After determining the raw materials, the manufacturer will carry out circuit board design. This involves using computer-aided design (CAD) software to convert the circuit layout, component placement, and wiring paths into a digital format. During the design process, factors such as signal integrity, electrical performance, and thermal management need to be considered.
Board Layer Overlay: For complex military circuit boards, a multi-layer board design may be required. The lamination process involves laminating multiple circuit boards together and using adhesive or prepreg coating to hold them together. This design increases board density and performance and reduces electromagnetic interference.
Printed Circuit: After completing the design, the circuit diagram of the circuit board will be transferred to the substrate. This is typically accomplished by printing a conductive material, such as copper, onto the surface of the substrate. Printed circuits are usually defined by chemical etching or mechanical milling.
Drilling: After printing the circuit, holes must be drilled in the appropriate locations to mount the components. Drilling is usually done with a CNC drill machine, ensuring that the location and size of the holes are accurate.
Metallization and Surface Treatment: After drilling, the surface of the circuit board is often metallized to provide connection points. This may involve coating the holes with metal, such as copper or gold plating. In addition, the surface of the circuit board may also receive surface treatments such as tin plating or spray coating to improve soldering performance and corrosion resistance.
Assembly and soldering: After the surface preparation is completed, the components on the circuit board will be mounted and soldered to its surface. This is usually done with automated equipment, but for some special components, manual work may be required.
Overlay: To protect a circuit board from environmental damage, a protective overlay is often applied to its surface. This can be a coated material such as epoxy, or a thermoset plastic or flexible polymer.
Final Inspection: The final step in the manufacturing process is complete inspection and testing of the finished circuit board. This includes visual inspection, electrical testing, solder joint quality inspection and, if necessary, X-ray inspection. Only through strict quality control procedures can the reliability and performance of the final product meet military standards.
Throughout the manufacturing process, manufacturers must follow strict quality management and control procedures to ensure product consistency and compliance. The manufacturing process of military circuit boards requires a high degree of expertise and technology to meet the stringent requirements of military applications.
How are military circuit boards made?
The manufacturing of military circuit boards is a complex and precise process involving advanced equipment and technology to ensure high-quality products. Military circuit board manufacturers usually use the following advanced equipment and technologies:
High-precision CNC machines and cutting equipment: The manufacturing of military circuit boards requires precise cutting and processing of substrates to ensure dimensional and shape accuracy. High-precision CNC machine tools and cutting equipment enable precise processing of substrates, ensuring the quality and performance of circuit boards.
Automated production lines: Many military circuit board manufacturers adopt automated production lines to improve production efficiency and product quality. These automated production lines can automate processes such as raw material handling, printing, chemical etching, drilling, metallization and final inspection, thereby reducing interference from human factors and improving product consistency and reliability.
Surface mounting technology (SMT): Surface mounting technology is an advanced technology commonly used in circuit board production. It can realize automated and precise welding of electronic components, improving the assembly efficiency and quality of circuit boards.
Control quality management system (QC): Military circuit board manufacturers usually have established a complete quality management system, including full-process quality control from raw material procurement to product delivery. They will use advanced quality inspection equipment and technologies, such as X-ray inspection, optical inspection, electronic probe testing, etc., to conduct strict inspection and evaluation of products to ensure that the products meet military standards and customer requirements.
R&D and innovation: Military circuit board manufacturers focus on technological innovation and R&D investment, and constantly introduce new materials, processes and technologies to improve product performance, reliability and adaptability. They often work closely with customers to customize and optimize products based on customer needs and feedback to ensure products can meet the stringent requirements of military applications.
To sum up, military circuit board manufacturers use a series of advanced equipment and technologies to produce high-quality circuit boards, and ensure product reliability and performance through strict quality management and continuous R&D innovation. They continuously pursue technological advancement and product optimization to meet changing military needs and challenges.
How much do military circuit boards cost?
The cost of military circuit boards is affected by many factors. First, the complexity of military circuit boards is one of the main factors that determines cost. Military applications typically require higher levels of technology and tighter specifications, so the cost of designing and manufacturing these boards is higher. Secondly, the scale of production will also affect costs. Typically, low-volume production of military circuit boards will cost more than mass production because the fixed costs of low-volume production are spread more per unit. In addition, material selection and procurement costs will also have an impact on the total cost. Because military circuit boards require the use of high-quality, durable materials, their material costs are typically higher than commercial circuit boards.
Military circuit boards typically cost more than commercial circuit boards. This is primarily because military circuit boards need to meet more stringent performance and reliability requirements. Military applications require circuit boards to operate stably under extreme environmental conditions, such as high temperature, low temperature, high humidity, and electromagnetic interference. To meet these requirements, military circuit boards often require more expensive materials and manufacturing processes, which increases their cost. In addition, the design and manufacturing process of military circuit boards also requires more time and human resources, further increasing costs.
Although military circuit boards cost more, their critical performance and reliability in military applications often far exceed that of commercial circuit boards. In the military field, performance and reliability are often more important than cost, so the high cost of military circuit boards is regarded as a necessary investment to protect national security and national defense interests.
What materials are used in military circuit boards?
Military circuit boards are an indispensable component of modern military equipment, and their durability and reliability are crucial. In order to meet the strict requirements of military applications, military circuit boards use a series of special materials with unique properties and characteristics.
First of all, the choice of base material for military circuit boards is crucial. Commonly used substrates include fiberglass reinforced epoxy resin (FR4), polyimide (PI), polyetheretherketone (PEEK), etc. These substrates have excellent mechanical strength, heat resistance and chemical stability, allowing them to maintain stable performance under harsh environmental conditions.
Secondly, the selection of conductive and insulating layers is critical to the performance and reliability of the circuit board. The conductive layer usually uses high-purity copper foil, which has good conductivity and welding performance. The insulation layer needs to have good insulation properties and high temperature resistance. Common insulation materials include polytetrafluoroethylene (PTFE) and polyimide film (PI Film).
In addition to the base material and conductive layer, military circuit boards may also use some special coatings and covering materials to enhance their durability and environmental resistance. For example, common anti-corrosion coatings include silicone, polyurethane and epoxy resin, which can effectively prevent circuit boards from being corroded by moisture, chemicals and corrosive media.
In addition, military circuit boards may also use some special technologies and processes during the design and manufacturing process to enhance their performance and reliability. For example, surface treatment technology can improve welding performance and corrosion resistance; controlled impedance line design can reduce signal interference and transmission loss; covering layer and packaging technology can improve the moisture resistance and corrosion resistance of circuit boards, etc.
To sum up, military circuit boards use a series of special materials and processes to achieve excellent durability and reliability. The selection and application of these materials and technologies ensure that military circuit boards can operate stably under harsh environmental conditions and meet the strict requirements of military applications.
Who can make military circuit boards?
In the military field, manufacturing high-quality military circuit boards is crucial. So, who can meet this stringent demand and produce reliable military circuit boards? In fact, there are many suppliers with rich experience and technical strength in the field of military circuit board manufacturing. However, when choosing the right manufacturer, the key is to find a company that can provide high-quality products, meet military specifications, and meet customer needs.
As a leading military circuit board manufacturer, our company has many years of experience and expertise and is committed to providing customers with the highest quality products and services. Our industry-leading manufacturing processes and technologies ensure that our military circuit boards perform exceptionally well in a variety of harsh environmental conditions.
Our manufacturing factory is equipped with the most advanced equipment and technology, including automated production lines, precision processing equipment and strict quality control systems. This enables us to achieve efficient production capabilities and guarantees that every circuit board undergoes rigorous inspection and testing to ensure compliance with the most stringent quality standards.
In addition to technical strength, we also focus on understanding and meeting customer needs. Our team of experienced engineers and technicians can provide customers with customized solutions to meet their specific needs and requirements. We always maintain close communication with our customers to ensure they have a clear understanding of product quality and delivery time.
As a reliable military circuit board manufacturer, we not only provide high-quality products, but also strive to establish long-term and stable cooperative relationships. Our customers include the defense sector, military industrial enterprises and scientific research institutions, who all give high praise and trust to our products and services.
All in all, as a professional military circuit board manufacturer, our company has rich experience, advanced technology and good customer reputation, and can meet the needs of various military applications. We will continue to work hard to improve product quality and technical level to provide customers with better products and services.
What are 5 qualities of a good customer service?
In military circuit board manufacturing, providing excellent customer service is critical. Here are five key attributes of great customer service:
Excellent customer service starts with professional attitude and behavior. From product inquiries to order tracking, the customer service team is expected to handle customer needs in a professional, courteous, and knowledgeable manner. They should be able to accurately understand their customers’ problems and provide timely and effective solutions.
Customers expect prompt responses when they have questions or concerns. Therefore, one of the keys to good customer service is responding promptly to customer inquiries, complaints or suggestions. The customer service team should maintain open communication channels to ensure that customers can contact them at any time and receive a response in the shortest possible time.
Understanding your customers’ needs and providing personalized service are the keys to building good customer relationships. A good customer service team should treat each customer individually, focusing on their specific needs and preferences, and working hard to provide them with customized solutions and support.
In customer service, solving problems and exceeding customer expectations is crucial. A quality customer service team should have good problem-solving skills, be able to quickly identify and resolve customer difficulties, and proactively seek lasting solutions to ensure customer satisfaction and loyalty.
Excellent customer service is not just about responding to customer needs, but more importantly, continuous improvement and improvement of service levels. The customer service team should actively collect customer feedback, analyze problems and bottlenecks, and continuously improve service processes and quality standards to ensure continuous improvement of customer satisfaction and corporate competitiveness.
Through high-quality customer service that embodies the above five attributes, military circuit board manufacturers can build strong customer relationships, enhance brand reputation, and succeed in a highly competitive market.
FAQS
What are the main challenges in designing military circuit boards?
Designing military circuit boards faces many challenges, including ensuring signal integrity, thermal management, and environmental suitability. Military circuit boards must be able to operate stably for a long time under harsh conditions, so designers need to consider how to reduce signal interference in the circuit and reduce the impact of temperature on electronic components, while ensuring the reliability of the circuit board under various environmental conditions.
What is the difference between military circuit boards and commercial circuit boards?
Compared with commercial circuit boards, military circuit boards have higher requirements and strict specifications. Military circuit boards need to work under extreme environmental conditions, such as high temperature, low temperature, high humidity and strong electromagnetic interference. Therefore, military circuit boards require more consideration in design, material selection, and manufacturing processes to ensure their reliability and stability.
What certifications should a military circuit board manufacturer have?
Military circuit board manufacturers should have a series of certifications and qualifications to ensure that their products comply with relevant standards and specifications. These include ISO 9001 quality management system certification, AS9100 aerospace quality management system certification, and ITAR (International Trade Regulations) compliance certification. These certifications demonstrate a manufacturer’s professionalism and compliance in quality management, product design and production processes, providing customers with confidence and assurance.
What are the main challenges in designing military circuit boards?
When designing circuit boards for military use, one of the main challenges is ensuring that the board can operate reliably under extreme environmental conditions. These environmental conditions may include high temperatures, low temperatures, high humidity, severe vibration, and electromagnetic interference. Therefore, designers need to use special materials and processes to ensure that the circuit board has sufficient durability and anti-interference capabilities.