Rogers 4003C PCB manufacturing. High frequency materials Ro4003C PCB and Rogers Series material PCBs Vendor, We offer HDI Rogers Mixed media pressing PCBs from 4 layer to 30 layers, Ultra-small spacing and Minimum trace with 1.2mil.
What is Rogers 4003C PCB?
Rogers 4003C PCB, referred to as Rogers 4003C printed circuit board, is a high-performance printed circuit board known for its excellent electrical characteristics and reliability. This type of PCB is suitable for many high-frequency and high-speed applications, such as radio frequency (RF)/microwave circuits, high-speed digital designs, etc. It has been widely used in aerospace, communications, medical electronics and other fields because of its outstanding performance.
The material of Rogers 4003C PCB is one of its keys. It is made of Rogers’ special 4003C laminate material. This material is a glass fiber reinforced hydrocarbon/ceramic composite with excellent dielectric properties and thermal stability. Rogers 4003C has a dielectric constant of 3.38 ± 0.05 at 10 GHz, making it ideal for high frequency applications. In addition, the material also has excellent mechanical strength and chemical stability, and can maintain stable performance in various harsh environments.
Because of its superior performance and reliability, Rogers 4003C PCB requires special attention during the design and manufacturing process. Designers need to use professional software, such as Altium Designer or Cadence Allegro, to ensure that the PCB design complies with high-frequency design principles and maximizes signal integrity and reduction of signal loss. During the manufacturing process, various steps, including substrate preparation, copper foil patterning, etching, drilling and surface treatment, need to be strictly controlled to ensure that the final product meets stringent performance requirements.
Overall, Rogers 4003C PCB is a high-performance printed circuit board based on Rogers 4003C laminate material with excellent electrical properties, thermal stability and mechanical strength. It plays an important role in various high-frequency and high-speed applications and plays an integral role in modern electronics.
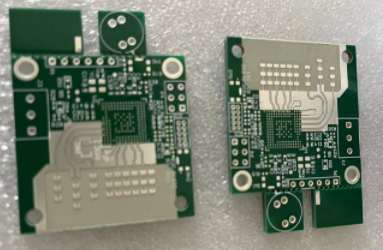
Rogers 4003C PCB
How to design PCB using Rogers 4003C?
Designing a PCB with the Rogers 4003C is a delicate and complex process that requires consideration of several key factors to ensure the performance and reliability of the final product. First, designers need to have a deep understanding of the electrical and material properties of Rogers 4003C. Rogers 4003C is a glass fiber reinforced hydrocarbon/ceramic material with excellent dielectric properties and stability for high frequency and high speed applications. Designers should be familiar with parameters such as dielectric constant, loss factor, and dielectric thickness to ensure design accuracy.
Secondly, designing a PCB using Rogers 4003C requires special attention to signal integrity. High-frequency circuits have extremely high requirements for signal integrity, so impedance matching, signal transmission paths and signal losses need to be strictly controlled during the PCB layout and wiring process. Through reasonable layout and wiring design, signal distortion and crosstalk can be minimized to ensure the stability and reliability of signal transmission.
In addition to this, designers should consider factors such as thermal management and mechanical strength. Rogers 4003C has a low thermal expansion coefficient and good thermal conductivity, but in high-power applications you still need to pay attention to the heat dissipation design to prevent circuit components from overheating. At the same time, considering that PCBs may be subject to vibration and shock in practical applications, designers also need to ensure that PCBs have sufficient mechanical strength and stability to prevent components from falling off or breaking.
In terms of software, designing PCBs using Rogers 4003C usually requires the use of professional PCB design software, such as Altium Designer, Cadence Allegro or Mentor Graphics PADS. These softwares provide a wealth of design tools and functions that can help designers achieve complex layout, wiring and simulation. They also support the integration of Rogers 4003C material library, making the design process more efficient and accurate.
To sum up, designing a PCB using Rogers 4003C requires comprehensive consideration of electrical, thermal and mechanical factors, and the use of professional design software to achieve design goals. Only with an in-depth understanding of the characteristics and requirements of Rogers 4003C can designers design PCB products with excellent performance, reliability and stability.
What is the manufacturing process of Rogers 4003C PCB?
The manufacturing process of Rogers 4003C PCB is a complex and precise process that requires multiple critical steps to ensure the quality and performance of the final product. Below we will detail the main steps in manufacturing Rogers 4003C PCB and how they ensure the quality and performance of the PCB.
The first step in manufacturing Rogers 4003C PCB is to prepare raw materials, which mainly include Rogers 4003C laminate, copper foil and other necessary materials. These raw materials must meet strict quality standards and be handled properly throughout the manufacturing process to ensure the consistency and reliability of the final product.
During the lamination process, Rogers 4003C laminates are stacked with copper foil layers as per the design requirements. Then, the stacked materials are fed into a high-temperature and high-pressure laminator, where they are heated and compacted at preset temperatures and pressures, thereby firmly bonding the laminate and copper foil.
In the patterning process, the designed circuit pattern is transferred to the copper foil layer on the surface of the laminate by using photolithography techniques and chemical etching. The key to this step is to ensure the accuracy and clarity of the pattern to ensure the electrical performance of the PCB.
After patterning is complete, holes are drilled into the PCB surface in order to mount electronic components and connect wires between different layers. The drilled surface is then plated with a thin layer of copper to enhance connectivity and conductivity.
During every manufacturing step, there are strict quality controls and performance testing to ensure the PCB meets design specifications and industry standards. This may include using X-rays to check the uniformity of board lamination, using automated optical inspection systems to check patterning accuracy, and performing electrical testing to verify circuit connectivity and performance.
Through these critical steps and strict quality control measures, the process of manufacturing Rogers 4003C PCB not only guarantees the reliability and stability of the PCB, but also ensures its superior performance in high-frequency and high-speed applications.
What are the cost considerations for using Rogers 4003C PCB?
Using Rogers 4003C PCB as a printed circuit board of choice requires careful consideration of cost factors. First of all, Rogers 4003C is a high-performance special material, which is more expensive than traditional FR-4 materials. This is because Rogers 4003C has excellent electrical performance and thermal stability and is suitable for high-frequency and high-speed applications, so its raw material cost is higher.
Secondly, designing and manufacturing Rogers 4003C PCB requires more technology and craftsmanship. High-frequency designs require stricter layout and routing rules to ensure signal integrity and minimal transmission loss. During the manufacturing process, the use of high-precision equipment and processes to ensure the quality and performance of PCBs will also increase costs.
In addition, the cost of Rogers 4003C PCB is also affected by market supply and demand. Due to its widespread demand in specific application areas such as aerospace, communications, and medical, suppliers usually charge a higher premium for Rogers 4003C PCB. Therefore, costs may fluctuate due to changes in market demand and supply.
The cost of Rogers 4003C PCB will usually be higher compared to other materials. However, for specific high-frequency and high-speed applications, choosing Rogers 4003C PCB may be a more economical choice because it can provide more stable and reliable performance, thereby reducing the cost of later maintenance and repair.
In short, choosing to use Rogers 4003C PCB needs to take into account its high performance characteristics and relatively high cost. When conducting a cost-benefit analysis, the benefits need to be weighed against the costs to ensure that the final design and manufacturing choices meet the needs of the project and remain economically viable.
What material is the Rogers 4003C PCB made of?
As a high-performance printed circuit board, Rogers 4003C PCB uses specific materials during its manufacturing process to ensure its excellent electrical performance and stability. The main materials include Rogers 4003C laminate, copper foil and pad cover. Let’s take a closer look at the characteristics of these materials:
Rogers 4003C is a glass fiber reinforced hydrogen carbon/ceramic material with excellent dielectric properties and stability. Its introduction
The electrical constant is 3.38 ± 0.05 at 10 GHz, making it ideal for high frequency applications. Compared with conventional FR-4 materials, Rogers 4003C has lower loss and better signal fidelity, making it suitable for fields such as RF/microwave circuits and high-speed digital design.
Copper foil is used to form wire paths on circuit boards, providing electrical connections and signal transmission. Rogers 4003C PCB usually uses high-purity copper foil to ensure good conductivity and stability. The thickness and coverage area of the copper foil are precisely controlled based on the design requirements to meet the performance requirements of the specific application.
Pad overlays are used to protect the soldering areas of the circuit board and provide additional mechanical support and corrosion protection. For Rogers 4003C PCB, a high temperature resistant and corrosion resistant pad covering layer is usually used to ensure the stability and reliability of the soldering connection.
Rogers 4003C laminate has excellent dielectric properties and thermal stability for high frequency and high speed applications. Its low loss and high signal fidelity make it the material of choice in areas such as wireless communications, satellite systems and radio frequency radar.
Copper foil provides good electrical and thermal conductivity, ensuring the stability and performance of the circuit. Its high purity and precisely controlled thickness allow it to perform well in high-frequency environments.
The pad overlay provides effective protection and mechanical support to prevent damage to the circuit board from environmental factors and mechanical stress. Its high temperature resistance and corrosion resistance ensure the reliability and long-term stability of welded connections.
Taken together, the material selection and characteristics of Rogers 4003C PCB make it the first choice for many critical applications, providing a solid foundation for the performance and reliability of modern electronic equipment.
Who is manufacturing the Rogers 4003C PCB?
In the industry of manufacturing Rogers 4003C PCB, supplier selection is crucial. Many leading PCB manufacturing companies offer Rogers 4003C PCBs, but in this market, a few companies stand out, providing customers with superior service and product quality.
As a leading PCB manufacturer, our company is committed to producing high-quality Rogers 4003C PCB to meet the various needs of our customers. We have advanced equipment and technology, as well as an experienced team, to stand out in the field of PCB manufacturing.
First, our company focuses on quality. We employ strict quality control measures to ensure that every Rogers 4003C PCB meets the highest quality standards. From the selection of raw materials to the monitoring of the production process, we always put quality first.
Secondly, we offer flexible production capabilities. Whether our customers require small batches or large-scale production, we can meet their needs. We have flexible production lines and precision craftsmanship to deliver high-quality Rogers 4003C PCBs in a timely manner.
Additionally, we focus on customer service. Our team consists of experienced professionals capable of providing customers with a full range of technical support and solutions. Adhering to the principle of customer first, we strive to meet the needs of our customers and ensure that they receive satisfactory service throughout the entire cooperation process.
In addition, we are committed to continuous innovation and improvement. We work closely with leading technology partners in the industry to keep pace with technological developments and continuously improve our production processes and product performance to meet the changing needs of our customers.
To sum up, as a leading PCB manufacturer, our company has rich experience and technical advantages in manufacturing Rogers 4003C PCB. We are committed to providing customers with high-quality products and excellent services, and working with customers to create a better future.
What are 5 qualities of a good customer service?
Excellent customer service is of the utmost importance to Rogers 4003C PCB Manufacturing Company. Here are the key attributes to ensure customers receive the best experience and support:
Timely response and communication: Ability to respond and resolve customer inquiries, needs or problems in a timely manner and maintain effective communication channels. Prompt responses to emails, phone calls, and online messages, as well as regular order status updates, are key to building customer trust and satisfaction.
Professional knowledge and technical support: With rich industry knowledge and technical expertise, we can provide accurate and comprehensive consultation and support on the design, manufacturing and application of Rogers 4003C PCB. Understanding customers’ needs and providing customized recommendations based on their specific application scenarios helps build long-term relationships.
Personalization and flexibility: Able to flexibly meet customers’ specific needs and provide customized solutions. Understand the client’s project requirements and budget constraints and provide diverse options to ensure the best match and maximize client value.
Problem-solving capabilities and after-sales service: Able to quickly and effectively provide solutions to problems or challenges that customers may encounter, and provide ongoing after-sales support. Remain patient and professional when handling complaints and issues to ensure customer satisfaction with service quality and resolution.
Continuous improvement and customer feedback: Actively listen to customer feedback and suggestions, and continuously improve service quality and product performance. Establish a feedback mechanism to regularly collect and analyze customer opinions in order to promptly adjust business processes and improve service levels, and grow and succeed together with customers.
By possessing the above key attributes, Rogers 4003C PCB Manufacturing Company can establish good customer relationships, win customer trust and reputation, and achieve long-term stable business growth and market competitive advantages.
Frequently Asked Questions
What are the key steps in the process of manufacturing Rogers 4003C PCB?
The process of manufacturing Rogers 4003C PCB includes critical steps such as substrate preparation, copper paving, etching, drilling and surface treatment. Each step requires strict control and precise operation to ensure the quality and performance of the final product.
In which industries is Rogers 4003C PCB widely used?
Rogers 4003C PCB is widely used in wireless communications, aerospace, medical equipment, radar systems and high-speed digital electronics. Its outstanding properties make it the material of choice for a variety of high-frequency and high-speed applications.
How to choose the right Rogers 4003C PCB manufacturer?
Choosing the right Rogers 4003C PCB manufacturer requires considering its level of expertise, manufacturing capabilities, quality assurance, and customer service. Leading manufacturers usually have extensive experience and advanced equipment, able to meet the needs of various projects and provide excellent technical support.
What is the life cycle of Rogers 4003C PCB?
Rogers 4003C PCB has a long life cycle and can usually meet the long-term needs of the project. Its excellent performance and stable material properties make it widely used in different industries, and it has high reliability and durability.