What is PGA Package Substrate?
PGA Package Substrate Vender and PGA Package Service.High speed and high frequency material packaging substrate manufacturing. Advanced packaging substrate.
PGA Package Substrate is an integral and critical component of modern electronic packaging. It is a specially designed substrate designed to support pin array configurations of electronic components, providing a solid foundation for device packaging. In electronic devices, PGA Package Substrate plays a vital role as it not only provides mechanical support for electronic components but also ensures good electrical connections. So, how does PGA Package Substrate ensure the performance, reliability and miniaturization of device packaging?
First, the PGA Package Substrate is architected for optimal electrical performance. Through precise wiring and tight electrical connections, it ensures stable and reliable signal transmission, thereby improving the performance of the device. Whether it is data transmission or power transmission, PGA Package Substrate can effectively meet the needs of various electronic devices and provide them with a stable electrical environment.
Secondly, PGA Package Substrate also has excellent thermal management capabilities. In modern electronic equipment, thermal issues are a challenge that cannot be ignored, and PGA Package Substrate effectively solves this problem through excellent heat dissipation performance. Through appropriate material selection and optimized design, PGA Package Substrate is able to effectively conduct heat from electronic components to the surrounding environment, ensuring that the device maintains a stable temperature over long periods of operation.
In addition, PGA Package Substrate also helps achieve device miniaturization and weight reduction. As electronic devices become more and more miniaturized and portable, the compact design and high integration level of PGA Package Substrate make the device’s packaging structure more compact, thus saving valuable space. This not only helps improve the portability of the device, but also helps reduce production costs.
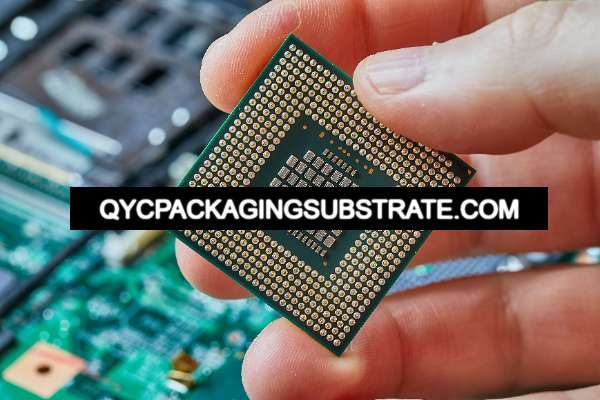
PGA Package Substrate
Overall, PGA Package Substrate is a key electronic packaging material that ensures the performance, reliability and miniaturization of electronic devices by providing excellent electrical performance, excellent thermal management capabilities, and compact packaging structure. In the field of modern electronic engineering, the application of PGA Package Substrate will continue to play an important role in promoting the continuous innovation and progress of electronic equipment.
What types of PGA Package Substrate are there?
As a key component in electronic component packaging, PGA Package Substrate has various types to suit different application needs. The following will introduce the main types and characteristics of PGA Package Substrate:
Organic PGA Package Substrate uses organic substrates such as glass fiber reinforced resin (FR-4), which has lower cost and good mechanical properties. They are suitable for general electronic applications, providing reliable electrical connections and modest thermal management capabilities.
Ceramic PGA Package Substrate uses high-temperature ceramic materials with excellent high-temperature resistance and electrical insulation properties. They are suitable for high power and high frequency applications and provide excellent thermal management and signal transmission performance.
Metal substrate PGA Package Substrate uses a metal substrate, such as aluminum or copper, which has excellent heat dissipation performance and mechanical strength. They are suitable for electronic devices that require higher thermal management capabilities, such as LED lighting and power modules.
Flexible PGA Package Substrate uses a flexible substrate, such as polyimide (PI) or polyester film, which is flexible and lightweight. They are suitable for curved packaging and tight space applications, and can provide reliable electrical connections and moderate thermal management.
These different types of PGA Package Substrate have their own advantages and disadvantages in terms of material selection, performance characteristics, and applicable scenarios. Engineers need to make comprehensive considerations based on specific application requirements when making selections.
What are the advantages of PGA Package Substrate?
As an important part of the electronic packaging field, PGA Package Substrate has many advantages. These advantages are not only reflected in performance improvements, but also have a positive impact on overall device performance, reliability, and manufacturing costs. The following is a detailed introduction to the advantages of PGA Package Substrate:
First, PGA Package Substrate has significant advantages in thermal management. Its material properties and structural design enable it to effectively conduct and dissipate heat, thereby improving the thermal stability and performance of the device. Especially in high-power applications, PGA Package Substrate can effectively reduce the operating temperature of the device and extend its service life.
Second, PGA Package Substrate excels in electrical performance. Due to its precise manufacturing process and high-quality materials, PGA Package Substrate can provide stable electrical connection and transmission performance, ensuring the stable operation and high-speed signal transmission of the equipment, helping to improve the overall performance and reliability of the system.
In addition, PGA Package Substrate offers excellent mechanical strength and stability. Its structural design and material selection have been carefully optimized to maintain a stable structure under various environmental conditions and resist external vibration and shock, thus improving the durability and reliability of the equipment and reducing maintenance and replacement costs.
Another advantage of PGA Package Substrate is its miniaturization capabilities. Due to its compact structure and precise dimensions, PGA Package Substrate can achieve higher device integration and smaller package size, helping to design thinner and more compact electronic devices to meet the needs of modern electronic products for miniaturization and portability. .
Finally, PGA Package Substrate also has certain advantages in terms of cost. Compared with other packaging technologies, the manufacturing process of PGA Package Substrate is more mature, the production efficiency is higher, and it can achieve mass production, thereby reducing costs and providing customers with a competitive price and performance ratio.
To sum up, PGA Package Substrate provides comprehensive support for the design and manufacturing of electronic devices with its advantages in thermal management, electrical performance, mechanical stability, miniaturization and cost, and promotes the innovation and development of electronic products. develop.
Why choose PGA Package Substrate?
In the field of modern electronic packaging, PGA Package Substrate plays a vital role. Compared with traditional PCB boards, they have obvious advantages in many aspects. First, PGA Package Substrate excels in high-density pin layout. Traditional PCB boards may face challenges when dealing with high pin counts and fine pitches, while PGA Package Substrate can support higher-density pin layouts and provide more compact packaging solutions through precision manufacturing processes and design optimization.
Secondly, PGA Package Substrate has significant advantages in thermal management. For high-power electronic equipment, such as servers, industrial control equipment, etc., effective dispersion of heat is crucial. PGA Package Substrate usually uses high thermal conductivity materials, and through optimized thermal design, it can effectively conduct heat from electronic devices to the radiator or housing to ensure stable operation of the device.
In addition, PGA Package Substrate also performs well in terms of electrical performance and signal transmission. Due to its optimized design structure and material selection, PGA Package Substrate can provide lower signal transmission loss and higher signal integrity, ensuring reliable transmission of data and signals. It is especially suitable for application scenarios with high signal quality requirements. Such as communication equipment, medical equipment, etc.
In some cases, choosing PGA Package Substrate can also bring production cost savings. Although the manufacturing process of PGA Package Substrate may be slightly more complicated than that of traditional PCB boards, since it provides a more compact and higher-performance packaging solution, it can reduce the overall material cost and packaging cost of the system, thus improving the efficiency to a certain extent. production efficiency and reduced overall costs.
In summary, based on its advantages in high-density layout, thermal management, electrical performance and cost-effectiveness, PGA Package Substrate is a more preferred packaging solution in certain specific application scenarios. Especially for electronic devices that require high performance, miniaturization and reliability, choosing PGA Package Substrate can provide designers and engineers with greater flexibility and innovation space, and promote the progress and development of electronic technology.
What is the manufacturing process of PGA Package Substrate?
The manufacturing process of PGA Package Substrate is a complex and precise process that requires multiple critical steps to ensure that the final product has precise dimensions and reliable electrical connections. Here are the main steps of this process:
The first step in manufacturing a PGA Package Substrate is to prepare the substrate. This usually involves selecting a substrate of appropriate material, such as an organic material, a ceramic or a metallic substrate, chosen based on the requirements of the specific application. The substrate must have the proper thickness and surface flatness to ensure the accuracy of subsequent process steps.
Next, materials are stacked layer by layer on the substrate to form the desired circuit structure. This typically involves using thin film materials, copper foil, or other conductive materials that are layered and pressed to form a multilayer structure. Each layer must be precisely positioned and aligned to ensure the final electrical connection.
Once the stack-up is complete, the next steps are patterning and circuit fabrication. This involves using photolithography or other patterning techniques to transfer the desired circuit pattern to the substrate surface. Then, chemical etching or other processing methods are used to remove the unwanted material and form the desired circuit structure.
After the circuit is completed, metallization needs to be performed on the surface of the substrate to form a reliable electrical connection. This usually involves depositing a metal layer, such as gold plating, nickel plating, or other conductive material, over the circuit pattern. The metallization process ensures good connection and conductivity between circuits.
Finally, surface treatments are performed to improve the durability and reliability of the substrate. This may include applying anti-corrosion coatings, adding protective layers, or other surface treatments to ensure that the substrate maintains good performance in a variety of environmental conditions.
Through the above steps, the manufacturing process of PGA Package Substrate can ensure that the substrate has precise dimensions and reliable electrical connections. Each step requires strict control and precision processing to ensure the final product meets high quality and performance standards.
What are the application areas of PGA Package Substrate?
PGA Package Substrate is a key electronic packaging technology with wide applications in various industries. Its flexibility and reliability allow it to meet the needs of different fields. Here are some of the main application areas:
In the field of communications and networks, equipment is required to have high performance and reliability, as well as miniaturization and high-density integration. PGA Package Substrate provides excellent electrical performance and thermal management capabilities, making it an ideal choice for equipment such as network routers, switches, and communication base stations.
Industrial automation and control systems often require processing large amounts of sensor data and executing complex control algorithms. PGA Package Substrate provides high-density pin connections to support the integration of a variety of sensors and actuators. Its excellent thermal management performance is also suitable for industrial scenarios in high-temperature environments.
In the field of automotive electronics, electronic components are required to have the characteristics of high temperature resistance, vibration resistance and high reliability. PGA Package Substrate provides excellent mechanical strength and thermal management capabilities and is suitable for applications such as automotive control units, in-vehicle entertainment systems, and driver assistance systems.
Medical devices often require compact designs, stable performance and long-term reliability. PGA Package Substrate can meet these requirements and is widely used in medical equipment and instruments such as heart rate monitors, X-ray machines, and medical imaging equipment.
In the aerospace and defense fields, electronic equipment is required to be lightweight, high-strength, and highly reliable. PGA Package Substrate’s thin and light design and excellent thermal management performance make it the first choice for applications such as satellite communications equipment, navigation systems and military radars.
The application of PGA Package Substrate in the above fields benefits from its diverse material selection, flexible design and reliable performance, providing a stable and reliable foundation for electronic equipment in different industries.
Where can I find PGA Package Substrate?
When looking for a reliable PGA Package Substrate supplier, there are several sources to consider. First, you can find suppliers through professional exhibitions and conferences in the industry. These shows typically attract a variety of electronic component and materials manufacturers, including suppliers of PGA Package Substrate. Attending these exhibitions allows you to communicate directly with suppliers, learn about their products and services, and establish connections.
Second, you can search the Internet to find suppliers of PGA Package Substrate. Many suppliers have websites or online platforms where their product catalogs, technical specifications and company profiles can be viewed. An online search can help you find multiple suppliers around the world and help compare products and prices from different suppliers.
In addition, you can also find suppliers through professional forums and social media platforms in the industry. On these platforms, industry experts and practitioners often share their experiences and advice, including recommendations for reliable suppliers. By participating in discussions and asking questions, you can get useful information and contact details.
As our company, we can provide our customers with a variety of services and solutions. First, we can provide customized PGA Package Substrate solutions according to customer needs, including different types of substrate materials, sizes and technical specifications. Secondly, we have advanced manufacturing equipment and technical team, which can guarantee product quality and delivery cycle. In addition, we also provide technical support and after-sales service to ensure customer smoothness and satisfaction during use.
In summary, finding a reliable PGA Package Substrate supplier requires searching and comparing through multiple sources. As a supplier, we are committed to providing customers with high-quality products and professional services to meet their needs and achieve mutual development.
What is the quote for PGA Package Substrate?
Quoting PGA Package Substrate is a complex process involving many factors. When determining a quote, suppliers typically consider the following key factors:
Material Cost: The cost of PGA Package Substrate is mainly affected by the price of the materials used. Different types of substrate materials (such as organic materials, ceramic materials, metal substrates, etc.) have large price differences, which have an important impact on the final quotation.
Manufacturing process: The manufacturing process of PGA Package Substrate involves a variety of complex processes, including substrate preparation, layer stacking, metallization, surface treatment, etc. Different processes require different equipment, technology and labor costs, which will directly affect the cost.
Size and number of layers: The size and number of layers of the PGA Package Substrate also have a significant impact on cost. Larger size or multi-layer substrates usually require more materials and processes, so the cost will increase accordingly.
Production batch size: Production batch size is one of the important factors affecting the cost of PGA Package Substrate. Generally speaking, large-volume production can reduce unit costs, while small-volume production is relatively costly.
Customization requirements: If customers have special customization requirements, such as specific materials, thicknesses, surface treatments, etc., additional costs will usually be added. Custom production typically requires more process adjustments and manual operations.
Taking the above factors into consideration, the supplier will make reasonable pricing based on the customer’s specific needs and specifications, combined with market conditions and production costs. Therefore, the price quoted for PGA Package Substrate may vary for different projects and customers.
Frequently Asked Questions (FAQs)
How do PGA Package Substrates differ from other package substrate types?
PGA Package Substrates are specifically designed to support pin grid array configurations in electronic components, providing a robust foundation for interconnecting pins or leads. Unlike traditional PCBs, PGA Package Substrates offer enhanced thermal dissipation, improved electrical performance, and miniaturization capabilities, making them ideal for high-pin-count applications requiring reliable signal transmission and thermal management.
What factors should be considered when selecting PGA Package Substrates for a particular application?
When selecting PGA Package Substrates, several factors should be considered, including thermal conductivity, dielectric strength, mechanical stability, and compatibility with the intended application environment. Additionally, considerations such as pin count, pitch size, and package size should align with the specific requirements of the electronic device and its operating conditions.
Are PGA Package Substrates compatible with surface-mount technology (SMT) components?
Yes, PGA Package Substrates can be compatible with surface-mount technology (SMT) components. However, compatibility may vary depending on factors such as substrate material, surface finish, and component size. Proper design and assembly techniques should be employed to ensure optimal solderability and reliability of SMT components on PGA Package Substrates.
Can PGA Package Substrates be used in high-frequency applications?
Yes, PGA Package Substrates can be used in high-frequency applications. However, careful consideration should be given to substrate material properties, signal integrity, and impedance control to minimize signal loss and ensure optimal performance at higher frequencies. Advanced design and manufacturing techniques may be required to meet the stringent requirements of high-frequency applications.