Mini led pcb manufacturing. Features: microtrace(30um), ultra-small spacing(30um), ultra-thin finished board thickness, finished board surface flatness is higher, easier to assemble components.
Mini LED PCB (Printed Circuit Board) is an innovative product that combines micro LED (Light-Emitting Diode) and circuit board technology. This circuit board enables a highly integrated display solution by embedding micro LEDs within it. Mini LED PCB plays a key role in electronic display technology, mainly through the following ways:
First, Mini LED PCB provides higher brightness and wider color gamut, resulting in more vivid and realistic image performance. The tiny but powerful LED light source enables the display to present finer details and deeper colors, providing users with a more stunning visual experience.
Secondly, Mini LED PCB has excellent contrast and black performance capabilities. The high-density layout and precise control of micro LEDs enable Mini LED displays to achieve deeper blacks and clearer images, thereby enhancing the layering and realism of the picture.
In addition, Mini LED PCB also has excellent energy efficiency characteristics. Compared with traditional LCD displays, Mini LED displays can achieve higher energy efficiency, greatly reduce energy consumption, and at the same time extend the battery life of the device, providing users with a longer use experience.
In general, Mini LED PCB, as an innovative electronic display technology, achieves a more efficient, vivid and energy-saving display solution by combining micro LED and printed circuit board technology. Its development in the field of electronic display will bring users a better visual experience and push the entire display technology industry to new heights.
How to Design a Mini led pcb manufacturing?
Designing manufacturing for mini LED PCBs involves considering several key factors:
Size and Layout: Mini LED PCBs typically require small dimensions, so the design must optimize the layout to ensure dense placement of LED components and maximum space saving.
Thermal Management: LEDs generate heat during operation, so effective thermal management measures need consideration in the design. This may include heat sinks, thermal vias, or metal core boards to ensure stable temperatures during LED operation.
Electrical Wiring: Designing proper electrical wiring ensures good electrical connectivity between LED components, reducing circuit impedance, and enhancing circuit stability and reliability.
Material Selection: Choosing materials with high thermal conductivity and heat resistance is crucial for designing mini LED PCBs. For example, aluminum substrates or ceramic substrates are commonly used due to their excellent heat dissipation performance and high-temperature resistance.
Manufacturing Processes: Manufacturing mini LED PCBs requires precise manufacturing processes and highly automated production lines. Employing advanced manufacturing technologies and equipment ensures the accuracy and quality of the PCBs.
In summary, designing mini LED PCBs involves comprehensive consideration of factors such as size and layout optimization, thermal management, electrical wiring, material selection, and manufacturing processes. Through rational design and manufacturing, mini LED PCBs that are compact in size and stable in performance can be produced, meeting the needs of various portable electronic devices and lighting fixtures.
What is the Mini led pcb manufacturing Fabrication Process?
The fabrication process of mini LED PCB manufacturing typically involves the following steps:
Design and Layout: Firstly, PCB design and layout are conducted based on the requirements of LED size, quantity, and layout. Factors such as electrical connections, thermal management, and size constraints are considered during the design phase.
Material Preparation: Materials required for PCB manufacturing are prepared, including substrate materials (such as aluminum or ceramic substrates), metal foils (typically copper foils), insulation materials, and encapsulation materials.
Photolithography: Photoresist is applied to the surface of the metal foil, and then the designed pattern is transferred to the photoresist using photolithography equipment. Through the exposure and development process, circuit patterns are formed on the surface of the metal foil.
Etching: The metal foil treated with photolithography is placed into an etching solution, where the unprotected metal parts not covered by the photoresist are etched away, forming conductive paths.
Drilling: Holes are drilled on the PCB using drilling equipment for component installation and electrical connection.
Plating: The surface of the PCB is plated to enhance its conductivity and improve its corrosion resistance and solderability.
Assembly: LEDs and other electronic components are mounted onto the PCB and soldered to form a complete LED circuit board.
Testing and Quality Control: Electrical testing and visual inspection are conducted to ensure that the quality and performance of the LED PCB meet the design requirements.
Encapsulation: Finally, the LED PCB is encapsulated to protect the circuit board and components, and to provide external connection interfaces.
These steps constitute the basic process flow of mini LED PCB manufacturing. Through precise manufacturing processes and quality control, stable performance and reliable quality mini LED PCB products can be produced.
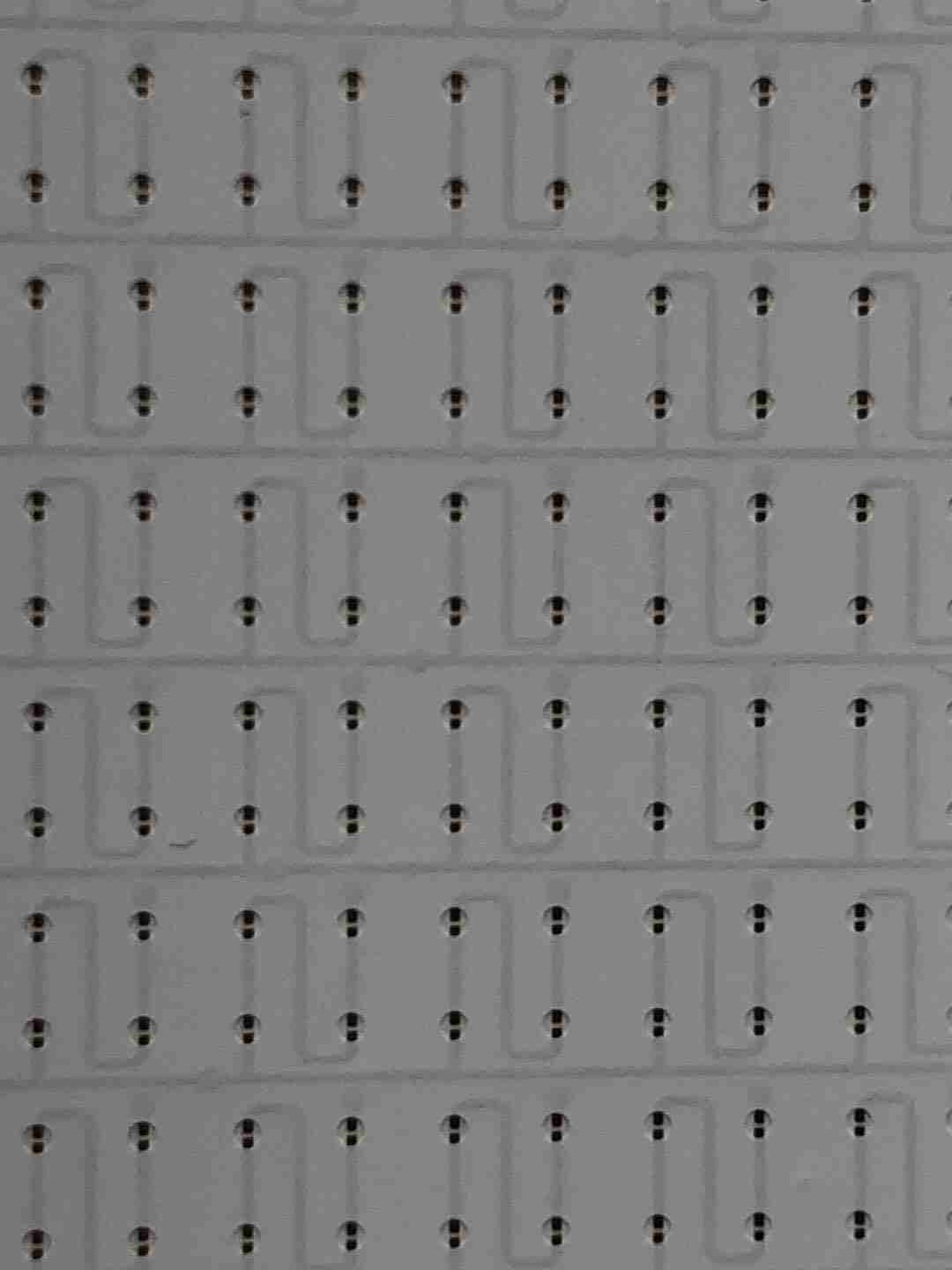
Mini led pcb
How Much Does a Mini led pcb manufacturing Cost?
The manufacturing cost of mini LED PCBs is influenced by various factors, making it difficult to provide specific cost figures. Here are some key factors affecting the manufacturing cost of mini LED PCBs:
PCB Size and Complexity: Mini LED PCBs typically require small sizes and dense layouts, which may increase manufacturing costs. Smaller PCBs demand higher manufacturing precision and more complex processes.
Material Cost: Opting for high-quality materials usually increases manufacturing costs. For instance, materials with better heat dissipation properties like aluminum substrates or ceramic substrates tend to be relatively expensive.
Process Requirements: Manufacturing mini LED PCBs often entails higher process requirements and more sophisticated equipment, which can raise manufacturing costs.
Production Scale: Bulk production generally lowers unit costs. Therefore, order quantity and production scale also impact the manufacturing cost of mini LED PCBs.
Additional Services: Additional services such as testing, quality control, and encapsulation may increase manufacturing costs.
In summary, the manufacturing cost of mini LED PCBs varies depending on specific requirements. For an accurate cost estimate, it is advisable to engage in detailed discussions with potential manufacturing partners and consider these factors.
How to manufacturing a Mini led pcb manufacturing?
The manufacturing of Mini LED PCB (Printed Circuit Board) is a precise and complex process that involves multiple key steps, each of which is vital to ensure the quality and performance of the final product. Here are the key steps for making Mini LED PCB:
The first step in manufacturing Mini LED PCB is to prepare the substrate. The substrate can be organic, metallic or ceramic, depending on application needs and performance requirements. The surface of the substrate needs to be cleaned and treated to ensure good adhesion and reliability.
Precise positioning of Mini LEDs on a substrate is the next critical step in the manufacturing process. Precision automated equipment is used to mount the Mini LEDs into their intended locations and ensure they are properly aligned with the rest of the substrate.
After the Mini LED is positioned, soldering is performed to connect the LED to the substrate. Use different soldering techniques, such as hot air soldering iron soldering or reflow soldering, to ensure a solid connection between the LED and the substrate and maintain good electrical contact.
At every stage of the manufacturing process, quality control is critical. Use automated inspection equipment and visual inspection systems to ensure each Mini LED PCB meets specifications and to detect and correct any potential defects or defects.
After completing the soldering, perform surface treatment to protect the outer layer of the Mini LED PCB. This may involve the application of protective coatings or special surface treatments to enhance resistance to corrosion and wear and provide additional protection.
Finally, the manufactured Mini LED PCB needs to undergo rigorous testing and verification to ensure its performance and reliability. This includes electrical testing, optical testing, and environmental and durability testing to ensure the product will perform properly under a variety of conditions.
Manufacturing Mini LED PCBs is a highly sophisticated and complex process that requires precision equipment, strict quality control, and a high level of technical knowledge. By following the key steps above, manufacturers can produce high-quality Mini LED PCBs that advance display technology and meet growing market demands.
What materials are Mini led pcb manufacturing made of?
Mini LED PCBs are typically manufactured using the following materials:
Substrate Materials: Common substrate materials include aluminum substrate, ceramic substrate, and FR-4 substrate. Aluminum substrate offers excellent heat dissipation performance, suitable for applications requiring efficient heat dissipation; ceramic substrate exhibits outstanding high-temperature resistance, suitable for high-temperature environments; FR-4 substrate is a commonly used glass fiber-reinforced epoxy substrate suitable for general LED PCB manufacturing.
Metal Foil: Copper foil is commonly used as the conductive layer of LED PCBs. Copper foil boasts good conductivity and processability, suitable for manufacturing the conductive paths of LED circuits.
Encapsulation Materials: LED chips typically need to be encapsulated to protect them from external environmental influences. Common encapsulation materials include epoxy resin, silicone gel, etc., which offer good insulation performance and high-temperature resistance.
Insulation Materials: Insulation materials used to protect circuits and prevent circuit short circuits are typically polyimide (PI) film or polyamide film. These materials exhibit good insulation performance and mechanical properties, suitable for manufacturing mini LED PCBs.
In summary, mini LED PCBs are typically manufactured using aluminum substrate, ceramic substrate, or FR-4 substrate as substrate materials; copper foil as the conductive layer material; epoxy resin, silicone gel, etc., as encapsulation materials; and polyimide film or polyamide film as insulation materials. These materials play important roles in the manufacturing of mini LED PCBs, ensuring the performance and reliability of the PCBs.
Who manufactures Mini led pcb manufacturing?
When looking for a quality Mini LED PCB supplier, it is crucial to choose a reliable manufacturer. Here are some key steps to find a reliable Mini LED PCB manufacturer:
Before choosing a manufacturer, it is crucial to conduct market research. Understanding the reputation, product quality, and customer feedback of different manufacturers will help determine the best option.
Make sure the selected manufacturer has the necessary qualifications and certifications. For example, ISO 9001 certification indicates that the manufacturer meets international quality management standards, which is an important indicator to ensure product quality.
Make sure that the manufacturer you choose can provide products that meet quality standards. It is important to understand their production processes, quality control measures, and materials and techniques used.
In addition to product quality, the service and support provided by the manufacturer are also key factors in selection. Ensure they can provide timely technical support, after-sales service and customized solutions.
Considering the manufacturer’s delivery time and cost are also important considerations in selection. Make sure they deliver the product on time and at a reasonable price.
What are 5 qualities of a good customer service?
Qualities of good customer service are crucial for maintaining customer satisfaction and loyalty. Here are five key traits:
Timely Responsiveness: Excellent customer service requires promptly addressing customer needs and issues. Responding to calls, emails, or messages promptly, resolving customer inquiries, and making them feel valued and attended to.
Professional Knowledge: Good customer service represents a deep understanding of products or services and the ability to resolve customer issues. Providing accurate, clear information, assisting customers in problem-solving, and offering professional advice and guidance.
Friendliness and Politeness: Outstanding customer service stems from friendliness and respect towards customers. Interacting with customers in a friendly, patient manner, listening to their needs and opinions, and demonstrating respect and understanding.
Personalized Care: Good customer service is based on understanding and caring for individual customer needs. Knowing customers’ preferences, purchase history, and special requirements, and providing personalized service and advice based on this information to enhance the customer experience.
Continuous Improvement: Continuously improving and optimizing customer service is crucial for maintaining competitiveness. Collecting customer feedback and suggestions, continuously refining service processes and solutions to enhance customer satisfaction and loyalty.
In summary, good customer service includes timely responsiveness, professional knowledge, friendliness and politeness, personalized care, and continuous improvement. By continuously striving to improve these aspects, customer experiences can be effectively enhanced, leading to increased customer satisfaction and loyalty.
Frequently Asked Questions (FAQs)
What are Mini LED PCBs and how do they differ from traditional PCBs?
Mini LED PCBs are advanced printed circuit boards that integrate miniature LEDs, revolutionizing display technology. Unlike traditional PCBs, Mini LED PCBs offer superior visual performance, energy efficiency, and thermal management capabilities.
What types of Mini LED PCB substrates are available?
Mini LED PCBs are commonly manufactured using organic substrates, metal core substrates, and ceramic substrates. Each substrate type offers unique characteristics tailored to specific application requirements.
What are the advantages of using Mini LED PCBs?
Mini LED PCBs offer several advantages over traditional PCBs, including enhanced brightness, improved color accuracy, energy efficiency, and space efficiency. Additionally, Mini LED PCBs provide precise lighting control and superior thermal management, ensuring optimal performance and reliability.
How is the manufacturing process of Mini LED PCBs different from traditional PCBs?
The manufacturing process of Mini LED PCBs involves additional steps such as LED placement and soldering. Advanced technologies such as automated assembly and precision laser etching are utilized to ensure high levels of accuracy and efficiency throughout the production process.
What are the key applications of Mini LED PCBs?
Mini LED PCBs find applications in various industries including televisions, monitors, automotive lighting, gaming consoles, and wearable devices. These PCBs deliver immersive visual experiences, enhanced safety features, and improved energy efficiency in a wide range of products.