Minimum spacing PCB manufacturer. Ultra-small gap BGA substrates, Smallest gap LED PCBs, and High speed and high frequency material HDI PCBs,We offer minimum clearance PCB from 2 layer to 30 layers.
In the world of minimum pitch PCB manufacturing, we will explore exciting areas! Printed circuit boards (PCBs) are the backbone of modern electronics, enabling the seamless flow of power and data by etching or printing conductive paths on a non-conductive substrate. In this guest post, we’ll take a deep dive into the process, materials, and cost factors of minimum pitch PCB manufacturing. By understanding this key information, readers will better understand how to succeed in the field of minimum pitch PCB manufacturing and play an important role in the development of high-performance electronic devices.
What is a Minimum spacing PCB ?
Minimum pitch PCB is an important part of electronic equipment. It provides a platform for electronic components to connect circuits and transmit power and data through conductive paths. It not only provides mechanical support but also enables electrical connections between electronic components. As one of the key components of modern electronic technology, minimum pitch PCB plays a vital role in various electronic devices.
First, minimum pitch PCBs provide physical support and connections for electronic components. On a PCB, wires, connection points, and electronic components are connected to each other through wire patterns to form a complete circuit. These wires and connection points are tightly laid out, allowing PCBs to accommodate a large number of electronic components and enable highly integrated circuit designs where space is limited. Therefore, the minimum pitch PCB can be regarded as the “nerve center” of electronic equipment, organically connecting various components together.
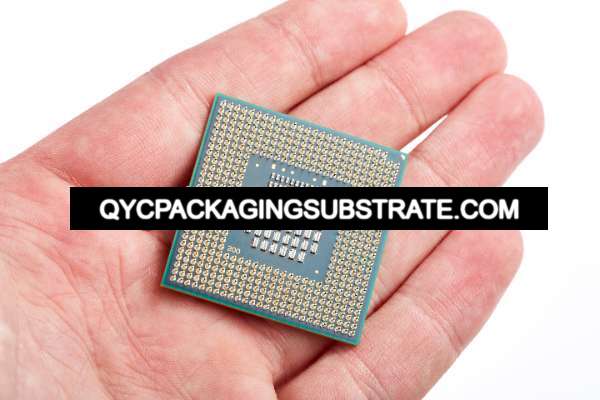
Minimum spacing Minimum spacing PCB manufacturer
Secondly, the minimum pitch PCB enables the transmission of power and data. Through the wire paths on the PCB, current can flow between various electronic components, enabling power transmission. At the same time, data signals can also be transmitted through wires on the PCB to achieve communication between different components. This power and data transmission function makes PCB the core of data processing and control in modern electronic equipment.
In addition to providing mechanical support and enabling electrical connections, minimum pitch PCBs also have other important functions and characteristics. For example, PCB layout and design can be optimized based on specific application needs to ensure circuit performance and stability. In addition, PCBs are highly reliable and stable and can operate stably for a long time under various environmental conditions. This makes PCB widely used in various fields, including consumer electronics, communications, medical and industrial control.
In general, as an important part of electronic equipment, minimum pitch PCB not only provides mechanical support and electrical connections, but also realizes the transmission of power and data. It plays a vital role in modern electronic technology, promoting the continuous progress and innovation of science and technology.
How to Design a Minimum spacing PCB ?
Designing a minimum pitch PCB involves multiple key steps, each of which is critical and affects the quality and performance of the final product. Here are the main steps for designing a minimum pitch PCB:
Schematic design is the starting point for PCB design. At this stage, engineers need to translate the functional requirements of the circuit into a graphical circuit diagram. They use professional circuit design software, such as Altium Designer or Cadence Allegro, to create circuit diagrams and add the required electronic components.
During the component placement stage, engineers place electronic components into the PCB layout to meet design requirements and space constraints. When placing components, they need to consider circuit connectivity, signal transmission paths, and factors such as heat dissipation and EMI (electromagnetic interference).
Wiring is the process of connecting electronic components, which directly affects the performance and reliability of PCB. Engineers need to ensure signal integrity and stability during the wiring process to avoid signal interference and crosstalk. In minimum pitch PCB design, wiring requires special attention to the distance between wires and impedance control.
After the design is completed, engineers usually make a prototype of the PCB for verification. Prototyping involves converting the design into an actual PCB board, assembling and testing the prototype. Through the prototyping stage, engineers can discover and solve problems in the design and make necessary modifications and optimizations.
During these steps, engineers use professional software to assist in design and verification, ensuring that the PCB layout meets electrical and mechanical requirements. Through careful design and strict control, minimum pitch PCB can achieve excellent performance and reliability to meet the requirements of modern electronic equipment.
What is the Minimum spacing PCB Fabrication Process?
Minimum pitch PCB manufacturing involves multiple key stages, each of which is critical and has a direct impact on the quality and reliability of the final product. Below we describe these stages in detail:
In the minimum pitch PCB manufacturing process, the substrate needs to be prepared first. The substrate is usually made of non-conductive material, such as FR4 fiberglass board. At this stage, the substrate is cleaned and cut to the required size, ensuring a smooth surface for subsequent process steps.
Layer alignment is a critical step to ensure alignment accuracy between different layers. In multi-layer PCB manufacturing, the patterns on each layer need to be precisely aligned to ensure the correct connection of the wires. This is usually achieved through optical equipment and alignment marks.
Copper patterning is the process of forming conductive lines and connection points on a substrate. Copper patterns are formed on the surface of the substrate through techniques such as chemical methods or metal evaporation, and these patterns become conductive paths. Precise control of this process ensures the accuracy and reliability of the conductors.
Corrosion is the process of removing unwanted copper material from the substrate. By immersing the substrate in a corrosive solution or using chemical methods, the unwanted copper is removed to create the required wires and connections. The timing and conditions of corrosion need to be precisely controlled to ensure final wire quality.
Drilling holes in the PCB are used to mount components and connect wires between different layers. This process involves using a drill to drill holes into the substrate and making sure the location and size of the holes are accurate. The accuracy of drilling is critical to PCB performance and reliability.
Finally, the PCB surface needs to be treated to improve its corrosion resistance and solderability. This may involve applying a protective solder film to protect the metal from oxidation and to facilitate soldering components to the PCB surface.
At every stage, precise operation and compliance with industry standards are critical. Mistakes in any link may lead to defects in the final product, affecting its performance and reliability. Therefore, minimum pitch PCB manufacturing requires strict quality control and process management to ensure the quality and reliability of the final product.
How to manufacturing a Minimum spacing PCB ?
When manufacturing minimum pitch PCBs, the key is to select appropriate materials and employ advanced manufacturing techniques to ensure tight tolerance requirements are met and space and performance are optimized.
First, choosing the right materials is crucial for manufacturing minimum pitch PCBs. Commonly used substrate materials include FR4 fiberglass panels, which have excellent insulation properties and mechanical strength and are suitable for most application scenarios. In addition, copper foil is used as a conductive layer, and its good conductivity and easy processability make it one of the preferred materials for PCB manufacturing.
Secondly, the use of advanced manufacturing technology is critical to achieving minimum pitch PCBs. Photolithography is a commonly used manufacturing technology that covers copper foil with photosensitive resin, then uses a photolithography machine to expose the designed pattern on the resin, and finally performs chemical etching to form conductive paths. This approach enables very fine line widths and line spacing to meet minimum pitch PCB requirements.
Minimum pitch PCB manufacturing also requires a focus on achieving tight tolerance requirements, which means ensuring that the distance between conductive lines is small enough to optimize space utilization and performance. In order to achieve this goal, the manufacturing process needs to strictly control the accuracy of each step, including patterning, etching and surface treatment. In addition, manufacturers may also use some special processes and technologies, such as controlling etching rates, optimizing photolithography exposure parameters, etc., to ensure that the final PCB meets design requirements.
All in all, manufacturing minimum pitch PCBs requires careful selection of materials, the use of advanced manufacturing technologies, and strict control of each step in the manufacturing process to ensure that the quality and performance of the final product reaches the expected level.
How Much Does a Minimum spacing PCB Cost?
How much does a minimum pitch PCB cost? This is a critical question often asked during PCB manufacturing. The cost of PCB is determined by many factors, and minimum pitch PCB pays more attention to precision and high quality, so it may incur higher costs.
First of all, size is one of the important factors affecting the cost of minimum pitch PCB. Larger PCB sizes require more materials and a more complex manufacturing process, increasing costs. In addition, minimum pitch PCBs often require more stringent design and manufacturing requirements to ensure that the distance between conductors is small enough, which also has an impact on cost.
Secondly, complexity is another factor that affects minimum pitch PCB cost. If the PCB has a complex layout, multi-layer design or high-density wiring, the manufacturing process will become more complex, requiring more process steps and time, thereby increasing costs.
Material quality is also one of the important factors that determine the cost of minimum pitch PCB. High-quality materials typically cost more but offer better performance and reliability. For minimum pitch PCB manufacturing, it is critical to use high-quality substrates and conductive materials to ensure the required accuracy and stability.
Finally, production volume also affects the cost of minimum pitch PCBs. Typically, mass production reduces unit costs because fixed costs can be spread over more products. However, minimum pitch PCBs often require low-volume custom production, which can result in higher costs as more manpower and resources are required to meet specific designs and requirements.
To summarize, the cost of a minimum-pitch PCB depends on many factors, including size, complexity, material quality, and production volume. Because these factors directly affect the complexity and accuracy of the manufacturing process, minimum pitch PCBs may incur higher costs. However, with careful design and selection of the right manufacturer, it is possible to optimize costs to the greatest extent and ensure a high-quality minimum pitch PCB is achieved.
What materials are Minimum spacing PCB made of?
Minimum pitch PCB manufacturing is an important area in the modern electronics industry, where the materials used are critical to its performance and reliability. Let’s dive into what materials minimum pitch PCBs are typically made of.
Substrate material: The substrate of the minimum pitch PCB is a key component that supports the entire circuit structure. One of the common substrate materials is FR4 fiberglass board. FR4 is an insulating material with excellent electrical properties and mechanical strength, and can withstand working in high temperature and high pressure environments. Its advantages include high temperature resistance, good flame retardancy, and high mechanical strength, so it is widely used in various PCB manufacturing.
Conductive layer: The conductive layer of minimum pitch PCB is formed on the surface of the substrate and is used to connect electronic components and transmit current. Typically, copper foil is used as the material for the conductive layer. Copper has good electrical conductivity and mechanical strength and can meet the needs of high-frequency and high-speed circuits. The copper foil is bonded to the substrate and chemically etched or machined to form the desired circuit pattern.
Protective layer: In order to protect the PCB circuit from the external environment and provide identification and aesthetics, a protective layer is often added to the PCB surface. The most common protective layers include solder film and silk screen. Solder film is a thermoplastic material that covers the surface of a PCB to protect circuits from oxidation, chemical corrosion, and mechanical damage. Silk screen printing is to print text, graphics or logos on the surface of PCB to facilitate identification and assembly.
By using these materials, minimum pitch PCBs can achieve highly reliable circuit connections and operate stably under various environmental conditions. At the same time, the selection and processing of these materials also directly affect the cost, performance and manufacturing difficulty of PCB. Therefore, when designing and manufacturing minimum pitch PCBs, materials must be carefully selected and strict quality control standards must be followed to ensure the quality and reliability of the final product.
Who manufactures Minimum spacing PCB ?
In the field of minimum pitch PCB manufacturing, manufacturers are a crucial part. Among the many PCB manufacturers, there are some companies that focus on providing minimum pitch PCB manufacturing services to meet the needs of high-performance electronic devices. Among them, as a leading PCB manufacturer, our company has rich experience and expertise in the field of minimum pitch PCB.
As a professional manufacturer of minimum pitch PCBs, our company is committed to providing high-quality, high-performance PCB solutions. We have advanced manufacturing equipment and technology to meet our customers’ requirements for complex circuit designs and compact layouts. Through continuous technological innovation and process optimization, we are able to achieve extremely small wire spacing, thereby improving PCB integration and performance.
The company’s manufacturing process strictly follows international standards and industry specifications to ensure that each PCB has excellent quality and reliability. We adopt advanced process control and quality management systems to strictly monitor and test each process to ensure that the products meet customer requirements and expectations.
In addition to high-quality manufacturing capabilities, the company also focuses on close cooperation with customers. Our team consists of experienced engineers and professionals capable of providing customers with customized solutions and technical support. We adhere to the customer-centric concept and continuously improve and enhance service quality to meet the changing needs of customers.
Overall, as a leader in the field of minimum pitch PCB manufacturing, our company has won the trust and recognition of customers with its high-quality products and services. We will continue to be committed to technological innovation and quality improvement, providing customers with better PCB solutions and helping them succeed in the fiercely competitive market.
What are 5 qualities of a good customer service?
In minimum pitch PCB manufacturing, excellent customer service is key to ensuring customer satisfaction. These five qualities are explored in detail below:
Professionalism: Excellent customer service starts with professionalism in industry knowledge and product understanding. The manufacturer’s team should have in-depth technical knowledge and experience and be able to provide accurate technical support and solutions. From knowledge of the design and manufacturing process to understanding customer needs, professionalism is the cornerstone of trust and partnership.
Responsiveness: Responding promptly to customer needs and questions is one of the key attributes of great customer service. Manufacturers should be able to respond to customer emails, phone calls or online inquiries quickly and efficiently, and provide necessary support and guidance when customers need it. Quick response not only demonstrates respect and concern for the customer, but also reduces potential production delays and issues.
Personalized care: Understanding a customer’s needs and preferences and providing personalized service based on their specific situation is the key to building a good customer relationship. Manufacturers should actively listen to customer feedback and opinions, customize solutions according to their needs, and provide customized technical support and services. Through personalized care, manufacturers can enhance customer satisfaction and loyalty.
Problem-solving ability: In the face of customer problems and challenges, quality customer service should have the ability and determination to solve problems. Manufacturers should be able to quickly identify and resolve various technical and production issues that customers may encounter, ensuring that orders are delivered on time and meet customer quality standards. Proactive problem solving not only enhances customer trust but also helps build long-term and stable relationships.
Continuous improvement: The ultimate goal of quality customer service is continuous improvement and continuous improvement. Manufacturers should learn from customer feedback and experience and continuously optimize service processes and product quality to meet customers’ changing needs and expectations. Continuous improvement is key to maintaining competitiveness and customer satisfaction, and manufacturers should consider it an important strategic task.
To sum up, in minimum pitch PCB manufacturing, high-quality customer service is not only a means to meet customer needs, but also an important factor in establishing long-term cooperative relationships and enhancing corporate competitiveness. Through the combined application of five attributes: professionalism, responsiveness, personalized care, problem solving and continuous improvement, manufacturers can win the trust and respect of customers and stand out in the market competition.
FAQS
What is the minimum spacing requirement for PCB wires?
Minimum spacing requirements for PCB traces depend on design specifications, circuit complexity, and application environment. In general, smaller pitches enable higher integration and performance, but also increase manufacturing complexity and cost. For common PCB designs, the usual minimum spacing requirements can range from tens to hundreds of microns.
How does minimum pitch PCB manufacturing improve circuit performance?
Minimum pitch PCB manufacturing can effectively reduce the electrical distance between wires, reduce resistance and crosstalk during signal transmission, thereby improving circuit performance and reliability. In addition, smaller spacing can also achieve higher integration, reduce the size of the PCB board, and further improve the performance and efficiency of the system.
What are the factors that affect the cost of minimum pitch PCB?
Factors that affect the minimum pitch PCB cost include design complexity, material selection, manufacturing process and production volume. Smaller pitch requirements typically require higher-precision manufacturing processes and more expensive materials, which results in increased manufacturing costs. In addition, increased production volume can often reduce unit costs, but the impact of starting costs and fixed expenses also need to be considered.
How to ensure the reliability of minimum pitch PCB?
Ensuring the reliability of minimum pitch PCB requires comprehensive control from design, manufacturing to testing. During the design phase, factors such as signal integrity, thermal management, and mechanical strength need to be taken into consideration, and appropriate routing rules and material selection should be adopted. During the manufacturing process, the manufacturing process needs to be strictly controlled to ensure accuracy and consistency at each step. Finally, PCB performance and reliability are verified and validated through rigorous testing and quality control processes.
For high-frequency applications, what are the special considerations when designing minimum pitch PCBs?
For high-frequency applications, designing minimum pitch PCBs requires considering signal integrity, impedance matching and signal transmission stability. Special wiring rules and material selection are usually required to reduce signal propagation delay and loss and ensure signal stability and reliability. In addition, electromagnetic interference (EMI) and radio frequency interference (RFI) suppression also need to be considered, and appropriate shielding and grounding designs should be used to minimize the impact of external interference on the system.