RF PCB Manufacturer.An RF PCB Manufacturer specializes in crafting printed circuit boards (PCBs) tailored specifically for radio frequency (RF) applications. These expert craftsmen employ advanced techniques to ensure optimal performance in wireless communication devices, radar systems, and other RF-driven technologies. Their precision engineering and stringent quality control measures guarantee the integrity of signals, minimizing interference and maximizing efficiency. With a keen focus on meeting the exacting demands of modern communication standards, an RF PCB Manufacturer stands as a cornerstone in the seamless integration of RF technology across various industries.
In today’s highly interconnected world, wireless communication technology has become an important driving force for modern life and industrial development. In this field, the design and manufacturing of radio frequency (RF) PCBs are crucial. This article will delve into the key concepts, design principles and manufacturing process of RF PCB, aiming to help readers better understand and apply this key technology, thereby unlocking the key to wireless communications.
What is RF PCB?
RF PCB, or radio frequency (RF) printed circuit board, is a key component specially designed for radio frequency signal transmission and processing. Compared with traditional printed circuit boards (PCBs), RF PCBs require higher precision and technical levels in design and manufacturing to ensure stable transmission and optimal performance of high-frequency signals on the circuit board.
The transmission and processing of RF signals on circuit boards require extremely demanding circuit layout, line characteristics and material selection. RF PCBs usually require stricter impedance matching to ensure the stability and consistency of signals during transmission. In addition, RF PCB also needs to consider issues such as signal transmission loss, reflection, interference, and ground return to optimize signal transmission quality to the greatest extent.
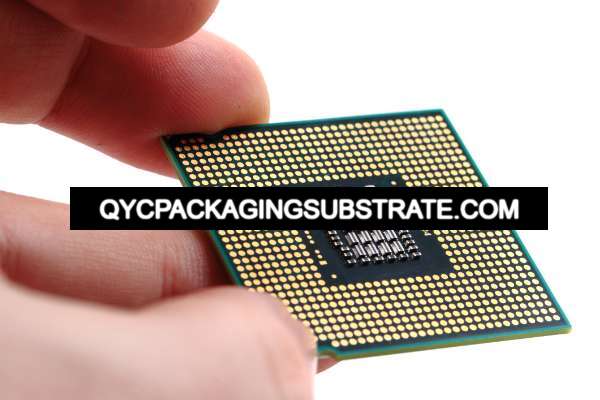
RF PCB Manufacturer
Various factors need to be considered during the design and manufacturing process of RF PCB, including board material selection, circuit layout, packaging design, and process control. Using appropriate plates (such as PTFE, RO4003C, etc.) can reduce dielectric loss and improve signal transmission efficiency; carefully designed circuit layout and reasonable packaging selection can minimize signal interference and crosstalk; strictly controlled manufacturing processes can ensure RF PCB performance and stability.
In short, RF PCB is a key component of radio frequency signal transmission and processing, and its design and manufacturing are crucial to the performance of wireless communication systems. Through precise design and manufacturing processes, RF PCB can transmit signals stably and reliably in high-frequency environments, providing important support for the development of wireless communication technology.
RF PCB design Reference Guide.
In modern wireless communication systems, the design of radio frequency (RF) PCB plays a vital role. Correct design can ensure stable transmission and optimal performance of signals, thus providing strong support for the development of wireless communication technology. The following are key principles and guidelines for RF PCB design to help engineers and designers achieve excellent RF PCB design:
Board material selection: Choosing a suitable board material is one of the primary considerations in RF PCB design. Commonly used high-frequency plates include polytetrafluoroethylene (PTFE), low dielectric loss materials, etc. These materials have lower dielectric constants and losses, which help reduce signal attenuation and improve transmission efficiency.
Transmission line design: Transmission lines are a vital component in RF PCB design. When designing transmission lines, factors such as impedance matching, signal integrity, and suppression of ground return flow need to be considered. Using appropriate transmission line design can ensure stable signal transmission and minimal signal attenuation.
Layout optimization: Reasonable layout design can reduce signal interference and crosstalk and improve system performance. Trace lengths and crossovers should be minimized to avoid electromagnetic coupling between RF components. At the same time, ensure good grounding between RF components to reduce ground return.
Package Selection: Choosing the right package is critical to RF PCB performance. Packages with good high-frequency characteristics should be selected, such as QFN, LGA, etc. At the same time, pay attention to good thermal management to ensure the stability and reliability of the package.
Electromagnetic compatibility (EMC) design: During the RF PCB design process, electromagnetic compatibility (EMC) design should be considered. Using appropriate shielding measures and filters can effectively reduce external interference and electromagnetic interference within the system, and improve the stability and reliability of the system.
Testing and Validation: After the design is completed, comprehensive testing and validation must be performed to ensure that the design performs as expected. Commonly used test methods include impedance testing, S-parameter testing, power testing, etc. Through testing and verification, problems in the design can be discovered and solved in time to ensure the performance and reliability of RF PCB.
To sum up, RF PCB design is a complex and critical task that requires designers to have solid professional knowledge and rich experience. Following the above guidelines and principles can help designers achieve excellent RF PCB design and contribute to the development of wireless communication technology.
What material is used in RF PCB?
The design and manufacturing of RF PCB (radio frequency printed circuit board) requires special attention to material selection, because the performance of the material directly affects the transmission and processing of high-frequency signals. Here are some key materials commonly used in RF PCBs:
PTFE (polytetrafluoroethylene): PTFE is a commonly used high-frequency material with low dielectric constant and low loss characteristics, suitable for high-frequency signal transmission requirements. In RF PCB, PTFE is usually used as the substrate material, providing good insulation properties and stable high-frequency characteristics.
RO4003C: RO4003C is a composite material with excellent high-frequency characteristics, composed of PTFE and glass fiber reinforced materials. It has low dielectric constant and loss and is suitable for high-frequency application scenarios, such as microwave communications, radar systems, etc.
FR4 (fiberglass reinforced epoxy): Although FR4’s high-frequency characteristics are not as good as PTFE or RO4003C, it is still widely used in some low-frequency or cost-sensitive RF PCB applications. FR4 has good mechanical strength and processability and is suitable for general radio frequency applications.
Metallized ceramics: Metallized ceramic materials have excellent thermal conductivity and mechanical strength and are suitable for high-power RF applications, such as radar antennas, microwave RF modules, etc.
Copper foil: Copper foil is a commonly used conductive material in RF PCB, used to make wires, ground planes, shielding layers, etc. The selection of copper foil should consider its thickness, purity and surface treatment to ensure good conductive properties and reliability.
When selecting RF PCB materials, factors such as dielectric properties, thermal properties, mechanical strength, processability, and cost need to be comprehensively considered. Appropriate material selection can ensure that RF PCB works stably and reliably in high-frequency environments, providing important support for the performance of wireless communication systems.
What size are RF PCB?
RF PCB dimensions can vary depending on application needs and often need to be determined based on specific design requirements and space constraints. Due to the high-frequency characteristics and sensitivity of radio frequency signals, the size design of RF PCB must consider factors such as signal transmission integrity, impedance matching, and signal attenuation.
For some small wireless devices or embedded systems, the RF PCB usually needs to be very small in size. This allows it to fit into compact spaces while reducing the length of transmission lines and the potential for signal attenuation and interference. Small RF PCBs are commonly found in portable devices such as Bluetooth headsets and smart watches.
In some applications that need to process complex RF signals or require high power transmission, a larger RF PCB size may be required. These boards are usually used in radar systems, communication base stations, satellite communications and other fields, and require more space to accommodate components such as complex signal processing circuits and power amplifiers.
With the development of flexible electronic technology, flexible RF PCB is gradually becoming a trend. This type of PCB has the ability to bend and fold and can be used with curved devices and is suitable for applications that need to match irregular surfaces, such as wireless sensor networks and wearable devices.
For some special applications, a custom size and shape of RF PCB may be required. Customized RF PCBs can be designed and manufactured according to specific project requirements to ensure perfect fit to the equipment structure and spatial layout, maximizing system performance and stability.
To summarize, the size and shape of the RF PCB depends heavily on the application requirements and design goals. Whether it is a small portable device or a large communication system, a carefully designed RF PCB is required to ensure stable signal transmission and good performance.
The Manufacturer Process of RF PCB.
The manufacturing process of RF PCB is similar to traditional PCB, but requires higher precision and stricter process control. During the manufacturing process, there are a series of critical steps that need to be gone through to ensure the performance and reliability of the RF PCB.
First, the selected substrate material needs to be pretreated to ensure that its surface is smooth, clean, and has good adhesion. This step involves removing surface oxides, oil, and other impurities, usually through chemical cleaning, sandblasting, or mechanical grinding.
RF PCBs typically have a multi-layer structure, with different layers used for functions such as routing, signal shielding, and power distribution. The layer stacking process involves stacking the pre-processed substrate with the copper foil layer and dielectric layer according to the design requirements, and firmly bonding them together through a lamination or hot pressing process.
After the layer stacking is completed, the surface of the board needs to be treated with copper foil. This involves pressing a copper foil layer to the substrate surface and chemically or mechanically removing excess copper foil to create the desired circuit patterns and connection points.
Once the copper foil layer is in place, the next step is to drill holes in the board. These holes are used to connect circuits between different layers and for soldering or insertion when mounting components. Drilling accuracy and position control are critical to RF PCB performance, so a high-precision CNC drilling machine and suitable drill bits are required.
Line printing is a key step in printing circuit patterns and connection points onto the board surface. This is usually achieved through photolithography and etching processes, where a light-sensitive photoresist is coated on the surface of the board and then exposed and etched to form the desired circuit pattern.
Finally, pad coating is performed to protect the circuitry and provide a surface for component mounting. Solder pads usually consist of solder paste or wax that is applied to the area to be soldered. During assembly, the pads will be used to connect component pins and ensure a stable electrical connection.
Throughout the manufacturing process, strict control of process parameters is key to ensuring RF PCB performance and reliability. From material selection to final assembly, each step requires careful monitoring and adjustment to ensure design requirements are met and expected performance levels are achieved. Through careful manufacturing processes, RF PCB can operate stably and reliably in high-frequency environments, providing solid support for the development of wireless communication technology.
The Application area of RF PCB.
RF PCB has extensive and critical applications in the field of wireless communications. From wireless network equipment to satellite communications, from radar systems to wireless sensor networks, the advantage of RF PCB lies in its excellent performance in high-frequency signal processing and transmission, making it the first choice for many critical applications.
First of all, RF PCB plays a vital role in wireless network equipment. Whether it is Wi-Fi routers, base station equipment, or transmission equipment in cellular networks, reliable RF PCBs are needed to ensure stable transmission and efficient processing of signals. Design optimization of RF PCB can improve the performance and coverage of network equipment, thereby providing users with faster and more stable wireless connections.
Secondly, RF PCB also plays an irreplaceable role in satellite communications. Satellite communication systems require electronic equipment that can operate stably in extreme environments, and RF PCB is a key component of it. Whether used for satellite communication terminal equipment or satellite transmitters, high-quality RF PCB can ensure stable transmission and reliable reception of signals, thereby achieving a seamless connection between the earth and space.
In addition, radar systems are also one of the important application areas of RF PCB. Radar systems need to detect targets quickly and accurately, and transmit and process signal data in a timely manner. The design of RF PCB needs to take into account the high-frequency signal processing requirements of the radar system, as well as the ability to resist interference and noise, so as to ensure that the radar system can operate reliably under various environmental conditions.
Finally, in wireless sensor networks, RF PCB also plays a key role. Wireless sensor networks are usually deployed in various environments for monitoring and collecting data, such as environmental monitoring, industrial control, and smart Internet of Things. The high-frequency signal processing capabilities and stability of RF PCB can ensure fast and reliable data transmission between sensor nodes, thereby achieving real-time monitoring and control of the environment and equipment status.
In short, the applications of RF PCB in the field of wireless communications are diverse and crucial. Whether used for network communications, satellite connections, radar detection or sensor networks, the superior performance of RF PCB provides reliable technical support for various key applications and promotes the continuous development and innovation of wireless communication technology.
What are the advantages of RF PCB?
RF PCB has significant advantages over traditional circuit boards, which make it an indispensable and key component in wireless communication systems. First, RF PCB has lower signal attenuation. In high-frequency environments, signal attenuation is a common challenge, leading to signal quality degradation or even signal loss. Because the RF PCB uses high-quality materials and precise manufacturing processes, its signal attenuation is lower, which ensures that the signal maintains a high intensity during transmission and improves the transmission distance and stability of the system.
Secondly, RF PCB has higher signal integrity. In wireless communication systems, signal integrity is a key factor to ensure the accuracy and stability of data transmission. Through optimized layout design and special transmission line technology, RF PCB can effectively reduce signal distortion and waveform distortion, ensuring that the signal maintains integrity during transmission, thereby improving system performance and reliability.
In addition, RF PCB has better anti-interference ability. In complex wireless environments, various sources of interference may negatively impact system performance. The RF PCB adopts specially designed layout and shielding measures, which can effectively suppress the influence of external interference and ensure the stable operation of the system. Its excellent anti-interference ability enables it to perform well in complex electromagnetic environments, providing reliable protection for the system.
Finally, RF PCB ensures stable and reliable signal transmission in high-frequency environments through precise design and manufacturing. High-frequency environments have higher requirements on PCBs, requiring more precise manufacturing processes and higher-quality materials. RF PCB uses advanced manufacturing technology and high-quality materials to ensure its stability and reliability in high-frequency environments, providing important support for the performance of wireless communication systems.
To sum up, RF PCB has become an indispensable key component in wireless communication systems due to its low signal attenuation, high signal integrity, excellent anti-interference ability and stable and reliable performance. With the continuous development of wireless communication technology, RF PCB will continue to play an important role in promoting the progress and development of wireless communication systems.
FAQ
How to choose suitable materials for RF PCB?
Choosing the right materials for your RF PCB is key to ensuring high performance and reliability. First, the dielectric constant and loss need to be considered, which directly affect the speed and attenuation of signal transmission. Materials such as PTFE (polytetrafluoroethylene) generally have low dielectric constants and losses, making them suitable for high-frequency applications. Secondly, factors such as thermal stability, mechanical strength and cost also need to be considered to balance the relationship between performance and cost. Common RF PCB materials include PTFE, FR4, etc., which should be selected according to specific application requirements.
How to avoid signal interference from RF PCB?
Avoiding signal interference from RF PCB is one of the keys to ensuring stable system performance. First, signal interference and crosstalk should be reduced through reasonable layout design. This includes minimizing trace lengths, crossovers, and loops, and optimizing the placement of RF components. Secondly, measures such as impedance matching, shielding and ground wire design should be taken to minimize the impact of external interference on the system. In addition, choosing appropriate packaging and shielding technology can also effectively improve the anti-interference ability of the system.
What are the precautions for the manufacturing process of RF PCB?
During the manufacturing process of RF PCB, special attention needs to be paid to the control of process parameters to ensure the stability and consistency of the material. First of all, the appropriate manufacturer and process should be selected to ensure that it has experience and technical strength in RF PCB manufacturing. Secondly, in key steps such as material preprocessing, layer stacking, copper foil preparation, drilling, line printing, pad coating, etc., the temperature, humidity, and concentration of chemical substances should be strictly controlled to prevent changes in material properties and improper stability. In addition, production equipment should be maintained and calibrated regularly to ensure its normal operation and production quality.