RF SIP Substrate Manufacturer.As an RF SIP substrate manufacturer, we specialize in crafting high-quality substrates for Radio Frequency System in Package (RF SIP) applications. Our expertise lies in delivering precision-engineered substrates that ensure optimal signal integrity and performance in wireless communication devices.
With the rapid development of wireless communication technology, RF SIP substrate plays a key role in modern electronic equipment. This substrate integrates radio frequency circuits and packaging technology, providing a reliable solution for high-frequency, high-speed data transmission. This article will explore the application of RF SIP substrates in the fields of communications, consumer electronics, automotive electronics, and industrial automation, as well as its advantages in integration, miniaturization, high performance, reliability, and flexibility.
What is RF SIP Substrate?
RF SIP substrate, the full name of RF System in Package substrate, is a multi-layer board that integrates radio frequency circuits and packaging technology and is used to transmit data and signals in a high frequency range. Compared with traditional RF solutions, RF SIP substrates provide a more compact and efficient design solution by integrating RF circuitry and packaging technology.
Usually, RF SIP substrates are made of special high-frequency materials. These materials have excellent dielectric properties and radio frequency characteristics and can meet the signal transmission requirements of complex communication systems. Since the RF SIP substrate integrates radio frequency circuits and packaging technology, the system design and layout are more simplified, reducing the number of components and connection lines, and improving the integration and stability of the system.
In the high frequency range, the transmission of radio frequency signals needs to consider factors such as signal stability, transmission efficiency, and anti-interference ability. The RF SIP substrate effectively improves the signal transmission performance by optimizing the radio frequency circuit design and packaging process, and achieves high-frequency and high-speed data transmission and signal processing. Therefore, RF SIP substrates are widely used in mobile communications, wireless networks, satellite communications, radar systems and other fields.
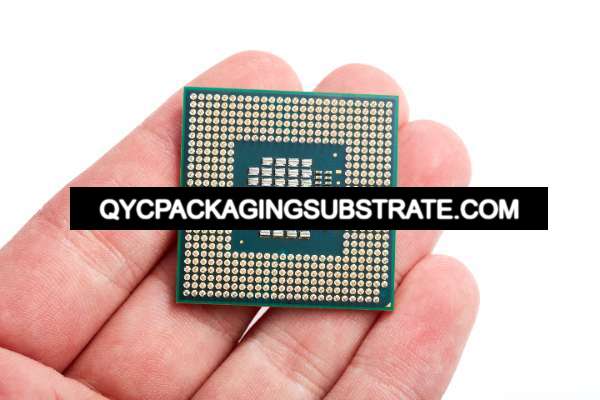
RF SIP Substrate Manufacturer
Overall, the RF SIP substrate provides a reliable and efficient solution for data transmission and signal processing in the high frequency range by integrating radio frequency circuits and packaging technology. Its excellent performance and flexible design features make it an indispensable key component in modern communication systems.
RF SIP Substrate design Reference Guide.
RF SIP (Radio Frequency System Integrated Package) substrate design is a vital part of modern wireless communication systems. The following is a best-practice RF SIP substrate design reference guide to help you ensure the performance and reliability of your design.
Choosing the right substrate material is critical to RF SIP design. Commonly used high-frequency materials include PTFE (polytetrafluoroethylene), PTFE composite materials, and low-loss dielectric constant ceramic materials. These materials have excellent dielectric and radio frequency properties and are suitable for high-frequency signal transmission.
In RF SIP substrate design, a reasonable layer stacking structure is crucial to maintain signal integrity and reduce signal coupling. Signal distortion and crosstalk can be minimized by controlling the distance between layers, choosing appropriate ground plane settings, and using techniques such as layered leads.
In RF SIP design, ensuring impedance matching of signal lines is critical, especially for high-frequency signals. By correctly designing the microstrip line width, spacing, and ground plane settings, precise control of impedance can be achieved to ensure stable transmission and matching of signals.
In RF SIP design, high-power RF devices may generate a lot of heat, so good thermal design is crucial. By rationally arranging heat sinks, adding ventilation holes, and selecting substrate materials with high thermal conductivity, the heat dissipation efficiency can be effectively improved and the stability and reliability of the system can be ensured.
The packaging technology of RF SIP substrate has an important impact on system performance and reliability. Common packaging technologies include ball grid array (BGA), QFN (padless packaging), and LGA (top contact array). Selecting the appropriate packaging technology can achieve effective protection of the device and good signal transmission.
After completing the RF SIP substrate design, simulation and testing are key steps to verify the design performance. By using RF simulation software for signal integrity analysis, impedance matching simulation, and thermal analysis, potential design problems can be discovered and solved early to ensure the performance and reliability of the design.
RF SIP substrate design is a complex and critical process that requires comprehensive consideration of material selection, layer stacking structure, impedance matching, heat dissipation design, packaging technology, and simulation testing. By following the above guidelines, you can design an RF SIP substrate with excellent performance, stability and reliability, providing strong support for the development and application of wireless communication systems.
What material is used in RF SIP Substrate?
The main materials used in RF SIP substrates play a key role in achieving high-frequency, high-rate data transmission and signal processing. The following are the main materials commonly used for RF SIP substrates:
High-frequency glass fiber reinforced polyimide (FR-4): FR-4 is a commonly used substrate material with good mechanical strength and thermal stability, suitable for general RF applications. However, at higher frequencies, FR-4’s dielectric losses may limit its performance.
Polytetrafluoroethylene (PTFE): PTFE is a material with a low dielectric constant and low dielectric loss, making it suitable for high-frequency RF applications. Its characteristics enable the RF SIP substrate to have lower signal attenuation and higher signal transmission efficiency at high frequencies.
Polyimide (PI): PI material has excellent thermal stability and mechanical strength and is suitable for radio frequency applications in high temperature environments. It also has good chemical stability and corrosion resistance, making it suitable for applications in harsh environments.
Ceramic substrate: Ceramic substrate has excellent dielectric properties and RF characteristics, making it suitable for UHF and millimeter wave RF applications. Its characteristics enable the RF SIP substrate to have more stable performance at high frequencies and high rates.
Polystyrene (PS): PS material has low cost and good processing properties, making it suitable for general RF applications. However, due to its relatively poor dielectric properties, it is usually used in low-frequency or low-rate applications.
When selecting RF SIP substrate materials, factors such as the frequency range of the application, signal transmission requirements, environmental conditions, etc. need to be considered to ensure that system performance and reliability requirements are met. Different materials have different properties and application ranges, so careful material selection and performance evaluation are required during the design phase.
What size are RF SIP Substrate?
RF SIP substrate sizes vary depending on application needs and design requirements. Typically, RF SIP substrates can be designed in various sizes to suit different electronic devices and systems. Generally speaking, the size of the RF SIP substrate can vary from a few millimeters to tens of centimeters, depending on the following factors:
Application scenarios: RF SIP substrates are widely used in communication equipment, consumer electronics, automotive electronics, industrial automation and other fields. Different application scenarios have different requirements for substrate size. Some applications require miniaturized design to fit into a compact space, while others require larger sizes to accommodate more functional modules.
Performance requirements: The size of the RF SIP substrate is also affected by performance requirements. Some high-performance RF applications may require larger substrate sizes to accommodate complex circuit designs and reduce signal loss, while some low-power or portable devices may require smaller substrate sizes to achieve compact designs and save space.
Manufacturing process: The manufacturing process of the RF SIP substrate also affects its size. The use of advanced manufacturing processes and materials enables smaller substrate designs while maintaining good RF performance and reliability.
Overall, the size of the RF SIP substrate can be customized based on specific application needs and design considerations to achieve optimal performance and reliability. With the continuous development and advancement of radio frequency technology, we can expect to see the emergence of more compact and high-performance RF SIP substrates in the future, promoting the further development and application of wireless communication systems.
The Manufacturer Process of RF SIP Substrate.
The manufacturing process of RF SIP substrate is a complex and precise process involving multiple steps and expertise. The following will briefly introduce the manufacturing process of RF SIP substrate:
Material preparation: The manufacturing of RF SIP substrates usually uses high-frequency materials, such as PTFE (polytetrafluoroethylene) substrates or low dielectric constant glass fiber reinforced composite materials. Before the manufacturing process can begin, these materials need to be prepared to ensure that their quality and performance meet requirements.
Sheet Processing: The first step in the manufacturing process is cutting the raw sheet into the desired size and shape. This requires precision cutting equipment and process control to ensure the dimensional accuracy and surface quality of the panels.
Circuit design and layout: Designing and laying out RF circuits on RF SIP substrates is one of the key steps in the manufacturing process. Designers need to accurately plan circuit layout, signal paths and connections based on system requirements and performance indicators to ensure optimal RF performance and signal transmission quality.
Circuit Printing: Next, the RF circuit is added to the substrate by printing or etching. This typically involves the use of special printing equipment or chemical treatments to create accurate circuit patterns on the surface of the substrate.
Metallization: After the circuit pattern is completed, it needs to be metallized. A metallized film is usually used to cover the circuit path to provide good conductivity and signal transmission performance.
Packaging and Assembly: After the RF circuit is completed, the RF SIP substrate needs to be packaged and assembled to protect the circuit and connect external components. This may involve soldering, gluing or other packaging techniques to ensure reliable connections between circuits and components.
Quality testing and debugging: The final stage of the manufacturing process is quality testing and debugging of the RF SIP substrate. This includes rigorous testing and verification of the circuit’s functionality, performance specifications, and signal transmission quality to ensure it meets design requirements and standards.
Through the above steps, after the RF SIP substrate manufacturing process is completed, products with excellent radio frequency performance and reliability will be obtained, which can be widely used in wireless communications, consumer electronics, automotive electronics and other fields, promoting the development and application of modern electronic technology.
The Application area of RF SIP Substrate.
RF SIP substrates are widely used in various fields, including communication equipment, consumer electronics, automotive electronics and industrial automation.
First of all, in the field of communication equipment, RF SIP substrates are widely used in key equipment such as mobile communication base stations, satellite communications and radar systems. These systems require high-rate data transmission and radio frequency signal processing capabilities, and the RF SIP substrate can provide reliable radio frequency performance and excellent signal transmission performance to meet the needs of complex communication systems.
Secondly, in the field of consumer electronics, RF SIP substrates are widely used in products such as smartphones, tablets, and wireless network equipment. These products require wireless connectivity and high-performance radio frequency functionality, and the miniaturization and integration of RF SIP substrates can meet the compact design and high-performance communication requirements of these products.
In addition, RF SIP substrates also have important applications in the field of automotive electronics. It is used in key components such as vehicle communication systems, radar sensors, and Internet of Vehicles to support data exchange and communication between vehicles and between vehicles and infrastructure. The high performance and reliability of RF SIP substrate can ensure the stable operation of automotive electronic systems in complex vehicle environments.
Finally, in the field of industrial automation, RF SIP substrates are widely used in key applications such as industrial control systems, IoT devices, and sensor networks. It can achieve efficient data collection and remote monitoring, and provide reliable technical support for the intelligence and networking of industrial automation systems.
In general, RF SIP substrates have a wide range of applications in the fields of communications, consumer electronics, automotive electronics, and industrial automation, providing reliable solutions for high-performance communication and data processing of various electronic devices and systems.
What are the advantages of RF SIP Substrate?
RF SIP substrate (RF System in Package Substrate), as an advanced solution integrating radio frequency circuit and packaging technology, has significant advantages in the field of modern electronic communications. The following are the main advantages of RF SIP substrate:
High integration: RF SIP substrate integrates radio frequency circuits and packaging technology, greatly simplifying system design and layout. Compared with traditional RF solutions, it reduces the number of components and connection lines, improves system integration, and helps achieve more compact and lightweight electronic equipment design.
Excellent radio frequency performance: The RF SIP substrate is made of special high-frequency materials and has excellent radio frequency characteristics and signal transmission performance. It can support high-frequency, high-rate data transmission and signal processing to meet the high performance requirements of complex communication systems.
Miniaturized design: Due to the use of multi-layer board structure and high-frequency materials, the RF SIP substrate has smaller size and weight. This makes it ideal for electronic devices with limited space, allowing for more compact and lightweight product designs.
Good thermal stability: RF SIP substrate adopts advanced manufacturing processes and materials and has good thermal stability. In high temperature environments, it can maintain stable performance and is not prone to failure or deformation, ensuring reliable operation of the system under various working conditions.
Flexible customization: The RF SIP substrate is designed to be flexible and can be customized according to specific application requirements. It supports the integration of a variety of RF circuits and packaging solutions, and can be customized according to different application scenarios to meet the specific needs of customers.
To sum up, RF SIP substrate has become an indispensable part of modern electronic communication systems due to its advantages such as high integration, excellent radio frequency performance, miniaturized design, good thermal stability and flexible customization. , promoting the sustainable development and innovation of wireless communication technology.
FAQ
What is RF SIP substrate?
RF SIP substrate is a multi-layer board that integrates radio frequency circuits and packaging technology and is used to transmit data and signals in a high frequency range. It combines RF circuit design and packaging technology to provide high-performance solutions for wireless communication systems.
What are the application areas of RF SIP substrate?
RF SIP substrates are widely used in communication equipment (such as mobile communication base stations, satellite communications), consumer electronics (such as smartphones, tablets), automotive electronics (such as vehicle-mounted communication systems, radar sensors), and industrial automation (such as industrial control systems, Internet of Things devices) and other fields.
What are the advantages of RF SIP substrates over traditional RF solutions?
RF SIP substrate has the advantages of integration, miniaturization, high performance, reliability and flexibility. It integrates radio frequency circuit and packaging technology, simplifying system design and layout; due to the use of multi-layer board structure and high-frequency materials, it has smaller size and weight; at the same time, it has excellent radio frequency characteristics and signal transmission performance, ensuring the system stable operation.
How to choose a suitable RF SIP substrate?
Selecting a suitable RF SIP substrate requires considering factors such as the frequency range of the application, signal transmission performance, and packaging requirements. It usually requires custom design based on specific application requirements and selection of appropriate RF circuits and packaging solutions to achieve optimal performance and reliability.
What is the manufacturing process of RF SIP substrate?
The manufacturing process of RF SIP substrate includes material selection, lamination process, circuit design, packaging process and other links. Advanced manufacturing technology and materials are used to ensure that the substrate has good RF characteristics and stable performance.