Professional Package substrate manufacturer, We offer Package substrate prototypes up to mid-volume production. we mainly produce ultra-small bump pitch substrate, ultra-small trace and spacing packaging substrate and HDI PCBs.
The packaging substrate, referred to as PCB (Printed Circuit Board), is a key electronic component, usually made of insulating materials with conductive paths and connection points printed on it. These paths and connection points form the basic circuit structure of electronic devices.
In the realm of contemporary electronics, packaging substrates stand as an essential component, furnishing the structural support and electrical connections vital for the seamless operation of electronic devices. Serving as the carrier for electronic components, these substrates play a crucial role in connecting and supporting an array of chips, resistors, capacitors, and other integral elements. Their significance extends to influencing the performance, reliability, and stability of electronic devices. This article aims to explore various facets of packaging substrates, spanning from material characteristics to manufacturing methodologies, and further delving into emerging trends that shape the future landscape of this fundamental electronic component..
What is a packaging substrate?
Packaging substrate is a key electronic component, usually a plate-like structure made of dielectric materials. Its basic function is to provide a bridge between the supporting structure of electronic devices and the connecting circuit. These substrates serve as critical foundations in electronic devices, carrying various chips and circuit components, allowing them to communicate with each other and work together.
In contemporary electronic devices, the role of packaging substrates is paramount. These substrates serve as essential elements by offering mechanical support and establishing electrical connections. They facilitate the collaboration of diverse chips and components, culminating in the creation of a comprehensive circuit system. Beyond being mere physical supports for electronic elements, packaging substrates also function as conduits for current transmission and signal conduction. The quality and intricacy of the packaging substrate directly impact the device’s performance, reliability, and longevity. Consequently, a thorough comprehension of fundamental packaging substrate concepts is crucial for fine-tuning the design and optimizing the overall performance of electronic devices.
Material Properties of Package Substrate
A pivotal characteristic of packaging substrates lies in their dielectric materials, a crucial factor determining performance and reliability. Let’s delve into an in-depth exploration of dielectric materials within packaging substrates and the consequential impact of material selection on overall performance.
Dielectric materials in packaging substrates play a fundamental role in establishing interlayer insulation. Common options include fiberglass-reinforced epoxy (FR-4), polyimide (PI), and polytetrafluoroethylene (PTFE), notably utilized in high-density interconnect boards (HDI). These materials exhibit varying dielectric constants and thermal properties, necessitating careful consideration during selection for specific applications.
FR-4, recognized for its cost-effectiveness and robust mechanical strength, stands as a prevalent choice for numerous common applications. Conversely, PI finds extensive use in high-end electronic equipment, attributed to its elevated temperature stability and superior electrical properties. In the realm of HDI technology, PTFE emerges as the material of choice for achieving higher frequencies and mitigating signal distortion.
Material selection profoundly shapes packaging substrate performance. For instance, in applications requiring high-frequency performance, the careful choice of materials with low dielectric constants becomes critical to minimize signal distortion during transmission. High-temperature stable materials, like polyimide, ensure unwavering performance in extreme operating conditions.
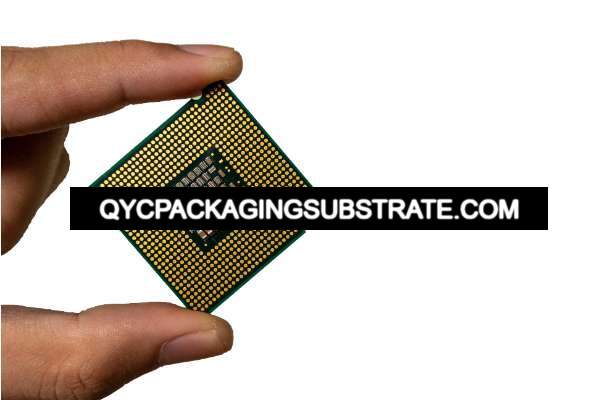
Package substrate dielectric marke
Furthermore, considerations extend beyond dielectric properties to encompass mechanical strength, thermal stability, and chemical resistance. The selection process must weigh these factors, especially for applications demanding stability in high temperatures or harsh environments, making overall material performance a comprehensive consideration.
In packaging substrate design, engineers must weigh these factors and select the most appropriate materials based on the specific needs of the application to ensure that the product performs well in all aspects.
In summary, the material properties of the packaging substrate are a key factor in determining its performance and reliability. Careful selection and balance of different dielectric materials will help meet the needs of diverse electronic applications.
Manufacturing process of packaging substrate
The production process of packaging substrates is a pivotal facet of the electronics industry, intricately linked to the performance and reliability of electronic equipment. The subsequent discussion will intricately explore the manufacturing process of packaging substrates, shedding light on its intricate and exacting procedures, encompassing key steps and technologies crucial to the final product’s quality and functionality.
Revealing the manufacturing process of packaging substrates
The manufacturing process of packaging substrates often involves multiple stages, each of which has a profound impact on the quality of the final product. First, select the appropriate substrate material, which is directly related to the dielectric properties and heat dissipation performance. The different materials are then layered together through a lamination process to form the basic structure of the substrate. This process requires highly sophisticated equipment and technology to ensure that each layer is positioned and connected accurately.
The production process of packaging substrates unfolds through several crucial stages, each exerting a significant impact on the ultimate quality of the end product. Initial considerations involve the selection of an appropriate substrate material, a decision that directly influences dielectric properties and heat dissipation performance. Subsequently, these diverse materials undergo a lamination process where they are intricately layered to establish the fundamental structure of the substrate. This intricate step necessitates cutting-edge equipment and technology to ensure precise positioning and connection of each layer.
The subsequent stage involves copper foil bonding, wherein copper foil is securely affixed to the substrate to confer conductive properties to the circuit. Achieving a robust and dependable bond between the copper foil and the substrate demands meticulous control of temperature and pressure.
The final phase encompasses the formation of the circuit pattern on the substrate’s surface using high-density interconnection technology. This pivotal step in the manufacturing process directly shapes the performance and power consumption of electronic devices, underscoring its critical significance.
Highlight key process steps and techniques
In the manufacturing of packaging substrates, the application of key process steps and technologies is crucial.
Precision control of the lamination process: ensuring that the thickness, material and positioning of each layer meet design requirements. This requires advanced manufacturing equipment and highly precise process control.
Copper foil bonding technology employs sophisticated techniques to establish a robust connection between the copper foil and the substrate, ensuring exceptional conductive properties.
In parallel, high-density interconnection technology relies on advanced printing and etching methodologies to guarantee the precision and clarity of circuit patterns. This approach is crucial in meeting the exacting demands for high performance and stability in electronic devices.
The successful application of these process steps requires manufacturers to possess highly specialized knowledge and technical capabilities to address the various challenges in packaging substrate manufacturing.
The meticulous execution of crucial process steps and advanced technologies is the linchpin in guaranteeing the quality of packaging substrate manufacturing. This necessitates not only cutting-edge equipment and technology but also a proficient team and a commitment to ongoing innovation to align with the dynamic requirements of the ever-evolving electronics industry.
Application of packaging substrates in the electronics industry
As an indispensable component of modern electronic equipment, packaging substrates are widely used in various fields and provide solid support for the development of the electronics industry. The following is an introduction to the wide application of packaging substrates in electronic devices and some actual successful cases.
Introducing the wide application of packaging substrates in electronic equipment
Printed Circuit Board (PCB): The packaging substrate plays a key role in PCB manufacturing by providing mechanical support and electrical connections to enable the orderly arrangement of electronic components. PCB is the “skeleton” of electronic equipment, and the high reliability and performance optimization of the packaging substrate are crucial to the stability of the overall equipment.
Chip packaging: In the manufacture of integrated circuits, packaging substrates are used to protect and connect chips. Advanced packaging technology enables electronic devices to integrate more functions in a smaller space, improving the performance density and efficiency of the device.
Communication equipment: Packaging substrates play a key role in wireless communication equipment, supporting signal transmission and processing. From smartphones to base station equipment, the high performance of packaging substrates ensures the stable operation of communication systems.
Consumer Electronics: Consumer electronics products such as televisions, audio systems, and home appliances extensively utilize packaging substrates to enable advanced functionality and superior performance.
Practical application cases and success stories
Medical Devices: In the healthcare industry, a leading medical device manufacturer has adopted advanced packaging substrate technology to make its next generation of medical imaging equipment lighter and more reliable while delivering higher image resolution.
Industrial Automation: An industrial automation solutions provider uses advanced packaging substrates to make control systems on its production lines more compact and reliable, improving production efficiency.
Through these practical cases, we can clearly see the diverse applications of packaging substrates in various industries, providing a solid foundation for the innovation and performance improvement of electronic equipment. This also reflects the irreplaceable position of packaging substrates in promoting the development of the electronics industry.
Future trends in packaging substrates
As an important part of the electronic field, packaging substrates present eye-catching potential and innovation in their future development. The following is a discussion of future trends in packaging substrate technology:
Discuss the future development direction of packaging substrate technology
In the future, packaging substrate technology will move towards more advanced and complex directions. First, high-density interconnect technology will become a key trend to meet the needs of ever-shrinking device sizes and more complex circuits. This will drive packaging substrates toward more compact, higher-performance designs.
Secondly, advanced heat dissipation and thermal management technology will become the focus of future development of packaging substrates. As power consumption in electronic devices increases, effective thermal management becomes critical. Future packaging substrates will pay more attention to heat dissipation performance and use innovative materials and designs to ensure that devices maintain stable performance under high loads.
In addition, multi-layered and multi-functional packaging substrates will become a future trend. As the demand for multi-functionality in electronic devices continues to increase, packaging substrates will not only be the carrier of circuits, but will also integrate various sensors, antennas and other functions to achieve more diverse applications.
Industry demand for innovation
The rapid development of the electronics industry has put forward higher innovation requirements for packaging substrates.This will prompt the packaging substrate industry to pay more attention to R&D investment and promote continuous upgrading of technology.
Simultaneously, a heightened consciousness regarding sustainability and environmental conservation is catalyzing advancements in packaging substrate technology. Manufacturers are placing a greater emphasis on adopting eco-friendly materials and manufacturing processes to mitigate their environmental footprint. This dual focus not only aligns with market expectations but also contributes to shaping the company’s image as a socially responsible entity.
Fueled by a commitment to innovation, packaging substrates will persist in their pivotal role within the electronics sector. This ongoing evolution promises to lay the foundation for future generations of smart, efficient, and environmentally friendly electronic devices.