RF/microwave PCB Manufacturer.High speed and high frequency material packaging substrate Manufacturer. Advanced packaging substrate production.
With the rapid development of wireless communication technology, RF (radio frequency) and microwave circuit boards (PCB) have become indispensable key components in modern electronic equipment. This article will delve into the importance of RF/microwave PCBs in today’s electronics field and the key role they play in supporting key applications such as wireless communications, radar, and satellite communications.
What is RF/microwave PCB?
RF/microwave PCB is a printed circuit board designed for high-frequency signal transmission. They are carefully designed to meet the requirements of radio frequency (RF) and microwave bands for reliable signal transmission in a variety of wireless communications and radar systems. These circuit boards are not just components of traditional electronic equipment, but are at the heart of modern high-performance communications systems.
The design and manufacturing process of RF/microwave PCBs requires a high degree of technology and expertise to ensure they have excellent high-frequency characteristics. Compared with traditional printed circuit boards, RF/microwave PCB uses special materials and processes to achieve lower signal loss, higher operating frequency and better electromagnetic compatibility.
In RF/microwave PCB, signal transmission is usually achieved through microstrip lines, coaxial lines or waveguides. The design and layout of these transmission lines are critical to circuit performance because they directly affect signal transmission speed, attenuation, and immunity to interference.
Material selection for RF/microwave PCB is also crucial. Common materials include PTFE (polytetrafluoroethylene), FR-4 (fiberglass reinforced epoxy resin) and RO4003C, etc. These materials have low losses, high thermal stability and excellent dielectric properties, making them suitable for high frequency applications.
Overall, RF/microwave PCB plays a key role in modern communication systems. They can not only achieve high-performance data transmission in fields such as wireless communications, radar, satellite communications, and aerospace, but also promote the progress and innovation of wireless technology. As communications technology continues to evolve, RF/microwave PCBs will continue to play an important role and evolve to meet future needs and challenges.
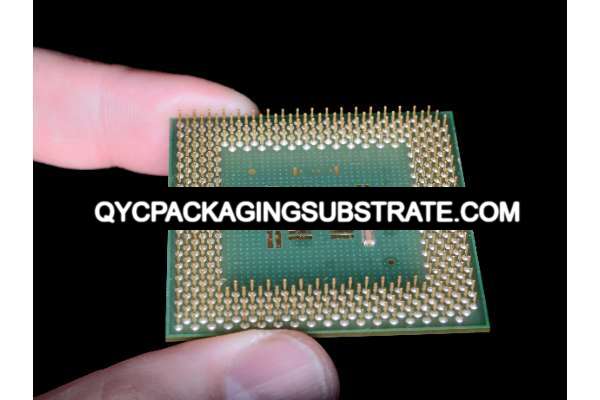
RF/microwave PCB Manufacturer
RF/microwave PCB design Reference Guide.
The design of RF/microwave PCB is a complex and critical task that requires the designer to consider several key factors to ensure the performance and reliability of the board. Here are a few important factors to note when designing RF/microwave PCBs:
Signal integrity
In high-frequency circuit design, signal integrity is critical. Designers must ensure that signals are not lost or distorted during transmission. In order to achieve good signal integrity, it is necessary to pay attention to factors such as the layout of signal lines, distance between layers, and gaps between signal and ground lines.
Transmission line characteristics
The characteristics of the transmission line directly affect the signal transmission quality on the circuit board. In RF/microwave PCB design, commonly used transmission line types include microstrip lines, coaxial lines, and waveguides. Designers need to select the appropriate transmission line type and properly match and adjust it to meet specific frequency and performance requirements.
Impedance matching
In high-frequency circuits, impedance matching is the key to ensuring signal transmission. Designers must ensure that the impedances of various parts of the circuit are well matched to avoid signal reflections and losses. Common impedance matching technologies include microstrip line width adjustment, impedance transformers and matching networks.
Coupling
Coupling refers to the transfer of energy and influence between different parts of a circuit. In RF/microwave PCB design, attention needs to be paid to reducing the coupling effect between different signal lines to reduce interference and signal distortion. Commonly used coupling suppression techniques include increasing separation distance, ground plane design optimization and wiring planning.
Electromagnetic compatibility
In high-frequency circuit design, electromagnetic compatibility is an important consideration. Designers must ensure that the circuit board has good immunity to external electromagnetic interference and will not cause interference to surrounding equipment. In order to achieve good electromagnetic compatibility, technical means such as shielding measures, ground wire design, and filter addition are required.
To sum up, designing RF/microwave PCB requires comprehensive consideration of multiple key factors such as signal integrity, transmission line characteristics, impedance matching, coupling and electromagnetic compatibility. Designers should follow strict specifications and best practices to ensure the board has excellent performance and reliability through proper layout and optimized design to meet specific application needs.
What material is used in RF/microwave PCB?
The material selection of RF/microwave PCB is crucial because it directly affects the performance and reliability of the circuit board. Typically, RF/microwave PCB uses a series of high-performance materials to meet the special needs for high-frequency signal transmission.
First, a common material is PTFE (polytetrafluoroethylene), which is known for its excellent dielectric properties. PTFE has extremely low loss factor and high thermal stability, and can maintain stable signal transmission at high frequencies. Due to its excellent properties, PTFE is often used to manufacture high-frequency radio frequency circuit boards.
Another commonly used material is FR-4 (fiberglass reinforced epoxy), which is a common general-purpose circuit board substrate. FR-4 has good mechanical properties and heat resistance, making it suitable for a wide range of applications. However, for high-frequency applications, the dielectric properties of FR-4 may not be ideal, so in some RF/microwave PCBs, FR-4 may be used in combination with other materials to improve performance.
In addition, another common high-performance material is RO4003C. RO4003C is a ceramic-reinforced PTFE composite material with low loss and high thermal stability similar to PTFE, as well as high mechanical strength and dimensional stability. This makes RO4003C one of the materials of choice in many RF/microwave PCB designs.
To sum up, RF/microwave PCB usually uses high-performance materials such as PTFE, FR-4 and RO4003C. These materials have low losses, high thermal stability and excellent dielectric properties to meet the requirements of high frequency applications. When selecting materials, designers need to make appropriate choices based on specific application needs and performance requirements to ensure circuit board performance and reliability.
What size are RF/microwave PCB?
RF/microwave PCBs vary in size and shape for their specific applications. In wireless communication systems, RF/microwave PCBs can come in many different sizes and shapes to meet various needs and design requirements. They range from small microstrip antennas to large RF front-end modules, which we discuss in detail below.
For small microstrip antennas and antenna arrays, RF/microwave PCBs usually have smaller sizes and simple shapes. Microstrip antennas are often integrated into a device’s housing or circuit board to achieve a compact design and efficient signal transmission. Their shape may be rectangular, circular, or other geometric shapes, depending on the desired radiation characteristics and spatial constraints.
In applications requiring higher performance and complex functionality, RF/microwave PCBs may be larger and more complex. For example, RF front-end modules usually contain multiple RF functional modules, such as amplifiers, filters, mixers, etc., which need to be integrated and laid out on the same circuit board. This type of RF/microwave PCB may have larger dimensions and a more complex layout to accommodate multiple components and ensure good connections and signal transmission between them.
In addition, for large-scale applications such as microwave communication systems, RF/microwave PCBs may require larger sizes and more complex structures. These systems often contain multiple RF links, antenna systems, power amplifiers, etc., requiring the design of highly integrated circuit boards to support complex communication functions and high-speed data transmission. Therefore, RF/microwave PCBs in these applications may take on various shapes such as rectangular, circular, polygonal, etc., with larger physical dimensions to accommodate multiple functional modules and antennas.
In general, the size and shape of the RF/microwave PCB depends on the requirements of the specific application. Whether it is a small microstrip antenna or a large microwave communication system, RF/microwave PCB plays a key role in providing reliable support and connection for wireless communication.
The Manufacturer Process of RF/microwave PCB.
The manufacturing process of RF/microwave PCB is a delicate and complex process involving multiple key steps. Each step is crucial and directly affects the performance and quality of the circuit board. The following is a detailed introduction to the RF/microwave PCB manufacturing process:
Design and layout
The design of RF/microwave PCB is the basis of the entire manufacturing process. Designers determine board layout, component locations, and signal paths based on specific application needs and performance requirements. They use professional design software to create circuit board schematics and wiring diagrams, and perform necessary simulation and verification to ensure the accuracy and reliability of circuit design.
Material selection
Choosing the right materials is critical to RF/microwave PCB performance. Commonly used materials include PTFE (polytetrafluoroethylene), FR-4 (glass fiber reinforced epoxy resin), RO4003C, etc. Designers select the most appropriate material based on requirements such as frequency, transmission line characteristics, and thermal stability of the circuit board.
Chemical processing
During the manufacturing process, circuit boards go through a series of chemical treatments, including steps such as etching, copper plating and residue removal. Etching is the process of removing unwanted copper foil from the surface of a circuit board, while copper plating is the process of adding extra copper foil over desired areas to create conductive paths.
Molding and printing
Forming is the process of cutting raw circuit board material into the desired size and shape. Printing is the process of transferring a designed circuit pattern to the surface of a circuit board, usually through screen printing or photolithography.
Copper
Copper laying is the process of forming a conductive layer on the surface of a circuit board to connect various components and signal lines in the circuit. Plate a layer of copper foil on the required area through methods such as chemical copper plating or electroplating copper.
Cutting
Once the copper is laid, the board is cut to the required size and shape to meet the specific application needs.
Assemble
Assembly is the installation of various components (such as transistors, capacitors, resistors, etc.) onto a circuit board and connecting them through soldering and other methods. The assembly process requires precise handling and instrumentation to ensure the correct positioning of components and the quality of connections.
Overall, the RF/microwave PCB manufacturing process requires a high degree of expertise and technology, and each step must be strictly controlled to ensure the performance and quality of the circuit board. Only a precise manufacturing process can produce high-quality circuit boards that meet high-frequency requirements.
The Application area of RF/microwave PCB.
RF/microwave PCB is widely used in communications, radar, satellite communications, wireless networks, military and aerospace and other fields. In today’s era of digitization and interconnection, wireless communication systems have become the core of modern life and various industries. As a key component of these systems, RF/microwave PCB plays an irreplaceable role in these fields.
First of all, the communication field is one of the main applications of RF/microwave PCB. From mobile phones to satellite communications, wireless communication systems enable the instant, reliable exchange of information around the world. RF/microwave PCB carries transmitters, receivers and signal processors in various communication equipment, ensuring high-speed transmission and stability of data.
Secondly, radar technology is also one of the important application areas of RF/microwave PCB. Radar systems are widely used in aircraft navigation, weather forecasting, military reconnaissance and other fields. RF/microwave PCB plays a key role in radar systems, supporting high-precision signal processing and target tracking.
Satellite communications is another important area of RF/microwave PCB applications. Satellite communication systems require highly reliable electronic equipment to transmit data between the ground and space. The high frequency characteristics and stability of RF/microwave PCBs make them ideal for satellite communications equipment.
Wireless networks are an indispensable part of daily life, and RF/microwave PCB is one of the key technologies that support the operation of wireless networks. From home Wi-Fi routers to wireless base stations in cities, RF/microwave PCBs play an important role in wireless network equipment, ensuring fast data transmission and stable network coverage.
In addition, the military and aerospace fields are also important application areas for RF/microwave PCB. Military communication systems require a high degree of confidentiality and anti-interference capabilities, while electronic equipment on spacecrafts need to withstand extreme environmental conditions. RF/microwave PCB provides critical support to the military and aerospace fields through its stable performance and reliability.
To sum up, RF/microwave PCB plays an irreplaceable role in the fields of communications, radar, satellite communications, wireless networks, military and aerospace. They support high-performance, high-reliability wireless communication systems and promote the development of modern society and technology.
What are the advantages of RF/microwave PCB?
Compared with traditional circuit boards, RF/microwave PCBs show significant advantages in many aspects, making them ideal for high-frequency applications.
First, RF/microwave PCB has lower signal loss. High-frequency signals will encounter signal attenuation during transmission, and the high-performance materials and precision manufacturing processes used in RF/microwave PCB can reduce signal loss, ensure stable transmission of signals on the circuit board, and improve system performance and reliability.
Secondly, RF/microwave PCB has a higher operating frequency. Due to its special design and material selection, RF/microwave PCB is able to support a higher operating frequency range, from hundreds of MHz to thousands of MHz or even higher frequencies, meeting the needs of various high-frequency applications.
In addition, RF/microwave PCB has better anti-interference ability. In high-frequency environments, circuit boards are susceptible to external interference, affecting system performance and stability. The materials and designs used in RF/microwave PCB can effectively suppress interference signals, improve the anti-interference ability of the system, and ensure the stability of signal transmission.
Finally, RF/microwave PCBs have smaller sizes. Due to the particularity of high-frequency signals, more compact and precise designs are required to implement high-performance circuits. RF/microwave PCB can achieve higher integration and smaller size, suitable for space-constrained applications, while reducing the weight and cost of the system.
In summary, RF/microwave PCB has the advantages of lower signal loss, higher operating frequency, better anti-interference ability and smaller size than traditional circuit boards, making it an ideal choice for many high-frequency applications. First choice. In the fields of wireless communications, radar, satellite communications, wireless networks and other fields, the application of RF/microwave PCB will provide an important guarantee for the performance and reliability of the system and promote the continuous development and application of high-frequency technology.
FAQ
What are the material selection considerations for RF/microwave PCBs?
Material selection is critical to RF/microwave PCB performance. Usually low-loss, high-dielectric-constant materials such as PTFE (polytetrafluoroethylene) are used, as well as metallized glass fiber cloth substrates (such as RO4003C). The material’s dielectric properties, dissipation factor, thermal stability and cost are all factors considered.
What is the manufacturing process of RF/microwave PCB?
The manufacturing process of RF/microwave PCB includes multiple steps such as design, layout, material selection, chemical processing, molding, printing, copper laying, cutting and assembly. Precise manufacturing processes and high-quality materials are key to ensuring circuit performance and reliability.
What are the application areas of RF/microwave PCB?
RF/microwave PCB is widely used in communications, radar, satellite communications, wireless networks, military and aerospace and other fields. They play a key role in high-frequency signal transmission and processing, supporting the performance and functionality of various wireless communication systems.
What are the advantages of RF/microwave PCB?
Compared with traditional circuit boards, RF/microwave PCB has lower signal loss, higher operating frequency, better anti-interference ability and smaller size. These advantages make it the first choice for many high-frequency applications, such as RF front-end modules, microwave communication systems, and antenna arrays.