Mixed dielectric PCB manufacturing.High speed and high frequency Mixed dielectric PCBs, or other types Mixed dielectric PCBs. we offer HDI Mixed dielectric layer PCB from 4 layer to 50 layers.
Mixed media PCB (Printed Circuit Board) plays an important role in modern electronic equipment. By combining the characteristics of different media, mixed-media PCBs provide electronic designers with more flexible solutions. This article will deeply explore the design principles, manufacturing processes and cost analysis of mixed media PCB, aiming to help readers fully understand the application value and manufacturing process of mixed media PCB.
What is a mixed media PCB?
Mixed media PCB (Printed Circuit Board) is a printed circuit board that combines a variety of different materials and is designed to overcome the limitations of traditional single-material PCBs and optimize circuit performance. Typically, mixed media PCBs are made up of multiple layers or different parts, each using a specific media, such as FR4 fiberglass board, Rogers, Isola, etc. This hybrid design aims to balance properties such as electrical performance, mechanical strength and thermal conductivity.
The manufacturing of mixed media PCBs involves layering these different materials together and ensuring a reliable connection between them. Designers must accurately consider thermal expansion coefficients, dielectric constants, and other physical properties between different materials to ensure overall circuit board stability and performance. In mixed media PCBs, different materials can be used for different layers to meet specific circuit layouts and requirements. This multi-material combination gives electronics designers greater flexibility and room for innovation, allowing them to better address complex circuit needs and challenges.
With mixed-media PCBs, designers can implement high-frequency, high-speed, high-power and high-density circuits on the same circuit board and overcome the limitations faced by traditional single-material PCBs. For example, using high-frequency materials can improve signal transmission performance, while using high thermal conductivity materials can improve thermal management capabilities. This comprehensive application makes mixed media PCBs ideal for many complex electronic devices, such as communication equipment, medical equipment, aerospace equipment, etc.
In summary, the design and manufacturing of mixed-media PCBs involves the selection and combination of multiple materials to achieve superior circuit performance and functionality. It not only expands the possibilities of electronic design, but also promotes the development and innovation of electronic technology.
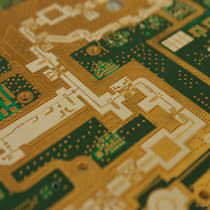
Mixed dielectric PCB
How to design a mixed media PCB?
The design process of mixed-media PCBs involves multiple key steps, which require comprehensive consideration of the characteristics of different materials and the performance requirements of the circuit board. The design process of mixed media PCB will be introduced in detail below:
Before starting the design, you first need to clarify factors such as the function, performance requirements, and environment of the circuit board. This includes determining the number of plies, board thickness, electrical characteristics, thermal management needs, etc.
Select the appropriate material combination based on design needs and performance requirements. Common mixed media PCB materials include FR4, Rogers, Isola, etc. They have different dielectric properties, thermal conductivity and mechanical strength, and designers need to make reasonable matches based on specific requirements.
After the materials are determined, a layer-by-layer design is performed to determine the function and layout of each layer. According to the complexity of the circuit and signal transmission requirements, determine the signal layer, ground layer, power layer, etc. The stack-up design of mixed-media PCBs requires special attention to matching and impedance control between different materials.
When laying out circuits, factors such as signal integrity, electromagnetic compatibility, and thermal management need to be considered. Proper circuit layout can minimize signal crosstalk and electromagnetic interference and improve circuit reliability and performance.
Conduct route planning based on circuit layout to ensure optimization of signal transmission paths. For high-speed signals and microwave frequency circuits, special attention needs to be paid to issues such as matching impedance and signal transmission delay.
When placing devices, factors such as spacing between devices, ease of heat dissipation, and wiring need to be considered. Reasonable device layout can reduce circuit noise and temperature and improve system stability and reliability.
During the design process, attention should be paid to energy conservation and environmental protection. By optimizing circuit layout and material selection, power consumption and heat loss are reduced to achieve energy saving and environmental protection goals.
After the design is completed, simulation verification is performed to ensure the performance and stability of the circuit. Through electromagnetic simulation, thermal simulation and other means, the electrical characteristics and thermal management effect of the design are evaluated, and potential problems are discovered and solved in a timely manner.
Based on simulation results and actual test feedback, the design is optimized and improved. Continuous optimization of design can continuously improve the performance and reliability of circuits to meet changing needs.
Finally, design documents and manufacturing files are generated and communicated with manufacturers. Design documents should include information such as detailed circuit diagrams, stack-up diagrams, device lists, and manufacturing requirements to ensure a smooth manufacturing process.
Through the above design process, designers can realize the optimized design of mixed media PCB to meet the needs of different application scenarios and maximize its performance advantages.
What is the manufacturing process of mixed media PCB?
The manufacturing process of mixed-media PCBs is a precise and complex process that requires precise control and coordination of multiple steps. The manufacturing process of mixed media PCB will be introduced in detail below:
First, mixed media PCB manufacturing starts with material preparation. According to the design requirements and performance requirements, appropriate FR4, Rogers, Isola and other materials are selected, and they are accurately cut and processed to ensure that the size and surface quality of the panels meet the requirements.
Next is the production of the printed circuit layer. According to the PCB design file, the circuit pattern is printed onto the board surface using printing technology. This step requires high-precision equipment and precise operations to ensure the clarity and accuracy of the circuit pattern.
This is followed by chemical etching and cleaning. The printed circuit board is placed in a chemical solution and the unprotected metal parts are removed through an etching process, leaving the desired circuit structure. Subsequently, the panels are thoroughly cleaned to remove residual chemicals and dirt to ensure a clean and smooth surface.
Drilling and plating are the next critical steps. Use a high-speed drill press to drill holes into the circuit board for mounting components and making electrical connections. Subsequently, a layer of metal is plated on the hole wall through an electroplating process to enhance the electrical conductivity of the hole wall for subsequent welding and connection.
Next comes the lamination and lamination of the circuit boards. The single-layer circuit board that has been drilled and plated is combined with other laminated materials (such as copper foil, dielectric layers, etc.) to form a multi-layer structure. The various layers of boards are tightly pressed together using a heat press to form a complete circuit board structure.
Finally comes surface treatment and inspection. The surface of the circuit board is coated and gold-plated to enhance its corrosion resistance and conductivity. Rigorous inspection and testing are then conducted to ensure that the quality and performance of the circuit boards meet design requirements and comply with industry standards and specifications.
Through the above carefully designed and strictly controlled manufacturing process, mixed media PCB can achieve high-quality, high-performance production, providing reliable support and guarantee for the application of electronic products.
How much does a mixed media PCB cost?
Cost assessment of mixed-media PCBs is a critical part of the manufacturing process, which directly affects the economic feasibility of the project and the price of the final product. Here’s a look at how to evaluate the manufacturing costs of mixed-media PCBs.
The manufacturing cost of mixed media PCB is mainly composed of the following aspects:
Material Cost: Material cost is one of the major costs of manufacturing mixed media PCBs. The cost of different materials varies greatly, such as FR4, Rogers, Isola and other materials. At the same time, the auxiliary materials required for mixed media PCB, such as pads, solder resist, etc., will also have an impact on costs.
Manufacturing process cost: Manufacturing mixed media PCB requires consideration of multiple processes, including printing, etching, drilling, electroplating, etc. Each process requires corresponding equipment and manpower investment, so it will directly affect the manufacturing cost.
Design complexity: The complexity of PCB design also has an important impact on manufacturing costs. Complex designs may require more layers, higher precision, and more complex processes, increasing manufacturing costs.
Quantity and scale: Production batch size and scale are also important factors that affect costs. Generally speaking, mass production can reduce the manufacturing cost of a unit product because the unit cost can be reduced through bulk purchasing and automated production lines.
Additional costs: In addition to direct material and manufacturing costs, other additional costs need to be considered, such as transportation costs, labor costs, taxes, etc.
Therefore, to evaluate the manufacturing cost of mixed media PCB, it is necessary to comprehensively consider all the above aspects and conduct reasonable estimation and analysis. Manufacturers usually provide detailed quotations and cost analysis based on the customer’s specific needs and project circumstances to help customers make decisions.
In general, the manufacturing cost of mixed-media PCB is a complex and multifaceted issue that requires comprehensive consideration of various factors to ensure that costs are reduced as much as possible and competitiveness is improved while ensuring quality.
What materials are mixed media PCBs made of?
As an advanced form of printed circuit board, the performance and characteristics of mixed media PCB are often affected by the materials used. Here are some common mixed media PCB materials and their characteristics.
FR-4 is a fiberglass-reinforced epoxy resin substrate, which is a commonly used material for manufacturing ordinary PCBs. It has good mechanical strength and high temperature resistance and is suitable for general electronic applications.
Rogers material is a special high-frequency medium with excellent high-frequency characteristics and low loss. Due to its low dielectric constant and low dielectric loss, it is often used in the manufacture of radio frequency (RF) and microwave circuits.
Isola material is a high-performance thermoplastic resin substrate with excellent mechanical strength and thermal stability. It is commonly used for high-speed digital signal transmission and high-frequency applications such as computer networks and communications equipment.
In addition to conventional glass fiber reinforced resin substrates, there are also some high thermal conductivity media used to manufacture mixed media PCBs, such as aluminum substrates and ceramic substrates. These materials have good heat dissipation properties and are suitable for high power and high temperature applications.
In addition to Rogers materials, there are some other special high-frequency media used to manufacture mixed-media PCBs, such as PTFE (polytetrafluoroethylene) substrate and PP (polypropylene) substrate. These materials have low loss and high frequency properties, making them suitable for applications requiring high frequency and broadband.
During the manufacturing process of mixed-media PCBs, some auxiliary materials, such as conductive adhesives, solder masks, and copper-clad foils, may also be used to meet specific design requirements and process needs.
To sum up, there are many types of materials used in mixed media PCBs, and each material has its own unique characteristics and scope of application. Designers should select appropriate materials based on specific application needs and performance requirements to ensure good performance and reliability of the final product.
Who makes mixed media PCBs?
In the current electronics industry, finding a reliable mixed media PCB manufacturer is crucial. As a company, we are committed to providing high-quality mixed media PCB manufacturing services to meet the growing needs of our customers.
First, the company has advanced production equipment and technical teams that enable high-quality mixed-media PCB manufacturing. We use the latest manufacturing processes and strict quality control standards to ensure that every PCB has excellent performance and reliability.
Secondly, the company has extensive experience and expertise and is able to provide customized solutions based on customers’ specific requirements. Whether it’s a complex lay-up design or the selection of special materials, we are able to provide our customers with professional advice and support to ensure their projects run smoothly.
In addition, the company focuses on communication and cooperation with customers and always puts customer needs first. We maintain close contact with our customers, keep abreast of their needs and feedback, and make adjustments and improvements based on actual conditions to ensure that the final product fully meets customer expectations.
Finally, as a PCB manufacturer with a good reputation, our company always adheres to the principles of honest operation and quality first. We are oriented by customer satisfaction, strive to provide customers with better products and services, and grow and develop together with customers.
To sum up, as our company, we have the ability and confidence to be your reliable mixed media PCB manufacturing partner. Whether you are a start-up or a large enterprise, we can meet your needs and inject new energy and motivation into your project success. Look forward to working with you!
Five Characteristics of Great Customer Service
What characteristics should a quality mixed media PCB manufacturer have? Here are the key five areas:
In the PCB manufacturing process, timely response to customer needs and questions is crucial. Quality manufacturers should establish effective communication mechanisms to ensure that they can respond quickly when customers have inquiries or needs. This includes prompt responses to channels such as emails, phone calls and online chats, as well as providing emergency support when necessary.
As a PCB manufacturer, it is crucial to have extensive expertise. They should understand various PCB materials, manufacturing processes and design technologies, and be able to provide professional advice and guidance to customers. By working closely with customers, they can help them optimize designs, improve performance, and resolve issues that may arise.
A quality PCB manufacturer should be able to provide customized solutions based on the specific needs of customers. They should be able to flexibly adjust their manufacturing processes to meet customer demands for PCB performance, size and special requirements. By working closely with customers, manufacturers can ensure that the final product meets customer expectations exactly.
Good communication is key to building good customer relationships. A quality PCB manufacturer should be able to maintain good communication with customers, including timely updates on project progress, providing detailed manufacturing reports, and answering customer questions. By establishing transparent and open communication channels, manufacturers can enhance customer trust and satisfaction.
A quality PCB manufacturer should be able to provide complete after-sales support and services. This includes helping customers solve problems they may encounter during use, providing technical support and training, and handling customer complaints and feedback in a timely manner. Through active after-sales support, manufacturers can enhance customer loyalty and establish long-term and stable cooperative relationships.
To sum up, a quality mixed media PCB manufacturer should have key characteristics such as prompt response, professional knowledge, customized solutions, good communication and complete after-sales support. These features not only improve customer satisfaction, but also provide manufacturers with a competitive edge in the market, creating a win-win situation.
FAQS
How can manufacturers ensure consistency and reliability in the production of mixed dielectric PCBs?
Manufacturers can maintain consistency and reliability by implementing strict quality control measures throughout the production process. This includes thorough material inspection, precise manufacturing techniques, regular performance testing, and adherence to industry standards and specifications.
What are some common applications of mixed dielectric PCBs?
Mixed dielectric PCBs are commonly used in high-frequency communication systems, aerospace and defense electronics, medical devices, automotive electronics, and industrial automation equipment. Their ability to accommodate diverse material properties makes them suitable for a wide range of demanding applications.
How can designers optimize the performance of mixed dielectric PCBs for specific applications?
Designers can optimize the performance of mixed dielectric PCBs by carefully tailoring the layer stackup, optimizing trace routing for signal integrity, implementing proper grounding techniques, and utilizing advanced simulation tools to predict and analyze performance characteristics.
What are the key factors to consider in designing a mixed dielectric PCB?
Designing a mixed dielectric PCB involves several critical considerations. These include understanding the electrical properties of each dielectric material, ensuring proper layer stack-up to achieve desired signal integrity, managing thermal properties to prevent overheating, and optimizing the mechanical strength to withstand environmental stresses.