Multilayer Load Board Manufacturer.A Multilayer Load Board Manufacturer specializes in creating high-performance testing boards for semiconductor devices. These boards feature multiple layers to accommodate complex circuitry and ensure precise signal integrity. By leveraging advanced materials and innovative design techniques, these manufacturers provide essential components for reliable testing and validation of integrated circuits in various applications, ensuring high-quality performance and functionality in the final products.
Multilayer Load Boards are specialized circuit boards designed to test and evaluate semiconductor devices, particularly during manufacturing and development. These boards are crucial in ensuring the reliability and performance of integrated circuits (ICs) by subjecting them to various electrical and environmental conditions.
What is a Multilayer Load Board?
A Multilayer Load Board is a type of printed circuit board (PCB) that consists of multiple layers of conductive and insulating materials. These boards are used to test semiconductor devices by providing a controlled environment where the devices can be subjected to different electrical stimuli and measured for performance.
Multiple Layers: The board consists of several layers that provide the necessary interconnections and support for the components being tested.
Test Points and Pads: These are strategically placed to connect to the device under test (DUT) and to various testing instruments.
High Reliability: Designed to withstand rigorous testing environments and provide accurate and consistent results.
Design Reference Guide for Multilayer Load Boards
Designing a Multilayer Load Board involves several steps to ensure that it meets the necessary performance and reliability requirements.
Choosing the right materials is essential for the board’s performance and durability. Common materials include:
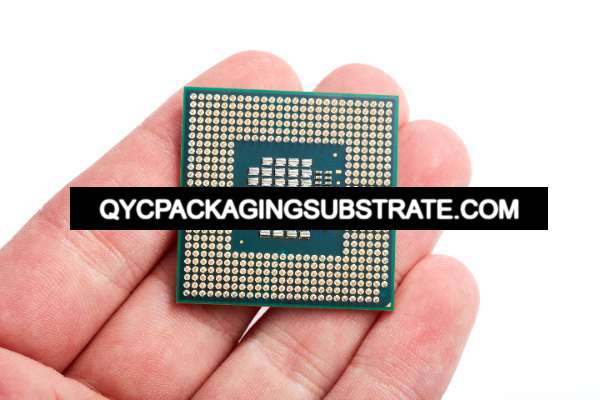
Multilayer Load Board Manufacturer
FR4: A widely used PCB material known for its good mechanical and electrical properties.
High-frequency Laminates: For high-speed and high-frequency applications, materials like Rogers or Taconic are preferred.
Copper: Used for conductive layers due to its excellent electrical conductivity.
Multilayer Load Boards typically consist of:
Core Layers: These provide the primary structural integrity and house the main power and ground planes.
Signal Layers: Multiple signal layers are sandwiched between the core layers, providing the necessary routing for electrical signals.
Prepreg Layers: These are insulating layers that bind the core and signal layers together.
Effective thermal management is crucial, especially when testing high-power devices. Techniques include:
Thermal Vias: These conduct heat away from the DUT to the heat sinks.
Heat Sinks: External components attached to the board to dissipate heat.
Material Considerations: Using materials with high thermal conductivity to enhance heat dissipation.
Ensuring optimal electrical performance involves:
Controlled Impedance: Maintaining consistent impedance throughout the board to ensure signal integrity.
Minimal Crosstalk: Designing the layout to minimize interference between adjacent traces.
Signal Integrity: Careful routing and shielding to maintain the integrity of high-speed signals.
Board Thickness: Determined by the number of layers and the overall design requirements.
Drill Holes and Vias: Precise drilling of holes and vias for inter-layer connections.
Component Placement: Strategic placement of components to ensure ease of testing and accurate results.
What Materials are Used in Multilayer Load Boards?
The materials used in Multilayer Load Boards must provide a balance of electrical, thermal, and mechanical properties. Common materials include:
FR4: A glass-reinforced epoxy laminate that is widely used due to its good mechanical strength and electrical insulation properties.
High-Frequency Laminates: Materials like Rogers or Taconic that offer low dielectric loss and stable performance at high frequencies.
Copper: Used extensively for conductive layers, providing excellent electrical conductivity and forming the traces and pads on the board.
Prepreg: A composite material made of fiberglass and resin, used to bond the layers together and provide additional insulation.
Solder Mask: A protective coating applied to the surface of the board to prevent solder bridges and protect the copper traces from oxidation.
Silkscreen: Used to apply labels and identifiers to the board, aiding in assembly and testing processes.
What Size are Multilayer Load Boards?
The size of Multilayer Load Boards can vary significantly depending on the application and the complexity of the devices being tested. Factors influencing the size include:
Device Under Test (DUT): The size and layout of the DUT dictate the board dimensions to ensure proper connection and testing.
Test Requirements: Different tests may require different configurations and sizes of the load board to accommodate various test points and instrumentation.
Manufacturing Capabilities: The capabilities and limitations of the manufacturing process also play a role in determining the size of the board.
Application-Specific Needs: Certain applications may require custom-sized boards to fit into specific testing environments or to meet unique requirements.
The Manufacturing Process of Multilayer Load Boards
The manufacturing process of Multilayer Load Boards involves several precise and controlled steps to ensure high quality and reliability.
CAD Design: Creating a detailed design using computer-aided design (CAD) software that incorporates all layers, traces, and components.
Simulation: Running simulations to optimize the design and ensure it meets performance specifications.
Lamination: Preparing and layering the core and prepreg materials to form the multilayer structure.
Drilling: Drilling holes and vias to create inter-layer connections.
Photo-etching: Applying a photoresist, exposing it to UV light through a mask, and etching away unprotected areas to create the circuit pattern.
Plating: Adding additional copper to the traces and pads to enhance electrical performance.
Surface Mount Technology (SMT): Placing and soldering surface-mount components onto the board.
Through-Hole Technology: Inserting and soldering through-hole components where needed.Electrical Testing: Conducting tests to ensure all connections are intact and the board functions as intended.
Thermal Testing: Verifying the board’s ability to dissipate heat effectively.
Final Inspection: A thorough inspection to ensure the board meets all design specifications and quality standards.
The Application Area of Multilayer Load Boards
Multilayer Load Boards are used in a wide range of applications where precise testing and evaluation of semiconductor devices are required:
Semiconductor Manufacturing: Used during the production process to test and validate semiconductor devices before they are packaged and shipped.
Research and Development: Essential in R&D labs for testing new designs and prototypes to ensure they meet performance and reliability standards.
Quality Assurance: Used in quality control processes to verify that products meet the necessary specifications and standards.
High-Performance Computing: Employed in testing CPUs, GPUs, and other high-performance computing components to ensure they can handle the required workloads.
Telecommunications: Used to test RF and microwave components, ensuring they meet the stringent requirements of communication systems.
What are the Advantages of Multilayer Load Boards?
Multilayer Load Boards offer several advantages that make them ideal for testing and evaluating semiconductor devices:
High Reliability: Designed to withstand rigorous testing environments and provide accurate and consistent results.
Enhanced Electrical Performance: Multilayer construction allows for complex routing and improved signal integrity, essential for high-speed and high-frequency applications.
Thermal Management: Advanced materials and designs enable effective heat dissipation, ensuring that devices under test remain within safe operating temperatures.
Compact and Efficient Design: Multiple layers allow for a compact design, saving space and enabling more complex testing setups.
Customizability: The ability to create custom designs tailored to specific testing requirements allows for optimized performance and flexibility.
FAQ
What are the main benefits of using Multilayer Load Boards in semiconductor testing?
Multilayer Load Boards provide high reliability, enhanced electrical performance, effective thermal management, a compact and efficient design, and customizability, making them ideal for semiconductor testing.
How are Multilayer Load Boards manufactured?
The manufacturing process involves design and simulation, material preparation, circuit patterning, component attachment, and rigorous testing and quality control to ensure high quality and reliability.
What materials are commonly used in Multilayer Load Boards?
Common materials include FR4, high-frequency laminates like Rogers or Taconic, copper for conductive layers, prepreg for insulation, solder masks for protection, and silkscreen for labeling.
In which industries are Multilayer Load Boards most commonly used?
Multilayer Load Boards are commonly used in semiconductor manufacturing, research and development, quality assurance, high-performance computing, and telecommunications.
How do Multilayer Load Boards improve thermal management?
Multilayer Load Boards improve thermal management through the use of thermal vias, heat sinks, and high-performance materials that enhance heat dissipation and maintain device performance during testing.