Rogers Cavity PCB manufacturing. Rogers Mixed medium Cavity PCBs and Rogers HDI PCB Vendor. we offer rogers Cavity PCBs from 4 layer to 50 layers. the PCB can de design with microtrace and small gap.
In today’s modern electronics world, Rogers Cavity PCBs are the cornerstone of advanced circuits due to their superior performance and reliability. This specialized printed circuit board plays a vital role in high frequency applications. In this comprehensive guide, we’ll take a deep dive into the manufacturing complexities of Rogers Cavity PCBs, exploring the details of the design process, manufacturing techniques, material selection, and more.
What is Rogers Cavity PCB?
Rogers Cavity PCB, also known as Rogers High Frequency PCB, is a special circuit board designed for high frequency applications. Their unique structure includes a dielectric material encapsulated inside the board layer, creating a cavity that helps control impedance and reduce electromagnetic interference. This unique design allows Rogers Cavity PCB to perform well in high-frequency electronic equipment, such as radar systems, wireless communication equipment, and satellite communication systems.
In traditional PCB, the circuit board usually consists of conductor layers, insulation layers and components. Rogers Cavity PCB uses a special structure in which the gaps between conductor layers are filled with high-performance dielectric materials to form one or more cavities. The presence of these cavities changes the electrical properties of the board, helping to optimize signal transmission and improve the board’s immunity to interference.
A significant advantage is that Rogers Cavity PCB can effectively control impedance, which is crucial for high frequency circuits. Impedance control ensures that signals remain stable as they travel across the circuit board, minimizing signal loss and distortion. In addition, the cavity structure can also reduce electromagnetic radiation and interference, improving the reliability and stability of the circuit board.
In practical applications, Rogers Cavity PCB is widely used in various high-frequency electronic equipment, including but not limited to wireless communication base stations, antenna systems, radio frequency amplifiers and microwave equipment. Its superior performance and stability make it the first choice in many industries, especially for applications that require extremely high signal quality and stability, such as satellite communications and aerospace. Therefore, Rogers Cavity PCB plays an indispensable role in modern high-frequency electronic technology, providing a solid foundation for the development and innovation of the electronics industry.
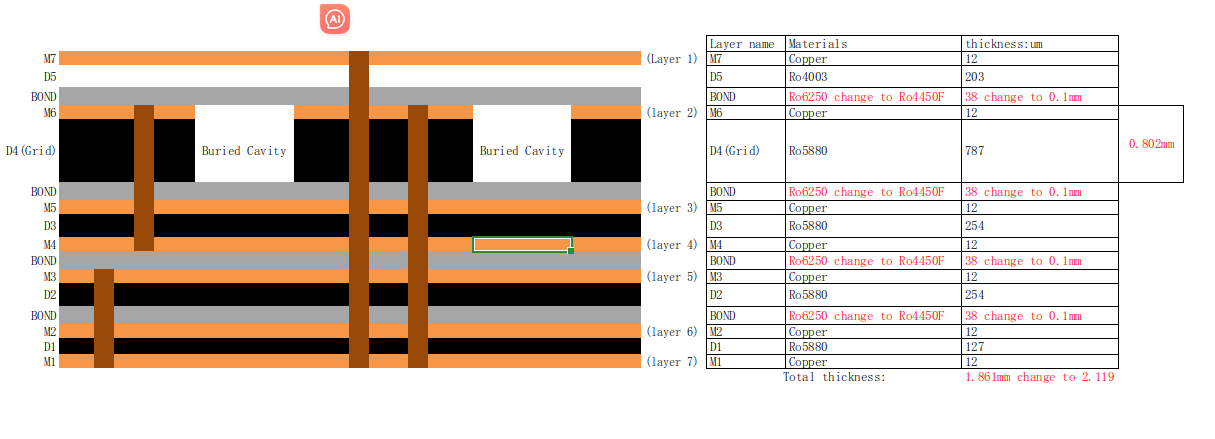
Rogers Cavity PCB
How to design Rogers Cavity PCB?
Designing Rogers Cavity PCB is a complex and critical task that requires engineers to have in-depth knowledge of high-frequency circuits as well as superb technical skills. During this process, engineers need to follow a rigorous series of steps to ensure that the final product meets the expected performance standards.
First of all, designing Rogers Cavity PCB requires extremely meticulous attention. Engineers must have a deep understanding of high frequency principles and understand how electromagnetic waves behave in circuit boards. This in-depth understanding is fundamental in the design process and provides support for effectively addressing potential electromagnetic interference and signal integrity issues.
Second, engineers use advanced PCB design software to lay out circuit traces, vias, and component locations. These software offer a rich set of features that allow engineers to perform precise layout and optimization during the design process. By cleverly arranging circuit components and connections, engineers can minimize signal path length and electromagnetic coupling, thereby improving overall circuit performance.
At the same time, engineers also need to focus on optimizing signal integrity. This means ensuring that the signal is not interfered with or distorted as it travels throughout the circuit board. To achieve this, engineers need to carefully consider the width, spacing, and layer spacing of signal traces, as well as the placement of nearby components and conductors. Through reasonable design and layout, signal attenuation and distortion can be minimized, thereby ensuring the stability and reliability of the circuit.
Finally, engineers also need to reduce electromagnetic coupling as much as possible. In high-frequency circuits, electromagnetic coupling can cause signal interference and performance degradation. To minimize this effect, engineers usually take a series of measures, such as using appropriate interlayer insulation materials, increasing the density of the ground layer and increasing the number of shielding layers. Through these measures, engineers can effectively reduce the impact of electromagnetic coupling and improve the performance and reliability of the overall circuit.
To sum up, designing Rogers Cavity PCB requires engineers to have in-depth knowledge of high-frequency circuits and superb technical skills. By using advanced PCB design software and following strict design principles, engineers can effectively optimize the performance and reliability of circuits to achieve desired design goals.
What is the manufacturing process of Rogers Cavity PCB?
The manufacturing process of Rogers Cavity PCBs involves a series of critical steps to ensure optimal performance and reliability in high frequency applications. The process begins with the preparation of the substrate material and proceeds through lamination and etching of the circuit pattern, with each stage requiring a high degree of precision and expertise. Let’s take a closer look at the Rogers Cavity PCB manufacturing process:
Substrate Material Preparation: The first step in manufacturing Rogers Cavity PCB is to prepare the substrate material. At this stage, choosing a high-quality substrate material is crucial as it will directly affect the performance and stability of the PCB. Commonly used materials include high-performance laminates produced by Rogers Corporation, such as the RO4000 series and RO3000 series, which have low dielectric loss and stable properties and are suitable for high-frequency circuit applications.
Lamination: After the substrate material is prepared, the next step is lamination. Lamination is the process of stacking multiple layers of substrate material together and using heat and pressure to bond them into a single unit. In the manufacturing of Rogers Cavity PCBs, the lamination process is crucial as it determines the structure and stability of the PCB.
Circuit pattern etching: Once the lamination of the substrate material is completed, the next step is the etching of the circuit pattern. This step uses chemical etching or laser etching technology to etch the designed circuit pattern onto the surface of the PCB. In the manufacturing of Rogers Cavity PCBs, the etching process must be precisely controlled to ensure the quality and accuracy of circuit traces.
Controlling impedance: Controlling impedance is a crucial part of the entire manufacturing process. Rogers Cavity PCBs are often used in high frequency applications, so the accuracy of the impedance is critical to maintaining signal integrity. Specialized equipment and techniques are used during the manufacturing process to ensure tight tolerances and precise control of impedance.
Quality Control: Finally, quality control is one of the critical steps in the Rogers Cavity PCB manufacturing process. At each stage, strict inspection and testing are required to ensure that the quality of the PCB meets standards. This includes using advanced test equipment to verify circuit trace connectivity and inspect PCB appearance and dimensions.
To sum up, the manufacturing process of Rogers Cavity PCB involves multiple key steps, each of which requires a high degree of expertise and precise control. Through careful manufacturing and quality control, Rogers Cavity PCBs are able to provide superior performance and reliability for a variety of high-frequency circuit applications.
How are Rogers Cavity PCBs manufactured?
Manufacturing Rogers Cavity PCBs requires advanced technology and skilled craftsmanship to ensure high performance and reliability of the final product. In this process, experienced technicians play a key role. They are proficient in every aspect of the PCB manufacturing process and strictly control every detail.
First, the manufacturing process starts with preparing the substrate material. Choosing a high-quality substrate material is critical to the performance of the final product. Once the material is ready, engineers will cut the panels according to the design requirements and ensure that the required dimensional accuracy is met.
Next comes the drilling and copper plating stage. At this stage, precision drilling equipment is used to drill holes into the board for mounting components and connecting circuits. Copper plating coats a conductive layer on the drilled surface to ensure circuit connectivity and stability.
This is followed by welding capping and surface treatment. The application of a solder cap layer is critical to ensure the robustness of the solder and protect the circuit from environmental influences. Precision surface treatment technology is used to ensure the flatness and cleanliness of the PCB surface, thereby improving the precise mounting and soldering quality of components.
Throughout the manufacturing process, strict quality control measures are implemented to ensure products meet specifications. Verification of dimensional accuracy is performed through the use of high-precision measuring tools and equipment. Signal integrity checks are performed through the use of professional testing equipment to ensure the stability and performance of the circuit under high-frequency conditions. In addition, verification of overall functionality is performed through rigorous testing and inspection of the finished PCB to ensure it meets the intended operating requirements.
Therefore, manufacturing Rogers Cavity PCB requires precision technology and highly specialized workmanship to ensure the highest level of product quality and performance. Experienced technicians play a vital role in the manufacturing process, and their technical knowledge and skills ensure the smooth progress of each production link, resulting in high-quality Rogers Cavity PCB products.
How much does a Rogers Cavity PCB cost?
Rogers Cavity PCBs are known for their superior performance and reliability, however, they often come with a higher cost compared to traditional PCBs. This cost difference is primarily due to several key factors, including material selection, board complexity, and manufacturing quantity.
First, material selection plays a vital role in the cost of Rogers Cavity PCBs. High-performance laminates from suppliers such as Rogers Corporation are relatively cost-effective because of their excellent electrical properties and stability. In addition, as performance indicators improve and specific application requirements increase, customers may choose higher-grade materials, further increasing costs.
Secondly, board complexity is also an important factor affecting cost. Rogers Cavity PCBs are typically designed for high frequency applications and therefore may require more complex routing and higher levels of manufacturing techniques. This complexity increases manufacturing costs and can result in longer production cycles.
Finally, the impact of manufacturing quantity on costs cannot be ignored. Low-volume production typically results in increased costs per unit because fixed costs need to be amortized over fewer volumes of output. In contrast, large-scale production often allows for higher efficiencies and lower unit costs.
However, despite the higher cost of Rogers Cavity PCBs, investments in their technology often bring significant returns. First, superior signal integrity and stability ensure reliable and consistent system performance. Secondly, high-quality materials and manufacturing processes can increase the life of the product and reduce maintenance costs and failure rates.
So while the initial investment may be higher, the long-term benefits of Rogers Cavity technology often far outweigh the costs. For applications that require superior performance and reliability, choosing Rogers Cavity PCB is often a wise choice.
The cost of Rogers Cavity PCBs is affected by several factors, including material selection, board complexity and manufacturing quantity. Although the initial investment is higher, investments in this technology often yield significant returns in terms of signal integrity, reliability and product longevity. Therefore, choosing Rogers Cavity PCB is often a wise decision for applications requiring high performance and reliability.
What materials are used in Rogers Cavity PCB?
In Rogers Cavity PCB manufacturing, material selection is crucial as it directly affects the performance and stability of the circuit board. Rogers Cavity PCB uses a range of specialized materials that perform well in high-frequency environments, ensuring reliable operation and excellent performance of the circuit.
Among them, the most common substrate materials include high-performance laminates from Rogers Company, mainly including RO4000 series and RO3000 series. RO4000 series is a special composite material with low dielectric loss and excellent electrical properties, suitable for high frequency applications. They are designed to maintain stable dielectric properties over a wide frequency band, ensuring accuracy and stability of signal transmission. In addition, RO3000 series laminates are also known for their excellent performance and stability. These materials have excellent dielectric properties and thermal stability, making them ideal for high-frequency circuit applications.
Manufacturers of Rogers Cavity PCBs typically select the appropriate materials based on specific application requirements. In addition to substrate materials, other auxiliary materials are also used, such as conductive copper foil and high-temperature resistant adhesives. These materials have been carefully selected to maximize the board’s performance and reliability.
Overall, Rogers Cavity PCB utilizes specially designed materials that perform well in high frequency environments. Rogers’ RO4000 series and RO3000 series laminates are the most representative materials. With their low dielectric loss and stable performance, they have become the preferred material for high-frequency circuit applications. By selecting the right materials, manufacturers can ensure Rogers Cavity PCBs achieve superior performance and reliability in a variety of harsh environmental conditions.
Who makes Rogers Cavity PCBs?
In the world of Rogers Cavity PCB manufacturing, manufacturer selection is crucial. Some of the renowned manufacturers specialize in Rogers Cavity PCB manufacturing and provide superior solutions to the market with their expertise and advanced technology. These manufacturers are highly recognized in the industry and have become the preferred partners for many businesses for their commitment to innovation, quality and customer satisfaction.
As a company, we strive to be the leader in Rogers Cavity PCB manufacturing. We have rich experience and technical strength to meet our customers’ needs for high-performance PCBs. We aim to continuously innovate and improve product quality, always adhere to the concept of customer first, and strive to provide customers with the best solutions.
By using advanced manufacturing processes and strict quality control systems, we ensure that every Rogers Cavity PCB meets the highest standards. Our team is composed of experienced professionals with extensive industry knowledge and technical expertise, able to provide customers with a full range of technical support and services.
At the same time, we continue to invest in technological innovation and equipment updates to ensure that we remain at the forefront of the industry. We have established long-term and stable cooperative relationships with our customers and jointly promote the development and progress of Rogers Cavity PCB manufacturing technology.
As a Rogers Cavity PCB manufacturer, we are committed to providing our customers with excellent products and services to meet their growing needs. Our goal is to become the trusted and preferred partner of our customers, to achieve win-win development and create a better future together.
What are the key attributes of great customer service?
In Rogers Cavity PCB manufacturing, providing excellent customer service is critical to the company’s success. Good customer service not only builds brand reputation but also drives customer satisfaction and business growth. The following are key customer service attributes in this area:
Clear communication: Clear and timely communication with customers is the foundation of a good relationship. Manufacturers should ensure that they maintain open lines of communication with customers and promptly respond to emails, phone calls and other inquiries to meet customer needs and resolve issues.
Responsiveness to customer needs: Manufacturers should actively listen to customer needs and opinions and take appropriate actions to meet those needs. Handle customer questions and complaints in a timely manner and demonstrate care and attention to customers.
Technical expertise: In high-tech fields such as Rogers Cavity PCB manufacturing, customers often seek professional technical support and advice. Manufacturers should have extensive technical knowledge and experience and be able to provide customers with accurate and useful information and advice.
On-time and reliable delivery: Timely delivery of products is one of the key factors in ensuring customer satisfaction. Manufacturers should strictly adhere to delivery schedules and communicate any potential delays in advance where possible to ensure customers have a clear understanding of delivery plans.
Positive problem-solving attitude: Customers may encounter various problems or challenges, and manufacturers should respond to them with a positive attitude and problem-solving skills. Promptly identifying problems and working with customers to find solutions can help build trust and collaborative relationships.
By prioritizing these key qualities, Rogers Cavity PCB manufacturers can build lasting relationships with customers and build a strong reputation in the industry. Excellent customer service not only increases customer loyalty and satisfaction, but also promotes a company’s business growth and success.
Frequently Asked Questions
What are the advantages of Rogers Cavity PCBs over traditional PCBs?
Rogers Cavity PCBs offer several advantages over traditional PCBs, particularly in high-frequency applications. Firstly, the cavity design helps to minimize signal loss and reduce electromagnetic interference, resulting in improved signal integrity and overall performance. Additionally, Rogers high-frequency laminates exhibit excellent dielectric properties, allowing for precise impedance control and consistent performance across a wide range of frequencies. Moreover, Rogers Cavity PCBs are renowned for their reliability and durability, making them ideal for demanding environments and mission-critical applications.
How does the cavity design contribute to improved performance in Rogers Cavity PCBs?
The cavity design in Rogers Cavity PCBs plays a crucial role in enhancing performance by providing better control over impedance and reducing signal loss. By encapsulating a dielectric material within the board layers, the cavity effectively isolates the signal traces, minimizing electromagnetic interference and ensuring signal integrity. This design feature is particularly beneficial in high-frequency applications where maintaining precise impedance matching is essential for optimal signal transmission and reception.
What factors should be considered when selecting materials for Rogers Cavity PCBs?
When selecting materials for Rogers Cavity PCBs, several factors should be taken into account to ensure optimal performance and reliability. These include the dielectric constant and loss tangent of the substrate material, which directly impact signal propagation and attenuation. Additionally, factors such as thermal conductivity, coefficient of thermal expansion, and moisture absorption should be considered to address thermal management and reliability concerns, especially in harsh operating environments.
Can Rogers Cavity technology be applied to multilayer PCB designs?
Yes, Rogers Cavity technology can be applied to multilayer PCB designs, offering enhanced performance and flexibility in high-frequency applications. By incorporating cavities within the multilayer stack-up, engineers can achieve precise impedance control and isolation between signal layers, reducing crosstalk and improving overall signal integrity. This approach allows for the integration of complex circuitry and functionality while maintaining high-frequency performance and reliability.
How can manufacturers ensure the reliability of Rogers Cavity PCBs in harsh operating environments?
Manufacturers employ various techniques and strategies to ensure the reliability of Rogers Cavity PCBs in harsh operating environments. These may include rigorous testing and qualification processes to verify compliance with industry standards and specifications. Additionally, manufacturers may implement design enhancements such as controlled impedance routing, thermal management features, and conformal coating to enhance durability and withstand challenging environmental conditions such as temperature extremes, humidity, and vibration.