Organic Package substrates Manufacturer. we offer the best samllest bump pitch with 100um, the best smallest trace and gap are 9um. the Organic Package Substrates will be finished with high quality and fast shipping time.
In the ever-evolving PCB engineering, organic packaging substrates play a vital role. They are a fundamental material used in electronic components, providing a solid foundation for the manufacture and functionality of modern electronic devices. Organic packaging substrates are made of organic materials, usually epoxy resin or polyimide. These substrates provide support and connections for electronic components and allow them to operate efficiently on the circuit board. In PCB engineering, the selection and design of organic packaging substrates are critical to device performance, stability, and reliability. By connecting to other components, organic packaging substrates help build modern electronic devices, from smartphones and tablets to medical devices and automotive electronic systems. Therefore, the existence and development of organic packaging manufacturers are crucial to driving innovation and advancement in PCB technology. Their continuous efforts and innovation drive the development of the electronics industry and bring us more efficient and reliable electronic products.
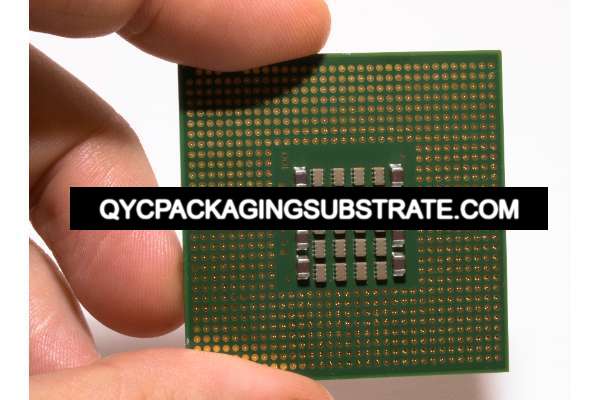
Organic Package Manufacturer
Types of organic packaging substrates?
This passage discusses the crucial role of organic packaging substrates in the contemporary design and manufacturing of electronic devices. These substrates come in various types tailored to meet specific requirements in different application scenarios.
This passage discusses the significance of flexible substrates, emphasizing their exceptional flexibility and bendability, particularly in the realm of electronic products that demand bending or folding capabilities. Typically constructed from flexible polyimide or polyamide materials, these substrates are characterized by their thin, lightweight, and compact nature. They find extensive use in applications such as wearable devices and curved displays.
The text then introduces rigid-flex substrates as a hybrid solution that combines the flexibility of flexible substrates with the stability of rigid ones. These substrates consist of layers composed of both flexible and rigid materials, offering support in areas requiring bending while retaining rigidity in other sections. This versatility makes them prevalent in various industries, including portable devices, aerospace applications, and medical devices.
Employing a multi-layer structure and advanced processes such as fine lines, blind holes, and buried holes, HDI substrates facilitate enhanced integration and performance in PCB designs. This results in high-speed signal transmission, increased circuit density, and reduced overall size.
This concluding part emphasizes the comprehensive product offerings of organic packaging manufacturers, which include flexible, rigid-flex, and HDI substrates to meet the diverse requirements of various industries and applications. Whether flexibility, high-density wiring, or a combination of both is needed, these manufacturers provide flexible solutions that offer a wide range of possibilities and convenience for designing and manufacturing electronic devices.
What are the advantages of organic packaging substrates?
First, organic packaging substrates excel in thermal management. Its optimized thermal management capabilities ensure the performance and reliability of electronic devices. By effectively dissipating heat, organic substrates can effectively reduce component temperatures and extend the service life of equipment while maintaining stable performance.
Second, organic packaging substrates have superior electrical properties that help improve signal integrity. These substrates support efficient signal transmission and reduce signal attenuation and crosstalk, ensuring data accuracy and stability. This is critical for applications with high frequency and high-speed data transmission, such as communications equipment and computer servers.
This passage highlights the advantages of utilizing organic packaging substrates in electronic device design. Firstly, it emphasizes their optimized thermal management properties, which help dissipate heat more efficiently, enhancing device reliability and performance. Secondly, it discusses the superior electrical properties of organic substrates, contributing to improved signal integrity and overall device functionality. Thirdly, it notes the compact and lightweight nature of organic substrates, enabling more flexible and intricate device designs while maintaining portability and aesthetics. Finally, the passage mentions the cost benefits associated with organic substrates, including streamlined production processes and reduced material costs, which ultimately lead to more affordable products for consumers. Overall, organic packaging substrates are portrayed as essential components in modern electronic device design, driving innovation and development in the electronics industry.
Why choose organic packaging substrate?
This passage discusses the advantages of organic packaging substrates over traditional substrates in contemporary electronics manufacturing. It emphasizes three key factors influencing this preference: versatility and adaptability, superior performance and reliability, and cost-effectiveness.
Organic packaging substrates are lauded for their flexibility, enabling them to accommodate intricate circuit layouts, thus catering to diverse application needs. Furthermore, these substrates exhibit outstanding thermal management and electrical properties, ensuring consistent operation and precise signal transmission, particularly crucial for demanding applications.
Secondly, organic packaging substrates offer superior performance and reliability compared to traditional materials. Their ability to dissipate heat effectively and maintain stable electrical properties enhances equipment longevity and signal accuracy, making them a preferred choice for manufacturers seeking dependable solutions.
This passage highlights the benefits of employing natural packaging materials, emphasizing their cost-effectiveness and strategic advantages for electronics producers. It clarifies that the efficient production processes and reduced spending on materials lead to lower manufacturing expenses and increased efficiency.This excerpt explores the benefits of employing organic packaging materials within the electronics sector. It emphasizes how companies can enhance their competitive stance by delivering superior products at competitive rates. The broad acceptance of natural packaging materials is credited to their adaptability, effectiveness, dependability, and economical nature. Consequently, this grants manufacturers a tactical edge in the dynamic electronics landscape.
What is the manufacturing process of organic packaging substrates?
The manufacturing process of organic packaging substrates is a meticulous and intricate procedure geared towards upholding the utmost industry standards in product precision and quality. Within the factories of organic packaging manufacturers, every phase is meticulously crafted and strictly regulated to ensure the dependability and efficiency of the final output.
Commencing with the material selection phase, organic packaging manufacturers meticulously opt for suitable organic materials, typically epoxy resin or polyimide, renowned for their superior electrical and mechanical properties. This initial selection bears significant weight as it directly impacts product performance and reliability.
Subsequently, the processing stage ensues, where the chosen material undergoes transformation into a substrate of the desired shape and size. This entails a sequence of procedural steps, including cutting, drilling, and surface treatment, each necessitating advanced equipment and technology to uphold substrate quality and uniformity.
Following this is the assembly phase, wherein electronic components are precisely affixed onto the substrate. This operation demands sophisticated automation equipment and technology to ensure accurate positioning and secure component attachment. Soldering and encapsulation procedures are also integral, shielding the electronic components from external environmental factors.
Lastly, the testing phase ensues, ensuring that the manufactured organic packaging substrate aligns with design specifications and performance requisites through rigorous testing and quality control protocols. These evaluations span electrical performance, reliability, and environmental adaptability testing to assure product stability and dependability.
In essence, the manufacturing process of organic packaging substrates constitutes a comprehensive endeavor involving multiple facets and technological advancements, striving to furnish high-quality, high-performance products. Through continual innovation and refinement, organic packaging manufacturers are dedicated to meeting customer demands and propelling the advancement of the entire electronics industry.
Applications in various industries?
The wide application of organic packaging substrates spans multiple key industries and plays a vital role in promoting technological innovation and improving product performance.
In the realm of consumer electronics, organic packaging substrates drive the efficiency of smartphones, tablets, and wearable devices. Employing these substrates enables manufacturers to attain compact, lightweight designs while ensuring heightened performance and dependability to satisfy the escalating demand for portable gadgets.
The automotive sector also reaps rewards from employing organic packaging substrates. These materials bolster advanced driver assistance systems (ADAS) and in-car entertainment setups, enriching the driving experience and augmenting safety measures. From sophisticated navigation systems to instantaneous data transmission, the superior performance and dependability of organic packaging substrates furnish a robust groundwork for automotive technological advancements.
Within the domain of medical devices, organic packaging substrates deliver dependability and accuracy for crafting life-saving medical apparatus. Ranging from medical monitoring gear to diagnostic imaging systems, the stability and efficiency of these substrates assure the precision and reliability of medical equipment, significantly impacting the advancement of healthcare.
Moreover, organic packaging substrates hold pivotal roles in the telecommunications sector, facilitating seamless connectivity and fortifying communication network infrastructure. From base station hardware to network routers, these substrates furnish essential support for communication technology development, fostering the establishment and proliferation of digital societies.
This paragraph essentially discusses the significant impact of incorporating organic packaging substrates across different industries. It highlights how this integration drives technological advancements, improves product performance, and enhances market competitiveness. Furthermore, it emphasizes the enduring importance of organic packaging substrates in facilitating sustainable and intelligent progress amid ongoing technological evolution and innovation.
How to find organic encapsulation manufacturers?
When searching for a reliable supplier of organic packaging substrates, it is imperative to engage with a reputable manufacturer. Leading manufacturers not only possess extensive industry experience but also leverage advanced technology and expertise to deliver tailored solutions that align with the dynamic market demands. To assist in selecting the manufacturer that best aligns with your requirements, consider the following recommendations:
Market Analysis:Prior to engaging in any collaboration, conduct extensive market analysis to assess the status and credibility of producers specializing in eco-friendly packaging materials. Employ online research, refer to industry publications, and solicit input from experts in the sector.
Supplier Assessment:Undertake a thorough evaluation of potential suppliers, taking into account factors such as their past performance, credentials, manufacturing capacities, and quality assurance protocols. Ensure that the selected supplier boasts a robust reputation and a dependable supply network.
Technological Proficiency:Verify that the supplier possesses cutting-edge technology and proficiency necessary for crafting bespoke solutions aligned with your project specifications. Evaluate their competency and ingenuity in eco-friendly packaging technology.
Quality Assurance:Opt for a manufacturer with a rigorous quality control system to guarantee that the produced organic packaging substrates meet your specified standards. Request relevant quality certifications and testing reports from the manufacturer.
Communication and Collaboration:Foster open communication with potential manufacturers to establish a clear understanding of project needs and expectations. Cultivate a strong working relationship to effectively address any issues that may arise and ensure seamless project execution.
By conducting thorough market analysis and assessing suppliers meticulously, while fostering open communication and collaboration with manufacturers, you can identify the ideal partner to deliver premium organic packaging substrates tailored to your project requirements.
Quote for organic packaging substrate?
When procuring an organic packaging substrate, obtaining an accurate quotation from the manufacturer is paramount. This not only aids in establishing a robust budget but also ensures the chosen final product aligns with the project’s requirements and specifications. Several crucial factors come into play when assessing an offer:
Variety of Organic Packaging Substrates: Different types of organic packaging substrates possess distinct characteristics and applications. Depending on project needs, one may require flexible, rigid, or a blend of both rigid and flexible substrates. Flexible substrates are apt for applications necessitating bending or folding, whereas rigid substrates are preferable for tasks demanding heightened mechanical strength.
Order Volume Impact: The quantity of purchase directly influences the quotation. Generally, bulk purchases offer a competitive advantage in pricing.
Securing a comprehensive understanding of these factors ensures an informed decision and an optimal outcome for the project.Therefore, when inquiring from manufacturers, the estimated order quantity should be accurately provided in order to obtain the most accurate quotation.
If the project requires customized organic packaging substrates, such as specific size, number of layers, aperture size or special process requirements, these customization requirements will also have an impact on the final quotation. Customized substrates often require additional processing and production steps, resulting in a corresponding increase in cost.
In addition to price, the transparency of quotes is also an important consideration in choosing a supplier. Make sure the quote is clear and includes all relevant fees and taxes. Knowing the details behind a quote can help you better understand why the price is formed and help you make informed decisions.
Prompt and adequate communication with the organic encapsulation manufacturer is also key to ensuring an accurate quote. Clearly communicate project needs and expectations so suppliers can provide you with the most appropriate solution and the most accurate quote.
In summary, obtaining an accurate organic packaging substrate quote is critical to the success of the project. Before selecting a supplier and developing a procurement plan, be sure to consider the above factors and ensure close communication and cooperation with the manufacturer to obtain a solution that best meets the project needs.
What are the advantages of Organic Packaging?
Organic Packaging offers several benefits, including improved signal integrity, enhanced thermal management, and increased design flexibility. These advantages contribute to the overall performance and reliability of electronic systems.
What distinguishes Organic Packaging from traditional PCBs?
Organic Packaging stands out by offering enhanced miniaturization, superior signal integrity preservation, and adaptability to complex geometries compared to conventional PCBs. It excels in modern electronic designs, showcasing its superiority in various scenarios.
What are the key advantages of Organic Packaging?
Organic Packaging brings several benefits, including improved signal integrity, efficient thermal management, and heightened design flexibility. These advantages contribute significantly to the overall performance and reliability of electronic systems.
How is Organic Packaging manufactured, and what are the key steps involved?
Organic Packaging involves intricate manufacturing processes for both motherboards and substrates. Motherboard production employs subtractive and additive methods with cutting-edge materials, while substrate fabrication utilizes techniques for achieving high-density interconnects, often incorporating organic materials like FR-4 and polyimide.
What types of Organic Packaging are available, and how do they cater to specific design needs?
Various types of Organic Packaging, such as HDI and flex PCBs, cater to diverse design requirements. HDI supports high-density interconnects, while flex PCBs provide flexibility for unique form factors. The choice depends on specific application needs.
How does the pricing of Organic Packaging solutions vary, and what factors influence quotes?
Organic Packaging quotes depend on factors such as substrate complexity, production volume, and customization features. Understanding these dynamics helps in making informed decisions aligned with project budgets and specifications.