Professional Mini Ceramics PCB manufacturing, Ultra-small bump pitch Ceramics substrate, ultra-small trace and spacing Ceramics substrate. We offer Mini Ceramics PCB and Ceramics package substrates from 2 layer to 22 layers.
In the field of modern electronics, PCB (Printed Circuit Board) plays a vital role. As the basic structure that connects and supports electronic components, the design and manufacturing process of PCB is crucial. In the continuous evolution of PCB, Mini Ceramics PCB, as a new type of printed circuit board material, has attracted much attention in specific fields because of its excellent performance. This article will delve into the manufacturing process, material properties and application scenarios of Mini Ceramics PCB, and answer related common questions to provide readers with a comprehensive understanding and reference.
What is Mini Ceramics PCB?
Mini Ceramics PCB (miniature ceramic printed circuit board) is a printed circuit board made of special ceramic materials that has unique characteristics and advantages compared to traditional fiberglass materials. This special ceramic material usually includes aluminum oxide (Alumina) or aluminum nitride (AlN), which exhibit unique advantages in electronic applications.
Compared with traditional materials, the ceramic materials used in Mini Ceramics PCB have several significant advantages. First of all, ceramic materials have excellent temperature resistance and can maintain stable electrical properties in extreme high-temperature environments, which makes Mini Ceramics PCB have broad application prospects in high-temperature applications. Secondly, ceramic materials have good thermal conductivity and mechanical strength, which enables Mini Ceramics PCB to effectively transfer heat in high-power electronic equipment and have high vibration resistance and wear resistance. In addition, ceramic materials also have good corrosion resistance and can resist the erosion of chemical substances, thereby improving the stability and reliability of Mini Ceramics PCB in harsh environments.
In addition to these advantages, Mini Ceramics PCBs have low dielectric losses and good high-frequency characteristics, making them excellent in radio frequency (RF) and microwave applications. The stability and reliability of this material make Mini Ceramics PCB widely used in military, aerospace, medical and industrial fields. In general, Mini Ceramics PCB provides higher performance and reliability for electronic devices by using special ceramic materials, providing reliable solutions for various special application scenarios.
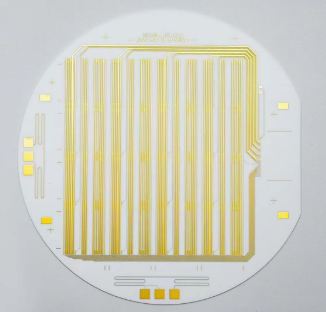
Ceramics PCB
How to design Mini Ceramics PCB?
Designing Mini Ceramics PCB is a complex and critical task that requires considering multiple factors to ensure that the final product meets the requirements. When designing, the following factors require special attention:
First, material selection is crucial. Mini Ceramics PCBs are made of micro ceramic materials, such as aluminum oxide (Alumina) or aluminum nitride (AlN). During the design process, it is necessary to ensure that the selected materials have excellent thermal conductivity, heat resistance and corrosion resistance to meet the requirements of the specific application.
Secondly, circuit layout and signal transmission are the focus of the design process. Good circuit layout can minimize signal interference and crosstalk and improve circuit performance and stability. During the layout process, care needs to be taken to avoid signal line crossings, maintain appropriate signal path lengths, and optimally place power devices and interfaces.
In addition, heat dissipation design is also a factor that cannot be ignored. Mini Ceramics PCB is usually used in electronic applications in high-temperature environments, so it is necessary to design an effective heat dissipation structure to ensure that circuit components can effectively cool down during operation and improve the reliability and stability of the system.
During the design and layout process, engineers usually use professional PCB design software, such as Altium Designer, Cadence Allegro, etc. These software provide a wealth of functions and tools to help engineers achieve fast and accurate design and layout. They also provide simulation and verification functions to help engineers evaluate the performance and reliability of the design.
In addition to the above factors, the design process also needs to pay attention to the cooperation with the manufacturing process to ensure the achievability and manufacturability of the design. For example, the processing technology of Mini Ceramics PCB’s special materials, cost factors, and communication and collaboration with manufacturers need to be considered.
To sum up, designing Mini Ceramics PCB requires comprehensive consideration of multiple factors such as material selection, circuit layout, heat dissipation design, and cooperation with the manufacturing process. Through reasonable design and strict verification, we can ensure that the final product has excellent performance and reliability and meets customer needs and expectations.
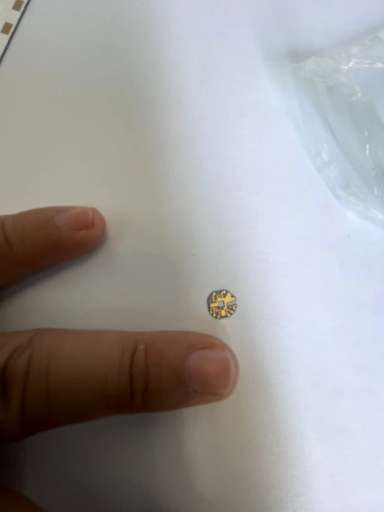
Mini Ceramics PCB
What is the manufacturing process of Mini Ceramics PCB?
The manufacturing process of Mini Ceramics PCBs is a precise and complex process involving multiple critical steps, each of which is critical to the quality and performance of the final product.
Before manufacturing Mini Ceramics PCB, design verification first needs to be done. This step ensures that the design meets specifications and requirements, including circuit layout, dimensional specifications, and material selection. The importance of the design verification phase is to ensure that the product’s functionality and performance are consistent with customer expectations while reducing errors and corrections in subsequent manufacturing processes.
Choosing the right ceramic material is critical to the performance of Mini Ceramics PCBs. Commonly used materials include aluminum oxide (Alumina) and aluminum nitride (AlN), which have excellent thermal conductivity and mechanical strength. The preparation and selection of materials determines the quality and stability of the final product and must therefore be carried out strictly according to specifications.
Printing of PCBs is one of the key steps in the manufacturing process. During the printing process, the circuit pattern and metallization pattern are transferred to the ceramic substrate. The accuracy and quality of printing directly affects the subsequent sintering and metallization steps, so precise control and adjustment are necessary.
Sintering involves subjecting printed ceramic substrates to high temperatures to form a solid structure and good thermal conductivity. Temperature and time control during the sintering process are crucial to ensure the density and stability of the ceramic substrate. Quality control is particularly important during the sintering stage to avoid product defects caused by uneven temperatures or incomplete sintering.
Metallization is to cover the surface of a ceramic substrate with a metal layer after sintering to achieve circuit connection and signal transmission. The uniformity and adhesion of metallization have an important impact on the stability and reliability of the circuit. Precise metallization processes and quality inspections ensure Mini Ceramics PCB performance meets requirements.
Surface treatment is to enhance the anti-corrosion performance and welding performance of Mini Ceramics PCB. Commonly used surface treatment methods include gold plating, silver plating and tin spraying. The quality and uniformity of surface treatment directly affects the reliability and stability of the welded connection, so it must be strictly controlled.
The last critical step is quality inspection of the manufactured Mini Ceramics PCB. Inspection includes visual inspection, dimensional measurement, electrical testing and reliability evaluation, etc. Only through strict quality testing can we ensure that products comply with standards and specifications to meet customer needs and expectations.
Through strict control and quality management of the above steps, the quality and stability during the manufacturing process are ensured, and Mini Ceramics PCB products that meet the requirements are finally produced.
How much does it cost to manufacture Mini Ceramics PCB?
The cost of manufacturing Mini Ceramics PCBs is a complex issue that is affected by multiple factors. First, the cost of Mini Ceramics PCB is affected by the cost of materials. Compared with the materials used in traditional PCBs, such as FR4 (fiberglass), Mini Ceramics PCBs use high-performance ceramic materials, such as alumina (Alumina) or aluminum nitride (AlN), which are usually more expensive. Therefore, material cost is one of the major costs of manufacturing Mini Ceramics PCB.
Secondly, the cost of Mini Ceramics PCB is also affected by the complexity of the design. Design complexity covers factors such as circuit layout, number of layers, and size. Generally speaking, designing more complex Mini Ceramics PCBs will result in increased manufacturing costs because more processes and higher manufacturing precision are required.
In addition, the cost of manufacturing Mini Ceramics PCB is also affected by the manufacturing process and technology. Compared with traditional PCBs, the manufacturing of Mini Ceramics PCBs requires higher temperatures and pressures to complete process steps such as sintering, which may require more advanced production equipment and stricter process control, thereby increasing manufacturing costs.
Compared with traditional PCB, the cost of Mini Ceramics PCB is usually higher. However, this additional cost is often worth it. Mini Ceramics PCB has higher temperature resistance, corrosion resistance and mechanical strength, and is suitable for more harsh environments and application scenarios. Therefore, although the cost of manufacturing Mini Ceramics PCB is higher, its performance advantages and applicability often make up for this cost.
In general, the cost of manufacturing Mini Ceramics PCB is affected by many factors, including material cost, design complexity and manufacturing process. Although the cost of Mini Ceramics PCB is higher compared to traditional PCB, its superior performance and applicability can often make it worth the cost. Therefore, when selecting PCB materials, a combination of cost and performance needs to be considered to ensure the most appropriate solution is selected.
What materials are Mini Ceramics PCBs made of?
Mini Ceramics PCB is a special type of printed circuit board, usually made of high-performance ceramic materials, mainly including aluminum oxide (Alumina) and aluminum nitride (AlN).
Alumina is a common ceramic material with excellent thermal conductivity and mechanical strength. Its features include high temperature stability, corrosion resistance and insulation. In Mini Ceramics PCBs, aluminum oxide is commonly used as the substrate material to support and connect electronic components. Due to its good thermal conductivity and mechanical strength, aluminum oxide is suitable for high-power and high-frequency electronic applications such as power amplifiers, radio frequency (RF) modules, and sensors.
Aluminum nitride (AlN) is a ceramic material with excellent thermal conductivity and insulation properties. Aluminum nitride has better thermal conductivity than aluminum oxide, so it is more common in some electronic applications that require higher heat dissipation. When aluminum nitride is used as the substrate material in Mini Ceramics PCB, it can effectively improve the heat dissipation performance and maintain stable operation of the circuit. Therefore, aluminum nitride is often chosen for the manufacture of Mini Ceramics PCBs in electronic applications with high power density, high temperature and high frequency.
The application of these high-performance ceramic materials in Mini Ceramics PCB brings many advantages. First of all, they have excellent thermal conductivity and can effectively dissipate heat to ensure the stable operation of electronic components in high-temperature environments. Secondly, these materials have good mechanical strength and corrosion resistance, can meet the requirements of harsh working environments, and improve the reliability and durability of circuit boards. In addition, these materials also have good insulation properties, which can effectively isolate signal interference between circuits and improve the performance and stability of the circuit.
In general, Mini Ceramics PCB is made of high-performance ceramic materials with excellent thermal conductivity, mechanical strength and insulation properties, and is suitable for high-power, high-temperature and high-frequency electronic applications. By selecting appropriate materials and adopting professional manufacturing processes, Mini Ceramics PCB can meet various stringent application requirements, providing an important guarantee for the performance and reliability of electronic products.
Who makes Mini Ceramics PCBs?
In the manufacturing process of Mini Ceramics PCB, the manufacturer plays a vital role. In this field, our company (here you can replace your company name) is an industry-leading manufacturer dedicated to providing high-quality Mini Ceramics PCB solutions.
Professional technical team: We have an experienced and skilled team that is proficient in the manufacturing process and technology of Mini Ceramics PCB. Our team of engineers not only have deep expertise in PCB design and manufacturing, but also continuously pay attention to the latest technology and trends in the industry to ensure that our products are always at the leading edge.
Advanced production equipment: In order to ensure the manufacturing quality and efficiency of Mini Ceramics PCB, we are equipped with advanced production equipment and facilities. From material processing to printing, sintering and final inspection and packaging, our production lines are carefully designed to meet production needs of all sizes and requirements.
Quality Control and Assurance: We strictly follow the ISO quality management system and implement strict quality control and assurance measures. From the procurement of raw materials to the delivery of final products, each of our steps is carefully monitored and inspected to ensure product stability, reliability and consistency.
Customized customer services: We understand that each customer’s needs are unique, so we provide flexible customized services. Whether it is a requirement for a specific application scenario or a tailor-made design, we are able to meet our customers’ needs and provide optimal solutions.
Continuous improvement and innovation: As a company leading the development of the industry, we constantly pursue technological innovation and improvement of production processes. We invest considerable resources in R&D and innovation to meet the growing market demand for Mini Ceramics PCBs and provide customers with higher levels of products and services.
Through our company’s efforts and commitment, we are committed to becoming your trusted partner, providing you with high-quality Mini Ceramics PCB solutions, and jointly promoting the development and progress of the electronics industry.
Five Traits of Great Customer Service
Excellent customer service is crucial in the Mini Ceramics PCB manufacturing industry. Here are five traits of great customer service, along with what they look like in this industry and how to ensure a high level of customer service:
Good customer service requires prompt and clear communication with customers. In the Mini Ceramics PCB manufacturing industry, communication skills are reflected in establishing effective communication channels with customers and maintaining close contact throughout the order process. Communication about production schedules, design requirements, and quality standards is critical to ensuring smooth product delivery. To ensure a high level of customer service, manufacturers can maintain communication with customers through regular updates, project progress reports and professional technical support.
Prompt response to customer inquiries and questions is an important part of excellent customer service. In the Mini Ceramics PCB manufacturing industry, responding quickly to customer needs and feedback can increase customer satisfaction and build long-term relationships. By establishing efficient customer service teams and processes, manufacturers can respond quickly when customers raise questions or needs and provide timely solutions.
Being empathetic means being able to understand and pay attention to your customers’ needs and concerns. In the Mini Ceramics PCB manufacturing industry, this means that manufacturers need to have a deep understanding of their customers’ project requirements, application scenarios and technical needs, and work hard to meet these needs. By actively listening to customer feedback and opinions, and making adjustments and improvements based on customer needs, manufacturers can build trust and partnership with their customers.
An important characteristic of good customer service is reliability, ensuring product quality and on-time delivery. In the Mini Ceramics PCB manufacturing industry, manufacturers need to strictly control the production process to ensure that each product meets design requirements and quality standards. At the same time, manufacturers should also plan production plans reasonably and take measures to ensure on-time delivery of products to meet customer needs and maintain a good reputation.
Excellent customer service requires treating customers with professionalism, courtesy, and efficiency. In the Mini Ceramics PCB manufacturing industry, manufacturers need to have extensive technical knowledge and experience and be able to provide customers with professional advice and support. By providing timely technical support, solutions and training, manufacturers can enhance customers’ trust and establish long-term and stable cooperative relationships.
In order to ensure a high level of customer service, Mini Ceramics PCB manufacturers can continuously optimize the customer service experience by establishing a complete quality management system, continuously improving customer service processes, and continuously improving the professional skills and service awareness of employees. At the same time, manufacturers can also timely understand customer needs and opinions through customer satisfaction surveys and feedback mechanisms, and make targeted improvements and adjustments. By continuously improving customer service levels, manufacturers can win the trust and support of customers and maintain a competitive advantage in the industry.
Frequently Asked Questions
Are Mini Ceramics PCBs suitable for all electronic applications?
While Mini Ceramics PCBs offer many advantages, they may not be suitable for all electronic applications. Their higher manufacturing costs and specialized properties make them best suited for applications requiring high temperature resistance, excellent thermal conductivity, and superior reliability in harsh environments. It’s essential to evaluate the specific requirements of your application and consult with the manufacturer to determine the suitability of Mini Ceramics PCBs.
What distinguishes Mini Ceramics PCB from traditional PCBs?
Mini Ceramics PCBs utilize miniature ceramic materials, offering enhanced thermal resistance and corrosion resistance compared to conventional materials. This makes them suitable for specialized electronic applications in challenging environments.
What is involved in the manufacturing process of Mini Ceramics PCBs?
The manufacturing process of Mini Ceramics PCBs includes several steps such as design validation, material preparation, printing, sintering, metallization, surface treatment, and testing. Each step is crucial in ensuring the final product meets quality and reliability standards.
How long does it take to manufacture Mini Ceramics PCBs?
The manufacturing time for Mini Ceramics PCBs depends on factors like design complexity and production capacity of the manufacturer. Typically, it ranges from several days to a few weeks.
Are Mini Ceramics PCBs more expensive compared to traditional PCBs?
Mini Ceramics PCBs may have slightly higher manufacturing costs compared to traditional PCBs due to the specialized materials and manufacturing processes involved. However, their benefits in specific applications often justify the investment.