Mini LED Substrate manufacturing . Black substrate(base), black solder mask, white substrate(base), white solder mask, The finished LED PCB is available in two colors, and we also can do the microtrace and smallest gap.
Mini LED (micro light-emitting diode) substrate manufacturing refers to the key process that provides support for Mini LED display technology. In the field of modern electronics, Mini LED technology is widely used in various display devices, such as TVs, mobile phones, and display screens. The fabrication of Mini LED substrates is one of the key steps to achieve high resolution, high brightness and high contrast for these devices. It not only provides a stable mounting platform for Mini LED chips, but also provides necessary support for circuit connection and signal transmission. Therefore, Mini LED substrate manufacturing is of extremely important significance in the field of modern electronics.
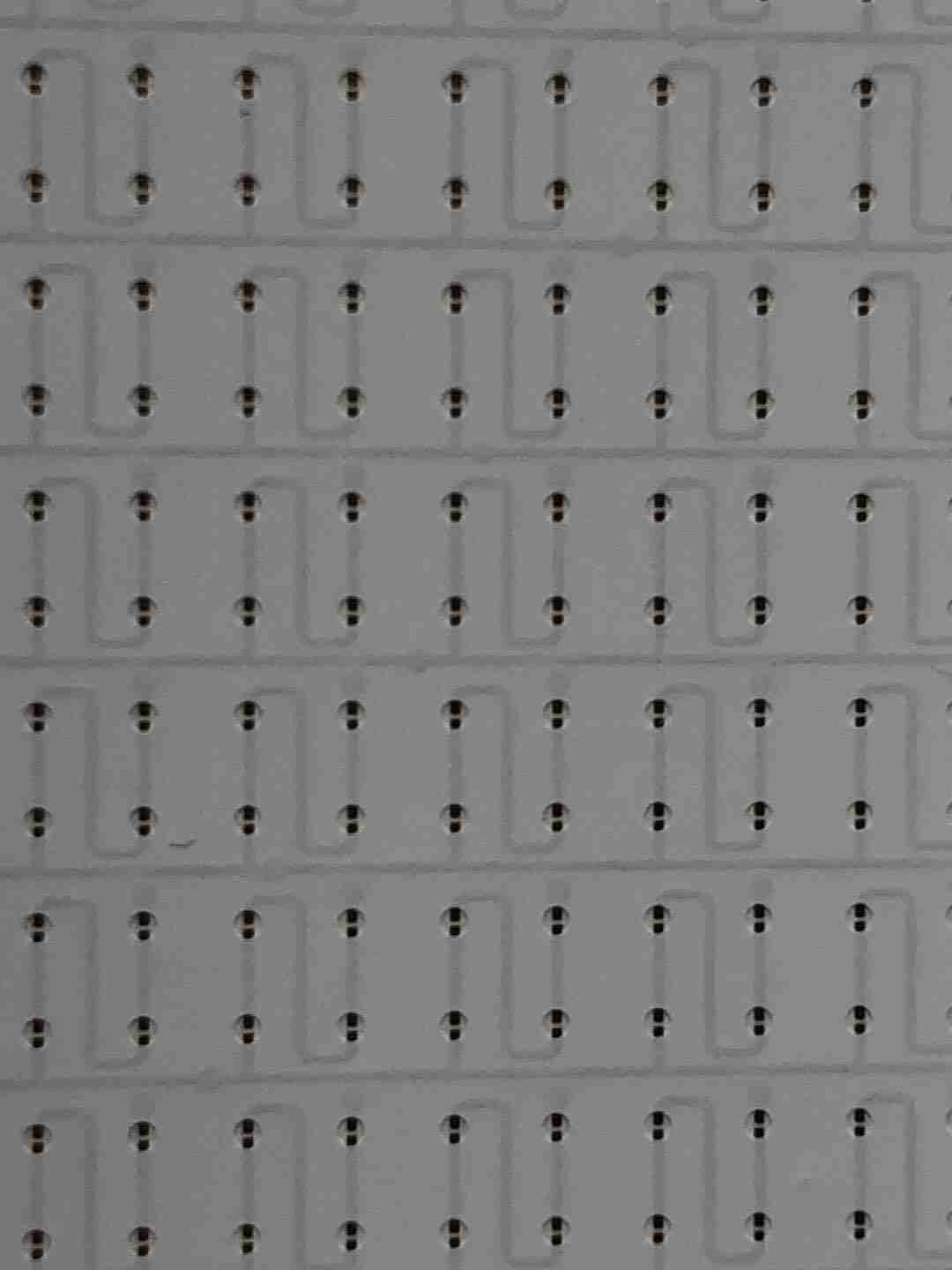
white base white soldermask LED PCBs( pad to pads gap are 2.2mil)
What is Mini LED substrate?
Mini LED substrate is an indispensable and important component of modern electronic equipment. It carries Mini LED chips and provides electrical connections. It is the core support of Mini LED display technology. Let’s dive into the definition and functions of Mini LED substrates.
Mini LED substrate is a thin sheet based on semiconductor material, usually composed of fiberglass reinforced epoxy resin (FR-4) or metal substrate. Its main function is to provide mechanical support and electrical connection for Mini LED chips so that they can work properly and be integrated into displays or other devices.
In Mini LED display technology, Mini LED substrate plays a key role. Mini LED chips are usually very small, and the design of Mini LED substrates needs to take into account the precise size and layout of these chips. One of the main tasks of the Mini LED substrate is to hold these tiny Mini LED chips in the correct position and ensure that the electrical connections between them are functioning properly.
Mini LED substrate connects Mini LED chips through circuit connections or wires. These wires are usually made of metallic materials, such as copper or silver, and are printed or etched onto the surface of the substrate to form a complex circuit network. These wires are not only responsible for connecting the Mini LED chips, but also provide a transmission path for power and control signals to ensure the normal operation of the Mini LED display.
In addition, the Mini LED substrate uses a special packaging process to protect the Mini LED chip from damage to the external environment. This kind of packaging usually uses materials such as epoxy resin or silicone to wrap the Mini LED chip in it while maintaining its fixed position on the substrate.
In general, Mini LED substrate is a key electronic component. It provides necessary support and connections for Mini LED chips, and ensures the stable operation of Mini LED display technology through circuit connections. As Mini LED technology continues to develop, the design and manufacturing of Mini LED substrates will continue to evolve to meet growing market demands and technical challenges.
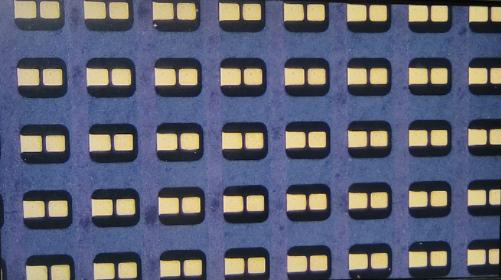
Black base and black soldermask LED PCBs. ( pads to pads gap are 2.4mil)
How to design Mini LED substrate?
Designing Mini LED substrate is one of the key steps in realizing Mini LED display technology. Its design quality directly affects the performance and reliability of the final product. The following will introduce in detail the key steps of Mini LED substrate design and the factors that need to be considered during the design process.
Layout design: When designing a Mini LED substrate, you first need to carry out layout design. This involves determining the location and layout of the Mini LED chip, as well as the arrangement of other electronic components (such as resistors, capacitors, etc.). Reasonable layout design can optimize the Mini LED display effect to the greatest extent and ensure the stability and reliability of the circuit.
Circuit connection: Another key step in designing Mini LED substrate is to determine the circuit connection method. This includes determining the circuit topology, signal transmission paths, and power supply methods. In circuit connection design, factors such as signal transmission stability, anti-interference ability, and power consumption management need to be taken into consideration.
Heat dissipation design: Mini LED chips will generate a certain amount of heat during work, so good heat dissipation design is crucial to ensure the stability and reliability of the Mini LED substrate. During the design process, the selection of heat dissipation materials, the design of the heat dissipation structure, and the optimization of the heat dissipation path need to be considered to effectively reduce the operating temperature of the Mini LED chip.
Electromagnetic compatibility (EMC) design: When designing Mini LED substrates, electromagnetic compatibility (EMC) issues need to be considered to ensure that the Mini LED display will not interfere with the surrounding environment and other electronic equipment, and can also withstand external Effects of interference. This involves circuit shielding design, ground wire design, and the use of filters.
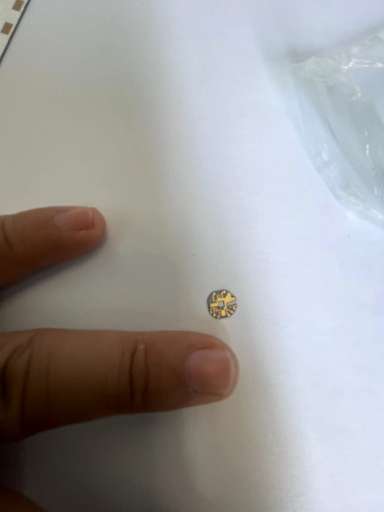
Mini LED Substrate
Key steps in Mini LED substrate manufacturing
The manufacturing of Mini LED substrates is a complex and precise process involving multiple key steps, each of which is crucial and directly affects the quality and performance of the final product. Let’s take a closer look at these key steps:
Substrate selection: First, choosing the right substrate material is crucial. Common substrate materials include fiberglass reinforced epoxy resin (FR-4), metal substrates, etc. Different substrate materials have different thermal conductivity, mechanical strength and electrical properties, so they need to be selected based on specific application requirements.
Photolithography patterning: Using photolithography technology to create metal electrode patterns on a selected substrate. These electrode patterns will be used to connect the Mini LED chips to ensure smooth transmission of current to each LED.
Welding and packaging: Weld the Mini LED chip to the substrate and package it. The welding process requires a high degree of precision to ensure the correct positioning and solid connection of the LED chips. Encapsulation is to protect the LED chip from the external environment and improve its durability and stability.
Inspection and testing: After manufacturing is completed, it is crucial to conduct strict inspection and testing of the Mini LED substrate. Through visual inspection, electrical performance testing, durability testing and other means, we ensure that each manufactured substrate meets the specification requirements and can work stably and reliably.
Surface Preparation: The last critical step is surface preparation. After the Mini LED substrate is manufactured, its surface is treated to protect the metal electrode pattern, prevent oxidation, and provide a good soldering surface. This step directly affects the reliability and durability of the Mini LED substrate.
Through the above key steps, the entire process of Mini LED substrate manufacturing is completed. Each step plays an irreplaceable role and is connected with each other to ensure the quality and performance of the final product. For electronic product manufacturers and consumers, understanding the importance of these steps is crucial to selecting a suitable Mini LED substrate supplier and ensuring product quality.
Mini LED substrate manufacturing cost
What is the manufacturing cost of Mini LED substrate? This is a key issue that affects the total cost and market competitiveness of Mini LED displays. The manufacturing cost of Mini LED substrate is mainly affected by the following factors:
Substrate material cost: Mini LED substrates usually use glass fiber reinforced epoxy resin (FR-4), metal substrates, etc. as substrate materials. The cost of different materials varies greatly, which directly affects the final manufacturing cost.
Manufacturing process complexity: The manufacturing of Mini LED substrates involves multiple process links such as photolithography, welding, and packaging. The higher the complexity, the greater the equipment, labor, and time costs required.
Quantity requirements: There is a significant difference in costs between mass production and low-volume production. Typically, unit costs gradually decrease as production scale increases.
Technical requirements: Some special technical requirements, such as high-precision photolithography, use of special materials, etc., will increase manufacturing costs.
Labor and equipment costs: The manufacturing of Mini LED substrates requires a lot of labor and equipment investment. Labor costs and equipment maintenance costs will directly affect the level of manufacturing costs.
Design complexity: The design complexity of Mini LED substrate will also have an impact on cost. Designing simple substrates usually costs less, while designing complex substrates requires more resources.
To sum up, the manufacturing cost of Mini LED substrate is affected by many factors. Reasonable evaluation and control of these factors can effectively reduce the total cost of Mini LED displays and improve market competitiveness.
Materials in Mini LED substrate manufacturing
Mini LED substrate is one of the core components of Mini LED display technology, and the selection of its manufacturing materials is crucial. Typically, Mini LED substrates are composed of a variety of materials, each with unique characteristics and uses.
The main supporting material of Mini LED substrate is usually fiberglass reinforced epoxy resin (FR-4) or metal substrate. FR-4 material has good insulation properties and mechanical strength and is suitable for most application scenarios. Metal substrates have excellent thermal conductivity and are suitable for occasions with high heat dissipation requirements.
The electrodes on the Mini LED substrate are usually made of metal materials with good electrical conductivity, such as copper or aluminum. These materials have good electrical conductivity and corrosion resistance, ensuring stable and reliable electrical connections.
Mini LED chips are usually packaged using materials such as epoxy resin or silicone. These materials have good heat resistance and corrosion resistance, and can effectively protect Mini LED chips and improve their service life and stability.
The solder contact material on the Mini LED substrate is usually tin or lead-tin alloy. These materials have good welding properties and conductive properties, which can ensure good electrical connections and improve the performance and stability of Mini LED displays.
The surface of Mini LED substrate usually needs to be treated to improve its welding performance and corrosion resistance. Commonly used surface treatment materials include gold plating, tin plating, etc. These materials can effectively prevent oxidation of metal electrodes and ensure stable and reliable welding connections.
To sum up, the materials used in Mini LED substrate manufacturing are diverse and have their own characteristics. Reasonable selection and application of these materials can ensure the performance and reliability of Mini LED displays.
Who makes Mini LED substrates?
In the field of Mini LED substrate manufacturing, finding reliable suppliers is crucial. For many companies, choosing a supplier not only means establishing a long-term relationship with them, but is also a key factor in ensuring product quality and performance. So, who makes Mini LED substrates? Let’s take a closer look.
Many companies choose to set up dedicated Mini LED substrate manufacturing teams in-house to ensure complete control and supervision of the manufacturing process. This approach allows the company to customize production according to its own needs and standards, and to adjust the production process in a timely manner to adapt to changes in market demand.
One of the main advantages of manufacturing Mini LED substrates in-house is the ability to better control product quality and performance. The company can produce according to its own standards and requirements, ensuring that each Mini LED substrate meets the company’s quality standards. In addition, in-house production can also reduce communication costs and time with external suppliers and improve production efficiency and flexibility.
Companies that manufacture Mini LED substrates in-house usually have rich technical expertise and innovation capabilities. They can use their technical advantages to develop new manufacturing processes and materials to improve the performance and reliability of Mini LED substrates. Through continuous technological innovation, these companies can maintain a competitive advantage in the market and meet customer demands for high-quality Mini LED substrates.
Since the Mini LED substrate is manufactured by our company, the company can provide better quality assurance and after-sales service. They can respond more promptly to customer questions and feedback and provide customized solutions to meet customers’ specific needs. This close partnership helps establish long-term and stable relationships and promotes the company’s business growth.
Overall, companies that choose to manufacture Mini LED substrates in-house can provide customers with better product quality and service experience. By giving full play to their technological advantages and innovation capabilities, these companies can meet customers’ needs for high-performance Mini LED substrates and maintain a competitive advantage in the market. Therefore, for many companies, choosing to manufacture Mini LED substrates in-house is a wise choice.
Five Characteristics of Great Customer Service
For any business, providing excellent customer service is key to ensuring customer satisfaction and loyalty. Here’s a look at the five key characteristics of great customer service and how you can use them to ensure customer satisfaction and loyalty.
Responsive: Quality customer service always prioritizes rapid response to customer needs and questions. Whether it’s a phone call, email, or message on social media, customers expect a prompt response. By establishing effective communication channels and response mechanisms, companies can quickly respond to customers’ various needs, thereby enhancing customer trust and satisfaction. Responding to customers in a timely manner can also reduce customer waiting time and improve customer experience and feelings.
Empathy: Excellent customer service requires starting from the customer’s perspective and truly understanding their needs and feelings. By listening to customers’ opinions and suggestions and understanding their pain points and needs, companies can better meet customer expectations and provide personalized solutions. Showing empathy and understanding when handling customer complaints and issues can increase customer trust and loyalty to the business, thereby increasing customer satisfaction.
Reliability: Reliability is one of the important characteristics of good customer service. Customers want to be able to rely on companies to provide stable and reliable products and services. Therefore, companies need to consistently deliver on their promises to ensure the stability and reliability of product quality and service levels. By establishing an effective quality management system and after-sales service system, companies can improve product reliability and enhance customer trust and loyalty.
Open communication: Good communication is the key to great customer service. Enterprises need to maintain close communication with customers and deliver product information, service updates, promotions and other information in a timely manner to enhance customers’ sense of participation and belonging. By establishing multiple communication channels, such as phone, email, social media, etc., companies can establish closer connections with customers and better understand customer needs and feedback, thereby improving customer satisfaction and loyalty.
Problem Solving: Excellent customer service requires proactive resolving of customer problems and difficulties. Customers may encounter various problems when using products and services, and companies need to respond promptly and provide effective solutions to ensure customer satisfaction and loyalty. By establishing a complete after-sales service system and complaint handling mechanism, companies can better solve customer problems, enhance customer trust and loyalty, and thereby improve customer satisfaction.
To sum up, quality customer service has five characteristics: responsiveness, empathy, reliability, smooth communication and problem solving. By following these characteristics, companies can effectively improve customer satisfaction and loyalty, enhance market competitiveness, and achieve sustainable development.
FAQS
What is the difference between Mini LED and traditional LED technology?
Mini LED technology involves smaller LED chips compared to traditional LEDs, allowing for higher pixel density and improved display performance. Mini LEDs also offer better control over local dimming, resulting in enhanced contrast and color accuracy.
How does Mini LED substrate manufacturing differ from conventional PCB manufacturing?
Mini LED substrate manufacturing requires specialized processes to accommodate the smaller size and higher density of Mini LED components. This includes precise placement of conductive traces, advanced materials for heat dissipation, and tighter quality control measures to ensure optimal performance.
What are the advantages of Mini LED substrate manufacturing?
Mini LED substrate manufacturing enables the production of displays with higher resolution, brightness, and contrast ratio compared to traditional LCDs. It also offers greater energy efficiency and longer lifespan, making it ideal for applications requiring superior image quality and reliability.
What challenges are associated with Mini LED substrate manufacturing?
Challenges in Mini LED substrate manufacturing include achieving uniformity in LED placement and brightness, managing heat dissipation effectively, and ensuring consistency in color and brightness across the display. Additionally, the complexity of the manufacturing process may result in higher production costs.