Multi-Chip FC-BGA Package Substrates Manufacturer.Our company is a leading manufacturer of Multi-Chip FC-BGA Package Substrates, specializing in cutting-edge solutions for high-performance electronics. With advanced technology and precision engineering, we deliver substrates that support multiple chips, ensuring optimal connectivity, thermal management, and signal integrity. Our substrates are trusted by industry leaders for their reliability and superior performance in applications ranging from data centers to consumer electronics.
With the continuous enhancement of the functions and integration of electronic equipment, multi-core FC-BGA packaging substrates, as an important part of the modern electronic field, are attracting increasing attention. The multi-core FC-BGA packaging substrate integrates multiple chips into one package, providing a highly integrated, optimized layout, high reliability and flexible design solution for electronic equipment. This article will deeply explore the definition, design advantages, manufacturing processes and wide range of application fields of multi-core FC-BGA packaging substrates to demonstrate its importance and advantages in promoting the development of modern electronic technology.
What are Multi-Chip FC-BGA Package Substrates?
Multi-core FC-BGA packaging substrate is an electronic component packaging solution based on multi-core packaging technology. This packaging technology plays a vital role in the design of modern electronic devices because it can effectively improve the performance and functional density of the device. Specifically, the multi-core FC-BGA packaging substrate integrates multiple functional chips into one substrate, and conducts electrical connection and signal transmission with the motherboard through a ball grid array (BGA, Ball Grid Array) interface.
Multi-Chip Packaging technology refers to packaging two or more chips on the same substrate or package to achieve high integration and high performance design goals. The advantage of this technology is that it can reduce the connection distance between chips and reduce the delay and loss of signal transmission, thus improving the overall performance of the system. In addition, multi-core packaging can also save space and make electronic devices thinner, lighter and more compact.
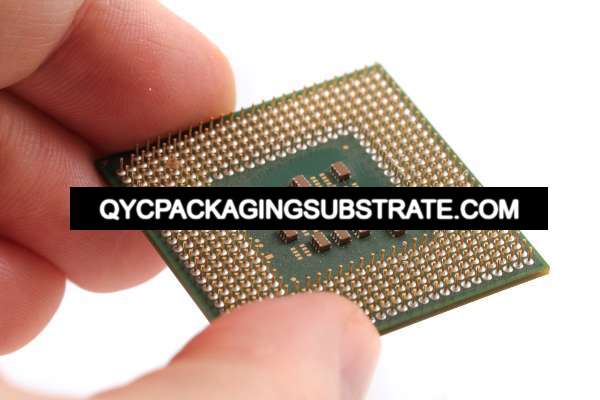
Ultra-small Size FC-LGA Substrates Manufacturer
In multi-core FC-BGA packaging substrates, the BGA interface is an important connection method. The BGA interface uses solder balls to connect the package substrate to the motherboard. The solder balls are arranged in a grid pattern, which can not only improve the reliability of the connection, but also provide higher pin density. The application of BGA packaging technology makes the connection between the chip and the motherboard stronger and the signal transmission more stable. This is particularly important for electronic equipment that requires high performance and reliability, such as servers, network equipment, and high-end consumer electronics.
The design of multi-core FC-BGA packaging substrate not only focuses on the arrangement and connection of the chips, but also needs to consider aspects such as power management, heat dissipation design and signal integrity. By optimizing these designs, the performance and reliability of the packaging substrate can be effectively improved. For example, in terms of power management, each chip can ensure a stable power supply through reasonable power distribution and decoupling capacitor design. In terms of heat dissipation design, you can increase heat dissipation channels and use high thermal conductivity materials to help dissipate heat quickly and prevent the chip from overheating. In addition, in order to ensure signal integrity, shielding layers and grounding layers can be added to the design to reduce electromagnetic interference and crosstalk.
In short, the multi-core FC-BGA packaging substrate provides an efficient and reliable electronic component packaging solution by integrating multiple chips into a packaging substrate and using the BGA interface to connect to the motherboard. It can not only improve the performance and functional density of the device, but also effectively reduce the power consumption and size of the system. In the future, as the function and performance requirements of electronic equipment continue to improve, multi-core FC-BGA packaging substrates will be widely used in more fields.
Multi-Chip FC-BGA Package Substrates design Reference Guide.
As the performance of electronic equipment continues to improve and its functions become increasingly complex, multi-core FC-BGA (Flip Chip-Ball Grid Array) packaging substrates are increasingly favored by engineers as an efficient solution. This article will introduce in detail the design reference guide for multi-core FC-BGA package substrates, including design principles, material selection, design tools and best practices, to help you achieve success in complex electronic system design. In the design of multi-core FC-BGA package substrate, we must first consider how to effectively integrate multiple chips into one package. The functions of each chip and their interconnection relationships require careful planning to ensure the performance and reliability of the overall circuit.
Due to multi-chip integration, thermal management becomes a critical issue. Effective heat dissipation methods should be considered during design, such as introducing a metal heat dissipation layer or using high thermal conductivity materials to ensure that the chip remains within a safe temperature range during operation.
Multi-chip designs require special attention to signal integrity. Signal paths that are too long and complex should be avoided to minimize signal interference and delay. Differential signal pair design, ground plane planning, and impedance matching are all important considerations.
Commonly used substrate materials include FR-4, ceramics and high-frequency materials. FR-4 is widely used due to its good mechanical properties and cost-effectiveness, while ceramic substrates excel in high-temperature and high-frequency applications.
Copper is the most commonly used conductive material and has excellent conductivity and reliability. For high frequency applications, special copper foil or other conductive materials may be required to reduce signal loss.
The choice of encapsulation material is equally important, usually epoxy or silicone. These materials need to have good mechanical protection and environmental protection, and at the same time, their thermal expansion coefficient must be matched with the chip and substrate materials to prevent damage caused by thermal stress.
Electronic design automation (EDA) tools are key to multi-core FC-BGA package substrate design, including Altium Designer, Cadence Allegro and Mentor Graphics. They provide full-process support from schematic design, PCB layout to signal integrity analysis.
Thermal management is a major challenge in multi-core design, so thermal analysis tools such as ANSYS Icepak and COMSOL Multiphysics can help engineers conduct thermal design and thermal simulation to optimize the thermal structure.
Multi-core packaging needs to be closely integrated with the mechanical structure, so mechanical design tools such as SolidWorks and AutoCAD are also indispensable to help design packaging structures that meet mechanical requirements.
At the early stage of the project, the layout and connection relationship of each chip should be fully planned, and the thermal management plan and signal integrity requirements should be determined. This can avoid repeated modifications in subsequent designs and improve design efficiency.
Use iterative design methods to continuously optimize and verify designs. Rigorous simulation and testing are performed at every design stage to ensure the correctness and reliability of every design decision.
The design of multi-core FC-BGA packaging substrates often requires close collaboration between electronic engineers, mechanical engineers and thermal management experts. Team members should maintain good communication and coordination to jointly solve problems encountered in the design.
Multi-core FC-BGA package substrate design is a complex but challenging task that requires comprehensive consideration of multiple factors such as functional integration, thermal management, and signal integrity. Through reasonable material selection, advanced design tools and best practices, engineers can design high-performance, high-reliability multi-core packaging substrates, providing a solid foundation for the innovative development of modern electronic devices.
What material is used in Multi-Chip FC-BGA Package Substrates?
Multi-core FC-BGA packaging substrate is a key electronic component packaging solution, which provides important support for the high performance and high integration of modern electronic equipment. In the manufacturing of multi-core FC-BGA packaging substrates, the materials used are crucial and directly affect the performance, reliability and application scope of the packaging substrate.
In multi-core FC-BGA packaging substrates, common materials include:
Substrate material: The substrate of multi-core FC-BGA package substrates usually uses high-performance non-conductive materials, such as fiberglass reinforced epoxy resin (FR-4) or polyimide (PI). These materials have good mechanical strength and high temperature resistance, and can effectively support and protect chips and connecting lines.
Conductive layer material: The material that forms the conductive layer on the surface of the substrate is usually copper (Cu). Copper has excellent electrical conductivity and workability, and can effectively transmit electrical current and connect various electronic components.
Encapsulation material: The material used to encapsulate the multi-core FC-BGA packaging substrate is usually epoxy resin (Epoxy) or polyimide. These materials have good packaging performance and high temperature resistance, can effectively protect the chip and provide a stable working environment.
Solder: The solder connecting the chip and the substrate is usually a solder with good conductivity and good reliability, such as lead-tin alloy (PbSn) or lead-free solder (Lead-Free). These solders can form reliable soldering connections under high temperature conditions, ensuring a stable connection between the chip and the substrate
To sum up, the material selection of multi-core FC-BGA packaging substrate directly affects the performance, reliability and application scope of the packaging substrate. By selecting appropriate materials and combining with advanced manufacturing processes, the high performance and reliability of multi-core FC-BGA packaging substrates can be achieved to meet the needs of different fields and applications.
What size are Multi-Chip FC-BGA Package Substrates?
The size of multi-core FC-BGA packaging substrates varies depending on application scenarios and design requirements. Typically, these substrates provide highly integrated circuit functionality within a relatively small size range. Its size depends on several factors, including chip count, chip size, layout density, and the number of input/output interfaces required
In general, the size of the multi-core FC-BGA package substrate can range from a few millimeters to tens of millimeters. For most applications, such packaging substrates are usually designed to be relatively compact to accommodate the miniaturization trend of electronic devices.
Some specific applications may require larger size multi-core FC-BGA packaging substrates to accommodate more chips or implement more complex circuit functions. For example, in high-end network equipment or data center servers, larger-sized multi-core FC-BGA package substrates may be required to support large-scale data processing and communication functions.
On the other hand, some portable devices, such as smartphones, tablets and wearable devices, may require smaller size multi-core FC-BGA packaging substrates to meet the demand for lightweight and thin designs.
In summary, the size of the multi-core FC-BGA package substrate can vary within a wide range, ranging from a few millimeters to tens of millimeters, to meet the design requirements of different electronic devices. Design engineers typically determine the most appropriate size and layout based on the needs of a specific application, combined with factors such as performance, power consumption, and space constraints.
The Manufacturer Process of Multi-Chip FC-BGA Package Substrates.
Multi-chip FC-BGA (Flip Chip Ball Grid Array) packaging substrate is a type of advanced electronic packaging technology and is widely used in high-performance and high-density electronic products. Its manufacturing process is complex and delicate, involving multiple steps and technical requirements. This article will introduce in detail the manufacturing process of multi-chip FC-BGA packaging substrates, including substrate design, material selection, printed circuit board production, chip mounting and welding, packaging and testing and other key links.
The first step in the manufacturing process is substrate design, which involves planning the layout of multiple chips and designing circuit connections. Design engineers use advanced CAD tools to create circuit diagrams and wiring diagrams to ensure that each chip’s electrical connections are correct. At the same time, considering signal integrity and thermal management issues, electromagnetic compatibility (EMC) and thermal simulation analysis are also required in the design.
Material selection is critical to the performance of multi-chip FC-BGA packaging substrates. High strength, high thermal conductivity substrate materials such as FR-4, ceramic or BT resin are usually used. For solder balls, choose a solder alloy with good conductivity and reliability (such as SnAgCu). In addition, copper foil and insulation layer materials need to be selected for high-density interconnection and high-frequency signal transmission.
The fabrication of a printed circuit board (PCB) involves multiple steps. It starts with cutting and drilling of the substrate, followed by copper foil lamination and pattern transfer. Precise conductive circuits are formed on the substrate through photolithography and etching processes. Next, the multi-layer boards are laminated and pressed to form the required multi-layer structure. Finally, electroplating and surface treatment are performed to prepare for subsequent chip mounting and welding.
Chip mounting is one of the key steps in multi-chip FC-BGA packaging. First, the chip is flipped over using Flip Chip technology so that its bottom solder balls are aligned with the pads on the substrate, and then the chip is firmly fixed on the substrate through hot pressure soldering or reflow soldering. In order to ensure welding quality, advanced detection technology (such as X-ray inspection) is used to inspect solder joints to ensure that each solder joint is defect-free.
After the chip is installed, it needs to be packaged and protected. Epoxy resin is usually used for filling and packaging to ensure that the chip and its solder joints are not affected by the external environment. For applications requiring high reliability, it may also be encapsulated with a ceramic or metal cover for enhanced protection.
The final step in the manufacturing process is testing. Verify the electrical performance and reliability of the multi-chip FC-BGA package substrate through functional testing, thermal cycle testing and highly accelerated life testing (HALT). Only products that pass all tests can be put into use to ensure their stability and long life in actual applications.
The manufacturing process of multi-chip FC-BGA packaging substrates is complex and delicate, involving multiple technical links. Through strict design, material selection, manufacturing and testing processes, we ensure that our products have high performance and reliability. This advanced packaging technology plays an important role in the fields of communications, industrial control, medical and automotive electronics, promoting the continuous progress and innovation of electronic technology.
The Application area of Multi-Chip FC-BGA Package Substrates.
The wide application of multi-core FC-BGA packaging substrates in various industries has promoted the development and innovation of modern electronic equipment. Its high degree of integration, optimized design and reliability make it widely used in the following fields:
Communication equipment: Multi-core FC-BGA packaging substrate plays a key role in communication equipment, such as base stations, routers, switches, etc. They can support complex communication protocols and data processing tasks, improve the performance and stability of communication equipment, and meet the growing demand for data transmission.
Industrial control system: The field of industrial automation has extremely high requirements for high performance, reliability and stability. Multi-core FC-BGA packaging substrates are widely used in industrial control systems. They can achieve fast and accurate data exchange and control between a variety of sensors and actuators, improving production efficiency and product quality.
Medical equipment: In medical diagnostic, monitoring and treatment equipment, multi-core FC-BGA packaging substrates provide key support for realizing highly integrated medical electronic equipment. They can process complex biological signals and data to achieve precise diagnosis and treatment, improving medical care and patients’ quality of life.
Automotive electronics: With the continuous development of automotive electronics technology, multi-core FC-BGA packaging substrates are increasingly used in automotive electronic systems. From in-vehicle infotainment systems to body control units, multi-core FC-BGA packaging substrates can realize high-performance and high-reliability automotive electronic functions, improving driving experience and vehicle safety.
Consumer electronics: Consumer electronics such as smartphones, tablets, and smart home devices have a growing demand for multi-core FC-BGA packaging substrates. They can support complex application software and smooth playback of high-definition videos, providing a more intelligent and convenient user experience.
In summary, the application of multi-core FC-BGA packaging substrates in the fields of communications, industry, medical, automotive and consumer electronics has provided strong support for technological innovation and product upgrades in various industries, and promoted the scientific and technological progress of modern society. and economic development.
What are the advantages of Multi-Chip FC-BGA Package Substrates?
Multi-core FC-BGA packaging substrate has significant advantages in the field of modern electronics. These advantages make it the first choice in the design of various electronic equipment.
First of all, the multi-core FC-BGA packaging substrate has a high degree of integration. By integrating multiple chips into a single package, the size and weight of electronic devices can be greatly reduced, resulting in a more compact and lightweight design. This is particularly important for applications that require high performance but limited space, such as mobile communication devices and portable consumer electronics.
Secondly, the multi-core FC-BGA packaging substrate has an optimized layout design. Through a carefully designed layout, compact connections between circuit components can be achieved, thereby improving signal transmission efficiency and system performance. This optimized design not only helps reduce the size of the circuit board, but also reduces electromagnetic interference between circuit boards and improves the stability and reliability of the system.
Third, the multi-core FC-BGA packaging substrate has excellent reliability. The use of advanced packaging processes and materials can ensure the stable operation of multi-core FC-BGA packaging substrates under various environmental conditions. High-quality packaging materials and precise manufacturing processes can effectively reduce component aging and failure caused by temperature changes, humidity and other factors, thereby extending the service life of electronic equipment.
In addition, the multi-core FC-BGA packaging substrate offers flexibility. The design is flexible and highly customized, and can be customized according to different application requirements to meet the design requirements of various complex electronic systems. Whether it is functionality or appearance design, multi-core FC-BGA packaging substrates can provide personalized solutions to meet customers’ specific needs.
In summary, multi-core FC-BGA packaging substrates have many advantages in electronic device design, including high integration, optimized layout, reliability and flexibility. These advantages make multi-core FC-BGA packaging substrates an ideal choice in the design of various electronic devices, promoting the continuous development and innovation of electronic technology.
FAQ
What are the advantages of multi-core FC-BGA packaging substrate compared with traditional packaging solutions?
Multi-core FC-BGA packaging substrate has higher integration and performance advantages than traditional packaging solutions. By integrating multiple chips into a package substrate, the size and weight of the circuit board can be reduced, and the overall system performance and reliability can be improved.
Is the manufacturing process of multi-core FC-BGA packaging substrate complicated?
The manufacturing process of multi-core FC-BGA packaging substrates is relatively complex and involves many aspects such as substrate design, material selection, printed circuit board production, chip mounting and welding, packaging and testing. However, advanced manufacturing technology and equipment have greatly simplified the manufacturing process and ensured product quality and stability.
What application areas are multi-core FC-BGA packaging substrates suitable for?
Multi-core FC-BGA packaging substrates are widely used in communication equipment, industrial control systems, medical equipment, automotive electronics and other fields. Its high level of integration, optimized design and reliability make it a key component in realizing the functionality of advanced electronic products.
What is the cost of multi-core FC-BGA packaging substrate?
The cost of multi-core FC-BGA packaging substrates is affected by multiple factors, including packaging materials, manufacturing processes, chip selection, etc. Compared with traditional packaging solutions, although the initial investment is higher, due to its high integration and reliability, it can reduce the overall system cost and maintenance cost.