Millimeter Wave Antenna PCB Manufacturer.As a leading Millimeter Wave Antenna PCB manufacturer, we specialize in designing and producing high-frequency circuit boards that meet the stringent requirements of advanced communication systems. Our state-of-the-art facilities and expertise in millimeter wave technology ensure superior performance, reliability, and precision in every PCB we deliver. Whether for 5G, radar, or satellite applications, our tailored solutions drive innovation and connectivity in the modern world.
Millimeter wave (mmWave) antenna PCBs are critical components in the realm of high-frequency communication systems. Operating in the frequency range of 30 GHz to 300 GHz, mmWave technology enables a wide array of applications, from 5G wireless networks to advanced radar systems and high-resolution imaging. The design and manufacturing of mmWave antenna PCBs involve intricate considerations to ensure optimal performance and reliability. This article explores the key aspects of mmWave antenna PCBs, including their structure, materials, manufacturing process, applications, and advantages.
What is a Millimeter Wave Antenna PCB?
A millimeter wave antenna PCB is a specialized printed circuit board designed to operate at frequencies in the mmWave spectrum. These PCBs integrate antenna elements and supporting circuitry to transmit and receive electromagnetic signals at very high frequencies. The high-frequency operation allows for greater data transmission rates and improved resolution in imaging and radar applications. However, designing and manufacturing mmWave antenna PCBs require precise engineering to address challenges such as signal loss, impedance matching, and thermal management.
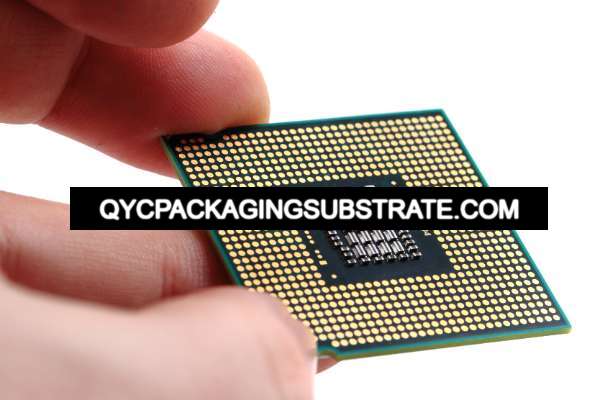
Millimeter Wave Antenna PCB Manufacturer
Structure of Millimeter Wave Antenna PCBs
The structure of mmWave antenna PCBs is carefully engineered to ensure efficient signal transmission and minimal loss. Key structural elements include:
The design of the antenna elements is critical for efficient signal transmission and reception. These elements can be patch antennas, dipole antennas, or other configurations suitable for mmWave frequencies. The size and shape of the antenna elements are meticulously designed to match the wavelength of the target frequency.
The substrate material must possess low dielectric constant and low loss tangent to minimize signal loss and maintain signal integrity at high frequencies. Commonly used materials include Rogers, Teflon, and other advanced laminates.
Ground planes are essential for providing a reference point for the antenna elements and supporting circuitry. They help in controlling the electromagnetic fields and minimizing interference.
Microstrip lines are used to connect the antenna elements to the supporting circuitry. The width and spacing of these lines are designed to ensure impedance matching and minimize signal loss.
Vias are used to create vertical connections between different layers of the PCB. These structures must be precisely fabricated to maintain signal integrity at high frequencies.
Shielding techniques, such as metallic enclosures and isolation structures, are employed to minimize interference and crosstalk between different components and signal paths.
Materials Used in Millimeter Wave Antenna PCBs
The choice of materials is critical for the performance of mmWave antenna PCBs. Key materials include:
High-frequency substrates such as Rogers RO3000, RO4000 series, Teflon (PTFE), and other low-loss laminates are commonly used. These materials offer low dielectric constant and low loss tangent, essential for maintaining signal integrity at mmWave frequencies.
Copper is the primary conductive material used for the antenna elements and microstrip lines due to its excellent electrical conductivity. In some cases, gold plating may be used to enhance performance and prevent oxidation.
Advanced dielectric materials with low loss and stable dielectric properties are used to insulate the conductive layers and ensure minimal signal loss.
Metallic materials such as aluminum or copper are used for shielding to prevent electromagnetic interference and ensure signal integrity.
The Manufacturing Process of Millimeter Wave Antenna PCBs
The manufacturing process of mmWave antenna PCBs involves several precise and controlled steps:
The design phase involves creating detailed schematics and layouts using computer-aided design (CAD) software. Electromagnetic simulation tools are used to optimize the antenna design, impedance matching, and signal integrity.
High-frequency substrate materials and conductive materials are selected based on the design requirements and performance specifications.
Multiple layers of substrate and conductive materials are laminated together to form a multilayer structure. Precise alignment and control are essential to ensure the layers are properly bonded.
Vias are drilled into the PCB to create vertical electrical connections between different layers. These holes are then plated with copper to establish conductive pathways.
The circuit patterns are created using photolithographic processes. This involves applying a photosensitive film (photoresist) to the copper surface, exposing it to ultraviolet (UV) light through a mask, and developing the exposed areas to reveal the desired circuit patterns. The PCB is then etched to remove the unwanted copper, leaving behind the circuit traces.
The antenna elements are fabricated using precise etching and plating techniques to ensure accurate dimensions and minimal signal loss.
Surface finishes such as ENIG (Electroless Nickel Immersion Gold) or immersion silver are applied to the contact pads to enhance solderability and protect the conductive traces from oxidation and corrosion.
The final PCBs undergo assembly, where additional components such as connectors, amplifiers, and filters are added. Rigorous testing, including signal integrity tests, impedance matching tests, and environmental stress tests, are conducted to ensure the PCBs meet the required performance standards.
Application Areas of Millimeter Wave Antenna PCBs
Millimeter wave antenna PCBs are used in a wide range of high-frequency applications across various industries. Key application areas include:
Wave antenna PCBs are critical for 5G networks, enabling high-speed data transmission and low-latency communication. They are used in base stations, small cells, and mobile devices to support high-frequency bands.
Wave antenna PCBs are used in automotive radar systems for advanced driver assistance systems (ADAS) and autonomous driving. They provide high-resolution imaging and precise object detection.
In satellite communication, mmWave antenna PCBs enable high-frequency data links between satellites and ground stations, supporting high-bandwidth communication.
Wave technology is used in medical imaging, security screening, and industrial inspection to provide high-resolution images and detailed analysis.
Wave antenna PCBs are used in IoT devices to enable high-frequency communication and connectivity, supporting applications such as smart cities, industrial automation, and smart homes.
In military applications, mmWave antenna PCBs are used in advanced radar systems, communication systems, and electronic warfare to provide high-frequency performance and reliability.
Advantages of Millimeter Wave Antenna PCBs
Millimeter wave antenna PCBs offer several advantages that make them indispensable for high-frequency applications. These advantages include:
mmWave technology enables extremely high data transmission rates, supporting the growing demand for bandwidth-intensive applications such as 5G and high-resolution imaging.
In radar and imaging applications, mmWave technology provides improved resolution and accuracy, enabling precise object detection and detailed analysis.
mmWave antenna PCBs allow for compact and lightweight designs, making them suitable for mobile devices, IoT applications, and other space-constrained environments.
mmWave technology supports low-latency communication, essential for real-time applications such as autonomous driving and industrial automation.
mmWave frequencies offer wide bandwidth, enabling multiple channels and high-capacity communication links.
mmWave antenna PCBs can be used in a wide range of applications, from wireless communication and radar systems to high-resolution imaging and IoT devices.
FAQ
What materials are commonly used in mmWave antenna PCBs?
Common materials used in mmWave antenna PCBs include high-frequency substrates such as Rogers RO3000, RO4000 series, Teflon (PTFE), and other low-loss laminates. Conductive materials like copper and sometimes gold plating are used for antenna elements and microstrip lines. Advanced dielectric materials and metallic shielding materials are also used to ensure signal integrity and prevent interference.
How do mmWave antenna PCBs improve the performance of 5G networks?
mmWave antenna PCBs improve the performance of 5G networks by enabling high-frequency operation, which allows for greater data transmission rates and low-latency communication. This supports bandwidth-intensive applications and provides the high-speed connectivity required for 5G networks.
Can mmWave antenna PCBs be used in automotive radar systems?
Yes, mmWave antenna PCBs are widely used in automotive radar systems for advanced driver assistance systems (ADAS) and autonomous driving. They provide high-resolution imaging and precise object detection, essential for safe and reliable vehicle operation.
What are the advantages of using mmWave technology in satellite communication?
The advantages of using mmWave technology in satellite communication include high-frequency data links, which support high-bandwidth communication between satellites and ground stations. This enables efficient data transmission and high-capacity communication links for various satellite applications.