RO4350B PCB manufacturing, Ro4350B PCB and other Rogers Series material PCBs Vendor. We produce multi-layer Rogers PCBs in mixed media materials from 4 to 30 layers.
In the field of modern electronics, Printed Circuit Boards (PCBs) play a vital role. They are one of the core components of electronic equipment, providing support and connection for the functions of various electronic equipment. Among many PCB types, RO4350B PCB is known for its excellent high-frequency performance and thermal stability. This article will delve into the manufacturing process of RO4350B PCB, every key step from design to finished product, and lead readers to fully understand the manufacturing process and application prospects of this special type of PCB.
What is RO4350B PCB?
RO4350B PCB (Printed Circuit Board) is a printed circuit board made of special materials with outstanding dielectric constant and low loss characteristics, making it an ideal choice for high-frequency applications. Its material is mainly composed of RO4350B substrate, which uses glass fiber reinforced polytetrafluoroethylene (PTFE) as the medium and has excellent high-frequency performance and thermal stability. RO4350B PCB is widely used in microwave communications, radar systems, satellite receivers and other fields, and its characteristics enable it to provide reliable circuit performance in high-frequency environments.
In the field of microwave communications, RO4350B PCB serves as an important part of the infrastructure and is used to manufacture high-performance microwave antennas, radio frequency amplifiers, frequency converters and other equipment. Its excellent dielectric properties and low loss ensure the stability and reliability of signals during transmission, providing important support for high-speed data transmission in communication systems.
Radar systems are another area where RO4350B PCBs are widely used. Radar systems need to process a large number of high-frequency signals and have extremely high requirements for signal accuracy and stability. The low dielectric loss and excellent thermal performance of RO4350B PCB make it a key component in radar systems, ensuring the accurate operation of radar systems in complex environments, including applications such as weather monitoring, flight navigation, and military defense.
In addition, RO4350B PCB is also widely used in satellite receivers. Satellite communication systems need to process high-frequency signals and ensure stable transmission, while also adapting to extreme working environments, such as high temperature, low temperature, and radiation. With its excellent high-frequency performance and reliability, RO4350B PCB provides high-quality signal processing and transmission solutions for satellite receivers, thereby achieving stable operation and data transmission of satellite communication systems.
Overall, RO4350B PCB’s excellent performance and wide range of applications make it an indispensable part of high-frequency electronic equipment. Its special materials and precision manufacturing processes ensure stability and reliability in high-frequency environments, providing strong support for the development of modern communications, radar and satellite technologies.
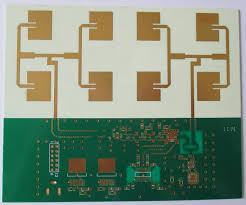
RO4350B PCB
How to design RO4350B PCB?
Designing the RO4350B PCB is a complex process involving multiple critical steps, requiring engineers to fully understand the circuit requirements and translate them into a physical layout for optimal performance and manufacturability. The following are the main steps for designing a RO4350B PCB:
First, designers need to accurately capture the circuit diagram. This includes analyzing circuit requirements, functional requirements, and performance specifications to ensure that the designed circuit board meets expected functionality and performance standards. With professional design software, designers can create circuit schematics and use them as the basis for their designs.
Secondly, carry out component layout. After determining the size and shape of the circuit board, designers need to place electronic components reasonably, including integrated circuits, resistors, capacitors, and connectors. The rationality of component layout directly affects the performance and stability of the circuit board, so it needs to be carefully considered.
Next is routing and layout. After placing all the components, the designer needs to draw connections on the circuit board to connect the various components and implement the circuit function. Through the layout of traces, designers can minimize signal interference and crosstalk on the circuit board and improve the anti-interference ability and stability of the circuit.
Finally, optimize space utilization and manufacturability. Designers need to consider board size, shape and layout to maximize available space and ensure the board can be produced smoothly during the manufacturing process. This includes taking into account ease of assembly and soldering, as well as rationally laying out the circuit board’s stack-up structure.
Through the above steps, designers can complete the design of RO4350B PCB and optimize circuit functions and performance. The quality and manufacturability of the design directly affect the performance and reliability of the final product, so designers are required to have extensive experience and expertise to ensure the quality and manufacturability of the design.
What is the manufacturing process of RO4350B PCB?
The manufacturing process of RO4350B PCB is a complex and precise process involving multiple critical steps, each of which is critical to the performance and reliability of the final product.
First, the first step in manufacturing a RO4350B PCB is substrate selection. The special dielectric properties and thermal stability requirements of RO4350B must be taken into consideration when selecting a substrate. Therefore, RO4350B sheets with excellent properties are usually chosen as the base material.
Next is the layer stacking stage. At this stage, multiple layers of substrates are brought together to form the complete PCB structure. Each layer contains specific circuit elements and conductive paths, so the correct layering is critical to the functionality of the circuit.
Copper processing is the next key step. At this stage, copper foil is attached to the surface of the substrate and the required conductive paths are formed by chemical or mechanical means. The processing quality of copper foil directly affects the conductive performance and stability of PCB.
This is followed by the drilling stage. At this stage, holes are drilled into the PCB using a mechanical drill to facilitate subsequent electrical connections. The precision and location of the drilled holes is critical to ensuring circuit continuity.
Plating is the next step, which enhances electrical conductivity and corrosion resistance by coating a thin metal film inside the drill hole or on the surface of the PCB. This step ensures long-term stability of PCB life and performance.
The last critical step is etching. At this stage, the unwanted portions of the copper foil are etched away from the PCB surface using a chemical solution, leaving the desired conductive paths. Precision and control of etching are key to ensuring a fully functional PCB.
These above steps combined form the RO4350B PCB manufacturing process. Each step must be executed with precision to ensure that the resulting PCB has the superior functionality and performance stability required to meet the requirements of high-frequency circuit design.
How much does a RO4350B PCB cost?
The cost of RO4350B PCB is a complex and variable issue that is influenced by many factors. First, size is a key factor. Larger PCB sizes require more substrate material and copper foil, and therefore cost more. Additionally, complexity is an important consideration. If a PCB requires more layers, complex wiring, or special processes, manufacturing costs will increase accordingly. Materials are also a factor in determining cost. The RO4350B substrate material itself is relatively expensive, but is necessary in some specific applications, such as high-frequency circuit design. Finally, quantity also has an impact on cost. Generally speaking, the cost of PCBs produced in large quantities will be relatively low because manufacturers can reduce the unit price by purchasing in bulk.
Therefore, understanding these cost drivers is critical to budgeting and optimizing production costs. During the design phase, engineers should strive to optimize PCB size and complexity to minimize cost. Choosing the right materials and suppliers is also crucial. In addition, by estimating the required quantity and negotiating bulk orders with the manufacturer, you can get a more competitive price. In summary, by comprehensively understanding and properly controlling these cost drivers, the cost of RO4350B PCB can be effectively managed and optimization of budget and production costs can be achieved.
What material is the RO4350B PCB made of?
The material composition of RO4350B PCB is the key to its superior performance and stability. It is mainly composed of various materials such as RO4350B substrate material, copper foil and solder film.
First, the RO4350B substrate material is the foundation of the RO4350B PCB. RO4350B is a special dielectric material with excellent high frequency characteristics and thermal stability. Its low loss and stable dielectric constant make it ideal for high-frequency circuit design. The excellent performance of RO4350B substrate material ensures the stability and reliability of PCB in high-frequency applications.
Secondly, copper foil is one of the key materials in PCBs and is used to form conductive paths. In a RO4350B PCB, copper foil is typically deposited precisely on the surface of the substrate to form the circuit connections. Copper’s good conductivity and workability make it one of the most commonly used conductive materials in PCBs. In RO4350B PCB, the high-quality selection of copper foil ensures the efficiency and stability of circuit transmission.
Finally, the solder film serves as insulation and protection in the RO4350B PCB. Solder film is applied to the PCB surface to cover and protect copper foil and other circuit components from environmental factors such as oxidation, moisture, and chemical corrosion. Solder film also provides a solderable surface to facilitate the installation and connection of electronic components. With proper selection and application of solder film, the RO4350B PCB can receive additional insulation protection, thereby increasing its reliability and durability.
In general, RO4350B PCB is mainly composed of RO4350B substrate material, copper foil, solder film and other materials. These advanced material technologies ensure RO4350B PCB’s superior performance and stability in high-frequency circuit applications, making it the preferred circuit board choice in many fields.
Who makes the RO4350B PCB?
Choosing a reliable supplier is crucial during the manufacturing process of RO4350B PCB. As a professional electronic equipment manufacturing company, we adhere to the principles of high quality and reliability to provide customers with excellent products and services. Therefore, we carry out the manufacturing of RO4350B PCB in-house to ensure product quality and controllable delivery time.
As an independent manufacturer, we have advanced production facilities and technical teams that can flexibly respond to customer needs and keep the production process efficient and sustainable. Our production process strictly follows international standards and industry best practices. From material procurement to production and manufacturing, every link is strictly controlled to ensure that product quality reaches the optimal level.
During the manufacturing process of RO4350B PCB, we pay attention to every detail, from material selection to production process, striving for excellence and striving to present the best products to customers. We use advanced production equipment and technology, coupled with a strict quality control system, to ensure that each RO4350B PCB meets customer requirements and standards.
In addition, we are committed to establishing long-term and stable cooperative relationships with customers, listening to their needs and feedback, and constantly optimizing products and services to meet changing market needs. Our goal is to become a trusted partner of our customers, providing them with the highest quality RO4350B PCB products and solutions.
All in all, as a manufacturer of RO4350B PCB, we are committed to providing customers with high-quality, reliable products and services through independent manufacturing and strict management, and working with customers to create a better future.
Five traits of great customer service
In the modern business environment, excellent customer service is one of the key factors for business success. Here are five qualities that make customer service outstanding:
Excellent customer service starts with prompt responses to customers. When customers have inquiries or concerns, responding promptly and effectively is the foundation for building customer trust and satisfaction. Whether it’s a phone call, email, or message on social media, responding to customers quickly and accurately will make them feel valued and increase their trust in your business.
Empathy is key to understanding and empathizing with your customers’ needs. In customer communication, being able to treat customers’ problems and needs with compassion and understanding can not only establish good interpersonal relationships, but also better grasp the real needs of customers and provide more considerate and effective solutions.
Reliability is one of the core qualities of customer service. Always keeping our promises and commitments to our customers is the cornerstone of building customer trust and loyalty. Whether it is providing products, services or solving problems, companies should ensure stability and reliability to ensure that customers can always get the expected value and experience.
Clear, transparent communication is key to building good customer relationships. During the service process, maintaining clear communication with customers, conveying important information in a timely manner, explaining complex issues, and ensuring customer understanding and acceptance can not only reduce misunderstandings and disputes, but also improve customer satisfaction and loyalty.
Customers will inevitably encounter problems and challenges when using products or services, and the ability to proactively solve problems is an important indicator of customer service levels. Enterprises should set up a dedicated customer support team to respond to customer feedback in a timely manner, actively find solutions, and ensure that problems are satisfactorily resolved to meet customer expectations and improve customer satisfaction.
To sum up, great customer service is not just a behavior, but a culture and attitude. Through a combination of responsiveness, empathy, reliability, communication and problem-solving skills, companies can win the trust and support of their customers, maintain a competitive advantage, and achieve sustained growth.
Frequently Asked Questions
How does the manufacturing process of RO4350B PCB differ from standard PCB fabrication?
The manufacturing process of RO4350B PCB involves specialized handling and processing techniques tailored to its unique material properties. This includes precise control of temperature, pressure, and chemical exposure to ensure optimal performance and reliability.
Can RO4350B PCBs be used in harsh environmental conditions?
Yes, RO4350B PCBs exhibit excellent thermal stability and mechanical strength, allowing them to withstand challenging environmental conditions such as high temperatures, humidity, and mechanical stress. This makes them suitable for aerospace, automotive, and military applications.
Are there any limitations to the design flexibility of RO4350B PCBs?
While RO4350B PCBs offer high performance and reliability, their material properties may impose certain limitations on design flexibility compared to standard PCB materials. Designers should consider factors such as substrate thickness, dielectric constant, and signal integrity requirements when designing with RO4350B.
What surface finishes are compatible with RO4350B PCBs?
RO4350B PCBs are compatible with a variety of surface finishes, including ENIG (Electroless Nickel Immersion Gold), HASL (Hot Air Solder Leveling), and OSP (Organic Solderability Preservatives). The choice of surface finish depends on factors such as assembly process compatibility, cost considerations, and environmental requirements.