Mini led PCB Substrate Manufacturer.Small size Mini LED PCBs, Ultrathin LED PCBs, Ultra-small gap LED PCBs Vendor. we offer the LED pcb from 2 Layer to 16 layers.
In today’s digital world, the rise of Mini LED technology has brought revolutionary changes to the display industry. As one of the core components supporting Mini LED technology, the manufacturing process and material selection of Mini LED PCB substrate are crucial. This article will delve into the role of Mini LED PCB substrate manufacturers and their key role in the production process. The precise design and high-quality manufacturing of Mini LED PCB substrates are crucial to achieving the efficient operation of Mini LED display technology.
What is Mini LED PCB substrate?
Mini LED PCB substrate is one of the key components of modern Mini LED display technology. It plays an important role in connecting and supporting the Mini LED chip, providing a stable platform and electrical connection for the Mini LED display. The design and material selection of this substrate are critical to the performance and stability of Mini LED displays.
Mini LED PCB substrates are usually made of specific materials to ensure they have excellent electrical conductivity and heat dissipation properties. These materials are carefully selected and processed to effectively conduct current and dissipate heat, thereby ensuring that the Mini LED chip can maintain stable temperature and electrical performance during operation. This special design and material selection enables the Mini LED PCB substrate to withstand high-frequency current and high-temperature environments, thereby ensuring the long-term stability and reliability of the Mini LED display.
In addition to providing electrical connections and heat dissipation support, the Mini LED PCB substrate also carries the arrangement and layout of the Mini LED chips. Through rationally designed circuit layout and lamination structure, Mini LED PCB substrate can minimize signal interference and electromagnetic interference, ensuring the image quality and stability of Mini LED display. At the same time, the Mini LED PCB substrate also has certain waterproof and dustproof properties to protect the Mini LED chip from the external environment.
In general, Mini LED PCB substrate is a key technical support, providing a solid foundation for the high performance and stable operation of Mini LED displays. Through precision design and selection of high-quality materials, Mini LED PCB substrate can ensure that Mini LED displays perform well in various application scenarios and provide users with a high-quality visual experience.
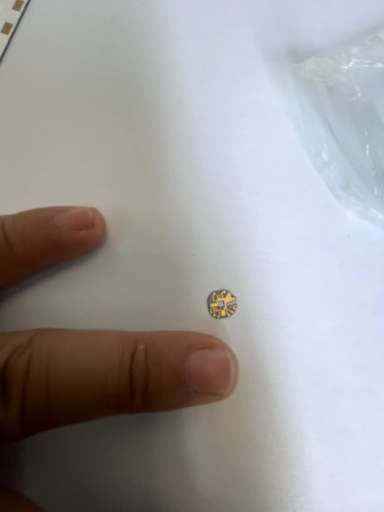
Mini led PCB Substrate
How is Mini LED PCB substrate designed?
The design of Mini LED PCB substrate is a complex and critical process, which directly affects the performance and reliability of the final product. The following will introduce the key steps of Mini LED PCB substrate design and how manufacturers ensure its performance and reliability.
Customer needs analysis: The first step in the design process is to fully communicate with customers to understand their needs and technical specifications. Manufacturers need to clearly understand the purpose, environmental conditions, electrical requirements, etc. of the Mini LED display in order to design a suitable Mini LED PCB substrate for it.
Circuit layout design: Based on customer requirements and technical specifications, manufacturers start circuit layout design. This involves arranging Mini LED chips, connectors, electrolytic capacitors and other components at appropriate locations on the PCB substrate, and designing the circuit connection method to ensure the integrity and stability of the circuit.
Material selection: During the design process, manufacturers need to select appropriate materials, including substrate material, copper foil thickness, solder mask and copper cladding thickness, etc. The selection of these materials directly affects the conductive performance, heat dissipation performance and durability of the Mini LED PCB substrate.
Stacked design: For complex Mini LED displays, manufacturers may design multi-layer PCB substrates. During the stack-up design process, they need to consider factors such as signal transmission, electromagnetic interference, and heat dissipation to ensure that connections and communications between layers operate properly.
Thermal management design: Since Mini LED chips generate a lot of heat during operation, manufacturers need to design effective heat dissipation solutions to ensure that the Mini LED PCB substrate can maintain a stable temperature during long-term operation.
Simulation and testing: After the design is completed, the manufacturer will conduct circuit simulation and prototype testing to verify the performance and reliability of the Mini LED PCB substrate. This includes circuit parameter testing, signal integrity analysis, thermal simulation, and more to identify and resolve potential issues.
Modification and optimization: Based on the simulation and test results, manufacturers may need to modify and optimize the design to further improve the performance and reliability of the Mini LED PCB substrate. This may involve layout adjustments, material replacement, optimization of heat dissipation solutions, etc.
Final confirmation: After many revisions and optimizations, the manufacturer will submit the final design plan to the customer and confirm it with the customer. After ensuring that the customer is satisfied with the design, the manufacturer will proceed to the next stage of production.
Through the above key steps, manufacturers can design Mini LED PCB substrates that meet customer needs and technical specifications, and ensure that their performance and reliability reach the best level through rigorous testing and optimization.
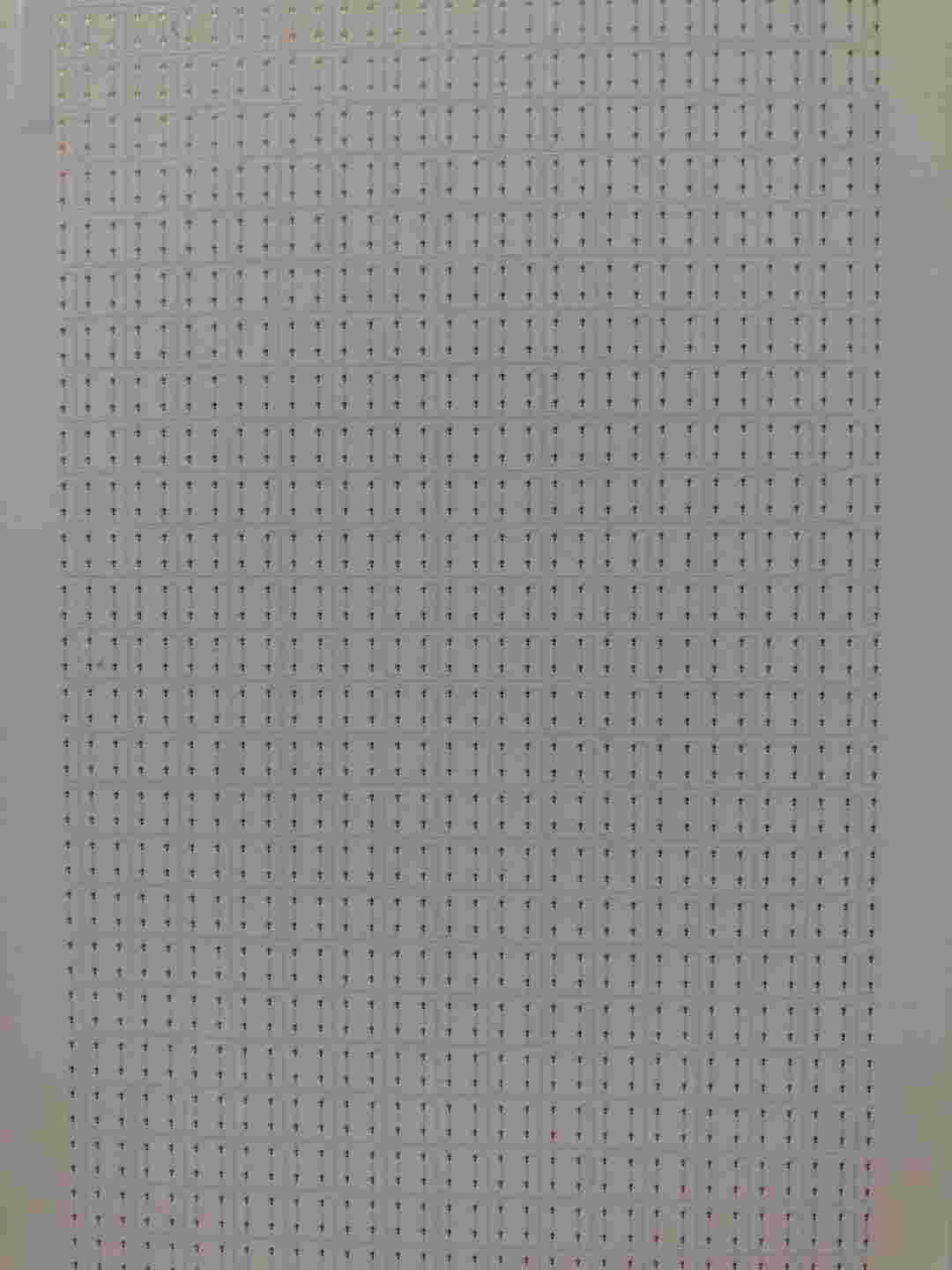
Small gap LED PCB Substrate
What is the manufacturing process of Mini LED PCB substrate?
The manufacturing process of Mini LED PCB substrate is a complex and precise process, involving multiple links, from the preparation of raw materials to the final testing. This process will be described in detail below, and how manufacturers ensure the quality of each link.
The raw materials required to manufacture Mini LED PCB substrates mainly include substrate materials (such as FR-4 fiberglass boards), conductive materials (such as copper foil), insulating materials, and chemicals (such as etching liquids, etc.). Manufacturers need to strictly select and purchase these raw materials to ensure that their quality meets standards and that they can meet customer requirements.
During the manufacturing process of printed circuit boards, manufacturers use special equipment to print designed circuit patterns onto the substrate. This step requires high-precision equipment and operations to ensure the accuracy and clarity of the circuit pattern.
Next, the substrate with the circuit pattern printed on it goes through a chemical process that involves etching and removing excess metal foil. This step requires strict control of the concentration and time of the etching solution to ensure the clarity and quality of the circuit pattern.
After etching is completed, the conductive layer on the substrate needs to be electroplated to increase its conductivity and corrosion resistance. Manufacturers will immerse the substrate in an electrolyte containing metal ions and deposit metal foil on the conductive layer through an electric current to form a uniform conductive layer.
During the drilling process, manufacturers use a laser or mechanical drill to drill holes into the substrate to install Mini LED chips and other components. This step requires high-precision equipment and technology to ensure the accuracy of aperture and location.
After drilling, the substrate needs to undergo appearance processing, including surface smoothing, gold plating, spraying, etc. This step is intended to improve the appearance quality of the substrate and prepare it for subsequent assembly and testing.
In the final stage of production, manufacturers will conduct rigorous testing on the Mini LED PCB substrate to ensure its performance and reliability. Test content includes electrical performance testing, fault detection, temperature testing, etc. Only after passing these tests can the substrate leave the factory and be delivered to the customer.
In order to ensure the quality of each manufacturing link, manufacturers need to adopt a series of strict quality control measures. This includes strict screening and inspection of raw materials, real-time monitoring and adjustment of production processes, and comprehensive testing and auditing of finished products. Through these measures, manufacturers can ensure that the quality and performance of Mini LED PCB substrates meet customer requirements and standards.
Manufacturing Mini LED PCB substrates is a precise and complex process that requires manufacturers to have advanced equipment and rich experience, as well as a strict quality management system. Only in this way can we produce high-quality and reliable Mini LED PCB substrates, providing solid support for the development and application of Mini LED display technology.
How much does it cost to manufacture Mini LED PCB substrate?
The cost of manufacturing Mini LED PCB substrate is a complex issue affected by many factors. These factors and whether a high-quality Mini LED PCB substrate will result in higher costs will be explored below.
First of all, the cost of Mini LED PCB substrate is affected by the following key factors:
Material Cost: The materials required for PCB substrate manufacturing are one of the major components of the cost. High-performance materials such as FR-4 fiberglass panels and metal substrates typically cost more than regular materials.
Manufacturing process: PCB manufacturing involves multiple complex process steps, including printing, chemical processing, electroplating, drilling, etc. High-quality manufacturing processes often require more advanced equipment and stricter quality control, which increases costs.
Scale and production capacity: Production scale and production capacity directly affect costs. Large-scale production often results in lower costs, while low-volume production may increase costs.
Technical requirements: If customers have specific technical requirements or special customization needs, manufacturers may need to invest more resources and costs to meet these requirements.
Market competition: The PCB manufacturing market is highly competitive, and prices are often affected by market supply and demand and competitor pricing strategies.
However, high-quality Mini LED PCB substrate does not necessarily mean higher cost. Conversely, high-quality substrates typically result in long-term stability and reliability, resulting in lower maintenance and replacement costs. In addition, high-quality substrates may also mean fewer failures and longer service life, reducing overall costs.
Therefore, manufacturing high-quality Mini LED PCB substrates may increase some initial costs, but in the long run, they may bring greater value and returns to customers. Therefore, when choosing a Mini LED PCB manufacturer, customers should consider factors such as cost, quality, and performance to find the most suitable solution.
What material is Mini LED PCB substrate usually made of?
In Mini LED PCB substrate manufacturing, a variety of materials are usually selected with different properties and uses. The following are some common Mini LED PCB substrate materials and their performance characteristics:
FR-4 fiberglass board: FR-4 fiberglass board is one of the most common Mini LED PCB substrate materials. It has excellent insulation properties and mechanical strength and can withstand high temperature and humidity environments. FR-4 fiberglass boards are affordable and have mature manufacturing processes, making them suitable for most application scenarios.
Metal substrate: Metal substrate is usually made of aluminum or copper materials and has good thermal conductivity and heat dissipation properties. Metal substrates are suitable for Mini LED applications that require high heat dissipation. They can effectively reduce the operating temperature of Mini LED chips and improve their performance and stability.
Aluminum substrate: Aluminum substrate is a common metal substrate material, which is lightweight and has good thermal conductivity. Aluminum substrates are relatively low-priced and suitable for some Mini LED application scenarios that do not have particularly strict heat dissipation requirements.
Ceramic substrate: Ceramic substrate has excellent insulation properties and high temperature stability, and can maintain stable performance in extreme environments. Ceramic substrates are more expensive and suitable for some Mini LED applications that require higher stability and high temperature resistance.
High molecular polymer substrate: High molecular polymer substrate is lightweight and flexible, and is suitable for some Mini LED products that have requirements on weight and shape. However, its thermal conductivity is poor and is not suitable for scenarios with high heat dissipation requirements.
When selecting Mini LED PCB substrate materials, manufacturers need to comprehensively consider various factors based on customer needs and application scenarios, such as thermal conductivity, mechanical strength, cost and processability, etc., to ensure that the final product has excellent performance and stability .
Who manufactures Mini LED PCB substrate?
Today, with the rapid development of Mini LED technology, it is crucial to manufacture high-quality Mini LED PCB substrates. So, who is responsible for manufacturing these critical components? For many companies, choosing a reliable supplier is crucial. While some companies choose to bring production in-house to ensure full control of the manufacturing process and quality control.
For many companies, choosing an experienced and professional Mini LED PCB substrate manufacturer is crucial. These manufacturers have advanced equipment and technology to provide high-quality products and customized solutions. By establishing cooperative relationships with these suppliers, the company can ensure that it obtains Mini LED PCB substrates that meet the requirements and receives timely technical support during product development and production.
For our company, it is crucial to choose a reliable Mini LED PCB substrate manufacturer. We needed a partner who could meet our specific needs, and who not only needed advanced manufacturing equipment and technology, but also had extensive experience and expertise. Our suppliers must be able to understand our needs and provide customized solutions to ensure we get products that meet our requirements.
Our company chose to cooperate with a Mini LED PCB substrate manufacturer with a good reputation. With advanced production lines and a professional team, this manufacturer is able to provide high-quality Mini LED PCB substrates and ensure that the products meet our quality standards. By establishing long-term cooperative relationships with them, we are able to obtain stable and reliable supply and receive timely technical support during product development and production.
When selecting partners, we not only consider the manufacturer’s technical strength and production capabilities, but also its service level and after-sales support. We hope to establish a long-term cooperative relationship with a manufacturer who can become our reliable partner to jointly promote the development and application of Mini LED technology.
What are the five qualities of great customer service?
When it comes to how Mini LED PCB manufacturers provide excellent customer service, it is important to ensure that they can meet their customers’ needs and provide satisfactory solutions. Here are five key attributes that ensure manufacturers can provide excellent customer service:
Responsive: Great customer service starts with a timely response. Manufacturers should respond as quickly as possible when customers have inquiries, questions or needs to show that they care about and value their customers. Fast response times build customer trust and ensure issues are resolved promptly.
Customized services: Every customer has different needs and requirements, so providing customized services is crucial. Manufacturers should listen to their customers’ needs and provide personalized solutions based on their specific application scenarios and requirements. Through customized services, manufacturers can better meet customer needs and improve customer satisfaction.
Quality Assurance: Excellent customer service must be based on high-quality products and services. Manufacturers should ensure that the Mini LED PCB substrates they offer are of excellent quality and stability to ensure long-term customer satisfaction. Through strict quality control and inspection processes, manufacturers can ensure that products meet customer standards and requirements.
Technical support: As a professional Mini LED PCB manufacturer, it is very important to provide professional technical support and guidance. Manufacturers should have a professional technical team that can provide customers with technical consultation, solution design, and problem solving support. By providing high-level technical support, manufacturers can help customers better understand and apply their products, increasing customer satisfaction and trust.
After-sales service: Excellent customer service includes not only the sales process of the product, but also after-sales service. Manufacturers should provide timely after-sales support and services to help customers solve problems and difficulties encountered during use. Whether providing remote technical support, product repair or replacement, manufacturers should ensure that customers receive timely help and support at all times.
To sum up, excellent customer service is crucial for Mini LED PCB manufacturers. Through five key attributes such as responsiveness, customized service, quality assurance, technical support and after-sales service, manufacturers can ensure that they can meet the needs of customers and provide a satisfactory customer service experience.
FAQS
How long is the production cycle of Mini LED PCB substrate?
The production cycle is affected by factors such as order volume, manufacturer’s production capacity, and current market demand. Generally speaking, the production cycle for small-scale orders may be completed within a few days, while large-scale orders may take several weeks. Manufacturers usually provide the exact production lead time after order confirmation.
What is the best material for Mini LED PCB substrate?
The best material depends on the specific application, requirements, and budget constraints. Common Mini LED PCB substrate materials include FR-4 fiberglass board, metal substrate, etc. FR-4 fiberglass boards have good insulation properties and workability and are suitable for most application scenarios; while metal substrates have excellent heat dissipation properties and are suitable for scenarios with high heat dissipation requirements. Manufacturers usually provide corresponding suggestions and options based on customer needs.
How to calculate the cost of Mini LED PCB substrate?
The cost of Mini LED PCB substrate is affected by multiple factors, including material cost, manufacturing process, scale and market competition. Normally, high-quality Mini LED PCB substrates tend to have higher costs, but will also bring longer-term stability and reliability to customers. When customers choose Mini LED PCB manufacturers, they should comprehensively consider price, quality, service and other factors to ensure that they choose the most suitable manufacturer.
How to ensure the quality of Mini LED PCB substrate?
Manufacturers usually ensure the quality of Mini LED PCB substrates through strict quality control processes. This includes rigorous screening and testing of raw materials, quality monitoring during production, and comprehensive testing of final products. Manufacturers usually continuously improve their quality management systems to ensure stable and reliable product quality.
What are the application ranges of Mini LED PCB substrate?
Mini LED PCB substrates are widely used in various display devices, including televisions, display screens, electronic signs, automotive display systems, etc. Because Mini LED technology has the advantages of high brightness, high contrast, and low energy consumption, it has broad application prospects in indoor and outdoor display applications.