Mixed dielectric Rogers PCB manufacturing. Rogers with FR4 Mixed dielectric PCBs, or Rogers with others types materials PCB Vendor, We offer microtrace Rogers PCBs from 4 layer to 50 layers.
In modern electronic equipment, Printed Circuit Board (PCB) is the core component that connects and supports various electronic components, and its design and manufacturing process are crucial. This article will delve into the manufacturing process of Mixed Dielectric Rogers PCB, providing readers with a comprehensive guide designed to help them fully understand and flexibly apply knowledge in this field. By gaining an in-depth understanding of the Mixed Dielectric Rogers PCB manufacturing process, readers will be better equipped to address the challenges of modern electronic device design and manufacturing.
What is Mixed Dielectric Rogers PCB?
Mixed Dielectric Rogers PCB is a special type of printed circuit board (PCB) that uses Rogers materials with different dielectric constants in its manufacturing process. This PCB design is designed to provide excellent high frequency performance and dimensional stability, making it ideal for many high-performance electronic devices.
In Mixed Dielectric Rogers PCB, Rogers materials with different dielectric constants are cleverly combined to form a stacked structure. Rogers materials are a type of special polymer material with excellent electrical properties and dimensional stability, and their dielectric constant can be adjusted as needed. By properly selecting and layering these materials, the complex dielectric properties required for Mixed Dielectric Rogers PCBs can be achieved.
The key to this kind of PCB design lies in reasonable material selection and stack-up structure design. Materials with different dielectric constants can form areas with specific electrical properties on the same PCB to meet different signal transmission and power distribution needs. By carefully designing and adjusting the combination and layout of materials, Mixed Dielectric Rogers PCBs can achieve higher frequency response, lower signal loss, and better dimensional stability, thereby improving overall performance and reliability.
Overall, Mixed Dielectric Rogers PCB represents the latest advancement in PCB design and manufacturing, designed to meet the stringent high-frequency performance and dimensional stability requirements of modern high-performance electronic equipment. Its unique material combination and structural design provide electronic engineers with more flexibility and choice, allowing them to better respond to changing technical challenges.
How to design Mixed Dielectric Rogers PCB?
Designing Mixed Dielectric Rogers PCB is a complex and critical process that requires full consideration of material properties, circuit layout, signal transmission and other factors. Here are some methods for designing Mixed Dielectric Rogers PCB:
Before designing Mixed Dielectric Rogers PCB, you first need to have an in-depth understanding of the characteristics of the selected Rogers material, including dielectric constant, dielectric loss, thermal stability, etc. Different Rogers materials have different properties, and the appropriate material combination needs to be selected according to specific requirements during design.
Good circuit layout is critical to the performance of your Mixed Dielectric Rogers PCB. By rationally laying out various components and signal lines, signal interference and crosstalk can be reduced, and the stability and reliability of the circuit can be improved. At the same time, it is also necessary to pay attention to the impact of layout on thermal management to avoid hot spot concentration and overheating.
Before designing the Mixed Dielectric Rogers PCB, various electromagnetic field simulation software can be used to simulate and verify the circuit. Through simulation analysis, the performance and stability of the circuit can be evaluated, potential problems discovered and optimized, thereby improving the accuracy and reliability of the design.
Mixed Dielectric Rogers PCB is usually used in high-frequency circuits and radio frequency applications, so special attention needs to be paid to the signal transmission characteristics during the design process. Including optimization of matching impedance, signal routing path, differential signal layout, etc. to ensure the high-frequency performance and signal integrity of the circuit.
When designing a Mixed Dielectric Rogers PCB, it is very important to work closely with the material supplier and manufacturer. Suppliers can provide professional advice on material properties and processing techniques to help the design team better select appropriate materials and manufacturing methods to ensure the successful implementation of the design.
Design is a process of continuous iteration and optimization. Once the preliminary design is completed, actual sample production and testing are required, and the design solution is continuously adjusted and optimized based on the test results until the expected performance and reliability requirements are achieved.
In summary, designing Mixed Dielectric Rogers PCB requires comprehensive consideration of multiple factors such as material properties, circuit layout, signal transmission, etc., and continuous optimization of the design solution through simulation verification and cooperation with suppliers to ensure that the final product has excellent performance and reliability.
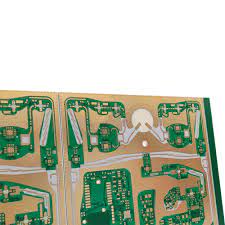
Mixed dielectric Rogers PCB
What is the manufacturing process of Mixed Dielectric Rogers PCB?
When manufacturing Mixed Dielectric Rogers PCBs, there is a complex series of steps to go through to ensure the final product meets design requirements and delivers high-quality performance. The following are the main steps of this manufacturing process:
Material preparation and selection: First, you need to prepare the materials required for Mixed Dielectric Rogers PCB manufacturing, including substrates and Rogers materials with different dielectric constants. Choosing appropriate materials is one of the key factors in ensuring PCB performance stability.
Printed circuit layer design: Before manufacturing PCB, the circuit layer needs to be designed. This includes determining the layout and connection of various components on the circuit board, as well as using CAD software to create PCB design files.
Special material lamination and etching process: The manufacturing process of Mixed Dielectric Rogers PCB involves the lamination and etching process of special materials. During the lamination process, Rogers materials with different dielectric constants are pressed together with the substrate layer to form a multi-layer structure. In the etching process, unnecessary parts of the multi-layer structure are removed through chemical etching, leaving the required circuit pattern.
High-precision drilling and plating: Drilling is an important step in processing the holes on the circuit board into guide holes. In Mixed Dielectric Rogers PCB manufacturing, high-precision drilling equipment is required to ensure the accuracy and precision of hole locations. Subsequently, a layer of metal is plated on the surface of the hole wall through an electroplating process to enhance conductivity and corrosion resistance.
Quality inspection and testing: After the manufacturing is completed, the Mixed Dielectric Rogers PCB needs to undergo strict quality inspection and testing. This includes checking the integrity and accuracy of circuit patterns, and using high-frequency test equipment to test the performance of the PCB to ensure it meets design requirements and standards.
Through the above steps, the manufacturing process of Mixed Dielectric Rogers PCB can be completed. This process requires specialized knowledge and skills to ensure stable performance and high-quality manufacturing of the final product.
What are the specific steps for Mixed Dielectric Rogers PCB manufacturing?
The manufacturing of Mixed Dielectric Rogers PCBs is a complex and precise process involving multiple critical steps to ensure the quality and performance of the final product. These steps are detailed below:
Before manufacturing Mixed Dielectric Rogers PCB, the circuit layer needs to be designed first. This includes determining the layout, routing, and connections of the circuit, as well as determining the location and size of various electronic components. Use CAD software for design to ensure accuracy and efficiency of circuit layout.
Choosing the right Rogers material is very important because it directly affects the performance and stability of the PCB. Based on the design requirements and application needs, select the appropriate Mixed Dielectric Rogers material and perform the necessary material preparation, such as cutting to the required size and shape.
A printed circuit layer is produced by transferring the designed circuit pattern to the substrate. This is usually accomplished through photolithography and etching methods, which transfer the desired circuit pattern to the substrate surface and remove excess material, leaving the desired circuit structure.
For Mixed Dielectric Rogers PCB, materials with different dielectric constants are usually involved. Therefore, during the lamination process, it is necessary to ensure the interlayer adhesion and compaction of various materials, and to ensure that no peeling or deformation occurs between the layers. Afterwards, chemical etching is used to remove excess copper material, making the circuit pattern clearer and more precise.
Drilling holes in PCBs are used to connect circuits between different layers and to install various electronic components. For Mixed Dielectric Rogers PCB, due to the particularity of the material, a high-precision drilling process is required to ensure the accuracy of the hole diameter and the accuracy of the position. After drilling is completed, an electroplating process is performed to enhance the conductivity of the hole wall for subsequent installation of electronic components.
Through the above steps, the manufacturing process of Mixed Dielectric Rogers PCB is basically completed. This process requires a high degree of professional knowledge and skills, and the quality and process parameters of each link need to be strictly controlled to ensure that the performance and stability of the final product meet the design requirements.
Manufacturing Mixed Dielectric Rogers PCB requires in-depth professional knowledge and experience, but through strict quality control and appropriate process optimization, high-quality PCB products can be obtained to meet the needs of various high-frequency applications.
How much does a Mixed Dielectric Rogers PCB cost?
Before looking at the cost of a Mixed Dielectric Rogers PCB, we need to consider several factors. First, the cost of PCB manufacturing depends on factors such as the complexity of the design, the size and number of layers of the board, the type of materials used, and the production quantity. For Mixed Dielectric Rogers PCB, due to the use of special Rogers materials, the cost may be slightly higher than traditional FR4 PCB.
Mixed Dielectric Rogers PCBs use Rogers materials, which generally cost more than regular FR4 materials. The cost of Rogers materials depends on their dielectric constant, thickness and other properties. In addition, the different dielectric constant materials used in Mixed Dielectric Rogers PCB will also have an impact on cost.
Manufacturing Mixed Dielectric Rogers PCBs requires a special production process. Compared with traditional FR4 PCB, these processes may require more time and precision equipment to implement. For example, special lamination processes and delicate etching processes can increase manufacturing costs.
Costs also vary as production quantities increase. Generally speaking, high-volume production reduces the cost per PCB because the fixed costs of the production process can be spread over more units. On the contrary, the cost of low-volume production may be higher.
In addition to the above factors, there are some other factors that may have an impact on the cost of Mixed Dielectric Rogers PCB. For example, special process requirements, customized design requirements, special testing requirements, etc. may increase costs.
Therefore, to determine the cost of Mixed Dielectric Rogers PCB, the above factors need to be considered comprehensively. Generally speaking, due to the particularities of its materials and production processes, the cost of Mixed Dielectric Rogers PCB may be slightly higher than that of traditional FR4 PCB. However, by optimizing design and increasing production quantity, costs can be effectively controlled and production efficiency improved.
What material is the Mixed Dielectric Rogers PCB made of?
In the manufacturing of Mixed Dielectric Rogers PCBs, the materials typically used have a critical impact, and these materials need to meet a specific set of requirements to ensure the performance and stability of the PCB. The following are the main materials commonly used in Mixed Dielectric Rogers PCB:
Rogers material is a special type of high-frequency circuit board substrate material with excellent dielectric properties, stability and processability, and is suitable for high-frequency circuit design. Rogers materials are widely used in the manufacturing of Mixed Dielectric Rogers PCBs to provide excellent high-frequency performance and dimensional stability.
FR-4 is a common fiberglass reinforced epoxy resin material with good mechanical strength and insulation properties. In the design of Mixed Dielectric Rogers PCB, FR-4 material is often used as the substrate layer of the PCB to provide support and structural support.
PTFE is a material with excellent electrical properties and chemical stability and is widely used in high-frequency circuit design. In Mixed Dielectric Rogers PCB, PTFE material is often used as a dielectric layer to achieve a combination of different dielectric constants.
Ceramic materials have excellent dielectric properties and high temperature stability, making them suitable for high-frequency and microwave circuit design. In Mixed Dielectric Rogers PCBs, ceramic materials are often used in specific application scenarios to achieve optimized performance for specific frequency bands.
In the design of Mixed Dielectric Rogers PCB, the metal layer is often used as a conductor layer or ground layer to achieve circuit connection and shielding functions. Commonly used metal materials include copper, aluminum, etc., and their selection depends on specific application requirements and design needs.
To sum up, Mixed Dielectric Rogers PCB is usually composed of Rogers material, FR-4 material, PTFE material, ceramic material and metal layer. These materials play a key role in the PCB design and manufacturing process, providing important support for the high-frequency performance, dimensional stability and reliability of the PCB.
Who makes Mixed Dielectric Rogers PCBs?
In the world of Mixed Dielectric Rogers PCB manufacturing, choosing the right manufacturer is crucial. For many businesses, in-house manufacturing is an attractive option because it provides control over key factors such as production processes, quality control and delivery times. As a manufacturer of Mixed Dielectric Rogers PCB, our company draws on years of experience and expertise to provide customers with high-quality, reliable solutions.
As a manufacturer, we have advanced production equipment and technical teams that can flexibly respond to various complex manufacturing needs. We focus on product quality and adopt strict quality control standards and testing methods to ensure that each Mixed Dielectric Rogers PCB meets customer requirements and industry standards. In addition, we are committed to continuous innovation and improvement, leading the development trend of the industry and providing customers with more competitive products and services.
In addition to technical strength, our company also focuses on communication and cooperation with customers. Our team always focuses on customer needs, actively listens to customers’ opinions and suggestions, and discusses the best solutions with customers. We provide flexible customization services and can carry out personalized design and production according to customers’ specific requirements to meet the needs of different industries and application fields.
To sum up, as a manufacturer of Mixed Dielectric Rogers PCB, our company is committed to providing customers with quality products and services to meet their needs and expectations. We will continue to work hard to innovate, continuously improve our own strength, and share the joy of success with our customers.
Five Characteristics of Great Customer Service
When it comes to Mixed Dielectric Rogers PCB manufacturing, providing excellent customer service is paramount. Here are five characteristics of great customer service and the keys to providing great service to your Mixed Dielectric Rogers PCB design:
Timely response: Being able to respond promptly to customer needs and questions is a basic requirement for quality customer service. During the Mixed Dielectric Rogers PCB manufacturing process, customers may have various questions or needs, and timely responses and solutions are the key to maintaining customer satisfaction.
Professional knowledge: Have professional technical knowledge and experience and be able to provide customers with accurate advice and guidance. For the design and manufacturing of Mixed Dielectric Rogers PCB, customers want to receive professional advice to ensure that the quality and performance of the product meet expectations.
Customized solutions: Provide personalized solutions and services according to the specific needs of customers. In the design and manufacturing of Mixed Dielectric Rogers PCB, different customers may have different requirements and standards. Being able to tailor suitable solutions for them can improve customer satisfaction and trust.
Good communication: Establish good communication channels, maintain close contact with customers, and promptly update project progress and related information. During the Mixed Dielectric Rogers PCB manufacturing process, maintaining good communication with customers can enhance cooperative relationships and reduce misunderstandings and unnecessary problems.
After-sales support: Provide customers with comprehensive after-sales support and services to solve possible problems and ensure customer satisfaction. During the use and maintenance of Mixed Dielectric Rogers PCB, customers may encounter various difficulties and challenges. Providing timely technical support and maintenance services can enhance customer confidence and promote the establishment of long-term cooperative relationships.
FAQS
What are the advantages of using Mixed Dielectric Rogers PCB?
Mixed Dielectric Rogers PCB offers several advantages, including excellent high-frequency performance, dimensional stability, and reduced signal loss. By combining different dielectric constants, it provides designers with more flexibility in optimizing signal integrity and minimizing interference.
What factors should I consider when selecting materials for Mixed Dielectric Rogers PCB?
When selecting materials for Mixed Dielectric Rogers PCB, it’s essential to consider factors such as dielectric constant, thermal stability, cost, and compatibility with manufacturing processes. Rogers materials are often preferred due to their consistent performance and reliability.
What are the key steps involved in manufacturing Mixed Dielectric Rogers PCB?
The manufacturing process for Mixed Dielectric Rogers PCB involves several key steps, including material preparation, layer stacking, circuit pattern imaging, etching, drilling, plating, and final inspection. Each step requires precision and attention to detail to ensure the quality of the final product.
How does Mixed Dielectric Rogers PCB affect the overall cost of production?
The cost of manufacturing Mixed Dielectric Rogers PCB depends on various factors, including material costs, complexity of design, production volume, and manufacturing technology. While using high-quality materials and advanced manufacturing techniques may increase initial costs, they can also lead to improved performance and reliability, potentially reducing long-term expenses.