Multi-Chip FC-BGA Substrates Manufacturer. We use advanced Msap and Sap technology, High multilayer interconnection substrates from 4 to 18,
In the design of modern electronic equipment, PCB (Printed Circuit Board) plays a crucial role. With the continuous development of technology, multi-core FC-BGA substrate, as a new circuit board design solution, is attracting more and more attention. This article will explore the definition, design guidelines, material selection, manufacturing process, application areas and advantages of multi-core FC-BGA substrates. These contents will help readers better understand and apply multi-core FC-BGA substrate technology and promote innovation and development in the electronic field.
What are Multi-Chip FC-BGA Substrates?
In the design of modern electronic equipment, PCB (Printed Circuit Board) plays a crucial role. As a core component of electronic equipment, PCB provides a platform to support and connect various electronic components, promoting the function realization and performance optimization of electronic equipment. In the evolution of PCB design, multi-core FC-BGA substrates, as an advanced circuit board design, are receiving increasing attention.
Multi-core FC-BGA substrate is an innovative circuit board design. Its core feature is to integrate multiple chips into a single package, achieving higher integration and performance. Using ball grid array pad (BGA) technology, the multi-core FC-BGA substrate makes the connection between chips more compact and greatly reduces the size of the circuit board. Compared with traditional PCB design, multi-core FC-BGA substrate is not only more efficient in space utilization, but also improves the performance and reliability of the circuit.
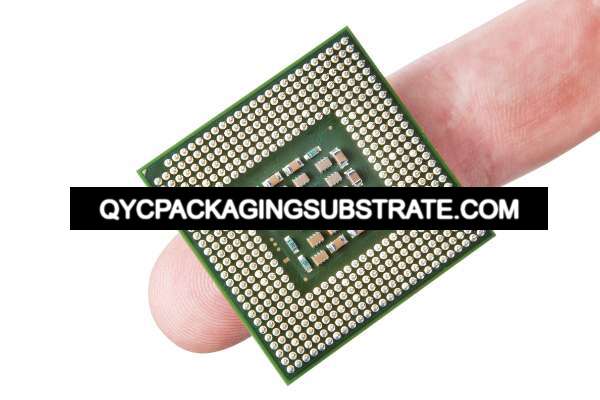
Multi-Chip FC-BGA Substrates Manufacturer
By integrating multiple chips into one package, multi-core FC-BGA substrates achieve a high degree of integration of functional modules, helping to simplify circuit board layout and design. This integrated design not only reduces the complexity of the circuit board, but also improves the stability and reliability of the circuit. In addition, multi-core FC-BGA substrates can also accommodate more functional modules in the same space, providing greater flexibility for functional expansion of electronic equipment.
The adoption of multi-core FC-BGA substrates also brings convenience to the manufacturing and assembly of electronic equipment. Since the connections between chips are more compact, the length and complexity of the circuits are reduced, thus greatly simplifying the circuit board manufacturing process. This not only reduces manufacturing costs, but also improves production efficiency and speeds up the time to market of electronic devices.
In summary, multi-core FC-BGA substrate, as an advanced circuit board design, not only has significant advantages in space utilization, performance improvement and reliability, but also brings new innovations to the design and manufacturing of electronic equipment. possibility. With the continuous development of electronic technology, it is believed that multi-core FC-BGA substrates will play an increasingly important role in future electronic equipment.
Multi-Chip FC-BGA Substrates design Reference Guide.
When designing a multi-core FC-BGA substrate, multiple important factors need to be considered to ensure optimal circuit performance and reliability. Here are some areas designers should focus on:
Circuit layout
Reasonable circuit layout is the key to ensuring balanced signal transmission and power consumption distribution. Designers need to take care to place chips, connecting lines, and circuit components in appropriate locations to minimize signal transmission path lengths and interference between circuit components.
Thermal design
Multi-core FC-BGA substrates will generate a lot of heat during operation, so good heat dissipation design is an important factor in ensuring stable performance. Designers should consider adding heat dissipation equipment such as radiators, heat sinks or heat pipes, and rationally design ventilation holes or heat dissipation slots to improve heat conduction and dissipation efficiency.
Signal integrity
In high-speed circuit design, signal integrity is key to ensuring the reliability of data transmission. Designers should pay attention to reducing the length of signal lines, reducing crosstalk and reflections of signal lines, and taking appropriate impedance matching measures to ensure the stability and accuracy of signal transmission.
Basic design principles
When designing multi-core FC-BGA substrates, designers should follow some basic design principles, such as minimizing the number of circuit board layers, reducing line impedance and loss, and rationally selecting wiring rules, to improve circuit performance and reliability. .
Flexible adjustment of design plans
Each application scenario has different requirements and restrictions, so designers should flexibly adjust the design plan according to the actual situation. During the design process, simulation analysis and experimental verification are carried out in a timely manner to discover and solve potential problems and ensure that the final product meets the expected performance requirements.
To sum up, designing a multi-core FC-BGA substrate requires comprehensive consideration of multiple factors such as circuit layout, heat dissipation design, signal integrity, etc., and following basic design principles and flexibly adjusting the design plan to ensure optimal performance and reliability. Through careful design and optimization, multi-core FC-BGA substrates will provide electronic products with higher integration, more stable performance and more reliable operation guarantees.
What material is used in Multi-Chip FC-BGA Substrates?
The materials used in multi-core FC-BGA substrates are crucial to the performance and stability of the entire circuit design. Typically, these substrates use FR-4 as the main substrate material, while using high-quality conductive materials such as copper to ensure efficient operation and stability of the circuit.
FR-4 is a glass fiber reinforced epoxy resin-based material widely used in PCB manufacturing. Its main components are fiberglass cloth and epoxy resin. This material has excellent mechanical properties and high temperature resistance. FR-4 substrate has high strength and rigidity and can withstand various stresses and pressures required for complex circuit designs. At the same time, the FR-4 substrate has good thermal conductivity, which helps dissipate heat and improve the stability and reliability of the circuit.
In addition to substrate materials, multi-core FC-BGA substrates also require high-quality conductive materials to achieve circuit connection and transmission. Copper is one of the most commonly used conductive materials with excellent electrical conductivity and mechanical properties. In multi-core FC-BGA substrates, copper is usually used to form wires, pads and connection points to ensure the stability and reliability of the circuit. High-quality copper materials can provide good current transmission and signal transmission effects while having low resistance and losses.
To sum up, the materials used in multi-core FC-BGA substrates include high-quality FR-4 substrates and high-quality copper conductive materials. These materials have excellent mechanical properties and electrical conductivity properties, which can meet the needs of complex circuit design and ensure the stability and reliability of the circuit. By selecting appropriate materials and strictly controlling the manufacturing process, the high quality and reliability of multi-core FC-BGA substrates can be ensured, promoting continued development and innovation in the electronics field.
What size are Multi-Chip FC-BGA Substrates?
The size of multi-core FC-BGA substrate is one of the crucial considerations in the design process. Their size directly affects the overall size, layout and available space of the circuit board, so they must be carefully tailored to specific application needs. Normally, multi-core FC-BGA substrates adopt standard packaging specifications, but in some special cases, non-standard sizes can also be customized to meet the requirements of specific product designs.
Size is a crucial consideration in the design of electronic products. Micro- and medium-sized multi-core FC-BGA substrates are suitable for different types of electronic products, from portable smartphones to industrial automation equipment, and can be customized according to their size requirements.
Micro-sized multi-core FC-BGA substrates are often used in thin and light portable devices, such as smart watches, portable medical equipment, etc. These products usually have strict requirements on size and weight, so miniaturized circuit boards are required to meet the compact design of the product. Micro-sized multi-core FC-BGA substrate can effectively utilize limited space and realize highly integrated circuit design.
On the other hand, medium-sized multi-core FC-BGA substrates are suitable for electronic products that require more functions and connection interfaces, such as industrial control systems, network equipment, etc. These products typically require larger circuit boards to accommodate more components and connectors and provide more expandability and flexibility. Medium-sized multi-core FC-BGA substrates can meet the design needs of these products and provide stable and reliable circuit solutions.
In general, the size of multi-core FC-BGA substrates can be customized according to specific application needs, ranging from micro to medium sizes. Whether you are pursuing thinness, lightness, portability or rich functions, multi-core FC-BGA substrates can provide flexible solutions to meet the design requirements of different electronic products.
The Manufacturer Process of Multi-Chip FC-BGA Substrates.
The manufacturing process of multi-core FC-BGA substrate is a complex and precise process, which involves multiple key steps. From design to final assembly, every link is crucial and affects the quality and performance of the product.
First of all, the first step in manufacturing multi-core FC-BGA substrate is design. At this stage, design engineers need to use professional design software to draw circuit diagrams and layouts based on the product’s needs and specifications. They need to consider factors such as circuit function, connections, heat dissipation, signal integrity, etc. to ensure that the design meets the product’s performance and reliability requirements.
Next comes the printing stage. After the design is completed, the circuit board pattern is printed on the substrate, usually through photolithography. Photolithography technology uses photosensitive resin and photoresist to transfer design patterns to the surface of a substrate to form conductive paths and component locations.
Then comes etching. At this stage, the uncovered portions of the metal are etched away by a chemical solution, forming the circuit board’s wires and connections. This step requires strict control of etching time and solution concentration to ensure the quality and accuracy of the circuit board.
Next comes the assembly stage. At this stage, chips and other components are precisely mounted onto the circuit board. Surface mount technology (SMT) is usually used, and components are welded to the circuit board through high-temperature hot melt adhesive. This process requires sophisticated automation equipment and superb technology to ensure the correct installation of components and welding quality.
Finally comes testing and quality control. At every stage of the manufacturing process, rigorous testing and inspection is required to ensure that the product meets specifications and quality standards. This includes circuit connection testing, signal integrity testing, visual inspection, etc. Only after passing strict quality control can products leave the factory.
To sum up, manufacturing multi-core FC-BGA substrates is a complex and precise process that requires sophisticated equipment and technology, and strict control of each link to ensure the quality and performance of the final product. Through continuous technological innovation and quality control, multi-core FC-BGA substrates will continue to play an important role in the electronic field, promoting continuous technological progress and innovation.
The Application area of Multi-Chip FC-BGA Substrates.
Multi-core FC-BGA substrates play a vital role in all walks of life today, and their wide range of applications cover many fields such as communications, computers, consumer electronics, and medical equipment. In the field of communications, multi-core FC-BGA substrates are widely used in wireless communications equipment, base stations, satellite communications and other systems. Its high integration and excellent performance provide efficient and stable circuit solutions for data transmission and promote communications technology. of rapid development. In the computer field, multi-core FC-BGA substrates are used in key facilities such as servers, network equipment, and data centers. Its high performance and reliability ensure the stable operation of computing systems and provide support for technologies such as cloud computing and big data processing. Reliable support. In the field of consumer electronics, multi-core FC-BGA substrates are widely used in smartphones, tablets, smart homes and other products. Its small size and high performance meet consumers’ needs for portability and functionality, promoting the Continuous innovation in consumer electronics products. In the field of medical equipment, multi-core FC-BGA substrates are used in key equipment such as medical imaging equipment, monitoring instruments, and implantable medical devices. Its high reliability and precise control ensure the safety and stability of medical equipment. , providing reliable support for medical diagnosis and treatment. Overall, the wide application of multi-core FC-BGA substrates not only promotes technological progress and innovation in various industries, but also provides strong technical support for the development of human society.
What are the advantages of Multi-Chip FC-BGA Substrates?
The advantage of multi-core FC-BGA substrate is its increasing importance in modern electronic product design. Compared with traditional circuit design, this advanced substrate technology has many advantages, including higher integration, smaller size, higher performance and reliability. These advantages make multi-core FC-BGA substrates an ideal choice to meet the high performance and high reliability requirements of modern electronic products, and are also an important development direction for future circuit design.
First, multi-core FC-BGA substrates achieve higher integration by integrating multiple chips into a single package. Traditional circuit design often requires multiple independent chips and connection components, which occupy a large space. The multi-core FC-BGA substrate integrates multiple functional modules into one package, effectively reducing the size of the circuit board and improving the system efficiency. Integration and overall performance.
Secondly, multi-core FC-BGA substrates have smaller sizes. As electronic products develop towards thinner, lighter and smaller sizes, the requirements for circuit board size are becoming more and more stringent. The multi-core FC-BGA substrate uses ball grid array pad (BGA) technology to achieve more compact connections between chips, further reducing the size of the circuit board and providing greater flexibility and space utilization for product design. Rate.
In addition, multi-core FC-BGA substrates have higher performance and reliability. Due to higher integration and more compact layout, multi-core FC-BGA substrates perform well in aspects such as signal transmission, heat dissipation, and electromagnetic compatibility. They can meet the needs of various complex circuit designs and ensure the stability and reliability of the system. In scenarios such as high frequency, high power, and high-speed data transmission, multi-core FC-BGA substrates can exert their excellent performance advantages and provide products with more stable and reliable circuit solutions.
To sum up, the multi-core FC-BGA substrate not only has higher integration and smaller size, but also has higher performance and reliability, which can meet the high performance and high reliability requirements of modern electronic products. It is An important development direction of future circuit design. With the continuous advancement and innovation of technology, multi-core FC-BGA substrates will play an increasingly important role in various application fields and promote the development of electronic products to a higher level.
FAQ
What are the advantages of multi-core FC-BGA substrate compared to other types of circuit boards?
Multi-core FC-BGA substrates have many advantages over other types of circuit boards. First, they enable higher integration and functional density by integrating multiple chips into a single package. This means that more functional modules can be accommodated on the same size substrate, making electronic products more compact and lightweight. Secondly, the multi-core FC-BGA substrate uses ball grid array pad (BGA) technology, which makes the connection between chips more reliable and stable, while improving the anti-interference ability and signal integrity of the circuit. In addition, the manufacturing process of multi-core FC-BGA substrates is quite mature and can meet the needs of complex circuit design and ensure product quality and performance. Therefore, multi-core FC-BGA substrates are widely used in high-performance and high-reliability electronic products.
Is the manufacturing process of multi-core FC-BGA substrate complicated?
The manufacturing process of multi-core FC-BGA substrate is slightly more complicated than the traditional circuit board manufacturing process, but through reasonable process flow and strict quality control, the quality and performance of the product can be ensured. The key steps in manufacturing multi-core FC-BGA substrates include design, material selection, printing, etching, assembly, etc. During the design phase, circuit layout, signal integrity, heat dissipation and other factors need to be considered to ensure circuit performance and reliability. During the manufacturing process, sophisticated equipment and technology, such as automated printing machines, chemical etching machines, etc., are required to achieve high-precision manufacturing. In addition, material selection and quality control are also crucial to ensure the stability and reliability of the circuit board. Therefore, although the manufacturing process of multi-core FC-BGA substrates is relatively complex, the quality and performance of the products can be ensured through scientific management and technical means.
What application fields are multi-core FC-BGA substrates suitable for?
Multi-core FC-BGA substrates are widely used in various fields. In the field of communications, they are often used in network equipment, base stations, communication modules and other products to meet the needs of high-speed data transmission and signal processing. In the computer field, multi-core FC-BGA substrates are widely used in servers, network equipment, data storage and other products to improve system performance and stability. In addition, multi-core FC-BGA substrates are also used in consumer electronics, medical equipment, automotive electronics and other fields to provide high-performance, high-reliability circuit solutions for these products. Therefore, multi-core FC-BGA substrates are suitable for various application scenarios that require high-performance and high-reliability circuits, and are an important part of future electronic product design.