RF Package Substrates Manufacturer .”RF Package Substrates Manufacturer” refers to a company specialized in producing substrates tailored for RF (Radio Frequency) applications. They design and manufacture substrates that ensure high-frequency performance, reliability, and efficiency in electronic devices such as communication equipment, radar systems, and satellite technology. These manufacturers employ advanced materials and processes to meet the stringent requirements of RF engineering, supporting seamless integration and optimal signal transmission in complex electronic systems.
In the context of today’s rapid development of wireless communication technology, RF packaging substrates play a key role in various high-frequency electronic devices. It is crucial for electronic engineers and wireless communication professionals to understand the definition, design, manufacturing process, application areas and advantages of RF packaging substrates. This article aims to provide a comprehensive introduction to the relevant knowledge of RF packaging substrates, covering everything from basic concepts to advanced applications.
What are RF Package Substrates?
RF Package Substrates are a key electronic component foundation specifically used in high-frequency electronic equipment. It is a flat plate-like structure made of insulating materials, usually materials such as FR4 (fiberglass reinforced epoxy laminate), which has good electrical insulation and mechanical strength. The main function of the RF packaging substrate is to support and connect various electronic components mounted on it.
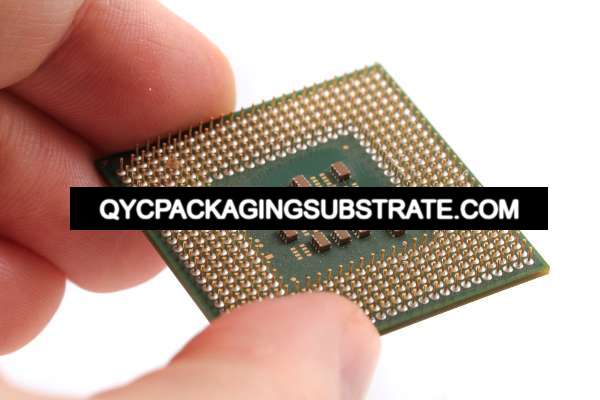
RF Package Substrates Manufacturer
On the RF package substrate, the connection and signal transmission between electronic components are realized through the wires, pads and other design features of the copper foil layer. The design and placement of these features must be precise to ensure good signal integrity and circuit performance at high frequencies. The manufacturing process of RF packaging substrates involves multiple key steps, including material preparation, copper foil processing, photolithography, etching, drilling, and final component mounting and testing.
Due to its special design and manufacturing requirements, RF packaging substrates are widely used in high-frequency electronic fields such as wireless communication systems, radar systems, satellite communications, and mobile communication equipment. In these applications, RF packaging substrates not only provide stable electrical performance and signal transmission characteristics, but also support reliable operation and high-efficiency operation of the equipment.
Overall, RF packaging substrates play an indispensable role in modern high-frequency electronic technology. Its precise design and highly sophisticated manufacturing process ensure the stability and reliability of modern electronic equipment in high-frequency environments. . With the continuous advancement of wireless communication technology, the design and manufacturing technology of RF packaging substrates are also constantly evolving to meet the needs of increasingly complex and high-frequency applications.
RF Package Substrates design Reference Guide.
The RF Package Substrate Design Reference Guide is an important tool for engineers and designers when creating RF package substrate layouts. This comprehensive handbook is more than just an instruction book; it is the key to ensuring design effectiveness and reliability in the field of high-frequency electronic equipment.
During the RF package substrate design process, it is critical to follow best practices. These practices cover everything from floorplanning to signal integrity. Through good layout planning, signal crosstalk and electromagnetic interference can be minimized, thereby ensuring system performance stability and reliability.
Design rules are basic guidelines that guide the design process and ensure that circuit boards meet specific electrical and mechanical requirements during production and use. These rules cover aspects such as how to select appropriate materials, how to design ground and power planes, and how to manage the routing of signal and power lines to maximize the performance of the board.
Software tools play a key role in modern RF packaging substrate design. From circuit design software to layout and simulation tools, these tools not only speed up the design process but also provide detailed signal and power analysis to help designers optimize layout and avoid potential design issues.
Design technology refers to the techniques and strategies designers apply in actual operations. These techniques include high-frequency circuit design, antenna design, power distribution, thermal management and EMC (electromagnetic compatibility) considerations. By deeply understanding and applying these technologies, designers can better solve complex design challenges and ensure that the final product meets expected performance and reliability requirements.
In summary, the RF Package Substrate Design Reference Guide provides engineers with a comprehensive framework to help them consider various critical factors during the design process. By following best practices, strictly adhering to design rules, making full use of software tools and proficient in design techniques, designers can effectively create high-performance, reliable RF packaging substrates to promote the development and application of wireless communication technology.
What material is used in RF Package Substrates?
RF packaging substrates are an integral component of modern high-frequency electronics, and their material selection is critical to performance and reliability. Typically, the main material used in RF packaging substrates is FR4 (fiberglass reinforced epoxy laminate). FR4 materials are known for their excellent electrical insulation properties and good mechanical strength, able to maintain stable electrical properties in high-frequency environments while providing sufficient structural support. This makes it the material of choice in most RF applications.
In addition to FR4, polyimide (PI) materials are selected for some RF packaging substrate applications that require flexible properties. Polyimide has excellent high temperature stability, chemical stability and flexibility, making it suitable for applications that require bending or bending. This material not only meets performance requirements in high-frequency environments, but also achieves good reliability and durability in complex engineering designs.
Overall, the material selection of the RF packaging substrate directly affects the performance and reliability of the overall circuit. During the design process, engineers need to select the most suitable material type and specifications based on specific application requirements and comprehensive consideration of electrical characteristics, mechanical strength, cost, manufacturing feasibility and other factors. Through precise material selection and reasonable design, the RF packaging substrate can be ensured to perform well in complex high-frequency environments, thus promoting the development and application of modern electronic technology.
What size are RF Package Substrates?
As an indispensable component of modern high-frequency electronic equipment, RF packaging substrates have various sizes and vary according to specific application requirements and equipment design. From tiny smartphones to massive industrial equipment, RF packaging substrates exhibit great flexibility and diversity in size.
First, micro RF packaging substrates are widely used in consumer electronics products, such as smartphones, tablets, and wearable devices. These devices often require compact designs to integrate multiple functions and electronic components within limited space. Micro RF packaging substrates not only need to be small and lightweight, but also ensure high performance and stable wireless communication connections, so the accuracy in the design and manufacturing process is extremely high.
Second, the RF packaging substrates used in industrial equipment and power electronics are often larger. Such devices may need to carry more electronic components and complex circuit structures to meet high power output or specific industrial application requirements. The large-sized RF packaging substrate not only provides a larger layout space, but also accommodates more radiators or other accessories, ensuring long-term stable operation of the equipment.
The choice of size directly affects the application effect and performance of RF packaging substrates in various industries. In the context of the ever-shrinking size of electronic components, the manufacturing technology of RF packaging substrates is also constantly improving to adapt to more complex and compact design requirements. At the same time, with the continuous development of wireless communication technology, the requirements for RF packaging substrates in terms of frequency response and signal transmission are becoming higher and higher, which further promotes the need for size and performance optimization.
In short, the size of RF packaging substrates varies depending on application scenarios, and the changes from micro to large sizes provide a wide range of options to meet the needs of different devices and industries for wireless communication and electronic integration. As technology advances and the market develops, RF packaging substrates will continue to play a key role in promoting innovation and application expansion of electronic products.
The Manufacturer Process of RF Package Substrates.
The manufacturing process of RF packaging substrates is a complex and delicate process involving multiple key steps, from substrate preparation to final testing, each step has an important impact on the quality and performance of the final product.
First, the process of manufacturing RF packaging substrates begins with substrate preparation. Commonly used base materials are fiberglass-reinforced epoxy (FR4) commonly used for high-frequency circuit boards, or for flexible applications, materials such as polyimide may be used. The quality and surface flatness of the substrate are crucial for subsequent process steps.
Next comes the copper layer deposition. Coat copper foil on the surface of the substrate to form a conductive layer. This step ensures the electrical conductivity of the circuit board. The thickness and uniformity of the copper foil directly affect the electrical performance of the circuit board.
This is followed by application of photoresist and exposure. Photoresist covers the entire copper foil surface and is exposed through a photomask. The exposed areas of photoresist are retained for subsequent etching steps.
Etching is a critical step that uses a chemical solution to etch away areas of the copper foil that are not protected by the photoresist to form the desired circuit pattern. The accuracy of etching determines the line spacing and line width of the circuit board, which is especially critical for high-frequency applications.
Drilling is to form through holes at designated locations for connecting circuits at different levels. These holes must be accurate to ensure the accuracy of subsequent component installation and connections.
Component mounting is the step of placing electronic components precisely in their intended locations. Depending on the design requirements and circuit complexity, Surface Mount Technology (SMT) or Through-Hole Technology (THT) can be used. SMT is suitable for miniaturization and high-density circuit boards, while THT is suitable for applications requiring higher mechanical strength and power transmission.
Soldering is a critical step in securing components and making electrical connections. By melting the solder, the component’s pins are connected to the copper foil, ensuring the integrity and stability of the circuit.
Finally, there is the testing phase, which includes electrical and functional testing. Electrical testing ensures that every line and connection on the circuit board meets design requirements, and functional testing verifies the performance and reliability of the circuit board in actual applications.
Overall, the manufacturing process of RF packaging substrates requires precise process control and a high degree of automated production equipment to ensure a balance between product quality and production efficiency. Each of these process steps is indispensable, and together they form an indispensable and critical component of modern high-frequency electronic equipment.
The Application area of RF Package Substrates.
As a key component of high-frequency electronic equipment, RF packaging substrate plays an indispensable role in modern technology applications. They are not just simple support structures for electronic devices, but also critical connectivity and processing cores in various industries. The following are the broad applications of RF packaging substrates in various major application areas:
In the field of consumer electronics, such as smartphones, tablets, home appliances and other products, RF packaging substrates carry wireless communication modules, antenna systems and high-frequency circuits. They are not only the basis for the realization of device functions, but also directly affect the performance and stability of the device. As consumer electronic devices increasingly integrate wireless communication functions, the demand for RF packaging substrates is also growing.
In the communications industry, such as base station equipment, satellite communications, radio frequency identification (RFID) systems and other fields, RF packaging substrates are the key to ensuring signal transmission quality and stability. The application of high-frequency circuits and microwave technology enables RF packaging substrates to handle complex communication requirements, such as widespread use in wireless networks, satellite communications and radar systems.
In automotive electronic systems, RF packaging substrates are used in key components such as vehicle communication systems, vehicle radars, and wireless control modules. They must be able to withstand harsh environmental conditions and ensure reliability and stability during high-speed movements. Advances in the design and manufacturing technology of RF packaging substrates enable automotive electronic systems to better achieve intelligence and interconnectivity.
In the aerospace field, RF packaging substrates are used in aircraft communication, navigation and control systems. These systems have extremely strict requirements for high-frequency signal processing and transmission. RF packaging substrates can also meet complex air communication and navigation requirements while ensuring lightweight, high strength and reliability.
In the field of medical equipment, RF packaging substrates are used in medical imaging equipment, wireless monitoring systems and telemedicine equipment. They support high-frequency signal processing and data transmission, ensuring the accuracy and safety of medical equipment. The reliability and stability of RF packaging substrates are critical to the normal operation of medical equipment.
In the field of industrial automation, RF packaging substrates are used in industrial control systems, sensor networks and smart manufacturing equipment. They can handle complex data communication and control tasks and support the realization of factory automation and intelligent production. The high performance and reliability of RF packaging substrates provide technical support for various applications in industrial environments.
Overall, the wide application of RF packaging substrates not only reflects its key position in high-frequency electronic technology, but also reflects the urgent need for high-performance and high-reliability electronic components in modern scientific and technological progress. With the continuous advancement of technology and the expansion of application fields, RF packaging substrates will continue to play an important role in promoting technological innovation and application development in various industries.
What are the advantages of RF Package Substrates?
RF packaging substrates show unique advantages in modern electronic equipment. Compared with traditional wiring methods, they have the following key advantages:
First, the compactness of RF packaging substrates allows electronic devices to achieve more miniaturized designs. Because RF packaging substrates can accurately lay out electronic components and wires and effectively utilize space, they are widely used in today’s miniaturized products such as smartphones and wearable devices.
Secondly, the RF packaging substrate adopts standardized manufacturing processes to ensure consistent product quality and reliability. This standardization not only reduces variability in the manufacturing process, but also enables each product to meet expected performance and life requirements, providing users with a reliable experience.
Third, the RF packaging substrate utilizes automated assembly processes, which greatly simplifies the production process. Automated assembly not only improves production efficiency, but also reduces labor costs and reduces the possibility of human errors, thereby further improving manufacturing efficiency and product consistency.
In addition, RF packaging substrates are highly customizable, enabling flexible layout and integration of complex circuits according to specific design requirements. This flexibility allows RF packaging substrates to meet the specific needs of a variety of different applications, including high-demand designs in wireless communications, satellite communications, medical equipment, and more.
Finally, because RF packaging substrates can be mass-produced, the unit cost can be significantly reduced, making them economical in mass manufacturing. This economy not only makes RF packaging substrates an ideal choice for various high-volume electronic products, but also promotes their widespread application and popularity around the world.
In summary, RF packaging substrate has become one of the indispensable key technologies in modern electronic equipment manufacturing through its compact, reliable, convenient, customizable and economical characteristics, promoting the continuous progress and innovation of electronic technology.
FAQ
What is the difference between RF packaging substrate and ordinary PCB?
RF packaging substrates are specially designed for high-frequency applications and have different material selection, manufacturing processes and electrical properties compared with ordinary PCBs. RF packaging substrates require higher electrical properties, such as low loss, low dielectric constant and good high-frequency characteristics, to ensure the stability and reliability of signal transmission.
What are the key design considerations for RF packaging substrates?
Key design considerations include optimization of high-frequency characteristics of circuit layout, ground plane design, matching network design of RF interfaces, signal loss reduction techniques and EMI (electromagnetic interference) management strategies, etc. These factors directly affect the performance of the RF packaging substrate and the effectiveness of the overall system.
How does material selection for RF packaging substrates affect performance?
Commonly used materials for RF packaging substrates, such as PTFE (polytetrafluoroethylene), RO4003C, etc., have low loss and stable high-frequency characteristics, and are suitable for applications with frequencies up to tens of GHz. The choice of materials directly determines the electrical performance of the packaging substrate, so a reasonable selection must be made based on specific application requirements during the design stage.
How to control the manufacturing tolerance of RF packaging substrate?
The manufacturing tolerances of RF packaging substrates are critical to the performance of high-frequency circuits. Manufacturing tolerances include line width and line spacing, hole position accuracy, plate thickness control, etc., which are usually required to be strictly controlled at the micron or even sub-micron level to ensure circuit matching and signal integrity.