RT/duroid® 5880 Laminates PCB Manufacturer, Rogers 5880 PCB, Rogers Mixed dielectric material PCBs Vendor. we offer Ro5880 PCB from 2 layer to 30 layers.
RT/duroid® 5880 laminates play a key role in today’s electronics landscape. Its unique performance characteristics make it one of the preferred materials in PCB design and manufacturing. In this article, we will take an in-depth look at the properties and manufacturing processes of RT/duroid® 5880 laminates, revealing the importance and application prospects of this material in the modern electronics industry.
What is a RT/duroid® 5880 Laminates PCB ?
RT/duroid® 5880 laminate is a high-performance material that plays an important role in modern electronics. Its unique properties and wide range of applications make it popular. As a high-frequency circuit board material, RT/duroid® 5880 plays a key role in communications, radar systems, satellite communications and other fields. Its excellent dielectric properties, low loss factor, and stable dimensional properties make it one of the materials of choice for many high-frequency applications.
In PCB design and manufacturing, RT/duroid® 5880 laminate offers a unique set of advantages. First of all, its high dielectric constant and low loss factor ensure the stability and reliability of signal transmission, and is especially suitable for circuit design of high-frequency and high-speed transmission. Secondly, RT/duroid® 5880 laminate has excellent high temperature resistance and can maintain stable electrical performance in extreme environments, which is crucial for some special applications.
The manufacturing process of RT/duroid® 5880 laminates involves precision craftsmanship and strict quality control. During the laminate manufacturing process, advanced materials and technologies ensure the highest level of quality and performance for each panel. From the selection of raw materials to lamination, etching, drilling, gold plating and other process steps, every link is carefully designed and strictly executed to ensure that the final product meets high standards.
Overall, RT/duroid® 5880 laminate is an indispensable material in modern electronic design and manufacturing. Its excellent performance and reliability provide a solid foundation for high-frequency circuit design. By gaining a deeper understanding of the properties and manufacturing processes of RT/duroid® 5880 laminates, engineers can better leverage the benefits of this material to drive innovation and development in the electronics field.
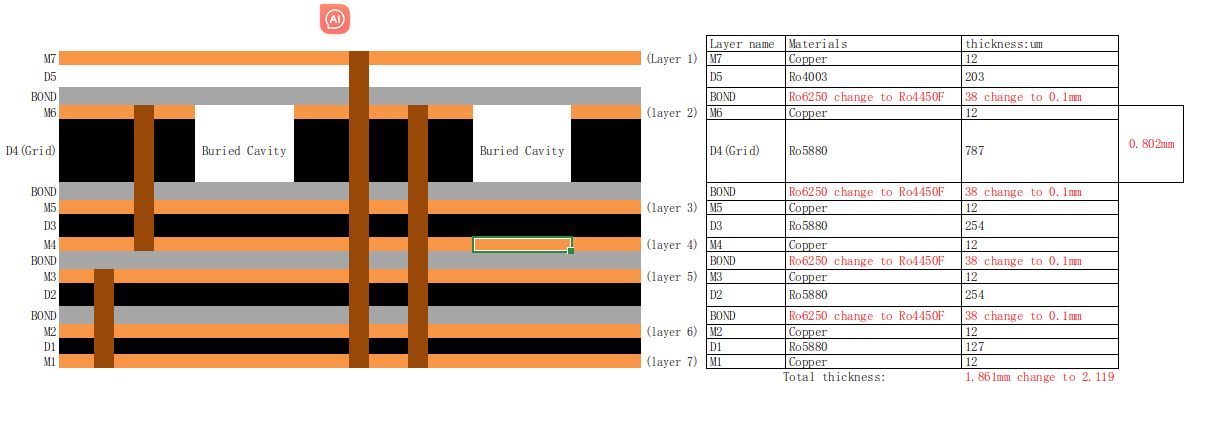
RT/duroid® 5880 Laminates PCB
How to Design a RT/duroid® 5880 Laminates PCB ?
When designing a PCB with RT/duroid® 5880 laminate, engineers must carefully consider several key factors to ensure optimal performance and reliability of the design. The following are several aspects that require special attention during the design process:
The substrate thickness of RT/duroid® 5880 laminate is critical to overall performance. The choice of thickness will directly affect the speed and loss of signal transmission, so engineers need to determine the most appropriate thickness based on the requirements of the specific application. For high-frequency applications, thinner substrates are often chosen to reduce signal transmission delays and losses.
The geometry of the conductor also has a significant impact on signal transmission. Engineers need to precisely design the width and spacing of the wires to ensure the required impedance matching and signal integrity. Using advanced design software, engineers can perform simulation analysis and use the results to optimize conductor layout to maximize signal performance.
During the design process, engineers must also ensure impedance matching across various parts of the PCB. RT/duroid® 5880 laminates have consistent dielectric constants and dissipation factors, which provides engineers with excellent design flexibility. By accurately calculating and adjusting parameters such as line width and line spacing, engineers can achieve ideal impedance matching and ensure stable signal transmission throughout the circuit.
In modern PCB design, design software and simulation tools are indispensable auxiliary means. Engineers can use these tools for circuit layout, conductor optimization and signal simulation to verify the performance of the design and make necessary adjustments. Through simulation analysis, engineers can discover potential problems in advance and carry out effective optimization to ensure that the final product reaches the expected performance indicators.
In summary, designing a PCB with RT/duroid® 5880 laminate requires engineers to consider factors such as substrate thickness, conductor geometry, and impedance matching. With advanced design software and simulation tools, engineers can optimize signal performance, minimize losses, and ensure the highest levels of functionality and efficiency in designs.
What is the RT/duroid® 5880 Laminates PCB Fabrication Process?
The manufacturing process of RT/duroid® 5880 laminate is a precise and complex process that requires highly professional technology and strict execution. From the selection of raw materials to the manufacturing and assembly of the final product, every step is critical and directly affects the quality and performance of the final product.
First, the key to manufacturing RT/duroid® 5880 laminates is material selection. This laminate uses high-performance polytetrafluoroethylene (PTFE) as the dielectric material laminated to a fiberglass-reinforced polymer substrate. Choosing the right PTFE material and substrate material is critical as they directly affect the dielectric properties, thermal properties and mechanical strength of the PCB.
After the material selection is determined, the next step is the precise operation of the manufacturing process. Manufacturers will use advanced equipment and technology for precision lamination to ensure a strong and even bond between the dielectric layer and the conductive layer. Subsequently, the PCB board will be sent to the etching equipment for the formation of circuit patterns. In this step, manufacturers need to ensure the accuracy and consistency of the etching process to ensure the quality and stability of the circuit.
Drilling is another critical step in manufacturing RT/duroid® 5880 laminates. Precise hole position and aperture are important factors to ensure the accuracy of PCB circuit connection. Manufacturers will use high-precision CNC drilling machines to drill holes and ensure the quality of the hole walls and surface smoothness.
Finally, the PCB board enters the metallization and surface treatment stage. This step involves plating the surface of the conductive layer with metal to ensure good electrical connectivity and corrosion resistance. Manufacturers use advanced gold plating techniques, such as electroplating or spraying metal, to complete the process.
Throughout the entire manufacturing process, strict quality control and inspection procedures are indispensable. Manufacturers will use a variety of inspection methods, such as X-ray inspection and automatic optical inspection systems, to ensure that the quality of each PCB board reaches the highest standards. Only through strict quality control can we produce high-quality products that meet industry standards and meet customer needs.
Overall, the manufacturing process of RT/duroid® 5880 laminate requires a high degree of expertise and strict quality control. Manufacturers utilize advanced equipment and technology to ensure every step is executed with precision and reliability, resulting in quality products that exceed industry expectations.
How to Manufacturer a RT/duroid® 5880 Laminates PCB ?
The manufacturing process of RT/duroid® 5880 laminate is a precise and complex process involving multiple critical steps, from material preparation to final inspection, each step is critical.
First, the manufacturing process begins with the preparation of raw materials. The key materials in RT/duroid® 5880 laminate are a high-performance polytetrafluoroethylene (PTFE) dielectric and a glass fiber reinforced polymer substrate. These materials must undergo rigorous quality inspection and testing to ensure they meet specifications.
Next comes the lamination process. In this step, the pre-cut media and substrate and copper foil layers are laminated together according to the design requirements. By applying pressure and temperature, they are held together to form a strong composite structure. The key to this step is to make sure each layer bonds together evenly and without bubbles or voids.
This is followed by etching and patterning. The desired circuit pattern can be transferred to the surface of the copper foil by placing a patterned film coated with a photosensitizer on the copper foil and exposing it to ultraviolet light. A chemical solution is then used to etch away the portions of the copper that are not protected by the photosensitizer, leaving the desired conductor pattern.
Next comes drilling and metallization. In this step, holes are drilled into the board using a mechanical or laser drill machine, and the inside of the holes are plated with metal to ensure continuity of the conductive paths. These holes can be used to connect wires between different layers to achieve multi-layer PCB designs.
Finally comes coating and final inspection. In this step, the surface is coated with a covering layer to protect the circuit from the external environment and a final visual and functional inspection is performed. The inspection process involves using tools such as X-rays and microscopes to check the integrity and accuracy of circuit patterns to ensure each PCB meets specifications.
In summary, the manufacturing process of RT/duroid® 5880 laminate is a precise and complex process that requires a high degree of professional knowledge and technology. Through strict quality control and exquisite craftsmanship, manufacturers are able to produce PCBs with high quality, reliability and excellent performance to meet the needs of various high-frequency applications.
How Much Does a RT/duroid® 5880 Laminates PCB Cost?
Cost is an important consideration for any project, especially in the field of PCB design and manufacturing. As a high-performance material, RT/duroid® 5880 laminate may cost slightly more than traditional materials, but the long-term benefits it brings are immeasurable.
First, the high-performance characteristics of RT/duroid® 5880 laminate can lead to more stable and reliable circuit designs. High dielectric constant and low loss factor make signal transmission in PCB more efficient, thus reducing signal attenuation and distortion. This means the equipment maintains stable performance over long periods of use, reducing maintenance and repair costs.
Secondly, the excellent performance of RT/duroid® 5880 laminate can also improve product life and reliability. Due to the high-quality properties of its materials, PCBs can better resist the effects of environmental factors such as humidity, temperature changes, etc., thus extending the life of the device. This means customers can use the product for longer, replacing equipment less frequently, which in turn saves overall costs.
Additionally, working with a trusted RT/duroid® 5880 laminate manufacturer provides engineers with customized solutions and professional support. Manufacturers usually have extensive experience and advanced technology and can provide customers with the best design suggestions and optimization solutions, thereby helping customers minimize costs and improve performance.
So while RT/duroid® 5880 laminates may be slightly higher in terms of initial investment, the investment is well worth it when considering the long-term stability, reliability and performance benefits. Through partnerships, engineers can optimize cost-effectiveness without sacrificing quality and provide customers with superior products and services.
What materials are RT/duroid® 5880 Laminates PCB made of?
RT/duroid® 5880 laminate is a high-performance PCB material composed of high-performance polytetrafluoroethylene (PTFE) dielectric material and glass fiber reinforced polymer substrate. This material combines the excellent electrical properties of PTFE with the mechanical strength of glass fiber reinforced polymers to provide outstanding performance and reliability for high frequency applications.
The process of manufacturing RT/duroid® 5880 laminate is very delicate and requires multiple steps to ensure the quality and performance of the final product. First, a polytetrafluoroethylene (PTFE) dielectric material is layered with a fiberglass-reinforced polymer substrate to form the base structure of the laminate. This step requires precise control of temperature and pressure to ensure uniformity and adhesion between the material layers.
Next, the circuit pattern and conductor outlines are transferred to the laminate surface using etching techniques. This step requires high-precision chemical processing and patterning techniques to ensure the accuracy and clarity of circuit patterns. This is followed by drilling operations for connecting wires and connectors between the different layers. These drilled holes must be precisely positioned and of consistent diameter to ensure circuit connectivity and stability.
Finally, surface treatment processes such as gold plating are used to enhance the conductivity and corrosion resistance of the laminate. This step not only improves the reliability and durability of the laminate, but also ensures its stability and reliability in complex environments.
Overall, the manufacturing process of RT/duroid® 5880 laminate requires a high degree of technical expertise and strict quality control to ensure that the final product meets high standards of electrical performance and mechanical strength requirements. Through precise lamination, etching, drilling and gold plating steps, RT/duroid® 5880 laminate can achieve high-precision manufacturing of complex circuit patterns, providing a solid foundation for performance improvement and reliable operation of high-frequency electronic equipment.
Who manufactures RT/duroid® 5880 Laminates PCB ?
The manufacturer of RT/duroid® 5880 laminate is our company. We are proud to be a leader in this field and have a strong reputation in the industry for our superior quality and innovation.
As a manufacturer of RT/duroid® 5880 laminate, we are committed to providing high-quality, reliable, and excellent-performance products to meet our customers’ stringent needs for high-frequency applications. Our manufacturing process is unique, using state-of-the-art technology and equipment to ensure consistent quality and performance with every RT/duroid® 5880 laminate.
Our team is comprised of experienced engineers and technical experts with an in-depth understanding of the properties and applications of RT/duroid® 5880 laminate. Whether in the design stage or during the manufacturing process, we strictly follow the highest quality standards to ensure product reliability and stability.
At the same time, we continue to conduct research and development and innovation to meet changing market needs and customer needs. We are not only committed to providing high-quality products, but also focus on working closely with our customers to understand their needs and provide customized solutions.
As manufacturers of RT/duroid® 5880 laminate, we understand the importance of product quality and customer satisfaction. Therefore, we will continue to work hard to provide customers with high-quality products and services and become their trustworthy partner.
In our factory, each RT/duroid® 5880 laminate undergoes rigorous quality control and inspection to ensure it meets industry standards and customer requirements. We are customer satisfaction oriented, constantly pursue excellence, and strive to become the world’s leading RT/duroid® 5880 laminate manufacturer.
In general, our company has won the trust and support of our customers with its excellent product quality, leading technical level and excellent customer service. As a manufacturer of RT/duroid® 5880 laminate, we will continue to work hard to provide customers with better products and services and jointly promote the development of the electronics industry.
What are 5 qualities of a good customer service?
In the PCB manufacturing industry, excellent customer service is a key factor in ensuring customer satisfaction and long-term loyalty. RT/duroid® 5880 laminate manufacturers understand this and put customer service at the heart of their business. The following are the key attributes of excellent customer service that RT/duroid® 5880 laminate manufacturers value:
Professionalism: RT/duroid® 5880 laminate manufacturers provide customers with professional advice and solutions based on professional knowledge and experience. No matter what challenge or need a client faces, they are able to provide accurate, timely assistance and ensure every job is handled properly.
Responsiveness: RT/duroid® 5880 laminate manufacturers remain highly responsive to customer inquiries, feedback or complaints. They quickly respond to customers’ emails, phone calls, or online messages to ensure customers receive timely support and solutions, thereby building good communication and trust.
Personalized Care: RT/duroid® 5880 laminate manufacturers understand that each customer’s needs and preferences may be different, so they provide personalized care and service. Whether the client is a large enterprise or a small startup, we tailor solutions to meet their needs based on their specific requirements and circumstances.
Problem-solving capabilities: RT/duroid® 5880 laminate manufacturers have excellent problem-solving capabilities when faced with various problems or challenges that customers may encounter. They actively listen to customers’ needs and feedback, quickly find the root cause of the problem, and provide effective solutions to ensure that customer problems are solved in a timely manner and to avoid similar problems from happening again.
Continuous improvement: In order to continuously improve the quality of customer service, RT/duroid® 5880 laminate manufacturers focus on continuous improvement. They regularly collect customer feedback and suggestions, evaluate and optimize service processes and operations, and continuously improve work efficiency and customer satisfaction to adapt to changing market needs and customer expectations.
To sum up, RT/duroid® 5880 laminate manufacturers ensure that customers receive the best in every cooperation with their professionalism, responsiveness, personalized care, problem solving and continuous improvement of quality customer service. experience and results, thereby building a solid partnership and long-term trust.
FAQS
How does RT/duroid® 5880 laminate compare to other PCB materials?
RT/duroid® 5880 laminate has a higher dielectric constant and lower dissipation factor than other common PCB materials, which makes it perform better in high-frequency applications. Its excellent dimensional stability and signal transmission performance make it the material of choice in fields such as wireless communications, radar systems, and satellite communications.
What are the key considerations when designing with RT/duroid® 5880 laminate?
When using RT/duroid® 5880 laminates in designs, engineers need to consider factors such as substrate thickness, conductor geometry and impedance matching. By carefully adjusting these parameters, signal transmission performance can be maximized and the stability and reliability of the design can be ensured.
How to optimize cost-efficiency when using RT/duroid® 5880 laminates in designs?
Although RT/duroid® 5880 laminate may have a higher cost, there are ways to optimize cost effectiveness. For example, choosing the appropriate substrate thickness and number of layers to minimize material waste; optimizing the design to reduce complexity and manufacturing difficulty; and working with reputable manufacturers to obtain competitive prices and quality services.
Are there specific design guidelines for using RT/duroid® 5880 laminate in high frequency applications?
Yes, for high frequency applications, there are some specific design guidelines that need to be followed when using RT/duroid® 5880 laminate. This includes ensuring impedance matching accuracy, minimizing signal loss, avoiding electromagnetic interference and crosstalk, and employing proper packaging and layout design to maximize performance and reliability.