RT5880 PCB manufacturing. Rogers RT5880 PCB and Rogers Series material mixed laminated PCB Vendor, We offer HDI mixed laminated rogers PCBs from 4 layer to 30 layers. Such as HDI Rogers PCBs, Cavity Rogers PCBs.
In the field of modern electronics, RT5880 PCB manufacturing is an indispensable part. As the support for almost all electronic devices, the RT5880 PCB carries important functions, especially in high-frequency applications. This article will delve into the RT5880 PCB manufacturing process, including design, materials, cost, and key manufacturing steps, aiming to provide readers with a comprehensive guide and in-depth understanding.
What is RT5880 PCB?
RT5880 PCB, referred to as high-frequency board, is a printed circuit board dedicated to high-frequency applications. It is commonly used in radio frequency (RF) and microwave circuits to meet applications with extremely high requirements on frequency response and signal transmission speed. Compared with traditional FR-4 PCB, RT5880 PCB has better dielectric properties and lower loss, which makes it perform well in high-frequency signal transmission and maintain signal stability and accuracy. Due to its excellent performance characteristics, RT5880 PCB is widely used in wireless communications, satellite communications, radar systems and other fields, becoming an indispensable key component in these fields. In the field of wireless communications, RT5880 PCB is used to manufacture high-performance antennas, signal amplifiers and filters to achieve more stable and faster data transmission. In satellite communications and radar systems, RT5880 PCB is responsible for the transmission and processing of high-frequency signals to ensure the stability and reliability of the system. Therefore, the excellent performance and wide application of RT5880 PCB make it an important part in the manufacturing of high-frequency electronic equipment, providing strong support for the development and application of modern communication technology.
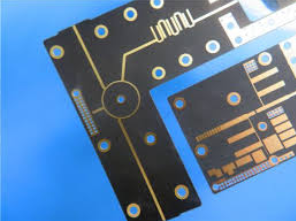
RT5880 PCB
What is the RT5880 PCB design process?
The RT5880 PCB design process is a delicate and critical stage that determines the performance and reliability of the final product. First, the design team needs to draw a schematic diagram of the circuit to clearly show the connection relationship between the various components in the circuit. This step is the foundation of the entire design process and lays a solid foundation for subsequent work.
Next is the component layout stage. At this stage, the design team places individual electronic components on the PCB board, taking into account the distance between components, connection relationships, and the overall size of the final product. Reasonable component layout can ensure the stability and reliability of the circuit and lay the foundation for subsequent wiring work.
Routing is a critical part of the design process. At this stage, the design team needs to plan and arrange the connection lines between various electronic components to ensure the stability and reliability of signal transmission. With the help of professional software, engineers can optimize the signal path, reduce signal interference and crosstalk, and improve circuit performance.
The last step is the layout design stage. At this stage, the design team will complete the design of the physical layout, including determining the size of the PCB board, the stacking method, and the location of external interfaces. By optimizing the layout design, you can maximize the use of space and improve the manufacturing efficiency and cost-effectiveness of PCB boards.
The entire design process requires close cooperation and precise planning by the design team to ensure that each stage proceeds smoothly and achieves the expected design goals. Through carefully designed RT5880 PCB, it can provide stable and reliable circuit support for high-frequency applications and meet the needs of various complex electronic devices.
What is the manufacturing process of RT5880 PCB?
What is the manufacturing process of RT5880 PCB? This is an issue worth understanding in depth, as it directly affects PCB quality and performance. Below we will introduce the manufacturing process flow of RT5880 PCB in detail to better understand this process.
First, the first step in manufacturing the RT5880 PCB is substrate selection. For RT5880 PCB, choosing the appropriate substrate material is crucial. Normally, high-frequency circuit boards need to choose materials with low dielectric constant and low loss to ensure good signal transmission performance. Commonly used materials include PTFE substrate and fiberglass-reinforced epoxy (FR-4).
Next is lamination (Layer Stackup). RT5880 PCB is usually a multi-layer structure. During the lamination process, sheets of different materials are laminated together and bonded together through high temperature and high pressure conditions to form a strong board structure.
Copper foil processing is one of the key steps in manufacturing RT5880 PCB. Copper foil is used to form wires and connectors, creating conductive paths on PCBs. The quality and thickness of the copper foil play an important role in the performance of the PCB and therefore need to be strictly controlled during processing.
Then comes drilling. Drilling is the process of forming connection holes in a PCB to connect circuits between different layers. For the RT5880 PCB, these holes need to be precisely positioned and drilled to ensure the transmission quality of high-frequency signals.
Next is copper plating. After drilling, a layer of copper needs to be plated inside the hole to form the connection. This step is also very critical because it directly affects the quality and reliability of the connection.
Finally, there is etching. Etching is the chemical removal of unnecessary parts of the copper foil, retaining the circuit pattern. This step requires precise control of the composition and concentration of the etching solution to ensure accurate removal of the copper foil in the target area.
All these steps together constitute the RT5880 PCB manufacturing process flow. Through strict control and precise operation, the quality and reliability of the final product can be ensured. Therefore, when designing and manufacturing the RT5880 PCB, attention must be paid to every detail to ensure that the final product can meet the requirements of high-frequency circuits.
How much does it cost to manufacture RT5880 PCB?
The manufacturing cost of RT5880 PCB is affected by many factors, including size, complexity, material and quantity. First of all, size is one of the important factors that determine the cost. Larger PCB sizes require more substrate material and processing steps, and therefore cost more. In addition, complexity is also a key factor affecting cost. Complex circuit designs require more wiring and processing steps, increasing manufacturing costs. Material selection also has a significant impact on cost. High-performance materials such as RT5880 have excellent electrical properties, but their prices are relatively high, which will increase manufacturing costs. Finally, quantity is another important factor in determining cost. Typically, high-volume production reduces the cost per PCB, while low-volume production increases costs. Understanding these cost drivers is critical to budgeting and optimizing production costs. Through rational selection of size, simplified design, selection of cost-effective materials, and reasonable planning of production quantity, the manufacturing cost of RT5880 PCB can be effectively controlled, thereby achieving budget targets and improving production efficiency.
What is the manufacturing material of RT5880 PCB?
What is the manufacturing material of RT5880 PCB? This is a crucial question because material selection directly affects PCB performance and reliability. Let’s take a closer look:
RT5880 PCB usually uses fiberglass reinforced epoxy resin (FR-4) as the substrate material. FR-4 is a very common substrate material and is widely used in PCB manufacturing due to its excellent mechanical strength, thermal stability and insulation properties. It is able to withstand high temperature and high humidity environments while maintaining stable electrical performance.
In the RT5880 PCB, copper foil is used to build the conductive traces. Copper is an excellent conductive material with good electrical conductivity and mechanical strength. By covering the surface of the substrate with copper foil and using chemical processing technology, precise circuit patterns can be formed to achieve connections between electronic components.
Additionally, pad overlays are used to insulate and protect circuitry. Pad coverage typically consists of a pad covering compound that provides protection during the soldering process and prevents short circuits or other damage caused by soldering. It can also prevent environmental factors such as moisture, dust, etc. from affecting the circuit, thereby improving the reliability and stability of the PCB.
Under specific design requirements, RT5880 PCB may use some advanced materials, such as flexible substrates and metal substrates. Flexible substrates have good flexibility and bendability and are suitable for electronic product designs that require bending or folding. Metal substrates have excellent heat dissipation performance and mechanical strength, and are suitable for high-power and high-frequency circuit applications.
To sum up, the manufacturing materials of RT5880 PCB include FR-4 substrate, copper foil, pad covering layer, etc. Under specific design requirements, advanced materials such as flexible substrate and metal substrate may also be used to meet the requirements of different electronic products. need. The selection of these materials needs to be weighed and selected based on the specific requirements and application scenarios of the PCB design to ensure the performance and reliability of the final product.
Who is the RT5880 PCB manufacturer?
RT5880 PCB manufacturers play a vital role in the market as they are responsible for converting design concepts into actual functional circuit boards. In this field, professional manufacturers play a key role in providing customers with high-quality products and reliable services. As a professional RT5880 PCB manufacturer, our company adheres to years of experience and expertise and is committed to providing customers with excellent products and services.
As a professional RT5880 PCB manufacturer, we have advanced production equipment and technology to meet our customers’ needs for high-quality circuit boards. Our manufacturing process strictly follows international standards to ensure that each RT5880 PCB has excellent performance and reliability. From raw material procurement to production and processing to final quality inspection, we strictly control every step to ensure product consistency and stability.
In addition to product quality, our company also focuses on cooperation and communication with customers. Our team consists of experienced engineers and professional customer service personnel who can provide personalized solutions and timely technical support. No matter what challenges or needs our clients face, we are able to help and support them with a professional attitude and efficient working style.
In addition, our company is committed to continuous innovation and technological advancement. We continuously invest in R&D and explore new manufacturing technologies and materials to meet changing market demands and customer needs. We believe that through unremitting efforts and innovation, we will be able to maintain our leading position in the field of RT5880 PCB manufacturing.
Overall, as a professional RT5880 PCB manufacturer, our company is committed to providing customers with high-quality products and excellent services. We will continue to work hard to work together with our customers to develop together and contribute to the development of the electronics industry.
What are the five qualities of great customer service?
Responding promptly and effectively when customers have inquiries or concerns is the key to building a good customer relationship. Quickly responding to customer needs can effectively shorten the time to solve problems and enhance customer trust and satisfaction with services. A team with excellent customer service will ensure that customer issues are attended to and dealt with in a timely manner, thus improving the overall service level.
Understanding your customers’ needs and feelings is at the heart of great customer service. By treating customers with compassion and understanding, service staff are better able to grasp the customer’s emotions and needs and take appropriate steps to solve the problem. Empathy not only reflects the care and attention of service personnel, but also enhances customer satisfaction and loyalty.
Continuous delivery of promises and commitments to customers is the basis for building a reliable reputation. Customers expect to be able to rely on service providers to provide stable and reliable services, so maintaining reliability is one of the important attributes of good customer service. By delivering timely and completing work with quality and quantity, the service team can win the trust and respect of customers.
Clear and transparent communication is the basis for building good customer relationships. During the service process, proactively communicate with customers, deliver important information in a timely manner, and help customers understand project progress and solutions. Through effective communication, service teams can avoid misunderstandings and unnecessary doubts, ensuring smooth cooperation between customers and teams.
Proactively resolving issues and striving to achieve customer satisfaction is the ultimate goal of great customer service. In the face of challenges and problems raised by customers, the service team should adopt a positive attitude, find solutions and follow up on implementation in a timely manner. By continuously striving to improve service quality and meet customer needs, the service team can win the trust and support of customers and achieve a win-win situation.
In practice, the five characteristics of high-quality customer service are interrelated and mutually reinforcing, and together they build a good service system to provide customers with a better and more efficient service experience. By continuously strengthening these characteristics, the service team can continuously improve service levels and achieve sustainable development and long-term cooperation.
Frequently Asked Questions
What is the difference between single-layer and multi-layer PCBs?
Single-layer PCBs have conductive traces on only one side of the board, while multi-layer PCBs feature multiple layers of conductive traces interconnected by vias, enabling greater circuit complexity and density.
How long does it take to manufacture an RT5880 PCB?
The manufacturing time for an RT5880 PCB varies depending on factors such as complexity, quantity, and supplier lead times, typically ranging from a few days to several weeks.
What are the common challenges in RT5880 PCB manufacturing?
Common challenges include ensuring design manufacturability, maintaining tight tolerances, managing material costs, and addressing quality control issues specific to high-frequency applications.
What is the significance of surface finish in RT5880 PCBs?
Surface finish plays a crucial role in protecting exposed copper traces from oxidation and providing a solderable surface for component attachment, ensuring reliable electrical connections, especially in high-frequency applications.
Can RT5880 PCBs be recycled?
Yes, RT5880 PCBs can be recycled to recover valuable metals such as copper and reduce environmental impact. However, the recycling process must be conducted responsibly to mitigate potential hazards associated with electronic waste.