Radar/Antenna Substrate Manufacturer, we mainly produce ultra-small bump pitch substrate, ultra-small trace and spacing packaging substrate.
Radar and antenna technology play an integral role in modern communications and wireless. Their performance and reliability are directly related to the quality and stability of communication. In these technologies, the choice of substrate materials is crucial. They not only provide support and conductive functions, but also directly affect the working effect and life of the system. Therefore, selecting the appropriate substrate material is crucial for the design and manufacturing of radar and antenna systems.
What is Radar/Antenna substrate?
Radar/antenna substrates are key components used in manufacturing radar systems and antennas. They are not just simple support structures, but also bear multiple functions and responsibilities. In the modern communications and wireless fields, the performance and reliability of radar and antenna systems are critical, and radar/antenna substrates play a vital role in this.
First, the radar/antenna substrate provides the necessary support and mechanical structure to mount and secure the antenna elements and other electronics. These substrates must have sufficient strength and stability to ensure that the antenna system can operate stably in a variety of environmental conditions, whether in mountainous areas at high altitudes or at sea in severe weather.
Secondly, the radar/antenna substrate has good electrical conductivity and can effectively transmit current and signals. Typically, the substrate is plated with copper foil or other conductive layers to provide the electrical ground needed for circuit connections and signal transmission. This conductivity ensures reliable transmission of signals throughout the system, thus safeguarding the performance of radar and antenna systems.
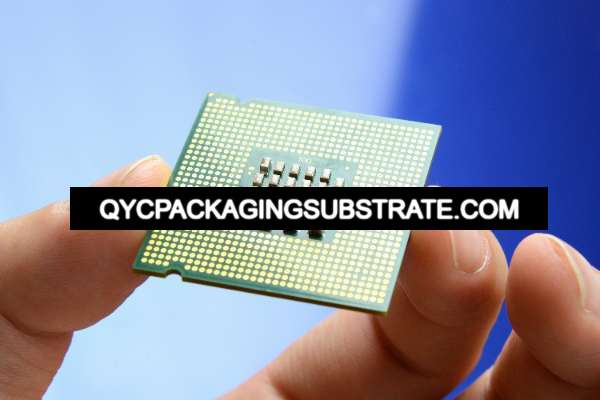
Radar/Antenna Substrate Manufacturer
In addition to support and conductivity, the radar/antenna substrate also performs the important function of isolation. In complex antenna systems, effective isolation is required between different parts to prevent signal interference and mutual interference. The radar/antenna substrate can provide good isolation performance through design and material selection, thereby ensuring stable operation of the system and accurate measurement.
To sum up, the radar/antenna substrate is an indispensable key component in modern radar and antenna systems. Not only do they provide support and mechanical structure, they also ensure system performance and reliability through good electrical conductivity and isolation. In the increasingly developing communication technology and wireless applications, the importance of radar/antenna substrates will continue to be highlighted, providing key support and guarantee for various application fields.
Radar/Antenna substrate design Reference Guide.
The design of radar and antenna substrates is a complex and critical process, which directly affects the performance and reliability of the entire radar system or antenna. When designing, multiple factors need to be considered to ensure that the final product meets the expected requirements and performs well. The following are key factors to consider when designing radar and antenna substrates, along with related best practices and guidelines:
Frequency Range
When designing radar and antenna substrates, you first need to clearly define the required operating frequency range. Different frequency ranges require different design parameters and material selections. For example, high frequency ranges may require special high-frequency materials to ensure good signal transmission and low losses.
Signal loss
Signal loss is one of the important factors to consider in design. During the design process, it is necessary to minimize the loss during signal transmission to maintain signal clarity and accuracy. Using low-loss materials and optimizing layout are effective ways to reduce signal loss.
Thermal management
Because radar systems and antennas can generate large amounts of heat during operation, thermal management is one of the issues that requires special attention during the design process. Effective thermal management measures can ensure that the system maintains a stable temperature during long-term operation, thereby improving system reliability and lifespan.
Manufacturing feasibility
When designing radar and antenna substrates, the feasibility and cost-effectiveness of the manufacturing process need to be taken into consideration. Selecting materials and processes suitable for mass production, and optimizing designs to reduce complexity and cost in the manufacturing process, are one of the key factors in ensuring that the final product can compete in the market.
Best practices and guidelines
Design Reference Guides provide best practices and guidelines to help engineers make informed decisions during the design process. These guidelines include recommendations for proper layout design, optimization of signal transmission paths, ground plane design, impedance matching and electromagnetic compatibility.
In summary, designing radar and antenna substrates requires considering multiple factors and following a set of best practices and guidelines to ensure excellent performance and reliability of the final product. By understanding and effectively applying these principles, engineers can design high-quality radar systems and antennas that meet the requirements.
What material is used in Radar/Antenna substrate?
Material selection for radar and antenna substrates is critical to performance and reliability. Common radar/antenna substrate materials include:
PTFE (polytetrafluoroethylene)
PTFE is a high-performance engineering plastic with excellent high temperature resistance, chemical corrosion resistance and electrical insulation properties. In radar and antenna applications, PTFE is often used as a substrate material because of its low dielectric loss and stable dielectric constant, making it suitable for high-frequency signal transmission.
FR-4 (fiberglass reinforced epoxy resin)
FR-4 is a common glass fiber reinforced epoxy resin with good mechanical strength and heat resistance. It is widely used in radar and antenna substrates because of its moderate cost, good processability, and relatively stable performance.
PTFE fiberglass
PTFE glass fiber is a composite material of PTFE and glass fiber, which combines the excellent properties of PTFE with the mechanical strength of glass fiber. This material is commonly used in radar and antenna applications where higher performance and durability are required.
Selecting the appropriate radar/antenna substrate material requires consideration of many factors, including frequency range, signal loss, thermal management, and manufacturing feasibility. The characteristics and performance of different materials will directly affect the quality and performance of the final product. Therefore, for a specific application, the most suitable substrate material must be carefully evaluated and selected to ensure that the required performance specifications and reliability requirements are achieved.
What size are Radar/Antenna substrate?
The size of the radar and antenna substrate is a critical consideration during the design and manufacturing process. The dimensions of these substrates often vary based on the needs of the specific application. From tiny antennas to large radar systems, substrates of all sizes play key roles in different applications.
For micro-antennas and small radar systems, the size of the substrate is usually smaller. This small size facilitates integration into compact devices such as smartphones, automotive radars, and wearables. In these applications, the substrate needs to be flexible and compact enough to fit within the device’s space constraints and provide stable signal transmission and performance.
For large radar systems, the size of the substrate may be larger. These systems are often used in military, aerospace, meteorological and other fields and need to handle larger amounts of data and longer-distance signal transmission. Large substrates accommodate more circuit components and connectors and provide more space to optimize signal transmission and thermal management.
In addition to differences in size, the shape of the radar and antenna substrates also varies depending on the specific application. Some applications may require long or shaped substrates to accommodate specific installation environments or signal coverage requirements. Other applications may focus more on the compactness and regular shape of the substrate to facilitate manufacturing and integration.
In short, the size of the radar and antenna substrate is the result of a comprehensive consideration, which needs to balance factors such as the space constraints of the device, signal transmission requirements, thermal management requirements, and manufacturing costs. Careful design and selection of appropriate materials ensure optimal performance and reliability of the substrate in a variety of applications.
The Manufacturer Process of Radar/Antenna substrate.
The manufacturing process of radar and antenna substrates is a complex and precise process involving multiple critical steps, each of which has a significant impact on the performance and reliability of the final product.
The first is the design stage, where designers use professional design software to lay out and wire circuits based on the requirements and specifications of the radar or antenna system. The accuracy of the design is directly related to the success of the subsequent manufacturing stages.
Next comes prototyping. At this stage, the designed circuit diagram is used to create samples. Prototyping requires high-precision equipment and technology to ensure the accuracy and reliability of the circuit.
Then comes chemical etching. This is one of the key steps in transferring the circuit diagram to the substrate. By covering the substrate with a special photosensitive material, then projecting the circuit diagram onto it, and finally chemically treating it to remove the unwanted parts, leaving the desired circuit shape.
Next comes drilling. In this step, holes for connecting circuits on different layers are drilled. This requires high-precision drilling equipment to ensure that the location and size of the holes meet the design requirements.
This is followed by metallization. This step is to make the circuit form a conductive path. By depositing a metal film on the circuit surface, wires and connection points are formed to ensure the conductivity and stability of the circuit.
Finally comes the assembly stage. At this stage, various components such as capacitors, resistors, and integrated circuits are mounted on the substrate and connected to the circuit through soldering, etc. This requires precision manual operations and high-temperature welding equipment.
Throughout the manufacturing process, each step requires strict control and monitoring to ensure that the quality and performance of the final product meet the design requirements. Deviations in any link may lead to failure of the entire product. Therefore, the precision and professionalism of the manufacturing process is crucial to ensure the stability and reliability of the radar and antenna substrates.
The Application area of Radar/Antenna substrate.
Radar and antenna substrates are indispensable components in modern technology and they play a key role in various industries. The following are their applications in military, aerospace, communications, automotive and consumer electronics fields:
Military applications
In the military field, radar and antenna substrates are widely used in various reconnaissance, surveillance and navigation systems. Whether it is land, sea or air combat, radar technology is an important part of ensuring combat effectiveness. The reliability and high performance of radar/antenna substrates are critical in military equipment because they need to operate for long periods of time in extreme environments and transmit signals quickly and accurately.
Aerospace field
In the aerospace industry, radar and antenna substrates are used in aircraft communications, navigation and telemetry systems. Drones, satellites and spacecraft all rely on advanced radar and antenna technology for precise navigation and communications, as well as monitoring of ground and air targets.
Communications industry
In the field of communications, radar and antenna substrates are used in wireless communications base stations, satellite communications and mobile communications equipment. They carry the task of transmitting and receiving information, ensuring stable transmission and efficient communication of data between different devices.
Auto industry
In the automotive industry, radar and antenna substrates are widely used in automotive radar systems, in-vehicle communications and navigation equipment. The development of smart driving, in-vehicle entertainment and Internet of Vehicles technologies has driven increased demand for radar and antenna substrates to achieve efficient communication and data exchange between vehicles and between vehicles and infrastructure.
Consumer Electronics
In the field of consumer electronics, radar and antenna substrates are used in a variety of smartphones, tablets, smart home devices and wireless network equipment. They help devices achieve wireless connections and support functions such as WiFi, Bluetooth, and GPS, providing users with convenience and connectivity.
In short, radar and antenna substrates have a wide range of applications, and they provide critical support and foundation for technological development and innovation in various industries. As technology continues to advance and demand continues to grow, the importance of radar and antenna substrates will be further highlighted.
What are the advantages of Radar/Antenna substrate?
Radar and antenna substrates offer many significant advantages over other circuit connection methods, making them an integral part of modern communications and wireless technologies. Here are a few outstanding advantages of radar/antenna substrates:
High frequency performance
Radar and antenna systems often need to process high-frequency signals, and the design and material selection of the radar/antenna substrate can provide excellent high-frequency performance. This means they can effectively transmit and process high-frequency signals, ensuring system stability and reliability.
Low signal loss
In radar and antenna applications, signal loss is a key consideration. The radar/antenna substrate is made of high-quality materials, combined with precise design and manufacturing processes, which can reduce signal loss during transmission, thereby improving system performance and efficiency.
Good thermal stability
In high-power radar and antenna systems, thermal management is critical. The material of the radar/antenna substrate has good thermal conductivity and stability, which can effectively disperse and remove heat, prevent the system from overheating and maintain a stable operating temperature, thus extending the service life of the equipment and improving performance.
Design flexibility
The design flexibility of radar/antenna substrates allows engineers to customize designs based on the needs of specific applications. Whether in size, shape, hierarchy or material selection, it can be flexibly adjusted to meet specific design requirements. This design flexibility provides customized solutions for a variety of different types of radar and antenna systems.
To sum up, radar/antenna substrates play an important role in the fields of modern communications and wireless technologies due to their excellent high-frequency performance, low signal loss, good thermal stability, and design flexibility. They provide reliable circuit support and signal transmission functions for various applications, and promote the continuous development and innovation of wireless communications and radar technology.
FAQ
What is the cost of the radar/antenna substrate?
The cost of radar/antenna substrates varies based on a variety of factors, including the materials used, the complexity of the manufacturing process, and size. Generally speaking, high-performance materials and complex manufacturing processes increase costs, while mass production may reduce costs.
What impact do radar/antenna substrates have on the environment?
The materials used in most radar/antenna substrates are environmentally friendly, but some waste and contamination may be generated during manufacturing and processing. Therefore, manufacturers typically take steps to minimize their impact on the environment and ensure compliance with relevant environmental regulations.
Can radar/antenna substrates be recycled?
Yes, many materials in the radar/antenna substrate, such as fiberglass and metal, can be recycled. However, it should be noted that the substrate may contain some toxic substances, such as lead or cadmium, which need to be processed and removed during the recycling process to ensure safety.
How to troubleshoot radar/antenna substrate failures?
When troubleshooting the radar/antenna substrate, you first need to check whether the circuit connections are normal and make sure there are no open circuits or short circuits. Second, you can locate the problem by measuring the signal strength and frequency in the circuit. When diagnosing faults, the help of professional testing instruments and technicians is often essential.
What is the lifespan of a radar/antenna substrate?
The life of the radar/antenna substrate depends on a variety of factors, including material quality, manufacturing processes, environmental conditions, and usage patterns. Generally, good quality substrates can last for many years or even longer with proper use and maintenance.