Military Substrate Manufacturer. IPC Class III PCBs production, Advanced High speed and high frequency material PCBs and BGA packaging substrates,
In today’s era of digitalization and high technology, the military industry has an increasing demand for reliable, high-performance electronic equipment. In this context, military substrates (PCBs) are particularly important as a key component. Military substrates not only need to meet stability and reliability requirements in extreme environments, but also must have advanced technology and precise manufacturing processes. Therefore, the design and manufacturing of military substrates requires a high degree of precision and expertise to ensure their excellent performance and reliability in military applications.
What is a military substrate?
Military substrates are an important part of connecting and supporting electronic components in electronic devices. They carry critical functions and provide stable and reliable electronic connections for various applications in the military field. Typically, military substrates are constructed from multiple layers of composite materials that include conductive layers, insulating layers, and possibly other functional layers. This composite structure enables military substrates to operate in extremely harsh environmental conditions, such as high temperature, high pressure and strong vibration.
First of all, the conductive layer is one of the core components of military substrates. These layers are usually made of copper foil and are used to carry current and signals. The design and layout of conductive layers determines the connection methods and signal transmission paths between electronic components, and is critical to the performance and reliability of the entire circuit.
Secondly, the insulation layer plays a key role in military substrates. These layers are typically constructed from high-performance insulating materials such as polyimide (PI) or polytetrafluoroethylene (PTFE). The insulation layer not only provides isolation and protection between electronic components, but can also withstand the effects of harsh conditions such as high temperature, high pressure, and chemical corrosion, ensuring the stable operation of the circuit.
In addition, military substrates may contain other functional layers, such as impedance control layers, heat dissipation layers, and shielding layers. These functional layers can further improve the performance and reliability of military substrates and meet the requirements of specific applications.
In general, military substrates play an important role in the military field. Their design and manufacturing require highly specialized technology and strict quality control to ensure reliability and performance under various harsh conditions. With the continuous development of science and technology and the increasing military needs, military substrates will continue to play an important role, providing key support for the development and application of military electronic equipment.
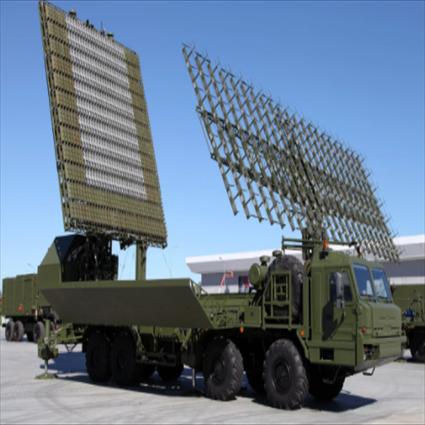
Military Substrate
Military Substrate design Reference Guide.
The design of military substrates is a complex and critical process that requires comprehensive consideration of many factors to ensure that the final product can operate stably and reliably in extreme environments. Here are the key guidelines and standards designers need to pay attention to when designing military substrates:
Environmental requirements
Military substrates usually need to work under various harsh environmental conditions, such as high temperature, high humidity, strong vibration and chemical corrosion. Therefore, these environmental factors must be taken into account during the design process and appropriate materials and processes must be selected to ensure that the substrate can operate stably under these conditions.
Electronic component layout
Proper electronic component layout is critical to the performance of military substrates. Designers need to consider factors such as distance between electronic components, layout compactness, signal transmission paths, and thermal management. Good layout design can minimize signal interference and electromagnetic interference and improve system performance and reliability.
Circuit connection
The circuit connections of military substrates must have a high degree of reliability and stability. Designers need to choose the appropriate connection technology, such as soldering, crimping or plugging, and ensure that the quality and reliability of the connection points meet standard requirements. In addition, the connection points must be rigorously tested and verified to ensure that they will not malfunction or become loose during long-term use.
Follow strict guidelines and standards
Designers must follow a series of strict guidelines and standards when designing military substrates, such as MIL-PRF-31032, IPC-6012, etc. These standards stipulate specific requirements for material selection, process flow, testing methods, etc., and designers must strictly abide by them to ensure that the quality and performance of the final product meet the requirements.
Design verification and testing
After the design is completed, the military substrate must be rigorously verified and tested to ensure that it meets the design requirements and standard requirements. This includes electrical testing, reliability testing, environmental testing and other aspects. Only after passing comprehensive testing and verification can the substrate be put into actual use.
During the design process of military substrates, designers must fully consider the above factors and take appropriate measures to ensure that the quality and performance of the final product meet the requirements of military applications. Only through rigorous design and testing can military substrates play their greatest role at critical moments and provide reliable technical support for military operations.
What material is used in Military Substrate?
The materials used in the manufacturing of military substrates are critical because they need to be highly reliable and durable to handle extreme environmental conditions and demanding work requirements. Here are some high-quality materials commonly used in military substrate manufacturing:
FR-4 epoxy resin
FR-4 epoxy resin is a widely used base material in PCB manufacturing. It has excellent insulation properties and mechanical strength, can effectively isolate circuits, and provide a stable support structure. In the military field, FR-4 epoxy resin is often used to manufacture low- and medium-level substrates, and its stability and reliability have been widely recognized.
Polyimide (PI)
Polyimide (PI) is a high-performance polymer material with excellent high temperature resistance and chemical stability. It is widely used in military applications to manufacture substrates in high-temperature environments, such as missile control systems and satellite communications equipment. The polyimide substrate maintains stable circuit connections under extreme temperature conditions, ensuring device reliability in harsh environments.
Polytetrafluoroethylene (PTFE)
Polytetrafluoroethylene (PTFE) is a material with excellent insulating properties and chemical inertness. It is widely used in high-frequency and microwave circuits in military substrate manufacturing, such as radar systems and communication equipment. PTFE substrate has the characteristics of low loss and high-speed signal transmission, and is suitable for military applications requiring high frequency and high-speed data transmission.
The use of these high-quality materials allows military substrates to maintain stable performance and reliability in harsh working environments, providing a solid foundation for the normal operation of military equipment.
By using these materials, military substrates can not only meet the high performance and stability requirements of military equipment, but also ensure long-term reliability in extreme environments. This makes military substrates play an indispensable role in modern military technology.
What size are Military Substrate?
Military substrate sizes vary based on specific application requirements. In the military field, there are a variety of equipment and systems that have different requirements for the size of the substrate.
First, some military equipment requires substrates that are as miniaturized as possible to accommodate compact space and lightweight design requirements. For example, reconnaissance drones, portable communication equipment, and identification devices often require miniaturized substrates to achieve compact designs that are easy to carry and deploy.
On the other hand, some military systems may require larger substrate sizes to accommodate more electronic components and functionality. For example, radar systems, navigation equipment, and military communications sites often require larger substrates to accommodate complex circuits and components and provide greater processing power and functionality.
In addition, some electronic systems on military vehicles and ships also require specially designed substrates to adapt to special environments and space constraints. These substrates may require heat, vibration and water resistance to ensure reliable operation under harsh conditions.
Therefore, military substrates come in a wide range of sizes, ranging from a few centimeters to several meters, depending on the application scenario and design requirements. In general, the size design of military substrates is carefully planned and adjusted according to specific military needs and technical requirements to ensure that the final system performance and reliability meet the expected requirements.
The Manufacturer Process of Military Substrate.
The manufacturing process of military substrates is a complex and sophisticated process that involves multiple key steps, from design to final testing, each step is critical to ensure that the quality and performance of the final product can meet stringent military standards.
The first is the design stage, where designers need to determine the circuit layout, wiring paths, and component locations based on customer requirements and technical specifications. At this stage, factors such as the distance between electronic components, signal transmission paths, and heat dissipation must be considered to ensure that the final design meets the requirements of military applications.
Next is the layout stage. The designer will arrange the positions of various components on the PCB board according to the design drawings and determine the connection paths. At this stage, factors such as space utilization, signal interference, and electromagnetic compatibility need to be considered to ensure the rationality and stability of the layout.
Then comes the printing stage, where the designed circuit pattern is transferred to the PCB board through printing technology. This process usually uses photolithography or inkjet technology to ensure the accuracy and clarity of the pattern.
Forming is an important step in the manufacturing process, which involves placing the PCB board into a heated press, which uses heat pressing technology to press the multiple layers of board material into a single unit. This process ensures tight connections between layers of the PCB board while improving the mechanical strength and thermal stability of the board.
The next step is to drill holes in the PCB board using mechanical or laser technology to install components and connect circuits. This process requires high-precision equipment and strict control to ensure accuracy of aperture and location.
Metallization is the coating of a PCB surface with a layer of metal, usually copper, to create conductive layers and connection points. This process can be achieved through electroless copper plating or electroplating copper technology to ensure the uniformity and conductive properties of the metal layer.
The last stage is the testing stage, where the manufactured PCB boards will be subjected to various tests, including connectivity testing, functional testing and environmental testing, to ensure that the quality and performance of the product meet the requirements. This process requires high-precision testing equipment and strict standards to ensure that each PCB board meets military standards and customer requirements.
In general, the manufacturing process of military substrates is a highly complex and precise process, which requires strict control and highly specialized technical support to ensure that the quality and performance of the final product can meet the stringent requirements of the military industry.
The Application area of Military Substrate.
Military substrates are a vital component of military equipment. Their application range covers various key fields, providing necessary support and guarantee for the success of military operations.
Communication Systems
Military communications systems are an important tool for the military to stay in touch, deliver instructions and obtain intelligence. Military substrates play a key role in connecting and supporting electronic components in communication equipment, ensuring the stability and reliability of communication equipment.
Radar system
Radar systems are of great significance in the military field and are used to monitor, detect and track air, sea and ground targets. Military substrates are responsible for signal processing, data transmission and control functions in radar equipment to ensure the efficient operation of the radar system.
Navigation System
Military navigation systems are used to determine and track the location, direction and movement path of military targets. Military substrates provide precise position calculations, navigation algorithms and data processing functions in navigation equipment, providing important support for the accuracy and real-time nature of military operations.
Drone
Drones play an increasingly important role in modern warfare and are used for reconnaissance, surveillance, strike and transportation missions. Military substrates play a key role in the control, navigation, communication and data transmission of UAVs, ensuring the safety and effectiveness of UAVs.
Military vehicles
Military vehicles are important equipment for army operations, including tanks, armored vehicles, transport vehicles, etc. Military substrates undertake key functions such as engine control, communication connections, and fire control systems in vehicle electronic systems, improving the vehicle’s combat capabilities and survivability.
To sum up, military substrates are widely used in various military equipment, providing key support and guarantee for the success of military operations. Their reliability, stability and performance are crucial to the success of military operations and are an important part of modern military technology.
What are the advantages of Military Substrate?
The advantage of military substrates is that they far exceed traditional circuit boards in terms of reliability, performance and service life. The following is a detailed description of the advantages of military substrates:
Higher reliability
The design and manufacturing of military substrates strictly follows military standards and specifications, using high-quality materials and advanced manufacturing processes. This allows military substrates to maintain stable performance under extreme conditions and are not easily affected by the external environment. Compared with traditional circuit boards, military substrates are better able to withstand factors such as temperature changes, vibration, and electromagnetic interference, thereby ensuring stable operation of equipment.
Better performance
Military substrates have excellent electrical performance and signal transmission characteristics, providing higher bandwidth and lower signal distortion. Its design takes into account factors such as circuit layout, signal transmission path, and noise control to ensure accurate signal transmission and processing. This enables military substrates to perform well in high-frequency and high-speed digital signal applications, meeting the stringent performance requirements of military equipment.
Longer service life
Because military substrates use high-quality materials and manufacturing processes, their service life is typically longer than traditional circuit boards. Military substrates have excellent heat resistance, corrosion resistance and mechanical strength, and can operate stably for a long time in harsh environments, reducing equipment maintenance and replacement costs. This makes military substrates a long-term and reliable solution in the military industry, providing reliable guarantee for the continued operation of military equipment.
Work under extreme conditions
Military substrates have been rigorously tested and verified to work in extreme conditions, such as high temperature, low temperature, high pressure and low pressure environments. Whether in combat scenarios or in harsh natural environments, military substrates can operate stably and reliably, ensuring the normal operation of military equipment and the safety of soldiers.
Maintain a stable electronic connection
Military substrates are designed with the connections and layout between electronic components in mind to ensure stable electronic connections. Using advanced welding technology and high-precision manufacturing processes, electronic components can be firmly fixed on the substrate and maintain good electrical connections. This ensures that military equipment will not malfunction or degrade in performance due to electronic connection issues during use.
To sum up, military substrates have the advantages of higher reliability, better performance and longer service life. They provide important guarantees for the design and manufacturing of military equipment and are one of the indispensable key technologies in the military industry. one.
FAQ
What is the difference between military substrates and ordinary PCBs?
There are obvious differences between military substrates (PCBs) and ordinary PCBs in terms of material selection, manufacturing processes and application fields. First of all, in terms of material selection, military substrates usually use high-quality materials, such as FR-4 epoxy resin, polyimide (PI) and polytetrafluoroethylene (PTFE) to ensure reliability and reliability under harsh conditions. stability. Regular PCBs, on the other hand, may use cheaper materials and are suitable for general commercial and consumer electronics.
What applications can the substrate be used for?
Military substrates are widely used in various military equipment, including communication systems, radar systems, navigation systems, drones, and military vehicles. In these applications, military substrates play an important role in connecting and supporting electronic components, and their reliability and performance are critical to the success of military operations.
How long is the manufacturing cycle of military substrates?
The manufacturing lead time for military substrates depends on the specific design and requirements and typically ranges from a few weeks to a few months. The manufacturing process may involve multiple stages such as design confirmation, sample production, test verification, and mass production, which will take a certain amount of time to complete.
What is the cost of military substrates?
Military substrates typically cost more than regular PCBs due to more demanding materials and manufacturing processes, as well as the need to meet military standards and specifications. Therefore, the cost of military substrates can be affected by factors such as material selection, design complexity, and manufacturing volume.
How to ensure the reliability of military substrates?
The reliability guarantee of military substrates needs to be achieved through strict design, manufacturing and testing. In the design stage, factors such as environmental requirements, circuit layout, and material selection need to be taken into consideration; in the manufacturing process, each step needs to be strictly controlled to ensure that the product meets specifications; in the testing stage, a variety of tests and verifications need to be performed to ensure that the product The performance and reliability meet the requirements.