Semiconductor Glass Substrate Manufacturer.As a leading Semiconductor Glass Substrate Manufacturer, we specialize in crafting high-quality substrates tailored to the precise needs of semiconductor devices. With advanced manufacturing processes and cutting-edge technology, we ensure superior performance, reliability, and precision in every substrate produced.
Semiconductor glass substrates are an indispensable and key component of modern electronic technology. As the basic structure of electronic devices, it stably supports various components, thereby promoting the continuous development of the electronics industry. This article will delve into the importance and widespread application of semiconductor glass substrates in the field of electronic technology, as well as its important role in promoting the advancement of electronic technology.
What is Semiconductor Glass Substrate?
Semiconductor glass substrate is an amorphous glass material that is widely used to manufacture high-performance semiconductor devices. It is characterized by good optical and electrical properties, making it an important component of many advanced electronic technologies. Compared with traditional substrate materials, semiconductor glass substrates usually have higher flatness and surface quality, and can provide a reliable basic support structure.
The excellent optical properties of semiconductor glass substrates mean that they have good transparency and optical uniformity, and are suitable for manufacturing optoelectronic devices, such as liquid crystal displays, photoelectric sensors, etc. At the same time, its excellent electrical properties make it have good insulation properties and electrical characteristics, and can be used to manufacture the basic structure of various electronic devices.
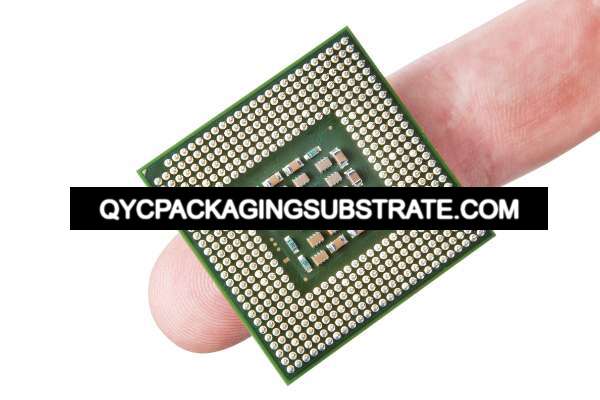
Semiconductor Glass Substrate Manufacturer
During the manufacturing process, the semiconductor glass substrate undergoes precise processing to ensure that its flatness and surface quality meet the requirements. This includes raw material selection, melt molding, cooling and solidification, polishing and other steps to ensure the quality stability and surface finish of the substrate.
In general, semiconductor glass substrates are of great significance in the field of electronic technology. They not only provide a reliable infrastructure for various semiconductor devices, but also promote the progress and innovation of electronic technology. With the continuous development of electronic technology, we can expect that semiconductor glass substrates will be widely used in more fields and contribute more to the development of electronic technology.
Semiconductor Glass Substrate design Reference Guide.
Semiconductor glass substrates play an important role in modern electronic devices, and their design is related to the performance, stability and production efficiency of electronic devices. Below is a brief reference guide for semiconductor glass substrate design to help you develop an efficient and reliable design.
Choosing a suitable semiconductor glass substrate material is crucial. Consider the material’s optical and electrical properties as well as its thermal stability. Common materials include silica glass, quartz glass, etc. Choose the most appropriate material according to specific application requirements.
When designing semiconductor glass substrates, taking into account the design of multi-layer structures can provide larger layout space and higher integration. Reasonable laminate structure design can reduce signal interference and improve circuit performance.
Line width and line spacing are key parameters in the design of semiconductor glass substrates, which directly affect the transmission rate and signal quality of the circuit. During the design process, line width and line spacing should be reasonably selected based on specific application needs and manufacturing process requirements.
Reasonable device layout can reduce the transmission delay of the circuit, reduce power consumption, and improve the stability and reliability of the circuit. During the design process, device layout optimization should be performed based on circuit functions and layout requirements.
In the design of semiconductor glass substrates, electromagnetic compatibility should be considered and effective electromagnetic shielding measures should be taken to reduce electromagnetic interference and ensure the stability and reliability of the circuit.
When designing semiconductor glass substrates, the requirements of the manufacturing process should be taken into consideration, and the wiring and spacing should be reasonably arranged to reduce defects and damage during the manufacturing process.
After the design is completed, rigorous testing and verification are conducted to ensure that the design meets performance and quality requirements. Through simulation and experimental verification, the design solution is optimized and the reliability and stability of the product are improved.
Semiconductor glass substrate design is a complex process that comprehensively considers many factors such as materials, structure, layout, and manufacturing processes. This guide provides some basic principles and considerations, hoping to help you develop a better semiconductor glass substrate design solution.
What material is used in Semiconductor Glass Substrate?
Semiconductor glass substrate is a key electronic material, usually made of high-purity glass materials, which mainly includes the following materials:
Borosilicate Glass: Borosilicate glass is a commonly used semiconductor glass substrate material with excellent chemical stability and thermal stability. Its low thermal expansion coefficient allows it to maintain stable dimensions at high temperatures, making it suitable for manufacturing high-temperature electronic devices.
Quartz Glass: Quartz glass is a high-purity inorganic glass material with excellent optical properties and chemical stability. Its high transparency and low thermal expansion coefficient make it ideal for manufacturing optoelectronic devices.
Soda Lime Borosilicate Glass: Soda Lime Borosilicate Glass is a commonly used industrial glass material with good mechanical strength and chemical stability. It is usually used to manufacture ordinary semiconductor glass substrates and is suitable for the manufacturing needs of general electronic devices.
Zirconium Oxide Glass: Zirconium Oxide Glass is a special glass material with high hardness and high compressive strength, with excellent wear resistance and chemical stability. It is often used to manufacture semiconductor glass substrates for special purposes, such as high-voltage electronic devices or high-speed electronic devices.
To sum up, the materials of semiconductor glass substrates mainly include borosilicate glass, quartz glass, soda-lime boron glass and zirconia glass. Each material has specific physical and chemical properties and is suitable for different types of electronic device manufacturing needs. .
What size are Semiconductor Glass Substrate?
The dimensions of semiconductor glass substrates often depend on specific application requirements and manufacturing processes. Generally speaking, semiconductor glass substrates can be manufactured in various sizes and shapes to meet the design and manufacturing needs of different electronic devices.
In the manufacture of large electronic devices such as flat panel displays, the size of the semiconductor glass substrate may be relatively large, usually tens of inches or even larger, to accommodate the size and resolution requirements of the display screen. For example, in LCD display manufacturing, common sizes include 24 inches, 32 inches, 42 inches, etc.
In the manufacturing of microelectronic devices, the size of the semiconductor glass substrate is usually smaller to accommodate the tiny size and high integration requirements of the device. These micro-semiconductor glass substrates may be only a few millimeters or even smaller, and are suitable for the manufacture of micro-electronic devices such as integrated circuits, sensors, and optoelectronic devices.
In addition to conventional rectangular substrates, semiconductor glass substrates can also be manufactured into other shapes, such as circles, ovals, etc., to meet the needs of specific applications. For example, in the manufacture of optical devices, circular or elliptical substrates can better meet the requirements of optical imaging and transmission.
Overall, semiconductor glass substrates are available in a wide range of sizes and can be customized to specific application needs and manufacturing processes. Whether it is a large-sized flat panel display or a miniature electronic device, semiconductor glass substrate can provide stable and reliable basic support and promote the continuous development and innovation of electronic technology.
The Manufacturer Process of Semiconductor Glass Substrate.
The manufacturing process of semiconductor glass substrates is a precise and complex process that requires strict control of each link to ensure the quality and performance of the final product. The following are the main steps of the manufacturing process:
Material Selection: The first step in manufacturing semiconductor glass substrates is selecting the appropriate raw materials. These raw materials are usually high-purity silicon oxides, such as silicon dioxide (SiO2). The purity and quality of materials are critical to the performance of the final product.
Melt molding: The selected raw materials are melted into a highly plastic glass state. This step is usually performed in a high-temperature furnace to ensure that the material is fully melted and reaches the desired molding temperature and shape.
Cooling and solidification: The glass material after melting and molding needs to undergo an appropriate cooling and solidification process so that it has the required hardness and stability during subsequent processing. The temperature and cooling rate need to be strictly controlled during the cooling process to avoid internal stress and structural defects.
Polishing processing: The surface of the glass substrate after cooling and solidification may have a certain degree of unevenness and roughness, so polishing processing is required to achieve the required flatness and smoothness on the surface. The polishing process usually uses techniques such as mechanical polishing or chemical mechanical polishing to ensure the flatness and optical quality of the substrate surface.
Inspection and quality control: Every critical step of the manufacturing process requires strict inspection and quality control to ensure that the product meets specifications and has stable performance. This includes testing and evaluating aspects such as material composition, dimensional accuracy, surface quality, and more.
Custom processing: Depending on customer needs and final application requirements, semiconductor glass substrates may require custom processing, such as cutting, drilling, etching, etc., to meet specific size, shape and functional requirements.
Packaging and Shipping: After final processing and inspection, the semiconductor glass substrates will be appropriately packaged and labeled, and then shipped to clients or downstream manufacturers for use in manufacturing various electronic devices and semiconductor products.
Through the above manufacturing process, the semiconductor glass substrate can achieve high quality, high stability and high performance, providing reliable basic support for the development of modern electronic technology.
The Application area of Semiconductor Glass Substrate.
Semiconductor glass substrates are widely used in various fields, and their excellent physical properties and stable performance make them ideal for many advanced electronic technologies.
First, semiconductor glass substrates play a key role in flat panel display manufacturing. Flat panel displays, such as liquid crystal displays (LCDs), organic light-emitting diode displays (OLEDs), etc., require substrates with excellent flatness and optical transparency to support the display panels to ensure image quality and display effects.
Secondly, semiconductor glass substrates also have important applications in the field of optoelectronic devices. Optoelectronic devices, such as optical fiber communication devices, optical sensors, etc., require substrates with excellent optical properties to ensure the stability and sensitivity of optical signal transmission and detection.
In addition, semiconductor glass substrates are also widely used in sensor manufacturing. Various types of sensors, such as pressure sensors, temperature sensors, optical sensors, etc., require stable substrates to support the sensor elements to ensure the sensitivity and reliability of the sensor.
In addition, in the field of solar cell manufacturing, semiconductor glass substrates are also widely used. Solar cells require substrates with high transparency and high weather resistance to support solar cell components to improve the absorption efficiency of light energy and the stable performance of the battery.
In general, semiconductor glass substrates are widely used in flat panel displays, optoelectronic devices, sensors, solar cells and other fields. Their excellent physical properties and stability can provide important support for the development of various advanced electronic technologies and promote Continuous innovation and progress in electronic technology.
What are the advantages of Semiconductor Glass Substrate?
Semiconducting glass substrates offer many advantages that make them ideal for use in the manufacture of many electronic devices. The following are the main advantages of semiconductor glass substrates:
High flatness: The surface of the semiconductor glass substrate has high flatness, which can meet the needs of micro device manufacturing. Its flat surface helps ensure device stability and performance.
Excellent optical properties: Semiconductor glass substrates have high transparency and excellent optical properties and can be used to manufacture optoelectronic devices. Its excellent optical properties make it widely used in display technology, optical communications and other fields.
Excellent electrical properties: Semiconductor glass substrate has good insulation properties and electrical characteristics, which can effectively isolate electrical signals between electronic devices and improve the stability and reliability of the device.
High-temperature stability: Semiconductor glass substrates can maintain stable performance in high-temperature environments and are suitable for the manufacturing of high-temperature electronic devices. Its excellent high temperature resistance makes it an important material in automotive electronics, aerospace and other fields.
Good chemical stability: The semiconductor glass substrate has good chemical stability and can resist corrosion and chemical property changes, ensuring the stability and reliability of the device in harsh environments.
Flexibility and processability: Semiconductor glass substrates have certain flexibility and can be bent or cut according to specific needs. It has good processability and facilitates precision processing and the manufacture of fine structures.
Environmentally friendly and sustainable: Semiconductor glass substrates have a low environmental impact and can be reduced through recycling and reuse. Its production process produces less harmful substances and meets modern environmental protection requirements.
In summary, semiconductor glass substrates have many advantages, including high flatness, excellent optical properties, good electrical properties, high temperature stability, chemical stability, flexibility and processability, and environmental sustainability, making them an ideal Important materials in electronic device manufacturing.
FAQ
What is a semiconductor glass substrate?
Semiconductor glass substrate is an amorphous glass material used to manufacture the basic structure of various semiconductor devices. It has excellent flatness and surface quality and is suitable for the manufacture of high-performance electronic devices.
How are semiconductor glass substrates different from traditional substrate materials?
Compared with traditional substrate materials, such as FR-4, semiconductor glass substrates have higher flatness and optical transparency, are suitable for the manufacture of micro devices, and have excellent electrical properties and high temperature stability.
What is the manufacturing process of semiconductor glass substrates?
The manufacturing of semiconductor glass substrates includes raw material selection, melting and molding, cooling and solidification, polishing and other steps. The precise manufacturing process ensures the quality stability and surface finish of the substrate, which is suitable for the manufacturing needs of various semiconductor devices.
What electronic devices are semiconductor glass substrates suitable for?
Semiconductor glass substrates are widely used in the manufacturing of various electronic devices such as flat panel displays, optoelectronic devices, sensors, solar cells, etc. Its excellent physical properties and stable performance make it an ideal choice for many advanced electronic technologies.