RF Modules Substrate Manufacturer. High speed and high frequency material BGA packaging substrate Vendor. we offer advanced RF BGA packaging substrate from 2 layer to 22 layers. the best smallest trace and gap are 9um/9um.
In today’s electronic devices, RF modules play an increasingly important role. From smartphones to Internet of Things devices, they all require high-performance radio frequency technology. However, the stability and performance of these modules hide a series of complex design and manufacturing processes. In this process, RF module substrate manufacturers play a key role, and their technology and innovation drive the entire industry forward.
What is RF Modules Substrate?
RF module substrate, referred to as PCB (Printed Circuit Board), is a printed circuit board used for radio frequency (RF) electronic equipment. It carries the components and connections of RF circuits and provides the necessary support structure for wireless communications. In modern wireless communication systems, RF module substrates play a vital role, providing basic support for device performance and reliability.
The design of the RF module substrate needs to take into account the special properties of the radio frequency signal, so it needs to be more precise and cautious during layout and wiring. Radio frequency signals have strict requirements on wiring spacing, wiring paths, grounding and power transmission to ensure signal integrity and stability. In addition, RF module substrates also need to consider issues such as electromagnetic interference (EMI) and electromagnetic compatibility (EMC) to avoid interference and signal distortion.
In the manufacturing process of RF module substrates, material selection is crucial. Common materials include FR-4 (fiberglass), PTFE (polytetrafluoroethylene), Rogers, Arlon, etc. They have different dielectric constants, loss factors, and thermal properties and are suitable for different types of RF applications. Manufacturers usually choose the most suitable materials based on customer needs and application scenarios.
RF module substrates also vary in size and shape, depending on specific application requirements and device design. They can be as small as a few millimeters required for tiny devices, or as large as tens of centimeters required for large base station equipment. The choice of size is often closely related to factors such as performance, power consumption, cost and physical space.
In short, as the core component of radio frequency electronic equipment, the RF module substrate carries the important task of signal transmission and processing. Their design, manufacturing and application directly affect the performance and reliability of wireless communication systems, so precise and professional technical support is required during the engineering design and production processes.
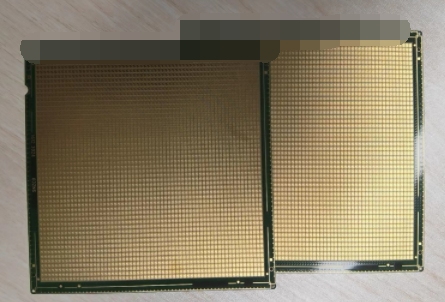
RF Modules Substrate
RF Modules Substrate design Reference Guide.
Designing RF module substrates requires sophisticated technology and expertise because the performance of the RF module is directly affected by the design. In design guidelines, an understanding of RF signals is critical. The characteristics and behavior of RF signals are very different from DC circuits and therefore require special handling and considerations.
First, design guidelines will emphasize layout and routing specifications. A good layout can minimize signal crosstalk and noise and improve system performance and stability. This includes avoiding signal line crossovers, minimizing loop areas, optimizing signal paths, etc. In addition, wiring specifications also involve the design and matching of transmission lines for high-frequency signals.
Secondly, signal integrity is also one of the important contents of the design guide. Signal integrity in RF modules involves the accurate transmission of signals and the ability to maintain signal quality. This includes the control and compensation of signal attenuation, distortion, delay and other factors. Design guides provide advice on selecting appropriate connectors, impedance matching, signal conditioning and filtering.
Finally, the management of EMI (electromagnetic interference)/EMC (electromagnetic compatibility) is also one of the focuses of the design guide. RF modules work in the high-frequency range and are prone to electromagnetic interference, which affects the normal operation of other equipment. Therefore, measures need to be taken to reduce the level of electromagnetic interference. The design guide provides recommendations on ground wire design, shielding, filters, and insulation to ensure system stability and reliability in electromagnetic environments.
In general, designing an RF module substrate is a complex process that requires comprehensive consideration of multiple factors. The design guide provides engineers with valuable guidance and suggestions to help them design RF module substrates with superior performance, stability and reliability to meet the needs of various applications.
What material is used in RF Modules Substrate?
The performance of the RF module substrate is directly affected by the materials used. In the design and manufacture of modern RF electronics, choosing the right materials is critical. Common RF module substrate materials include FR-4, PTFE (polytetrafluoroethylene), Rogers and Arlon, etc. Each material has unique properties and has different suitability for different application scenarios.
FR-4 is one of the most common substrate materials and has good mechanical strength and insulation properties. Its dielectric constant is relatively high, making it suitable for general RF applications such as Wi-Fi routers and Bluetooth devices. However, due to its relatively high loss factor, it may not be ideal for high frequency applications.
PTFE (polytetrafluoroethylene) is a material with low dielectric constant and low loss factor, suitable for the design of high-frequency radio frequency circuits. It has excellent thermal stability and chemical resistance and is often used in high-frequency wireless communication equipment, such as radar systems and microwave communication equipment.
Specialty RF materials such as Rogers and Arlon are developed for high-performance RF circuit design. They feature precise dielectric constant and loss factor control, providing more reliable signal transmission and lower signal loss. These materials are commonly used in RF applications that require extremely high performance, such as satellite communications systems and antenna arrays.
When selecting RF module substrate materials, trade-offs need to be made based on specific application requirements. In addition to considering the dielectric constant and loss factor, factors such as the material’s thermal properties, mechanical strength, cost and processability also need to be considered. By choosing the right materials, you can ensure optimal performance and reliability of the RF module substrate during design and manufacturing.
What size are RF Modules Substrate?
The size of the RF module substrate is an important aspect that requires special attention during the design and manufacturing process. The choice of these dimensions not only affects the performance and functionality of the device, but also directly affects the cost and practicality of the overall product. Therefore, when designing an RF module substrate, various factors must be carefully considered to ensure that the final product meets the expected requirements.
First, the size of the RF module substrate depends on the specific application requirements. For micro devices, such as smart watches, fitness trackers or portable communication devices, very small sizes are often required, perhaps only a few millimeters in size. Such a small size can make the device more lightweight and portable, and help improve the portability and comfort of the device.
On the contrary, for large base station equipment or other industrial applications, the RF module substrate may need to be larger in size, even tens of centimeters or larger. In this case, the increase in size is usually to accommodate more circuit components, provide more powerful signal processing capabilities, or to accommodate specific installation environment and physical space requirements.
In addition to application requirements, size selection will be affected by other factors. For example, performance requirements may have an impact on size, as some specific functionality or performance features may require more space to implement. Power consumption is another important consideration, as larger size may mean more power supplies and thermal design are needed to meet the device’s power consumption needs. Additionally, cost is an important consideration, as generally larger substrate sizes may result in increased material and manufacturing costs.
Physical space constraints must also be considered when sizing the RF module substrate. This includes the device’s case size, interface locations, thermal requirements, and other mechanical constraints. Therefore, designers must ensure that the size of the substrate matches the overall design and structure of the device for smooth installation and integration while meeting performance requirements.
To sum up, the size selection of RF module substrate is a complex process that requires comprehensive consideration of multiple factors. Only with a full understanding of application needs, performance requirements, cost constraints and physical space limitations can designers make appropriate sizing choices that ensure the performance and practicality of the final product.
The Manufacturer Process of RF Modules Substrate.
The manufacturing process of RF module substrate is a highly complex and precise process, which requires various professional technologies and strict quality control to ensure the performance and reliability of the final product. The following are the detailed steps of the RF module substrate manufacturing process:
The first step in the manufacturing process is to verify the PCB design. This includes verification of placement and routing with software simulation tools to ensure design specifications and performance requirements are met. During this phase, prototyping and testing may occur to verify the correctness of the design.
Once the design verification is completed, the raw materials required to manufacture the RF module substrate need to be procured. These raw materials include substrate materials, copper foil, chemicals, and other necessary materials and consumables. Excellent quality raw materials are critical to the performance of the final product.
During the printing stage, the designed circuit diagram is transferred to the substrate. This is usually achieved by printing a circuit pattern on a substrate, using printing technology to cover the surface of the substrate with conductive ink or metallized film to form the desired circuit pattern.
After printing, the substrate needs to be chemically treated to remove unwanted metallization material while retaining the desired circuit pattern. This usually involves chemical processes such as pickling and copper plating to ensure a clear, reliable circuit structure.
Next is the drilling stage, where holes are drilled into the substrate with a CNC drill machine to install components and connect wires. These holes must be accurately positioned and of consistent size to ensure smooth subsequent assembly and connection.
After drilling is completed, the wire holes on the substrate need to be metallized to conduct electricity. This usually involves covering the inside of the holes and the surface of the substrate with a metallized film to create channels for wire connections.
After the metallization is completed, the components can be installed and connected. This involves soldering the electronic components to the substrate and connecting the wires between the individual components. The assembly process requires precise manual operations and highly automated equipment support.
The last critical step is testing the fabricated RF module substrate. This includes functional testing, performance testing, reliability testing, etc. to ensure that the product meets specifications and requirements. Any potential flaws need to be discovered and fixed at this stage.
To sum up, the manufacturing process of RF module substrates involves multiple complex links and strict quality control. Only by strictly implementing standards and processes at every stage can the performance and reliability of the final product be guaranteed to reach the expected level.
The Application area of RF Modules Substrate.
RF module substrates play an important role in various fields, and their wide application not only promotes the development of technology, but also provides key support for innovation in various industries. The following are the specific applications of RF module substrates in communications, medical, military, aerospace, automotive and industrial control fields:
Communication
In the field of communications, RF module substrate is one of the core components of wireless communication systems. They are used in equipment such as base stations, antenna systems, satellite communications, radar and radio frequency identification (RFID). By providing stable signal transmission and highly integrated solutions, RF module substrates enable the rapid development of modern communication technology.
Medical
Medical devices are increasingly demanding high-performance RF technology. RF module substrates play a key role in medical imaging equipment (such as MRI and CT scanners), medical sensors, remote monitoring equipment, etc. They help the medical industry achieve faster and more accurate diagnosis and treatment options.
Military
The demand for RF technology in the military field is very important because communications, radars, drones, navigation systems, etc. all require high-performance radio frequency solutions. RF module substrates play a vital role in the reliability and security of military communication systems, and also support the modernization and intelligence of military equipment.
Aerospace
In the aerospace field, RF module substrates are widely used in flight control systems, communication systems, radar systems, satellite communications and navigation systems, etc. They carry radio frequency circuits in aerospace equipment and ensure the safety and reliability of aerospace missions.
Car
The automotive industry’s demand for wireless communications and intelligent driving technology continues to grow. RF module substrates are used in automobiles for applications such as in-vehicle communication systems, in-vehicle radars, wireless charging systems, Internet of Vehicles, and vehicle diagnostic systems. They provide important support for the intelligence and interconnection of the automotive industry.
Industrial control
In the field of industrial control, RF module substrates are used in industrial automation, sensor networks, remote monitoring systems, etc. They enable intelligent and efficient factory production by providing reliable data transmission and remote control functions.
To sum up, RF module substrates play a key role in communications, medical, military, aerospace, automotive and industrial control fields. Their technological innovation and application promote the development of science and technology and provide a solid foundation for innovation and progress in various fields of society.
What are the advantages of RF Modules Substrate?
The advantages of RF module substrates are key factors in the design and implementation of wireless communication systems. Compared with traditional wiring methods, RF module substrates have obvious advantages in many aspects, making them an indispensable part of modern wireless communication systems.
First, the RF module substrate has a higher level of integration. RF module substrates enable more compact and simplified designs by integrating RF circuitry and other necessary electronic components onto a single PCB. This highly integrated design not only saves space, but also reduces system complexity and improves system reliability.
Secondly, the RF module substrate has better signal integrity. Because RF signals are very sensitive to interference and noise, special attention needs to be paid to signal integrity when designing RF systems. Through carefully designed layout and inter-layer stacking structure, the RF module substrate can effectively manage signal transmission and maintain signal integrity, thereby ensuring system stability and performance.
In addition, the RF module substrate has lower signal loss. Compared with traditional line wiring, the design of RF module substrates usually uses shorter transmission lines and more optimized signal paths, thereby reducing signal loss during transmission. This low signal loss design can improve system efficiency and reduce power consumption, thereby extending the battery life of the device and improving user experience.
Finally, the RF module substrate has a smaller size. With the trend of increasingly miniaturized and lightweight wireless communication equipment, RF module substrates can provide compact design solutions to adapt to various space constraints and application scenarios. Their small size makes them particularly suitable for mobile devices, embedded systems and IoT devices.
To sum up, RF module substrate plays an irreplaceable role in the design and implementation of wireless communication systems due to its high integration, excellent signal integrity, low signal loss and small size. They not only provide a solid foundation for the development of modern wireless communication technology, but also promote innovation and progress in all walks of life.
FAQ
What are the advantages of RF module substrates compared to traditional line wiring?
RF module substrates have multiple advantages over traditional line wiring. First, the RF module substrate can achieve a higher level of integration, integrating multiple RF circuit components into a compact space, reducing the size and weight of the system. Secondly, the layout and wiring of the RF module substrate are carefully designed to provide better signal integrity, reduce signal interference and noise, and improve system stability and performance. In addition, the RF module substrate is made of high-quality materials and has lower signal loss, enabling longer transmission distances and more reliable communication connections. Finally, the production cost of RF module substrates is relatively low and has a shorter manufacturing cycle, which can meet the needs of rapid iteration and customization.
How long is the manufacturing cycle of RF module substrate?
The manufacturing lead time for RF module substrates depends on the specific project and manufacturer. Typically, the manufacturing lead time ranges from days to weeks from design confirmation to final delivery. Projects of lower complexity may have a shorter manufacturing cycle, while projects of higher complexity or requiring more customization may take longer to complete.
What is the cost of RF module substrate?
The cost of RF module substrates varies based on a variety of factors. These include the selected materials, size, complexity, quantity, production process and other factors. Generally speaking, the choice of materials has a greater impact on cost, and high-performance materials such as Rogers and Arlon are usually more expensive. In addition, size and complexity also affect cost, with large size or high-density layout substrates likely to cost more. Ultimately, customization requirements and the choice of production processes also affect costs. Detailed inquiries need to be made to manufacturers based on specific project needs to obtain an accurate quote.
What special skills are required for the design of RF module substrates?
The design of RF module substrate requires an in-depth understanding of RF signals and PCB layout, as well as the use of professional design software for layout and simulation. Designers need to be familiar with the characteristics and parameters of RF circuits, such as frequency, power, impedance matching, etc., to ensure that the design meets performance requirements. In addition, good layout and routing are key to a successful design, and factors such as signal integrity, RF noise, and interference need to be considered. Designers usually use professional PCB design software, such as Altium Designer, Cadence Allegro, etc., to carry out design and simulation work to ensure the accuracy and reliability of the design.