We are a professional Rigid-flex packaging substrate Maker, we mainly produce BGA Rigid-Flex Packaging Substrate and Rigid-Flex BGA Substrate from 4 layer to 20 layers.
The concept of Rigid-Flex Packaging Substrate, an electronic packaging solution that seamlessly integrates rigid and flexible materials, has emerged in response to the dynamic requirements for spatial efficiency and diverse shapes in electronic devices. In contrast to conventional circuit boards constrained by rigid materials, this innovative design offers unparalleled adaptability and moldability.
The inspiration behind the development of the Rigid-Flex Packaging Substrate stems from the inherent limitations of traditional circuit boards, which struggle to conform to intricate shapes and confined spaces. By ingeniously blending rigid and flexible materials, this cutting-edge technology introduces a new realm of possibilities in electronic engineering. It not only addresses the challenges associated with complex shapes but also excels in compact environments, marking a significant advancement in electronic packaging.
The key to this design concept is flexibility. The structure of Rigid-Flex Packaging Substrate allows it to bend freely in different shapes, allowing it to better adapt to the design requirements of various devices. Whether it is portable smart devices, wearable technology, or other applications that have strict requirements on shape, Rigid-Flex Packaging Substrate is ready to come out.
An additional significant benefit lies in the plasticity inherent in the design of Rigid-Flex Packaging Substrates. This innovative approach facilitates the placement of electronic components in three-dimensional space, resulting in heightened integration on the circuit board. This not only contributes to a more compact device but also affords engineers greater design flexibility, empowering them to optimize product performance more effectively.
In practical applications, Rigid-Flex Packaging Substrate has been successfully used in a range of fields. Curved screens in smartphones, flexible sensors in medical devices, and requirements for lightweight and shape adaptability in aerospace all demonstrate the broad potential of this technology.
When considering the adoption of Rigid-Flex Packaging Substrate, it is crucial to carefully evaluate several factors, including manufacturing costs, long-term reliability, and durability. Despite the rapid advancements in technology, practical decision-making should be rooted in specific scenarios and actual needs.
Rigid-Flex Packaging Substrate stands out as a transformative technology challenging traditional electronic engineering concepts. Its distinctive design seamlessly integrates rigid and flexible materials, resulting in unparalleled adaptability and flexibility. This innovative approach grants engineers greater freedom in designing electronic devices. However, successful implementation of this technology requires a comprehensive assessment of various considerations to ensure it attains its full potential in real-world applications.
What types of Rigid-Flex Packaging Substrate are there?
Double-sided Rigid-Flex
Double-sided Rigid-Flex Packaging Substrate combines rigid and flexible materials so that flexible circuit boards are distributed on both sides. This design provides greater flexibility and stability and is suitable for equipment with higher requirements on board layout and connectivity, such as some complex communication equipment and automotive electronic systems.
The Multilayer Rigid-Flex Packaging Substrate boasts a sophisticated design, seamlessly incorporating multiple rigid and flexible layers. This intricate structure not only enables a high level of integration but also grants designers precise control over circuit layout. Tailored for high-performance applications requiring extensive signal and data processing, such as advanced computers, servers, and industrial automation systems, the Multilayer Rigid-Flex stands out for its versatility and capability.
In contrast, the single-sided Rigid-Flex, with its flexible design, excels in scenarios demanding superior bending performance and lightweight characteristics. This makes it an ideal choice for applications like smart wearable devices and biomedical sensors where agility and portability are paramount.
For connectivity and reliability, the double-sided Rigid-Flex takes the spotlight. Its advantages position it as the preferred choice for complex communication equipment and automotive electronic systems that must endure extreme environmental conditions and high vibration levels. The Double-sided Rigid-Flex stands out as a robust solution ensuring stable performance in demanding applications.
Multi-layer Rigid-Flex is suitable for scenarios that require high integration and complex circuit layout, providing excellent performance in fields such as high-performance computers and industrial automation.
The multiple forms of Rigid-Flex Packaging Substrate provide electronic engineers with more choices to meet the needs of different application scenarios. Single-sided, double-sided and multi-layer designs each have unique advantages, bringing greater flexibility and performance advantages to device design. By understanding these different types of Rigid-Flex Packaging Substrate, engineers can better select solutions suitable for their projects, driving innovation and development in electronic engineering.
What are the advantages of Rigid-Flex Packaging Substrate?
Rigid-Flex Packaging Substrate is spearheading innovation in the field of electronic engineering, thanks to its distinctive design and numerous advantages. In contrast to conventional rigid circuit boards, Rigid-Flex Packaging Substrate demonstrates superior adaptability, reliability, and stability, offering engineers more versatile solutions.
Traditional rigid circuit boards are usually limited by the rigidity of their shapes, while Rigid-Flex Packaging Substrate allows electronic devices to more freely adapt to various shapes and space constraints through clever design that combines rigid and flexible materials. This flexibility gives designers greater freedom, especially in form-critical devices such as wearables and curved screens.
Rigid-Flex Packaging Substrate offers a notable advantage in enhanced reliability. Its distinctive structural design reduces the number of connection points and welds, minimizing potential points of failure. Additionally, the substrate demonstrates increased resistance to vibration and shock, significantly enhancing equipment stability in challenging working environments. This attribute holds particular significance for applications demanding high reliability and durability, such as military and medical equipment.
Another critical advantage of Rigid-Flex Packaging Substrate is its inherent stability. The overall structural robustness enables optimal functionality even in the presence of temperature fluctuations and electromagnetic interference. This resilience proves especially advantageous for equipment operating in extreme conditions, such as automotive electronic systems and avionics, ensuring consistent performance and an extended service life.
In contrast to traditional circuit boards, Rigid-Flex Packaging Substrate demonstrates a superior level of integration. By combining rigid and flexible sections, a larger number of electronic components can be accommodated within the same spatial constraints. This not only enhances circuit board performance but also streamlines the design of more compact devices, paving the way for the miniaturization and lightweighting of electronic products.
Overall, Rigid-Flex Packaging Substrate provides more advanced solutions for electronic engineers with its breakthrough in traditional design concepts and multiple advantages. Its advantages in adaptability, reliability, and stability make it a highly anticipated technology in the current electronics industry, indicating that future electronic equipment will be more flexible, reliable, and efficient.
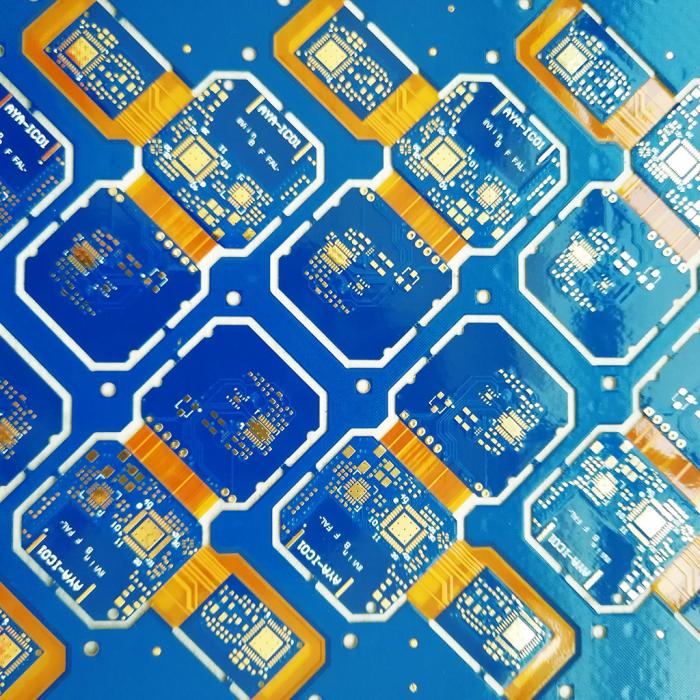
Rigid-flex packaging substrate Maker
Why choose Rigid-Flex Packaging Substrate?
The Rigid-Flex Packaging Substrate (RFP Substrate) has gained significant traction in electronic engineering design, emerging as a pioneering option for electronic packaging substrates. Engineers are progressively favoring RFP Substrate over conventional circuit boards, necessitating an exploration of the factors driving this transition.
To delve deeper into this matter, we need to examine the unique advantages and features that RFP Substrate offers in comparison to conventional circuit boards. The growing preference for RFP Substrate suggests that it presents distinctive benefits, potentially including enhanced flexibility, improved reliability, and increased design possibilities. By understanding these specific advantages, we can gain insights into why engineers are embracing RFP Substrate as a preferred option in electronic engineering design.
One of the biggest highlights of RFP Substrate is its unique flexibility and adaptability. Compared with the rigid structure of traditional circuit boards, RFP Substrate allows designers to use curved and folded shapes more freely in product layout. This flexibility provides greater scope for device design, especially in space-constrained applications such as portable devices or embedded systems.
The design of RFP Substrate greatly reduces the number of connection points between electronic components. Compared with the plugs and connectors required on traditional circuit boards, the flexible connections inside RFP Substrate are simpler, reducing the contact resistance between electronic components and improving the stability of the overall circuit.
Due to its flexibility and highly integrated nature, RFP Substrate can achieve higher performance while reducing the size and weight of electronic devices. In areas that require thin and light designs, such as wearable devices and mobile communication tools, the advantages of RFP Substrate are particularly obvious.
RFP Substrate is well-suited for applications necessitating intricate layouts, such as curved screens and three-dimensional structures. This opens up innovative possibilities for engineers, fostering greater creativity and product differentiation in design.
The flexibility of RFP Substrate’s materials facilitates efficient heat conduction and dissipation, enhancing the device’s overall heat dissipation performance. This feature is particularly crucial in demanding environments with high heat dissipation requirements, such as high-performance computers and communication equipment.
Because RFP Substrate uses flexible materials, it is more resistant to earthquakes and vibrations than the hard connections on traditional circuit boards. Therefore, RFP Substrate is more suitable for situations that require higher reliability, such as the aerospace field.
To sum up, RFP Substrate has obvious advantages over traditional circuit boards in terms of flexibility, space utilization, volume and weight, complex layout, heat dissipation performance and reliability. In the current electronic engineering design that increasingly pursues innovation and flexibility, more and more engineers choose RFP Substrate because it provides them with more design freedom while bringing higher performance and reliability. In the continuous development of the field of electronic engineering, RFP Substrate is becoming an important driver of technological progress.
What is the manufacturing process of Rigid-Flex Packaging Substrate?
The production of Rigid-Flex Packaging Substrate is a complex and crucial task in the field of electronic engineering, focused on seamlessly integrating rigid and flexible materials to ensure exceptional stability and reliability in the end product. The manufacturing process for Rigid-Flex Packaging Substrate begins with careful material selection. Usually, the rigid layer includes fiberglass-reinforced epoxy resin, while the flexible layer utilizes flexible materials like polyimide. This combination of materials is essential for preserving the structural integrity of the circuit board during bending and deformation.
The manufacturing process closely mirrors that of traditional rigid circuit boards for motherboards, encompassing key stages such as graphic design, printed circuits, etching, drilling, and other precision-oriented steps. These measures are essential to ensure optimal circuit performance and reliability in the final Rigid-Flex Packaging Substrate product.
The manufacturing of base plates involves the application of flexible materials. Through a precise lamination process, flexible layers and rigid layers intersect with each other to form a base plate with flexible bending properties. This step requires a high degree of technical reserve and experience.
The combination of motherboard and backplane needs to be cured through a lamination process. This step ensures a strong bond between the two, laying a solid foundation for subsequent process steps.
Following lamination, the subsequent processes of drilling and metallization become imperative. Drilling involves creating conductive vias to establish connections between various layers of the motherboard and backplane.
Common methods include tin spraying and nickel-gold spraying. These treatments provide a protective layer that contributes to the longevity and performance of the circuit boards.
The ultimate step in the manufacturing process involves stringent quality inspection. Utilizing advanced testing equipment, each Rigid-Flex Packaging Substrate undergoes thorough scrutiny to ensure compliance with design specifications and performance standards.
Throughout the manufacturing journey, meticulous design principles play a crucial role in guaranteeing stability and reliability. Given the flexible and curved nature of circuit boards, designers must focus on circuit layout, strategic connector placement, and additional protection for flexible components.
The intricate nature of the Rigid-Flex Packaging Substrate’s manufacturing process demands highly specialized skills and advanced equipment. Manufacturers, through innovative design approaches and rigorous quality control measures, succeed in producing adaptable and reliable electronic components. This drive towards innovation propels the field of electronic engineering into a promising future.
What is the application of Rigid-Flex Packaging Substrate?
Rigid-Flex Packaging Substrate is gradually gaining prominence and finding extensive use in the realm of electronic engineering. Its distinctive design and exceptional performance have led to significant success across various industries.
Primarily, Rigid-Flex Packaging Substrate has demonstrated considerable potential in the smartphone sector. With the growing demand for slimmer and more flexible mobile phone designs, this substrate facilitates the creation of more compact circuit layouts, enabling comprehensive enhancements in both the form and functionality of mobile phones.
In the domain of medical equipment, the successful integration of Rigid-Flex Packaging Substrate lays a robust foundation for innovation. This flexible circuit board not only accommodates the intricate shape requirements of medical equipment but also ensures reliable electrical connections
Rigid-Flex Packaging Substrate has proven to be exceptionally effective in demanding aerospace environments, showcasing outstanding performance attributes. Its remarkable qualities, including high temperature resistance, lightweight design, and efficient space utilization, position it as an optimal choice for aerospace devices such as satellites and missiles. The substrate’s stability and customizable nature empower engineers in the aerospace sector to design and deploy electronic systems with increased flexibility.
Furthermore, Rigid-Flex Packaging Substrate has achieved notable advancements in automotive electronics and industrial automation. In automotive applications, it enhances the spatial layout and reliability of vehicle electronic systems, addressing the demand for smarter and more compact electronic solutions by car manufacturers. In industrial automation, its flexibility and stability enable seamless integration into various automatic control systems, allowing them to adapt effectively to complex industrial environments.
The widespread adoption of Rigid-Flex Packaging Substrate has garnered significant attention in the field of electronic engineering, delivering efficient and innovative solutions across diverse industries. Its successful integration into smartphones, medical equipment, aerospace, and other sectors continues to drive advancements in electronic engineering, laying a robust foundation for future technological innovations.
How do I get a quote for Rigid-Flex Packaging Substrate?
Selecting the appropriate supplier for Rigid-Flex Packaging Substrates is paramount in electronic engineering, and securing an accurate quote serves as the initial stride towards project success. The following discussion outlines the steps to obtain a precise quotation for Rigid-Flex Packaging Substrates when choosing a supplier, thus guaranteeing the project’s prosperity.
First of all, to obtain an accurate quotation for Rigid-Flex Packaging Substrate, engineers can usually choose two main ways: contact the manufacturer directly or obtain a quotation through an online platform.
Reaching out to the manufacturer directly is a conventional and clear-cut approach. By initiating direct communication with the manufacturer, engineers can gather essential details such as product specifications, customization possibilities, and production lead times.The advantage of this approach is the ability to obtain immediate feedback and address special requests directly to the manufacturer. In addition, direct communication can help build a closer working relationship and help resolve potential technical and production issues.
On the flip side, the advent of the digital era has witnessed numerous suppliers offering convenient and swift quotation services via online platforms. Through these platforms, engineers can input product specifications and requirements, prompting the system to automatically generate corresponding quotes. This method streamlines the communication process and enhances options, allowing engineers to effortlessly compare prices and services from various suppliers.
Clearly defined product specifications are imperative for ensuring accurate quotes. This involves providing precise details such as size, material, number of layers, etc. Additionally, specifying mass production requirements and delivery lead times aids suppliers in organizing production plans and delivering more precise quotations.
When customization is required, engineers should articulate their needs for customized Rigid-Flex Packaging Substrate, enabling suppliers to furnish appropriate quotations. It is also crucial to comprehend any potential additional charges and services. Beyond the basic price, attention should be given to understanding whether there are extra fees and if the supplier offers supplementary services like technical support and after-sales assistance.
In summary, obtaining a precise quotation for Rigid-Flex Packaging Substrate is a pivotal step in ensuring project success. Engineers can opt to directly contact manufacturers or obtain quotes through online platforms based on project-specific needs. Simultaneously, highlighting product specifications, mass production requirements, and customization needs is essential for securing the most fitting quotation and providing foundational support for the seamless progression of the project.
What are the common problems with Rigid-Flex Packaging Substrate?
In what ways does Rigid-Flex Packaging Substrate outperform traditional circuit boards?
Rigid-Flex Packaging Substrate surpasses traditional circuit boards in terms of adaptability to complex shapes and spatial constraints. Its superior performance in reliability, stability, and size reduction makes it a preferred choice for modern electronic designs.
How is the manufacturing process of Rigid-Flex Packaging Substrate executed?
The manufacturing process involves a meticulous integration of rigid and flexible materials. The steps for producing the main board and base board are intricately designed to ensure the final product’s stability and reliability.
How can one obtain quotes for Rigid-Flex Packaging Substrate?
Obtaining quotes for Rigid-Flex Packaging Substrate can be done by directly contacting manufacturers or exploring online platforms. This ensures a comprehensive understanding of pricing considerations for making informed decisions.
What are some common issues associated with Rigid-Flex Packaging Substrate?
Common issues might include questions regarding the types of devices suitable for Rigid-Flex Packaging Substrate, its lifecycle, and potential challenges. Addressing these concerns helps in better comprehending the substrate’s practicalities.
What advantages does Rigid-Flex Packaging Substrate bring to the table?
Delve into the specific advantages Rigid-Flex Packaging Substrate offers over traditional rigid boards. How does it enhance adaptability, reliability, and stability in electronic devices?
Why opt for Rigid-Flex Packaging Substrate over other circuit boards?
Discover the distinctive features that make Rigid-Flex Packaging Substrate stand out in design. Why do more engineers choose it over conventional circuit boards?