Organic Substrate FC-BGA Design Guideline, we will help you to check the FCBGA substrates design questions, We are Professional FCBGA substrate manufacturer, we can produce the best samllest bump pitch with 100um, the best smallest trace are 9um.
In today’s electronics field, Printed Circuit Boards (PCBs) play a vital role, especially for the design of high-performance and high-density electronic devices. As a key component of PCB design, organic substrate FC-BGA is gaining more and more attention in modern electronic products. This article will provide an in-depth exploration of the design principles and best practices of organic substrate FC-BGA, providing valuable guidance for engineers and enthusiasts to help them better deal with complex electronic design challenges.
What is organic substrate FC-BGA?
Organic substrate FC-BGA (Flip-Chip Ball Grid Array) is a high-performance electronic packaging technology that connects chips to PCB (Printed Circuit Board) by flipping the chip. Compared with traditional BGA packaging, organic substrate FC-BGA uses organic substrates as carriers, providing higher performance and flexibility for circuit design.
In electronic design, organic substrate FC-BGA plays a vital role. First, it provides more space and freedom for the layout of high-density integrated circuits, allowing the circuit board to accommodate more functional modules and complex circuit structures. Secondly, the ball grid layout of the organic substrate FC-BGA provides better thermal management capabilities, helping to reduce the temperature of the circuit board and improve the stability and reliability of the system. In addition, the manufacturing process of organic substrate FC-BGA is relatively mature and can meet the needs of various complex circuit designs, providing reliable technical support for the rapid development and production of electronic products.
In general, the application of organic substrate FC-BGA in electronic design can not only improve the performance and reliability of circuits, but also speed up product time to market and reduce development costs, so it is favored by electronic engineers and manufacturers.
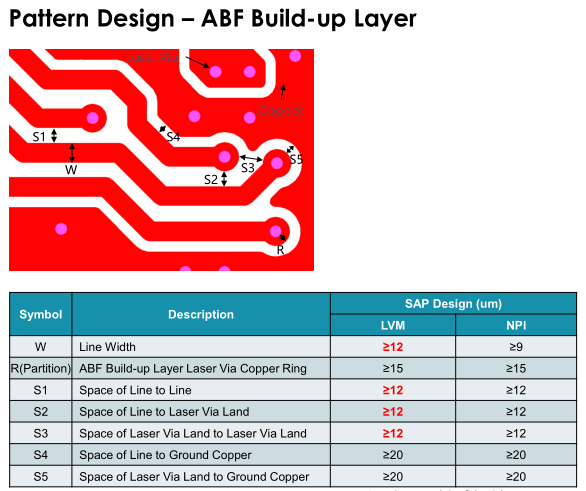
Organic Substrate FC-BGA Design Guideline
How to design organic substrate FC-BGA?
When designing an organic substrate FC-BGA, several key factors need to be considered to ensure good reliability and performance in the final design. These factors and corresponding design guidance are described in detail below.
First, designers should fully understand the functional requirements and performance specifications of the circuit. This includes having a clear understanding of the circuit’s operating frequency, signal integrity requirements, power consumption characteristics, etc. By in-depth understanding of circuit requirements, guidance can be provided for subsequent layout and routing.
Secondly, reasonable layout is one of the keys to ensuring the success of the design. In the layout stage, it is necessary to rationally arrange the positions of each functional module to minimize the length and complexity of the signal transmission path to reduce the possibility of signal interference and crosstalk. At the same time, ensure that the layout meets the signal integrity requirements of the circuit to avoid signal reflections and timing distortion.
During the routing phase, designers need to pay attention to maintaining good signal integrity. This includes using appropriate width wires, reducing wire bends and splits, and properly managing the distance between signal and power layers. By taking these measures, the transmission loss and delay of the signal can be reduced and the performance of the circuit can be improved.
In addition, designers need to consider factors such as thermal management and electromagnetic compatibility. In terms of thermal management, the heat dissipation structure needs to be properly designed to ensure that the circuit can maintain a stable temperature when working for a long time. In terms of electromagnetic compatibility, measures need to be taken to reduce electromagnetic radiation and sensitivity to ensure that circuits can work properly in complex electromagnetic environments.
Finally, designers also need to fully consider manufacturing feasibility and cost-effectiveness. During the design stage, you should try to choose common materials and processes and avoid using overly complex or expensive technologies. At the same time, attention should be paid to the maintainability and testability of the design so that subsequent production and maintenance work can proceed smoothly.
In summary, designing organic substrate FC-BGA requires comprehensive consideration of multiple factors such as circuit requirements, layout and routing, thermal management, electromagnetic compatibility, and manufacturing feasibility and cost-effectiveness. Through reasonable design processes and strict design specifications, we can ensure that the final design has good reliability and performance and meets the various requirements of the circuit.
What is the manufacturing process of organic substrate FC-BGA?
The manufacturing process of organic substrate FC-BGA is a complex and precise process involving multiple critical steps, each of which must be performed precisely to ensure the quality and reliability of the final product.
First, the manufacturing process begins with the preparation phase of the substrate material. At this stage, we select high-quality organic substrate materials, usually fiberglass-reinforced epoxy resin (FR-4), to ensure that the board has sufficient mechanical strength and heat resistance.
Next comes the laminating and laminating stage. At this stage, the layers of the multi-layer substrate are stacked according to the design requirements, and lamination equipment is used to firmly press them together to form an overall structure.
Inner layer circuit pattern generation is one of the key steps in the manufacturing process. At this stage, the circuit pattern of the inner layer is formed on the substrate through chemical processing according to the design file. The accuracy and precision of this step have a profound impact on subsequent processes.
The outer layer line pattern generation is similar to the inner layer, but on the outer layer, we usually use finer line widths and line spacing to meet higher density layout requirements. This requires highly precise photolithography and etching processes to achieve.
Mask pattern generation is used to define pads and component mounting areas. By coating a layer of solder resist on the surface of the board, and using photolithography and etching techniques to form a mask pattern, it protects areas that do not require soldering and provides accurate locations for soldering.
Drilling is done to create pass-through holes and mounting holes in the board. Precise positioning and drilling operations are performed through CNC drilling machines to ensure the accuracy and consistency of hole locations.
Electroplating is an important step in depositing copper onto via holes and trace patterns. Electroplating provides electrical connections and surface protection to protect copper from environmental oxidation and corrosion.
Etching is the process of removing unwanted copper layers from the board. Through chemical etching, only the circuit pattern and pad area are retained, and the excess copper is etched away to form the final circuit board structure.
Pad coating is used to protect the pad area and provide a solderable surface. This usually involves applying a layer of solder film or flux to the pad area to prevent oxidation and improve soldering reliability.
Finally comes the molding and final inspection stage. During the molding process, the boards are cut to the required dimensions and surface treated to remove possible dust and contamination. The final inspection phase includes visual inspection, dimensional measurements, electrical testing and reliability assessment of the board to ensure compliance with quality standards.
Throughout the manufacturing process, strict quality control and process monitoring are crucial to ensure that each step can be performed as required and ultimately produce high-quality organic substrate FC-BGA that meets design requirements.
How much does it cost to design an organic substrate FC-BGA?
Cost is an important consideration when considering designing FC-BGAs on organic substrates. The design cost depends on many factors, including substrate material, number of layers, line width/line spacing requirements, impedance control, pad shape, etc. Therefore, design costs can vary significantly from project to project.
First, substrate material is an important component of design cost. Generally, high-performance organic substrate materials are relatively expensive, while some common substrate materials such as fiberglass reinforced epoxy resin (FR-4) are relatively cheap. Additionally, design costs may increase further if the project requires the use of special materials or substrates of specific thicknesses.
Secondly, the number of layers will also directly affect the design cost. Compared with single-layer substrates, the manufacturing cost of multi-layer substrates will be higher. This is because multi-layer substrates require more production steps and more complex processes, which increases manufacturing costs.
In addition, design requirements such as line width/line spacing requirements, impedance control, and pad shape will also have an impact on cost. For example, smaller line width/line spacing requirements and tighter impedance control can increase production complexity and cost. Specially shaped pads may require additional processing steps, further increasing costs.
In terms of controlling design costs, we can take some effective measures. First, we can reduce costs by optimizing the design. Through rational layout and simplifying the design as much as possible, manufacturing complexity and material waste can be reduced, thereby reducing costs. Second, we can select the right suppliers and manufacturing processes to ensure optimal value without sacrificing quality. Adequate communication and consultation with suppliers can help us understand the key cost drivers in the production process and take appropriate measures to reduce costs.
Overall, designing the cost of organic substrate FC-BGA is a complex issue that takes multiple factors into consideration. Through reasonable design optimization and partner selection, we can effectively control design costs without sacrificing quality, thereby achieving successful project implementation.
What materials are used in organic substrate FC-BGA?
In the design and manufacturing process of organic substrate FC-BGA, a variety of materials are used, each playing an important role to ensure the performance, reliability and cost-effectiveness of the PCB. The following are the main materials and their characteristics:
Organic Substrate: Organic substrate is the core component of PCB and is mainly composed of glass fiber reinforced epoxy resin (FR-4). This material has excellent mechanical strength and thermal stability, making it suitable for most electronic applications. FR-4 substrate also has good electrical insulation properties and corrosion resistance, making it one of the preferred materials for PCB manufacturing.
Copper Foil: Copper foil is used to form the conductive layer on the PCB and is responsible for transmitting signals and power. Copper foil has good electrical conductivity and processability, and can meet high-speed signal transmission and high current requirements. In addition, the good weldability and corrosion resistance of copper foil also make it one of the indispensable materials in PCB manufacturing.
Solder Mask: Solder mask is applied to the PCB surface to cover the copper foil to protect the circuit from the environment. Solder resist is usually made of photo-curing or thermo-curing resin, which has good heat resistance and chemical stability. They are often available in a variety of colors to differentiate between functional areas and provide surface flatness for easier assembly and soldering.
Solder Pad: The solder pad is a key component connecting the pins of electronic components and the PCB. They are gold-plated or tin-plated to improve soldering quality and reliability. Pads are typically applied to the PCB surface and connected to electronic components through soldering techniques during assembly. They must have sufficient surface tension and heat resistance to ensure a good solder connection.
Printing ink (Legend): Printing ink is used to print logos and marks on the PCB surface, such as component pin marks, circuit board version numbers, etc. They generally have good adhesion and abrasion resistance to maintain long-term visibility and readability.
The above materials together form an important part of the organic substrate FC-BGA, and their selection and application affect the performance, reliability and cost of the PCB. Through reasonable material selection and optimized design, high-quality organic substrate FC-BGA can be realized to meet the needs of various electronic applications.
Who manufactures organic substrate FC-BGA?
In the process of manufacturing organic substrate FC-BGA, supplier selection is crucial. As a professional electronics manufacturing company, we are proud to announce that our company is one of the major suppliers of organic substrate FC-BGA.
As your supplier, we are committed to providing high-quality organic substrate FC-BGA to meet your design needs. We have advanced production equipment and technical team, able to provide you with a full range of support and services in design, manufacturing and quality control.
Our company is equipped with advanced production equipment, including automated printing, punching, drilling, etching and pad coating equipment. These equipment can ensure product production efficiency and quality stability to meet your mass production needs.
We have an experienced technical team with deep industry knowledge and technical expertise. Whether it’s design review, process optimization or quality management, our team can provide professional advice and support to help you achieve project success.
During the manufacturing process, we strictly implement quality control processes to ensure that each organic substrate FC-BGA meets the highest quality standards. From raw material procurement to finished product inspection, we strictly control every link to ensure product stability and reliability.
We provide customized solutions to meet your specific needs and requirements. Whether it is in terms of design specifications, material selection or production volume, we are able to flexibly adjust and provide the best solutions to ensure that your project goes smoothly.
As a supplier of organic substrate FC-BGA, our company is committed to providing customers with high-quality, reliable and customized products and services. We believe that through our efforts and cooperation, your project will be successful. Look forward to working with you!
What are the five qualities of great customer service?
What qualities should we possess as customer service providers? How to ensure customer satisfaction? In a highly competitive market, quality customer service is the key to a company standing out. Here are five key attributes that help ensure customer satisfaction and build long-term customer relationships:
Prompt response to customer inquiries and questions is a basic requirement of excellent customer service. Customers expect quick answers or solutions when they have a problem or need help. As a customer service provider, we need to establish efficient communication channels and respond to customer needs in a timely manner to demonstrate our professionalism and responsibility.
Empathy is key to building great customer relationships. Understand and empathize with customer needs, concerns and emotions to better connect with customers and provide personalized services. By listening to and paying attention to customer feedback, we can better meet customer expectations, increase customer satisfaction and build long-term trusting relationships.
Customers expect to find reliable support and service in their partners. As a customer service provider, we need to consistently deliver on our promises and ensure high-quality products and services. Building a reliable reputation will help attract more customers and keep them loyal.
Clear and effective communication is an important part of great customer service. We need to maintain open and transparent communication with our customers, share important information in a timely manner, and answer any concerns and questions our customers may have. By establishing a good communication mechanism, we can better understand our customers’ needs, avoid misunderstandings, and improve customer satisfaction.
Resolving customer issues quickly and efficiently is at the heart of great customer service. We need to have good problem-solving skills and innovative thinking to deal with various complex situations and provide customers with satisfactory solutions. By proactively solving problems, we are able to establish a good corporate image and win the trust and support of our customers.
To sum up, excellent customer service is not just about providing products and services, but also the process of building long-term trusting relationships. By possessing attributes such as responsiveness, empathy, reliability, communication skills and problem-solving skills, we ensure customer satisfaction, enhance brand reputation and achieve lasting business success.
FAQS
What factors influence the cost of organic substrate FC-BGA design and manufacturing?
The cost of organic substrate FC-BGA design and manufacturing is influenced by factors such as substrate material selection, layer count, trace width/spacing requirements, impedance control, and solder pad shapes.
Can organic substrate FC-BGA designs accommodate high-speed and high-density applications?
Yes, organic substrate FC-BGA designs can accommodate high-speed and high-density applications with proper layout techniques, signal routing, and impedance matching.
How do we ensure reliability in organic substrate FC-BGA assemblies?
Reliability in organic substrate FC-BGA assemblies is ensured through rigorous quality control measures, including thorough testing, adherence to industry standards, and proper handling during assembly and operation.
What are the advantages of using organic substrate FC-BGA in electronic systems?
The advantages of using organic substrate FC-BGA in electronic systems include enhanced thermal performance, improved electrical properties, and cost-effectiveness compared to alternative packaging solutions.