RO4350B PCB | High frequency PCB Manufacturer, HDI Rogers 4350b PCB and FR4 Mixed media material PCB’s Vendor, We offer Rogers PCB from 2 layer to 30 layers.
In today’s rapidly evolving technology landscape, printed circuit boards (PCBs) are the backbone of nearly every electronic device. Among the many choices, RO4350B PCB stands out for its excellent performance and reliability. In this comprehensive guide, we’ll take an in-depth look at the RO4350B PCB, including its design, manufacturing, manufacturing process, cost considerations, materials, reputable manufacturers, and the essential qualities of great customer service. With this guide, you’ll learn how to maximize the potential of your RO4350B PCB to bring superior performance and reliability to your projects.
What is RO4350B PCB?
RO4350B PCB (Printed Circuit Board) is a high-frequency laminate designed using Rogers’ cutting-edge material technology and is widely used in a variety of demanding applications. This special PCB is world-renowned for its excellent electrical characteristics, thermal stability and signal integrity. In industries such as telecommunications, aerospace, and high-speed digital computing, RO4350B PCB is highly favored and widely used in the following areas:
In high-frequency communication equipment, RO4350B PCB is widely used in manufacturing antennas, microwave circuits, radio frequency modules and other components. Its excellent signal transmission characteristics make it an ideal choice for building high-performance communication systems.
In the aerospace field, RO4350B PCB is used to manufacture key components such as radar systems, navigation equipment, and communication systems. Its excellent thermal stability and reliability enable it to operate in extreme environmental conditions and meet the stringent requirements of aerospace applications.
In high-speed digital computing equipment, such as servers, network equipment and high-performance computers, RO4350B PCB is used to manufacture high-speed data transmission channels, radio frequency filters and other components. Its excellent signal integrity and low loss characteristics help ensure the stability and reliability of data transmission.
In short, RO4350B PCB is highly regarded for its excellent performance in high-frequency, high-speed, and high-performance applications. Whether in the fields of communications, aerospace or digital computing, RO4350B PCB plays a key role, providing stable and reliable circuit solutions for various complex applications.
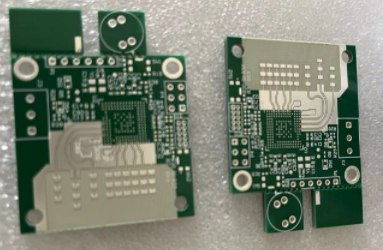
RO4350B PCB
How to design RO4350B PCB?
Designing the RO4350B PCB requires meticulous attention. Using software tools specifically targeted at high-frequency applications, engineers carefully design layout and routing to optimize signal integrity and minimize electromagnetic interference (EMI).
When designing the RO4350B PCB, engineers first need to have a deep understanding of the circuit’s requirements and characteristics. They carefully analyze key parameters such as signal frequency, speed and power consumption to determine the best design solution. For high-frequency applications, engineers usually choose specialized PCB design software, such as Altium Designer or Cadence Allegro. These software provide rich high-frequency characteristic models and analysis tools to help engineers more accurately predict and optimize circuit performance.
Before starting the actual design, engineers typically perform a schematic design, which converts the circuit diagram into a physical layout. They take into account the path length of the signal transmission, the width and spacing of the traces, and the placement of the components to minimize signal transmission delay and crosstalk. Additionally, engineers take care to maintain continuity of ground and power planes to minimize ground return and power supply noise.
After the layout design is completed, engineers begin wiring. In high-frequency applications, precise routing is critical because poor routing can lead to signal integrity and EMI issues. Engineers usually use special line structures such as microstrip lines or coaxial lines, and strictly control the length, bending and parallelism of the traces to minimize signal loss and interference.
After the wiring is completed, engineers perform signal integrity and electromagnetic compatibility analysis. They use simulation tools to perform time- and frequency-domain analysis of the circuit to verify that the design meets specification requirements and optimize possible problems. In addition, engineers will also conduct electromagnetic compatibility testing to ensure that the PCB design will not cause interference or be subject to external interference in the actual environment.
In general, designing the RO4350B PCB requires engineers to give full play to their professional knowledge and experience to ensure the optimization and reliability of circuit performance. By carefully designing the layout and routing, and utilizing professional software tools for simulation and analysis, engineers can achieve the best performance of the RO4350B PCB and meet the stringent requirements of high-frequency applications.
What is the manufacturing process of RO4350B PCB?
The manufacturing process of RO4350B PCB is a precise process that requires each step to be executed precisely to ensure the quality and reliability of the final product. The manufacturing process of RO4350B PCB will be introduced in detail below:
Material Selection: The first step in manufacturing RO4350B PCB is to select high-quality materials. RO4350B laminates are typically made from a glass fiber reinforced PTFE (polytetrafluoroethylene) substrate with excellent dielectric properties and thermal stability. During the material selection process, it is important to ensure that the materials comply with relevant industry standards and specifications.
Corrosion: Next, the material undergoes chemical etching. The purpose of this step is to form the desired line pattern by covering the pattern on the photosensitive adhesive on the surface of the board and then exposing it to UV light. Subsequently, the plate will be corroded by an acidic solution to remove the metal that is not protected by the photosensitive adhesive and form a circuit.
Drilling: After forming the circuit pattern, drilling is required. These holes are used for mounting components and connecting circuits. Drilling is usually done using a high-precision CNC drill machine to ensure the accuracy of the hole diameter and location.
Metallization: Once the drilling is complete, the surface of the board is metallized to allow the circuits to be connected. Chemical copper plating or electroplating copper is usually used to form a copper film on the surface of the board to fill holes and cover circuits.
Final Inspection: The final stage of the manufacturing process is to conduct final inspection. This includes a thorough inspection of the board for circuit integrity, aperture size, metallization quality and surface flatness. Only through strict quality control and inspection can we ensure that the performance and reliability of RO4350B PCB reaches the expected level.
In general, the manufacturing process of RO4350B PCB requires strict process control and a high degree of professional technology. Precise steps of material selection, etching, drilling, metallization and final inspection produce high-performance RO4350B PCBs that meet strict quality standards.
What steps are required to manufacture RO4350B PCB?
Manufacturing RO4350B PCB is a complex and sophisticated process that requires a series of precise steps and expertise to ensure that the final product meets high standards of quality requirements. Following are the main steps involved in manufacturing RO4350B PCB:
Material preparation: The first step in manufacturing RO4350B PCB is to prepare the required materials. This includes materials such as RO4350B high frequency laminate, copper foil and solder mask. These materials must undergo rigorous quality checks to ensure that they meet specifications and are free of any defects.
Engineering design: After the material preparation is completed, engineers will start designing the layout and routing of the PCB. This requires the use of specialized PCB design software to ensure that the layout of the PCB meets the design specifications and can operate normally in a high-frequency environment.
Graphical production: Once the design is completed, the PCB layout will be converted into a graphical file for production. These files include schematics, layouts, and laminates that will serve as the basis for manufacturing the RO4350B PCB.
Lithography: After the graphic file is ready, the next step is photolithography. During the photolithography process, the pattern of the PCB will be transferred to the photoresist layer, and through light and chemical treatment, the pattern will be transferred to the copper foil.
Etching: Next comes the etching process, where the unprotected copper foil is etched by a chemical solution, creating conductive paths for the PCB. This process requires a high degree of precision and control to ensure that the PCB’s circuit pattern is accurately replicated onto the board.
Drilling: Drilling is one of the key steps in manufacturing RO4350B PCB. In this step, engineers use a specialized drilling machine to drill holes in the PCB for mounting components and connecting wires.
Metallization: After drilling is completed, the PCB will be covered with a layer of metallization material, usually gold plating or spray plating. This layer of metallization improves the PCB’s electrical conductivity and protects it from environmental influences.
Final Inspection: The last step in manufacturing the RO4350B PCB is to conduct final inspection. During this step, the PCB will be inspected to ensure that it meets the design specifications and does not have any defects or damage. This includes testing the electrical performance of the PCB using advanced test equipment to ensure its quality and reliability.
Professional equipment and skilled technicians are crucial throughout the entire process of manufacturing RO4350B PCB. Only experienced engineers and operators can ensure that each step is performed correctly and the final product meets high quality standards. Therefore, it is crucial to choose experienced manufacturers and partners to ensure success in manufacturing RO4350B PCB.
What are the cost considerations?
Although RO4350B PCBs offer unparalleled performance, they are expensive. This is mainly due to the combined influence of multiple factors. First, material costs are an important part of the overall cost. RO4350B PCB uses high-performance materials such as RO4350B laminate and high-quality copper foil. Not only are these materials more expensive, but the supply chain is scarce, further driving up the cost. Secondly, the design complexity of RO4350B PCB will also affect the cost. High-frequency applications often require complex layouts and tight tolerances, which increases engineering and production costs during manufacturing. In addition, the scale of production is also a key factor in cost. Small batch production often results in an increased spread of fixed costs per unit of product, resulting in a higher unit price. However, although RO4350B PCB is expensive, the cost of investing in it is reasonable. This is because the superior quality and reliability offered by RO4350B PCB more than make up for its high cost. In areas with extremely high performance and reliability requirements, such as aerospace and communications, the investment in RO4350B PCB is worthwhile. Its excellent signal integrity, thermal stability and anti-interference capabilities can ensure the stable operation of the system and reduce losses and maintenance costs caused by circuit failures. Therefore, despite the high price, investment in RO4350B PCB is a guarantee of product quality and reliability, and is a reasonable choice to ensure long-term stable operation of the system.
What materials is the RO4350B PCB made of?
The material selection of RO4350B PCB is crucial, they directly affect the performance, stability and reliability of the PCB. RO4350B PCB is composed of several key materials, each carefully selected to ensure optimal performance in various application scenarios.
The first is RO4350B laminate, which is the core material of RO4350B PCB. RO4350B laminate adopts Rogers’ leading technology and has excellent high frequency performance and thermal stability. Its low dielectric constant and low dissipation factor make it perform well in high-frequency circuits, while its high glass transition temperature ensures its stability in high-temperature environments.
Next is copper foil, which is used to form the conductive layer of the PCB. Copper foil is a high-quality conductive material with good electrical and thermal conductivity, and can effectively transmit current and dissipate heat. In RO4350B PCB, the copper foil is specially treated to ensure good adhesion and stability to the RO4350B laminate, thereby improving the performance of the entire PCB.
Finally, there is the solder mask, which is used to cover the PCB surface to prevent short circuits or other undesirable situations during soldering. Solder mask is usually made of epoxy resin, which has good heat resistance and corrosion resistance and can effectively protect the surface of the PCB during the soldering process. In the RO4350B PCB, select a solder mask suitable for high frequency applications to ensure signal integrity is not negatively affected.
In general, the material selection of RO4350B PCB has been strictly screened and tested to ensure that each material has excellent electrical properties, thermal conductivity and durability. The excellent properties of these materials enable RO4350B PCB to perform well in a variety of harsh environments and high-frequency applications, making it the first choice for many leading industries.
Who is RO4350B PCB manufacturer?
In today’s technology industry, the choice of RO4350B PCB manufacturer is critical to the success of your project. Among many manufacturers, our company is proud to provide high-quality products and excellent services of RO4350B PCB.
As a leading RO4350B PCB manufacturer, our company is committed to providing customers with the most advanced technology and the highest quality products. We have advanced production equipment and technical teams that can meet the needs of various complex projects. Whether in telecommunications, medical, aerospace or high-speed digital, we provide the best solutions.
Our supply chain management team is well versed in industry standards and has established close cooperative relationships with outstanding material suppliers around the world to ensure that our RO4350B PCB always uses the highest quality materials and has excellent performance and reliability.
In our factory, strict quality control processes ensure that the quality of each RO4350B PCB meets international standards. From the receipt of raw materials to the delivery of final products, we strictly control every link to ensure product stability and reliability.
Our customer service team focuses on communication and cooperation with customers, providing personalized solutions and professional advice. No matter what challenges our customers face, we will respond proactively and do our best to provide our customers with the best support and service.
Therefore, if you are looking for a reliable RO4350B PCB manufacturer, our company will be your best choice. We will wholeheartedly provide you with high-quality products, excellent services and continuous support to help you achieve project success and development.
What are the essential qualities of great customer service?
Excellent customer service is a key element of success in any industry, and RO4350B PCB manufacturer builds its corporate culture on this. They know that in addition to excellent product quality and technical strength, good communication and relationships with customers are equally important. Here are five key attributes RO4350B PCB manufacturers have when it comes to providing customer service:
Professionalism: RO4350B PCB manufacturer provides customers with professional and authoritative advice and support based on professional knowledge and experience. No matter how complex the problem their customers face, they provide reliable solutions and ensure customers have a clear understanding of their products and services.
Timely response: RO4350B PCB manufacturers focus on responding to customer needs and questions in a timely manner. They have established efficient communication channels to ensure that customers’ questions can be answered quickly and the required support and assistance are provided in a timely manner to maintain a good cooperative relationship.
Personalized Care: RO4350B PCB manufacturers understand that each customer’s needs and situation are unique, so they are committed to providing personalized care and service. Regardless of the size of the customer, they will develop corresponding solutions based on the customer’s specific situation to ensure that the customer’s needs are met to the greatest extent.
Problem-solving capabilities: RO4350B PCB manufacturers take it as their mission to solve problems. Whether the problems encountered by customers are related to product quality, delivery cycle or technical support, they will go all out to actively find solutions and ensure that the problems are solved in a timely manner to protect the interests and satisfaction of customers.
Continuous Improvement: RO4350B PCB manufacturers continually strive to improve their customer service levels. They actively collect customer feedback, listen to their opinions and suggestions, and incorporate them into the company’s development plan. Through continuous improvement, they continue to improve the quality and efficiency of customer service to better meet customer needs.
In general, RO4350B PCB manufacturer is customer-centric and always adheres to the five key characteristics of professionalism, timely response, personalized care, problem-solving capabilities and continuous improvement to provide customers with high-quality service and support. They know that customer satisfaction is the key to business success, so they constantly strive to improve customer service levels, grow together with customers, and create a better future.
FAQs
What is the difference between RO4350B and other PCB materials?
RO4350B PCB uses Rogers’ proprietary high-frequency laminate material, which has excellent electrical characteristics and signal transmission performance. In comparison, other common PCB materials may not perform well in high-frequency environments, causing signal attenuation or crosstalk.
What are the advantages of using RO4350B PCB in high frequency applications?
RO4350B PCB features low loss, low dielectric constant and stable dielectric properties, making it suitable for high frequency and microwave applications. Its excellent signal integrity and reliability make it an ideal choice for communications, radar, satellite and radio frequency equipment.
How to optimize the design of RO4350B PCB to reduce costs?
The key to optimizing the RO4350B PCB design to reduce costs is to rationally utilize the PCB space, reduce the number of board layers, minimize material waste, and optimize wiring. In addition, choosing an experienced design team and the right manufacturer can also help reduce costs.
What certifications should you pay attention to when choosing a RO4350B PCB manufacturer?
When choosing a RO4350B PCB manufacturer, you should pay attention to whether it has ISO 9001 quality management certification and certification to relevant PCB manufacturing standards such as IPC-A-600 and IPC-6012. These certifications ensure that manufacturers meet industry standards and provide high-quality products and services.
How do RO4350B PCB manufacturers ensure product quality and reliability?
RO4350B PCB manufacturers ensure product quality and reliability through strict quality control processes and advanced testing equipment. Every aspect from raw material procurement to production process is strictly monitored and inspected to ensure that RO4350B PCB meets the highest standards.