Module Substates Manufacturer. the Package Substrate will be made with Rogers, BT, Showa Denko and Ajinomoto High speed materials.or other types high speed materials and high frequency materials.
Module Substrate is a crucial material in the manufacturing of electronic modules, encompassing various types, each tailored for specific applications. One prominent variant is the High-Density Interconnect (HDI) board, distinguished by its intricate wiring and multi-level structure. Characterized by a high circuit density, HDI boards facilitate numerous circuit connections in confined spaces, making them prevalent in miniaturized designs like smartphones, tablets, and other portable devices. Additionally, HDI boards boast superior signal integrity and minimal electromagnetic interference, rendering them sought after in high-performance electronic products.
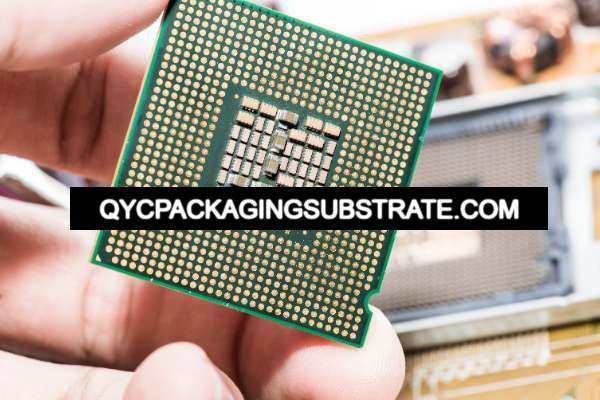
Module Substates Manufacturer
Another commonly used module substrate is the rigid-flex board. These laminates combine the advantages of rigid and flexible boards, incorporating segments that are both rigid and flexible to offer increased design flexibility and adaptability. Rigid-flex laminates, which can bend and fold, are utilized in electronic devices that require curved or intricate shapes, such as curved displays and flexible sensors. Additionally, these laminates can simplify component connections, improving overall reliability, thus making them suitable for applications that prioritize enhanced reliability.
In essence, diverse Module Substrate types exhibit unique characteristics and advantages tailored for specific application scenarios. Choosing the appropriate type mandates a comprehensive assessment based on factors like product design requirements, performance specifications, and manufacturing costs. Manufacturers, armed with a comprehensive understanding of Module Substrate variations, can aptly select materials aligning with their product needs, thereby bolstering product competitiveness and market share.
What are the advantages of Module Substrate?
Module Substrate offers numerous advantages over traditional circuit boards, making it the preferred choice for many electronic equipment manufacturers. Let’s delve into the specifics of Module Substrate’s benefits and how they contribute to enhanced performance, reduced dimensions and weight, cost efficiency, and improved product reliability.
Primarily, the Module Substrate’s high-density interconnect (HDI) configuration enables it to accommodate a greater number of electronic components within the same surface area, thereby boosting circuit board density and integration. This increased density facilitates superior circuit board performance, enabling electronic products to execute more complex functions within a smaller space.
Secondly, precise control over the design and manufacturing process of Module Substrate results in thinner and lighter circuit boards compared to traditional counterparts. This reduction in size and weight enhances the portability and overall convenience of electronic products, while also contributing to cost savings due to decreased material usage, leading to lower manufacturing expenses.
These enhancements not only bolster circuit board performance but also fortify its reliability. Through refined design and manufacturing processes, the stability and dependability of Module Substrate are significantly enhanced, thereby minimizing product issues stemming from circuit board failures and extending product lifespan.
In summary, Module Substrate offers improved performance, reduced size and weight, cost savings, and heightened product reliability compared to traditional circuit boards. These advantages position Module Substrate as a pivotal technology and a primary choice within the electronics industry, providing substantial support for the manufacturing of diverse electronic products and driving continuous advancements and innovations in electronic technology.
Why choose Module Substrate?
Why opt for Module Substrate? This question can be approached from various angles. As a pivotal material in the manufacture of electronic modules, Module Substrate’s benefits and range of applications increasingly attract manufacturers. Its significance and distinct utility in telecommunications, healthcare, and automotive sectors will be elaborated below.
Primarily, Module Substrate boasts heightened density and improved signal integrity compared to traditional circuit boards. This equates to its capacity to accommodate more electronic components within a smaller area and facilitate more efficient signal transmission, thereby boosting the performance of electronic devices. In the present trend toward more streamlined, lighter, and more compact products, Module Substrate offers increased design adaptability, enabling manufacturers to produce sleeker and more feature-rich products.
Moreover, the unique attributes of Module Substrate confer upon it vast and profound utilities across the telecommunications, medical, and automotive industries. In telecommunications, the compact Module Substrate facilitates swifter data transmission rates and more reliable signal propagation, fulfilling user needs for fast networks and wireless connectivity. Within healthcare, the downsizing and high-efficiency capabilities of Module Substrate render medical devices more portable and intelligent, thereby enhancing the effectiveness and precision of medical diagnostics and therapies. Within the automotive sector, Module Substrate’s exceptional performance assists vehicle manufacturers in developing more intelligent, safer, and fuel-efficient cars to meet consumer expectations for vehicular smartness and environmental consciousness.
In summary, the rationale for selecting Module Substrate encompasses its benefits such as increased compactness, enhanced signal fidelity, sleek and lightweight construction, and its broad array of applications in telecommunications, healthcare, automotive, and beyond. With ongoing technological progressions and evolving market needs, Module Substrate is poised to assume an increasingly central role in the future of electronic fabrication, furnishing essential support for the innovation and progression of electronic apparatus.
How is Module Substrate made?
The production process of Module Substrate entails a sophisticated and meticulous procedure, involving numerous critical stages, such as conception, material choice, fabrication, imprinting, molding, and other facets. These steps collectively guarantee the caliber and efficacy of the end product.
Primarily, the initial phase involves conceptualization. During this stage, engineers are tasked with devising a Substrate framework and arrangement that aligns with specific application requisites and technical specifications. The excellence of the design significantly influences the seamless advancement of subsequent operations and the ultimate performance of the product.
Subsequently, the selection of materials assumes paramount importance. Guided by design prerequisites and performance criteria, opting for suitable substrate and surface treatment materials is imperative to ensure product stability and dependability.
Leveraging state-of-the-art fabrication techniques and machinery, the envisioned Substrate layouts are translated into tangible product forms. Meticulous fabrication guarantees the dimensional precision and surface evenness of the circuit board, thereby enhancing product reliability and performance consistency.
The imprinting process constitutes a critical segment. Through imprinting, circuit patterns, insignias, textual elements, and other details are applied onto the Substrate surface. Accurate imprinting ensures the legibility and aesthetic appeal of the circuit board, serving as a significant indicator of product excellence.
Finally, molding signifies the conclusive step in the manufacturing sequence. Through molding, the original Substrate panel undergoes transformation into its ultimate product configuration. The molding operation ensures the dimensional accuracy and visual appeal of the product, facilitating a better alignment with customer requisites.
Overall, the manufacturing process of Module Substrate necessitates stringent quality oversight and procedural management, with each phase demanding meticulous planning and precise execution to uphold the quality and performance benchmarks outlined in the design. Through continual refinement and innovation, manufacturers can furnish Module Substrate products of superior quality and enhanced performance, thus fostering sustained progress and ingenuity within the electronics industry.
In what fields is Module Substrate widely used?
Module Substrate is extensively employed across various sectors of electronic module manufacturing due to its exceptional performance and adaptable design, rendering it a preferred choice in numerous industries. Its applications span across the realms of smartphones, tablets, and automotive electronic systems:
In the realm of smartphone manufacturing, Module Substrate assumes a pivotal role. As smartphone designs shrink in size, necessitating higher circuit board density and performance, Module Substrate emerges as a solution by offering high-density interconnection. This enables the miniaturization of mobile phone modules while ensuring the stability and reliability of signal transmission. Moreover, Module Substrate facilitates the integration of diverse sensors, cameras, and wireless communication modules, thereby expanding the functional capabilities of smartphones.
Module Substrate is integral to the manufacturing process of tablet computers, playing a pivotal role in accommodating the larger circuit boards required for these devices compared to smartphones. It facilitates a high-density circuit layout, resulting in sleeker, lighter tablets with improved performance and stability. This technology also enables the integration of advanced features like high-definition displays and multi-touch functionality.
In summary, Module Substrate finds widespread utilization in smartphones, tablets, and automotive electronic systems, offering robust support for enhancing performance and expanding functionality across these product categories. With ongoing technological advancements and innovations, the future holds even broader application prospects for Module Substrate.
How to get Module Substrate?
First, we can look for potential Module Substrate Manufacturers through the supplier network. These supplier networks may include various industry shows, professional forums and association meetings. On these occasions, we can contact and communicate with multiple manufacturers to understand their product lines, technical capabilities and service levels. By comparing with multiple manufacturers, we can better evaluate their comprehensive strength and select the partner that best meets our needs.
Secondly, we can also locate Module Substrate Manufacturers through online markets. Nowadays, many manufacturers showcase their products and services on various online platforms such as Alibaba, Global Sources, etc. These platforms offer a vast array of manufacturer information, including company background, product specifications, customer reviews, etc. Moreover, they typically provide convenient communication tools, allowing us to directly engage with manufacturers for further inquiries and negotiations regarding their offerings. Additionally, professional consulting agencies and intermediary services within the industry can be utilized to find suitable Module Substrate Manufacturers. These entities often possess extensive industry experience and resources, enabling them to furnish tailored supply chain solutions and assist in identifying the most suitable manufacturer. Collaborating with such professional organizations facilitates a swifter discovery of manufacturers aligning with our requirements, establishing robust cooperative relationships. In summary, locating a dependable Module Substrate Manufacturer can be accomplished through diverse channels, encompassing supplier networks, online markets, and professional consulting agencies. By conducting thorough research and comparisons, we can identify the manufacturer best suited to our needs, fostering enduring and stable cooperative partnerships to bolster the company’s development.
How to get a quote for Module Substrate?
The quotation process for Module Substrate is intricate and influenced by numerous factors. To secure the most competitive quote, it’s essential to grasp these factors and focus on pertinent details during the quoting process.
Foremost, several key factors impact Module Substrate’s quotation. These include material costs, process intricacy, design specifications, and production scale. Material selection and manufacturing processes directly impact ease and cost. Higher design standards or customizations typically incur additional costs. Additionally, production scale plays a pivotal role, with mass production generally lowering costs compared to smaller-scale runs.
When soliciting quotes, selecting the right manufacturer is paramount. The manufacturer’s experience, technical prowess, equipment quality, and quality control system significantly influence quote accuracy and competitiveness. Therefore, it’s advisable to assess a manufacturer’s overall capability and reputation alongside pricing considerations.
Furthermore, when requesting a quote, providing comprehensive information is crucial. This encompasses design blueprints, material specifications, process requirements, and anticipated production volumes. Detailed information facilitates an accurate assessment of costs by manufacturers. Effective and timely communication is also critical throughout the process, enhancing quote accuracy and competitiveness by addressing potential issues promptly.
Lastly, comparing quotes from different manufacturers is vital to securing the most competitive offer. Through thorough comparisons, differences in quotes, as well as each manufacturer’s strengths and weaknesses, become apparent. Price is only one aspect to consider; evaluating technical expertise, service quality, and delivery timelines is equally important in selecting the optimal manufacturer.
In conclusion, a nuanced understanding of the factors influencing Module Substrate quotations, coupled with attention to relevant details during the quoting process, can yield the most competitive quotes, ultimately driving cost savings and efficiency improvements in product manufacturing.
Frequently Asked Questions (FAQs)
What are the main differences between Module Substrate and traditional circuit boards?
Module Substrate typically offers higher density, better signal integrity, improved thermal management, and enhanced reliability compared to traditional circuit boards.
How can I ensure the quality of Module Substrate from a manufacturer?
Ensuring the quality of Module Substrate involves thorough supplier evaluation, including certifications, quality control processes, and possibly conducting factory audits.
What are the key considerations when integrating Module Substrate into product design?
Integrating Module Substrate into product design requires considerations such as electrical performance, mechanical compatibility, thermal management, and manufacturability.
How can Module Substrate contribute to product innovation and competitiveness?
Module Substrate enables product innovation by offering advanced features, miniaturization, improved performance, and cost-effectiveness, thereby enhancing competitiveness in the market.
How to choose a suitable Module Substrate Manufacturer?
When selecting a manufacturer, consider factors such as their experience, technical capabilities, production capacity, and quality management systems
What factors influence the pricing of Module Substrate?
The pricing of Module Substrate is influenced by various factors including materials, manufacturing processes, and design complexity. It is advisable to communicate with multiple manufacturers to obtain the most competitive quotes.