Radar HF substrate Manufacturer, High-frequency communication PCBs, or High-frequency antenna PCBs, RF BGA substrate production, we mainly produce ultra-small bump pitch BGA substrate, ultra-small trace and spacing packaging substrate.
In modern electronic equipment, PCB is a vital component. It carries various electronic components and provides connections so that the electronic equipment can work properly. As a Radar HF substrate Manufacturer, you understand the importance of PCBs in electronic systems. In this article, we will take an in-depth look at PCB definition, design, manufacturing process, and aspects related to PCB costs, materials, and manufacturers. With the development of technology and the continuous expansion of application fields, the demand for PCB is also growing day by day. Therefore, understanding the basic knowledge and manufacturing process of PCB is crucial for practitioners in all walks of life.
What is Radar HF substrate?
Radar HF substrate is a printed circuit board (PCB) specifically designed for use in radar high frequency (HF) applications. In radar systems, the HF band usually refers to the frequency range above 30MHz, and the radar HF substrate is designed for the special requirements of this frequency band. As a Radar HF substrate Manufacturer, you understand the stringent PCB requirements of HF radar systems and provide customized substrate solutions to meet the needs of high-performance radar systems.
In radar systems, the HF radar substrate carries various radio frequency (RF) components and antennas and is responsible for transmitting signals to other components of the system. These substrates not only need to provide stable electrical performance, but also need to have excellent high-frequency transmission capabilities to ensure accurate transmission and reception of signals. As a Radar HF substrate Manufacturer, your products provide critical basic support for the HF radar system, ensuring the performance and reliability of the radar system.
HF radar substrates need to have stable electrical properties to ensure the stability and reliability of signal transmission. This includes features such as good impedance control, low loss and low noise. At the same time, the substrate also needs to have excellent high-frequency transmission capabilities to ensure accurate transmission and reception of signals in high-frequency environments. As a Radar HF substrate Manufacturer, your products use high-quality materials and advanced manufacturing processes to provide stable electrical performance and high-frequency transmission capabilities for radar systems.
Different types and specifications of radar systems require customized substrate solutions to meet their specific needs and performance requirements. As a Radar HF substrate Manufacturer, you provide various types and specifications of HF radar substrates to meet the needs of different customers. Your products not only have excellent performance and reliability, but can also be customized to design and produce according to customers’ specific requirements, providing customers with customized substrate solutions.
As a manufacturer of radar HF substrates, your products play a vital role in radar systems. By providing stable electrical performance and excellent high-frequency transmission capabilities, you provide reliable basic support for your customers’ radar systems, ensuring optimal performance and reliability.
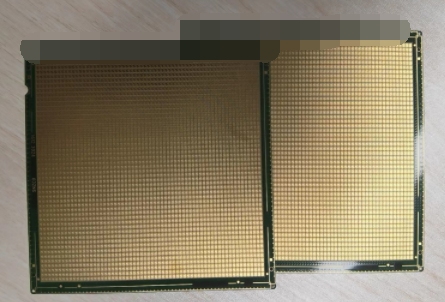
Radar HF substrate
How to Design a Radar HF substrate?
In radar systems, the HF radar substrate carries various radio frequency (RF) components and antennas and is responsible for transmitting signals to other components of the system. These substrates not only need to provide stable electrical performance, but also need to have excellent high-frequency transmission capabilities to ensure accurate transmission and reception of signals. As a Radar HF substrate Manufacturer, your products provide critical basic support for the HF radar system, ensuring the performance and reliability of the radar system.
Before designing a radar HF substrate, you first need to fully understand the technical specifications and performance requirements of the radar system. Including parameters such as operating frequency range, signal bandwidth, output power, etc., these parameters will directly affect the design and material selection of the substrate.
For the design of HF radar substrates, choosing the appropriate substrate material is crucial. Common high-frequency substrate materials include PTFE (polytetrafluoroethylene), RO4003C, etc. They have low loss, stable dielectric constant and excellent high-frequency characteristics, and are suitable for the application of HF radar systems.
During the design process, electromagnetic simulation software is used to simulate and analyze the substrate to evaluate its electromagnetic performance in a high-frequency environment. This includes analysis of signal integrity, impedance matching, coupling effects, etc. to ensure the stability and reliability of the substrate in the HF radar system.
Reasonable layout and wiring are crucial to the design of HF radar substrate. Through carefully designed layout and wiring, signal path length and transmission loss can be minimized, and signal transmission efficiency and accuracy can be improved.
Thermal management and mechanical structural aspects also need to be considered during the design process. HF radar systems usually work in high-power and high-temperature environments, so it is necessary to design appropriate heat dissipation structures and mechanical supports to ensure the stable operation of the substrate in harsh environments.
After the design is completed, experimental verification and debugging are required to evaluate the performance and stability of the substrate in actual applications. Through feedback from experimental data, the design plan can be adjusted and optimized in a timely manner to ensure that the substrate meets the expected performance requirements.
Designing radar HF substrate is a complex and important task, which is directly related to the performance and reliability of the radar system. As a Radar HF substrate Manufacturer, your products provide reliable basic support for HF radar systems and provide important guarantees for the development and application of radar technology. Through reasonable design and high-quality products, we are jointly committed to promoting the advancement of radar technology and providing more reliable and efficient solutions for applications in various industries.
What is the Radar HF substrate Fabrication Process?
The manufacturing process of radar HF substrate is a precise and complex process, designed to ensure that the substrate has stable high-frequency performance and excellent signal transmission capabilities. Here are the basic manufacturing steps:
Substrate material preparation: Radar HF substrate usually uses special high-frequency materials, such as PTFE (polytetrafluoroethylene), RO4003C, etc. Before the manufacturing process can begin, it is necessary to ensure that the substrate material meets specifications and carry out necessary inspections and tests.
Graphic Design and Chemical Processing: The manufacturing process begins with the design phase, which includes converting the circuit diagram into a PCB graphic design. Subsequently, the surface of the substrate needs to undergo chemical treatment, such as cleaning, removing oxides, etc., to ensure that the subsequent pattern copper coating and etching processes proceed smoothly.
Pattern copper pouring and etching: Next is the process of transferring the PCB pattern to the substrate surface. Through chemical etching technology, unnecessary copper material is removed from the substrate surface, leaving the required conductive pattern. This step requires highly precise control to ensure the precision and accuracy of the graphics.
Multi-layer stacking and lamination: For complex radar HF substrates, a multi-layer stacking design may be required. In this step, single-layer PCBs are stacked together and bonded firmly using lamination technology to form a multi-layer structure. This helps improve the substrate’s signal integrity and impedance control capabilities.
Drilling and Plating: After laminating the substrate, holes need to be drilled in order to connect the wires between the different layers. Subsequently, a layer of conductive material is plated on the hole wall through electroplating technology to ensure the connectivity and stability of the circuit.
Pad coating and final shaping: Coating pads on the PCB surface to provide support for the soldering of electronic components. Finally, the PCB is shaped and trimmed to ensure it meets the design requirements and has good appearance and dimensional accuracy.
Final Testing and Quality Control: The final stage of the manufacturing process is complete testing and quality control of the PCB. By using high-precision testing equipment and technology, we ensure that the performance and reliability of PCBs meet specification requirements, thereby ensuring the quality and stability of the final product.
The manufacturing process of radar HF substrates requires highly specialized equipment and technology to meet the strict requirements for high-frequency performance and signal transmission. As a manufacturer of radar HF substrates, we are committed to continuously improving our manufacturing processes and quality control levels to provide customers with high-performance and reliable product solutions.
How to Manufacturer a Radar HF substrate?
When manufacturing radar HF substrates, the key is to ensure they have excellent high-frequency performance and stable electrical characteristics. The following are the basic steps and key considerations for manufacturing radar HF substrates:
Choosing the right substrate material is critical. For radar HF applications, commonly used materials include PTFE (polytetrafluoroethylene) substrates, such as PTFE fiberglass composites. PTFE material has low dielectric loss and excellent high-frequency characteristics, and is suitable for the manufacture of high-frequency transmission lines.
The design of radar HF substrate needs to take into account the special requirements for high-frequency signal transmission. During the design process, layout and wiring need to be optimized to reduce signal path length and impedance mismatch to reduce transmission loss and signal distortion.
The printed circuit board manufacturing process includes steps such as substrate pretreatment, printing, plating, etching and final processing. When manufacturing radar HF substrates, it is necessary to strictly control the process parameters of each step to ensure that the substrate surface is smooth and flat, the metal layer thickness is uniform, and good dielectric properties are maintained.
After manufacturing is completed, high-frequency testing of the radar HF substrate is required to verify its performance and reliability. Commonly used test methods include S-parameter testing and eye diagram analysis, which are used to evaluate signal transmission characteristics, impedance matching, signal integrity and other indicators.
Quality control is a crucial part of the manufacturing process of radar HF substrates. Through strict quality control measures, including raw material inspection, production process monitoring and finished product inspection, we ensure that each substrate meets the design requirements and customer needs.
For different radar HF application requirements, manufacturers need to provide customized solutions. According to the customer’s requirements, the substrate material, number of layers, size, process parameters, etc. are adjusted to meet their specific design and performance requirements.
In the process of manufacturing radar HF substrates, manufacturers need to fully understand the working principles and performance requirements of the radar system, work closely with customers, and provide high-performance, high-quality substrate products to provide reliable guarantee for the stable operation of the radar system.
How Much Does a Radar HF substrate Cost?
As a Radar HF substrate Manufacturer, understanding the cost of radar high frequency (HF) substrates is crucial to customers’ purchasing decisions. The cost of radar HF substrates depends on multiple factors, including material type, process complexity, size and quantity, etc. The following are several key factors that affect the cost of radar HF substrate:
First of all, material type is one of the important factors that determine the cost of radar HF substrate. Common radar HF substrate materials include PTFE (polytetrafluoroethylene), RO4003C, etc. These high-performance materials have excellent high-frequency characteristics, but are correspondingly more expensive.
Secondly, process complexity will also affect the cost of radar HF substrate. For complex designs and demanding processes, more production steps and precision processing equipment are required, thus increasing production costs.
In addition, the size and quantity of radar HF substrates will also affect its cost. Generally speaking, large-sized substrates and low-volume production will increase production costs, while small-sized substrates and high-volume production are relatively cheaper.
Overall, the cost of the radar HF substrate is customized based on the customer’s specific needs and requirements. As Radar HF substrate Manufacturer, we can provide customized solutions according to customer needs and optimize the production process to control costs to meet customer budgets and requirements.
What materials are Radar HF substrate made of?
As Radar HF substrate Manufacturer, we know that the material selection of radar high frequency (HF) substrate is crucial to product performance. HF radar systems require excellent high-frequency transmission characteristics, stable signal integrity, and good electrical performance, so the selection of substrate materials is crucial.
In HF radar systems, commonly used substrate materials include polytetrafluoroethylene (PTFE), epoxy resin (FR-4), polyimide (PI), etc. Among them, polytetrafluoroethylene (PTFE) is an excellent high-frequency dielectric material. It has the advantages of low dielectric loss, stable dielectric constant and low temperature coefficient of dielectric constant. It is suitable for high-frequency detection in HF radar systems. Transmission and signal integrity requirements. PTFE material can provide stable dielectric properties and exhibit low signal attenuation and transmission loss in the HF band, thus ensuring the performance stability and reliability of the radar system.
In addition, epoxy resin (FR-4), as a common substrate material, is also widely used in HF radar systems. FR-4 substrate has good mechanical strength and heat resistance and is suitable for complex PCB design and manufacturing. Although the dielectric properties of FR-4 materials are not as good as PTFE, they still show good performance in some low- and medium-frequency applications.
In addition, high-performance engineering plastic materials such as polyimide (PI) are also used in the substrate manufacturing of HF radar systems. PI materials have excellent high-temperature stability, mechanical strength and chemical stability, and are suitable for high-temperature environments and complex circuit designs.
In summary, selecting a suitable substrate material is crucial to the performance and stability of the HF radar system. As a Radar HF substrate Manufacturer, we are committed to providing customers with high-quality substrate materials and customized solutions based on their specific needs to meet their requirements and expectations for HF radar system performance.
Who manufactures Radar HF substrate?
As a professional Radar HF substrate Manufacturer, we not only provide high-quality PCB products, but also are committed to producing high-quality radar high-frequency substrates. In radar systems, the performance of HF substrate directly affects the stability and performance of the system. Therefore, it is crucial to choose a reliable HF substrate supplier.
Our company is proud to announce that as a manufacturer of radar HF substrates, we not only have advanced production equipment and technical teams, but more importantly, our pursuit of product quality and customer service has never stopped. Here are some of the key advantages of our company as a manufacturer of radar HF substrates:
We have advanced production equipment and process technology to meet the high requirements of different radar systems for HF substrates. We use advanced material selection and production processes to ensure that our products have excellent electrical performance and stability.
During the production process, we strictly implement quality control procedures in accordance with international standards to ensure that each HF substrate meets customer requirements and specifications. From the procurement of raw materials to every aspect of production and manufacturing, we conduct strict inspection and testing to ensure product quality stability.
We can provide customized HF substrate solutions according to customer needs, including different sizes, number of layers, materials and process requirements, etc. Our technical team will work closely with customers to provide them with professional technical support and customized solutions to meet their specific application needs.
We focus on customer experience and are committed to providing customers with timely delivery services. We have efficient production capacity and supply chain management system, which can ensure that orders are delivered on time and meet customers’ production plans and needs.
As a technology-driven enterprise, we continue to carry out technological innovation and product improvement to meet changing market needs. We pay close attention to industry development trends and customer feedback, constantly optimize product performance and service quality, and provide customers with better products and services.
In short, as a manufacturer of radar HF substrates, we will always adhere to the principle of “quality first, customer first”, provide customers with high-quality products and services, and develop together with customers for a win-win future.
What are 5 qualities of a good customer service?
As a Radar HF substrate Manufacturer, providing excellent customer service is an important task for us. Here are five key features that help us ensure customer satisfaction and build long-term relationships:
Timely response: We value every need and problem of our customers and promise to respond in the shortest possible time. Whether it is technical consultation, quotation or after-sales service, we always keep communication open to ensure that customers can get the support and help they need in a timely manner.
Professional technical support: We have an experienced team of engineers who can provide customers with professional technical support and solutions. Whether it is PCB design optimization, material selection or manufacturing process optimization, we are able to provide our customers with the best advice and support to meet their specific needs and requirements.
Quality Assurance: We strictly follow international standards and quality management systems to ensure stable and reliable product quality. From raw material procurement to production and manufacturing to final delivery, we conduct strict quality control on every link to ensure that the products meet customer requirements and expectations.
Customized Solutions: We understand that each customer’s needs are unique, so we provide customized solutions to meet our customers’ specific needs and requirements. Whether it is PCB design, material selection or manufacturing process, we are able to provide customized solutions according to customer needs to ensure the best performance and quality of the product.
Integrity cooperation: We adhere to the principle of integrity and establish long-term and stable cooperative relationships with customers. We always adhere to the principles of honesty, trustworthiness and commitment, maintain good communication and cooperation with customers, and jointly achieve a win-win situation.
Through the above five characteristics, we are committed to providing customers with high-quality products and services, meeting their needs and expectations, and achieving the goal of win-win cooperation.
FAQS
What are the key points in the manufacturing process of Radar HF substrate?
The manufacturing process of Radar HF substrate includes material selection, lamination process, surface treatment and other aspects. Key points include ensuring the quality and stability of the substrate material, controlling parameters such as temperature and pressure during lamination, and precise surface treatment to ensure signal integrity and stable performance of the substrate.
What is the cost of Radar HF substrate?
The cost of Radar HF substrate depends on multiple factors, including material type, size, thickness, number of layers, etc. Generally speaking, compared with traditional PCB, the cost of Radar HF substrate will be slightly higher, but the corresponding performance and stability are also better.
How to evaluate the quality of Radar HF substrate?
Multiple indicators need to be considered to evaluate the quality of Radar HF substrate, including interlayer impedance control, surface flatness, in-hole connection quality, etc. In addition, performance and stability can be evaluated through high-frequency testing and reliability verification of samples.
What special requirements does the HF radar system have for PCB?
HF radar systems have relatively strict requirements for PCBs because of their high operating frequency, generally between 3 and 30 GHz. This means that PCB needs to have excellent high-frequency transmission characteristics and signal integrity to ensure stability and reliability in high-frequency environments. In addition, HF radar systems usually have high requirements for PCB impedance control and need to ensure signal matching and consistency during transmission.
How to choose the right PCB manufacturer?
Choosing the right PCB manufacturer is key to ensuring the performance and stability of your HF radar system. First of all, the manufacturer’s production capacity and equipment level should be inspected to ensure that it can meet the production needs of high-quality PCBs. Secondly, attention should be paid to the manufacturer’s quality control system to ensure that products comply with international standards and customer requirements. Finally, choose a manufacturer with rich experience and good reputation to ensure product quality and on-time delivery.