Minimum Clearance PCB Manufacturer , we mainly produce ultra-small bump pitch substrate, ultra-small trace and spacing packaging substrate.
With the continuous development of electronic equipment, PCB (Printed Circuit Board), as one of its core components, plays a vital role. In modern electronic manufacturing, minimum clearance PCB has become one of the focuses of attention. This technology not only plays an important role in the design and manufacturing of electronic equipment, but also directly affects the performance, reliability and stability of the equipment. Through an in-depth discussion of minimum gap PCB, we can better understand its key role in improving the performance of electronic equipment and provide stronger support for future electronic technology development.
What is Minimum Clearance PCB?
Minimum clearance PCB (Printed Circuit Board) is a key technology in circuit board design and manufacturing, aiming to improve electrical performance and reliability. In modern electronic equipment, the stability and reliability of signal transmission are critical to overall performance. Therefore, by adopting minimum gap PCB technology, you can effectively ensure that minimal gaps are maintained between wires, holes, and other components on the circuit board to minimize signal interference and cross-coupling.
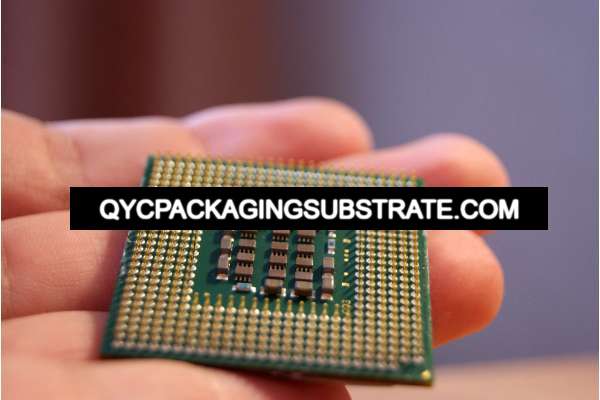
Minimum Clearance PCB Manufacturer
In minimum gap PCB technology, designers need to precisely control the distance between wires to avoid signal waveform distortion or data transmission errors. By reducing the gaps between components, crosstalk and delay during signal transmission can be reduced, and the bandwidth and speed of the circuit can be increased. This technology requires a certain level of manufacturing precision and material quality of circuit boards to ensure the performance stability of the final product.
In the minimum gap PCB design, factors such as circuit layout, ground and power line layout, and inter-layer distance also need to be considered. Reasonable layout design can reduce the length of signal transmission paths and interference sources, further improving the stability and reliability of the circuit.
Minimum gap PCB technology is not only suitable for high-speed circuit board design, but also suitable for most electronic equipment, including communication equipment, computers, medical equipment, etc. By using minimum gap PCB technology, it can ensure that the equipment can work stably and reliably under various environmental conditions, while improving the performance and life of the equipment.
In summary, minimum gap PCB technology is of great significance in modern electronic manufacturing. It can not only improve the performance and reliability of circuit boards, but also provide better solutions for the design and manufacturing of various electronic devices.
Minimum Clearance PCB design Reference Guide.
When designing a minimum clearance PCB, there are several key factors that need to be considered to ensure optimal board performance. Here are some design reference guides to help designers effectively create high-performance, minimum-clearance PCBs:
Circuit layout
Good circuit layout is one of the keys to ensuring minimum clearance PCB performance. During the design stage, designers should plan the circuit layout reasonably to avoid signal crossover and interference, and reduce the length and complexity of the signal path as much as possible. In addition, taking into account the minimum clearance requirements, components need to be positioned appropriately to ensure that the distance between them meets the design specifications.
Material selection
Choosing the right materials is critical to minimum clearance PCB design. Designers should choose substrate materials with excellent electrical properties and heat resistance, such as FR-4 fiberglass boards or high-frequency materials. In addition, metal substrates are also a good choice for applications requiring higher performance and reliability. When selecting materials, you also need to consider their compatibility with the environment and durability.
Interlayer distance
The interlayer distance refers to the separation distance between different layers of the PCB board. In minimum gap PCB design, reasonable setting of inter-layer distance can effectively reduce signal crosstalk and interference, and improve signal integrity and reliability. Designers should determine the inter-layer distance based on specific requirements and application scenarios to ensure that it meets design specifications and performance requirements.
Best Practices
Designers should follow some best practices when designing minimum clearance PCBs to ensure successful implementation of the design. This includes using advanced design tools and software for simulation and verification, timely prototype testing and revisions, and working closely with manufacturers to ensure design manufacturability and reliability. In addition, designers should pay close attention to industry standards and specifications to ensure that designs comply with relevant requirements and standards.
By comprehensively considering the above factors and following best practices, designers can effectively create high-performance and reliable minimum-clearance PCBs, providing reliable technical support for performance improvement and applications of electronic devices.
What material is used in Minimum Clearance PCB?
When it comes to the materials used in minimum gap PCBs, the key is to choose a high-quality substrate material that is suitable for the circuit requirements. These materials play a vital role in ensuring stable electrical performance and excellent thermal management capabilities of circuit boards.
First, FR-4 fiberglass board is one of the most common substrate materials. It is composed of fiberglass cloth and epoxy resin and has good mechanical strength and heat resistance. FR-4 fiberglass boards are suitable for a variety of application scenarios and are relatively low cost, so they are widely used in most minimum clearance PCB designs. One of its advantages is that it provides reliable insulation performance and prevents signal interference and short circuits in the circuit.
Another common substrate material is metal substrate. Metal substrates improve thermal conductivity by coating a metal layer on the surface of the substrate. This material is typically used in applications that require higher thermal conductivity, such as high-power electronics or situations where frequent heat dissipation is required. The metal substrate can effectively conduct heat away from the circuit and ensure the normal operating temperature range of circuit components, thus improving the stability and reliability of the entire system.
Regardless of the material chosen, the design and manufacturing of minimum clearance PCBs must strictly follow industry standards and quality control processes. This includes ensuring smoothness and flatness of the substrate surface, as well as avoiding material defects and poor connections during the manufacturing process. By selecting appropriate substrate materials and strictly controlling quality during the manufacturing process, minimum gap PCBs can be ensured to provide stable and reliable performance under various environmental conditions.
When designing minimum clearance PCBs, design engineers should select the most appropriate substrate material based on specific application needs and performance requirements. This will help ensure that the circuit board can operate stably and reliably under various operating conditions, providing strong support for the performance of electronic equipment.
What size are Minimum Clearance PCB?
When it comes to minimum clearance PCB size, it is actually a fairly flexible concept. Dimensions are typically established based on specific application requirements and industry standards to ensure versatility across a variety of devices while meeting performance and reliability requirements.
First, let’s consider industry standards. For common electronic equipment, the industry usually establishes some standard sizes so that various components and devices can be compatible and interchangeable with each other. These standard sizes usually take into account factors such as the size of the electronic device, heat dissipation requirements, signal transmission distance, etc., so as to save as much space as possible while ensuring functional integrity.
Additionally, the size of the minimum clearance PCB will vary based on specific application requirements. For example, for some high-density electronic equipment, a smaller PCB may be required to accommodate more electronic components; while for some industrial equipment or aerospace applications, more emphasis may be placed on the stability and durability of the PCB. performance, so a larger size PCB will be chosen to accommodate more connection points and strengthen the structure.
In practical applications, designers and engineers will determine the minimum clearance PCB size based on specific project requirements. They will consider factors such as the layout of electronic components, heat dissipation requirements, signal transmission distance, and mechanical structure, and design and manufacture based on industry standards. This ensures that the final product reaches the best level in terms of performance and reliability, while also being able to adapt to the needs of different environments and application scenarios.
To sum up, the size of the minimum clearance PCB is a concept that is affected by industry standards and flexibly changes according to specific application requirements. Through reasonable design and manufacturing, minimum gap PCB can provide high-performance and reliable solutions for various electronic devices, thereby promoting the continuous development and innovation of electronic technology.
The Manufacturer Process of Minimum Clearance PCB.
The manufacturing process of minimum gap PCB is a complex and delicate process that involves multiple critical steps, each of which has a significant impact on the quality and performance of the final product.
First, design verification is the starting point for manufacturing minimum clearance PCBs. At this stage, the designer converts the circuit diagram into an actual PCB layout and performs verification to ensure the accuracy and feasibility of the design. By using CAD software for simulation and simulation, designers can check whether the circuit layout meets the minimum clearance requirements and correct possible problems.
Next comes the printing stage. At this stage, the PCB design pattern will be printed onto the substrate. Photolithography technology is usually used to transfer the design pattern to the copper-clad substrate layer by layer. This process requires high-precision equipment and precise operations to ensure printing accuracy and consistency.
Plating is one of the key steps in minimum gap PCB manufacturing. After printing, the copper-clad substrate needs to be increased in thickness through an electroplating process and a uniform copper layer is formed on the surface. This not only improves the conductivity of the PCB, but also protects the circuit from environmental corrosion. Control of the plating process is critical to ensure consistency and quality with minimal gaps.
The last step is the shaping stage. At this stage, the PCB will be cut to the required size and necessary processing such as drilling and cutting will be performed. The quality of molding directly affects the final appearance and performance of the PCB, so high-precision equipment and skilled operators are required to complete this process.
To sum up, the manufacturing process of minimum gap PCB involves multiple key steps such as design verification, printing, plating and molding. Each step requires a high level of precision and technology to ensure the final product is of excellent quality and performance. Only when every link is strictly controlled and optimized can minimum gap PCB products that meet the highest standards be produced.
The Application area of Minimum Clearance PCB.
Minimum gap PCB has a wide range of applications, and its high performance and reliability make it an ideal choice for communications, medical, automotive, aerospace and other fields.
In the field of communication, minimum gap PCB is widely used in various communication equipment, such as base stations, routers, switches, etc. These devices require stable signal transmission and highly integrated circuit design, and minimum clearance PCB can provide high-density circuit layout and excellent signal integrity to ensure the performance and stability of communication equipment.
In the medical field, minimum clearance PCBs are used in various medical equipment, including medical monitoring equipment, diagnostic instruments, medical imaging equipment, etc. These devices have extremely high requirements on circuit reliability and stability, and minimum clearance PCB can provide highly reliable circuit design and stable signal transmission, thereby ensuring the accuracy and reliability of medical equipment.
In the automotive field, minimum clearance PCBs are widely used in automotive electronic control units (ECUs), in-car entertainment systems, driving assistance systems, etc. With the continuous improvement of automobile electronics, the requirements for circuit integration and stability are getting higher and higher. Minimum gap PCB can meet these requirements and provide stable and reliable electronic solutions for automobile electronic systems.
In the aerospace field, minimum clearance PCBs are used in various aerospace equipment, including flight control systems, navigation systems, communication systems, etc. These devices have extremely high requirements on the anti-interference ability and stability of the circuit, and the minimum gap PCB can provide excellent anti-interference performance and stable signal transmission, thereby ensuring the safety and reliability of aerospace equipment.
In short, the application of minimum gap PCB is not limited to specific industries, but covers a wide range of needs in various fields. Its high performance and reliability make it an ideal choice for various electronic devices, providing important support for the development of modern technology.
What are the advantages of Minimum Clearance PCB?
Minimum gap PCB (Printed Circuit Board) is a key technology in today’s electronic equipment manufacturing field, which has significant advantages in improving the performance and reliability of electronic equipment. Compared with traditional PCB, minimum gap PCB has higher density, better signal integrity and stronger anti-interference ability, thus bringing revolutionary changes to the development of electronic equipment.
First, minimum gap PCB has a higher density than traditional PCB. In traditional PCB design, the spacing between wires and components is relatively large, causing the circuit board to occupy a large space and limiting the overall size and complexity of electronic equipment. The minimum gap PCB uses advanced manufacturing technology and materials to achieve a more compact circuit layout, greatly increasing the wiring density of the circuit board, making electronic devices lighter and more portable.
Secondly, minimum clearance PCBs have better signal integrity. In traditional PCBs, signal transmission may be affected by insufficient wiring spacing and electromagnetic interference, resulting in signal attenuation, distortion or even loss. By optimizing the wiring design and using high-quality materials, the minimum gap PCB can effectively reduce the loss and interference in signal transmission, ensure stable signal transmission, and improve the performance of electronic equipment.
In addition, minimum gap PCB has stronger anti-interference ability. In modern electronic equipment, due to the increasing integration of electronic components, there are more and more interference sources inside the equipment. Traditional PCB may cause device performance degradation due to unreasonable circuit layout or large interference between lines. Through optimized design and material selection, the minimum gap PCB can effectively isolate different signal lines, reduce the spread of interference, improve the anti-interference ability of the equipment, and ensure the stable operation of the equipment.
To sum up, minimum gap PCB has higher density, better signal integrity and stronger anti-interference ability than traditional PCB. These advantages not only improve the performance of electronic equipment, but also enhance the reliability of the equipment. and stability. With the continuous advancement of science and technology and the continuous development of the electronic equipment market, minimum gap PCB technology will play an increasingly important role in the future and become one of the key technologies for electronic equipment manufacturing.
FAQ
How is a minimum clearance PCB different from a regular PCB?
Compared with conventional PCB, minimum gap PCB has stricter spacing and size requirements during the design and manufacturing process. This enables minimum gap PCBs with higher density and better signal integrity, enabling more complex circuit layouts in smaller spaces, improving the performance and reliability of electronic equipment.
What application scenarios are minimum clearance PCB suitable for?
Minimum clearance PCB is suitable for a variety of application scenarios that require high-performance and high-reliability electronic solutions, including communication equipment, medical equipment, automotive electronics, aerospace, etc. In these fields, there are extremely high requirements for the density of circuit layout and the stability of signal transmission, and minimum gap PCB can meet these needs.
Is the manufacturing process of minimum clearance PCB complicated?
Yes, the manufacturing process of minimum gap PCB is more complicated than that of conventional PCB. At every manufacturing step, size and spacing need to be strictly controlled to ensure the quality and performance of the final product. In addition, meticulousness in the manufacturing process is also key to ensuring minimum gap PCB reliability.
How to ensure the quality of minimum clearance PCB?
In order to ensure the quality of minimum gap PCBs, manufacturers need to strictly implement quality management systems and use high-quality raw materials and advanced manufacturing equipment. In addition, strict control and continuous monitoring during the manufacturing process are also critical steps to ensure product quality.