Organic FC BGA substrate Manufacturer. the Package Substrate will be made with BT core, Showa Denko core and Ajinomoto High speed materials.
This passage discusses the significance of Organic Substrate FC BGA (Fine-pitch Ball Grid Array) in the electronics industry. This advanced packaging technology utilizes organic substrates, offering superior thermal conductivity and mechanical properties compared to traditional inorganic substrates. The use of organic substrates enables high-density, high-performance integration of electronic devices through finely arranged solder ball grid connectors.
One key feature of FC BGA substrates is the adoption of organic substrates as the fundamental material. Organic substrates exhibit enhanced thermal conductivity and mechanical properties, making them well-suited for operation in high-temperature and high-pressure environments. Additionally, the lower processing cost and shorter production cycle of organic substrates make them a preferred choice for many electronic manufacturers.
The design of finely arranged solder ball grid connectors not only facilitates higher-density device integration but also ensures a robust electrical connection, contributing to the stability and reliability of electronic devices during operation. This design enhances signal transmission between devices, making the organic substrate FC BGA substrate a crucial component in various high-performance electronic devices.
Overall, the organic substrate FC BGA substrate plays a vital role in supporting the development of modern electronic equipment with its advanced packaging technology, superior performance, and reliability. Its applications span across communication equipment, computer hardware, and medical devices, influencing the electronics industry’s evolution and providing consumers with more convenient and efficient electronic product experiences.
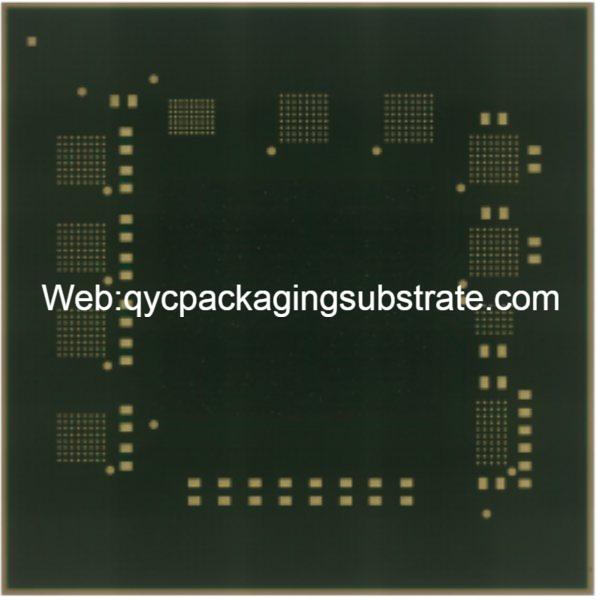
Organic Substrate FC BGA substrate Manufacturer
What are the advantages of organic substrate FC BGA substrate?
Organic substrate FC BGA substrate is very popular in electronic manufacturing, and its unique advantages make it the preferred packaging solution for many electronic manufacturers. The following are the main advantages of organic substrate FC BGA substrates compared to other packaging substrates:
Higher density: The organic substrate FC BGA substrate uses finely arranged solder ball grid connectors, which makes the device layout more compact and therefore has higher device density. This means that more functional modules and devices can be accommodated in a limited space, allowing for more complex circuit designs.
Lower inductance: Organic substrate FC BGA substrate focuses on reducing inductance during the design and manufacturing process, which helps reduce loss and interference during signal transmission. Lower inductance means higher signal quality and more stable circuit performance, especially in high-frequency applications.
Better heat dissipation performance: Organic substrate FC BGA substrate uses organic-based materials, which usually have better heat dissipation performance. This means that in high-power or high-density integrated circuit applications, organic substrate FC BGA substrates can more effectively transfer heat to the surrounding environment and maintain a stable operating temperature of electronic devices.
Strong adaptability: Organic substrate FC BGA substrates can be customized and designed according to specific application requirements, including selecting different materials, layouts and solder ball arrangements. This flexibility allows organic substrate FC BGA substrates to adapt to various environments and application scenarios to meet customers’ individual needs.
This paragraph highlights the competitive edge of organic substrate FC BGA (Flip Chip Ball Grid Array) substrates in electronic manufacturing. It emphasizes their lower production costs compared to other high-performance packaging technologies, attributing this advantage to simpler materials and manufacturing processes, as well as economies of scale. Furthermore, it underscores the broad application prospects of organic substrate FC BGA substrates, citing their high density, low inductance, efficient heat dissipation, adaptability, and cost-effectiveness. The conclusion suggests that with ongoing technological advancements and innovations, these substrates will continue to offer advanced and reliable packaging solutions to the electronics industry.
How are organic substrate FC BGA substrates made?
The manufacturing process of organic substrate FC BGA (Fine-pitch Ball Grid Array) substrate is a complex and precise endeavor comprising two primary steps: mainboard manufacturing and substrate manufacturing. These steps are characterized by a high degree of automation, ensuring consistency and high quality in the final product. Such meticulous processes are essential for meeting the stringent performance and reliability demands of contemporary electronic equipment.
The motherboard manufacturing process involves the selection and processing of organic substrates, printed circuit board (PCB) design, circuit tracing, and component mounting. In the manufacturing of organic substrate FC BGA substrates, the design of the motherboard must take into account the layout of the fine solder ball grid connectors to ensure reliable electrical connections and high integration.
Highly automated motherboard manufacturing processes typically include:
Prepare high-quality organic substrates with precision to meet design specifications. Design circuit board layouts using advanced computer-aided design (CAD) tools. Implement precise circuit tracking on the motherboard through automated production lines for signal path stability and reliability.
Component installation: Use advanced automated equipment to accurately install electronic components onto the motherboard.
The substrate, also called substrate, is another important part of the organic substrate FC BGA substrate. A key goal of substrate fabrication is to create a robust support structure that holds and connects a grid of fine solder balls. During the manufacturing process, highly sophisticated equipment ensures precise positioning and reliable connection of tiny components.
The highly automated substrate manufacturing process includes:
Substrate material preparation: Select and prepare specific materials suitable for organic substrate FC BGA substrates, usually organic materials with high insulation and good thermal conductivity.
This passage describes the manufacturing processes involved in creating a substrate for electronic components:
Lamination Process:Multiple layers of substrates are fused together through lamination to create a robust substrate structure.
Holes and Metallization: Holes are drilled through the substrate, and metallization processes are applied to create pathways for connection to the motherboard.
Micro-Solder Ball Grid Manufacturing: High-precision technology is utilized to manufacture a micro-solder ball grid, which facilitates connections with the solder points on the motherboard.
Through these automated steps, the manufacturing of organic substrate FC BGA substrates can achieve a high degree of consistency and quality. Such a manufacturing process not only improves production efficiency, but also ensures the reliability and performance of the final product, making organic substrate FC BGA substrates the preferred packaging solution for modern electronic devices.
In what fields are organic substrate FC BGA substrates used?
This passage discusses the versatile use of organic substrate FC BGA (Fine-pitch Ball Grid Array) substrates in diverse industries, including communication equipment, computer hardware, and medical devices. It underscores their exceptional performance, reliability, and adaptability to challenging technological environments.
In the realm of communication equipment, especially with the emergence of 5G technology, there exists a burgeoning demand for packaging solutions that offer both high performance and high density. Organic substrate FC BGA substrates are particularly adept at meeting these demands, excelling in aspects such as signal transmission speed and stability. Consequently, they have become prevalent in 5G base stations and network equipment.
Similarly, in computer hardware, where demands for performance and reliability are paramount, organic substrate FC BGA substrates are preferred for crucial components like processors, graphics cards, and motherboards. Their density, speed, and thermal management capabilities align well with the requirements of modern computing, especially in fields like big data processing and artificial intelligence.
Moreover, the medical device industry relies on packaging solutions that offer high reliability, density, and long-term stability. Organic substrate FC BGA substrates meet these criteria, enhancing the performance and safety of medical equipment such as imaging devices and implantable devices, thereby benefiting patient care and treatment outcomes.
Overall, organic substrate FC BGA substrates represent a high-performance and reliable packaging technology with extensive applications across various industries. As technology continues to advance and market demands grow, these substrates are expected to play an increasingly vital role in the electronics industry, fostering opportunities and advancements across diverse sectors.
Where can I find organic substrate FC BGA substrate?
This paragraph discusses the significance of selecting a reliable organic substrate FC BGA (Flip-Chip Ball Grid Array) substrate supplier in modern electronics manufacturing. The company emphasizes its commitment to delivering high-quality electronic products and highlights key factors in supplier selection.
The paragraph suggests that industry trade shows are valuable platforms for discovering the latest technologies and engaging directly with various organic substrate FC BGA substrate manufacturers. It emphasizes the importance of gaining an in-depth understanding of products and services through direct communication at these exhibitions.
Furthermore, the text acknowledges the role of the Internet in facilitating supplier selection. Online platforms are noted as a convenient means for browsing product options and communicating with suppliers to ensure they align with specific needs.
In addition to trade shows and online platforms, the paragraph underscores the significance of professional networks, including industry forums and social media platforms. These networks provide opportunities to share experiences with other professionals, seek recommendations, and gather advice to identify reputable organic substrate FC BGA substrate manufacturers. Overall, the company aims to convey its dedication to thorough supplier research and the utilization of diverse channels to make informed choices in the ever-evolving field of electronics manufacturing.
Why choose our company?
This passage underscores our company’s robust standing as a dependable provider within the electronics manufacturing sector. We take immense pride in our outstanding reputation, established on the pillars of top-notch products, dependability, and technological ingenuity, garnering the trust and admiration of our clientele. Our highly skilled team, equipped with vast knowledge and abilities, is committed to providing customized solutions to meet a wide range of needs. We adhere rigorously to strict quality assurance procedures, in accordance with international standards, and utilize state-of-the-art manufacturing technologies to guarantee the consistent superiority of our products.
Our proficient technical team is ready to provide expert consultation, solution design, and support to guarantee the smooth execution of your projects. In essence, choosing our company as your organic substrate FC BGA supplier means relying on our professional expertise, top-notch products, and dependable services to achieve your electronic product manufacturing objectives.
What is the quotation of organic substrate FC BGA substrate?
The quotation of organic substrate FC BGA substrate is indeed an important consideration when choosing a manufacturer. In this article, we will explore how the quotation of organic substrate FC BGA substrate affects customer choice and how to ensure the best value for money.
First of all, there are multiple factors to consider when understanding the quotation of organic substrate FC BGA substrate. These factors include substrate size, number of layers, material type, surface treatment, production volume, and other customization needs.
This paragraph emphasizes the significance of product quality and technical support in the selection of a manufacturer, particularly in the context of high-quality organic substrate FC BGA substrates. It stresses that while price is important, customers prioritize quality assurance and adherence to strict standards in material selection, manufacturing processes, and inspection testing. Furthermore, it highlights the necessity for manufacturers to offer proficient technical support, guiding customers through design phases, troubleshooting production issues, and providing post-sales assistance to ensure optimal performance and reliability of the products.
This paragraph emphasizes the significance of various factors that customers consider when selecting a manufacturer. It highlights the importance of timely delivery, quality products, and professional technical support in meeting customer needs and ensuring smooth production plans. By choosing a manufacturer with a good reputation and reliable delivery, customers can obtain the best value for their investment. Collaborating closely with manufacturers enables customers to receive tailored solutions that provide a competitive edge in the market.
What are the common problems with organic substrate FC BGA substrate?
What are the advantages of Organic Substrate FC BGA Substrates?
Organic Substrate FC BGA substrates offer unique advantages over other packaging substrates, such as higher density, lower inductance, superior thermal performance, among others. These attributes make them a preferred packaging solution for many electronic manufacturers.
Why should one choose a specialized manufacturer for Organic Substrate FC BGA Substrates?
Opting for a specialized manufacturer for Organic Substrate FC BGA substrates is crucial due to their advanced technology, extensive experience, and high manufacturing standards. These manufacturers ensure product quality and reliability, meeting the demanding requirements of electronic applications.
How are Organic Substrate FC BGA Substrates manufactured?
The manufacturing process of Organic Substrate FC BGA substrates typically involves two main steps: motherboard fabrication and substrate production. Utilizing highly automated production processes ensures product consistency and high quality.
What are the applications of Organic Substrate FC BGA Substrates?
Organic Substrate FC BGA substrates find wide applications across various industries, including telecommunications, computer hardware, medical devices, among others. Their high performance and reliability make them essential components in numerous advanced technologies.
Where can one find suppliers of Organic Substrate FC BGA Substrates?
Reliable suppliers of Organic Substrate FC BGA substrates can be found through industry exhibitions, online vendors, and professional networks. It’s essential to choose manufacturers with a good reputation and high recognition to ensure product quality.
How are quotes for Organic Substrate FC BGA Substrates determined?
While price is a consideration, the selection of Organic Substrate FC BGA substrate manufacturers should prioritize factors such as product quality, technical support, and delivery time. Evaluating these factors ensures obtaining the best value for money.