Semiconductor Glass Substrate Manufacturer.”Semiconductor Glass Substrate Manufacturer specializes in producing high-quality glass substrates tailored for semiconductor applications. Our advanced manufacturing processes ensure precise specifications, optimal performance, and reliability for cutting-edge semiconductor technologies.”
Semiconductor glass substrates are a specialized type of substrate used in various semiconductor applications. These substrates are made from glass materials that offer unique properties beneficial for semiconductor devices, including high thermal stability, excellent electrical insulation, and superior optical clarity. Semiconductor glass substrates are essential for the development of advanced electronics, optoelectronics, and photonics, providing a foundation for innovative technologies in these fields.
What is a Semiconductor Glass Substrate?
A semiconductor glass substrate is a type of substrate made from glass materials, specifically engineered for use in semiconductor devices. These substrates serve as the foundational layer upon which semiconductor circuits and components are built. The glass material provides a stable and inert platform, which is crucial for the fabrication and operation of semiconductor devices.
Glass substrates are used in a variety of applications, including thin-film transistors (TFTs), microelectromechanical systems (MEMS), photovoltaic cells, and various optoelectronic devices. The unique properties of glass, such as its transparency, chemical resistance, and thermal stability, make it an ideal material for these applications.
Semiconductor Glass Substrate Design Reference Guide
Designing semiconductor glass substrates involves several critical considerations to ensure optimal performance and reliability. The following sections outline the key aspects of the design process:
Material selection is paramount in the design of semiconductor glass substrates. The chosen glass material must exhibit specific properties to meet the requirements of semiconductor applications. Common materials used include:
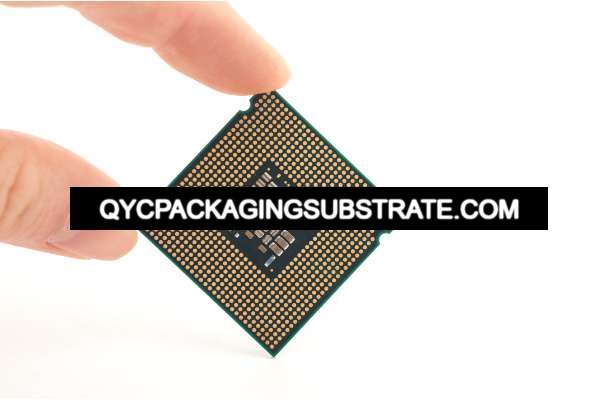
Semiconductor Glass Substrate Manufacturer
Borosilicate Glass: Known for its low thermal expansion and excellent chemical resistance, borosilicate glass is commonly used in semiconductor applications. Its stability under thermal cycling and harsh chemical environments makes it a preferred choice.
Fused Silica: Fused silica glass offers exceptional thermal stability, high optical clarity, and low dielectric loss. It is used in high-performance applications where these properties are critical.
Aluminosilicate Glass: This type of glass provides high mechanical strength and durability, making it suitable for applications requiring robust substrates that can withstand mechanical stresses.
Soda-Lime Glass: While not as advanced as the other types, soda-lime glass is often used in cost-sensitive applications where high performance is not as critical.
The layer structure of a semiconductor glass substrate is designed to support the specific requirements of the semiconductor device. The structure typically includes:
What Material is Used in Semiconductor Glass Substrates?
The materials used in semiconductor glass substrates are selected based on their electrical, thermal, and mechanical properties. The following materials are commonly used:
Borosilicate Glass: This type of glass is widely used due to its low thermal expansion, excellent chemical resistance, and good thermal stability. It is suitable for a variety of semiconductor applications, including TFTs and MEMS.
Fused Silica: Fused silica glass offers exceptional thermal stability, high optical clarity, and low dielectric loss. It is used in high-performance applications such as photonics and optoelectronics.
Aluminosilicate Glass: Aluminosilicate glass provides high mechanical strength and durability, making it suitable for applications requiring robust and resilient substrates.
Soda-Lime Glass: Although not as advanced as the other types, soda-lime glass is used in cost-sensitive applications where high performance is not as critical. It is commonly used in displays and low-cost electronics.
What Size are Semiconductor Glass Substrates?
The size of semiconductor glass substrates varies depending on the specific application and design requirements. The following factors influence the size of these substrates:
Thickness: The thickness of semiconductor glass substrates can range from a few micrometers to several millimeters. Thinner substrates are used in applications where weight and flexibility are critical, while thicker substrates provide additional mechanical strength and thermal stability.
Length and Width: The length and width of semiconductor glass substrates are determined by the size and layout of the semiconductor device. Standard sizes include small wafers for MEMS and sensors, and larger panels for displays and photovoltaic cells. The dimensions can range from a few millimeters to several centimeters or more, depending on the application.
The Manufacturing Process of Semiconductor Glass Substrates
The manufacturing process of semiconductor glass substrates involves multiple stages, each requiring precise control and advanced technology. The following steps outline the typical manufacturing process:
The process begins with the selection and preparation of the raw glass materials. The glass is melted and formed into sheets or wafers of the desired thickness. This step requires careful control of temperature and composition to ensure uniformity and purity.
The glass sheets or wafers are cut and shaped into the required dimensions. This is done using precision cutting tools and techniques to achieve the desired size and shape without introducing defects or stresses.
The surface of the glass substrate is treated to enhance its properties and prepare it for subsequent processing steps. This may include cleaning, polishing, and the application of surface coatings to improve optical, electrical, or thermal performance.
For applications requiring patterned substrates, photolithography and etching techniques are used to create the desired patterns on the glass surface. This involves applying a photoresist, exposing it to light through a mask, and etching away the exposed areas to create the desired structures.
Various coatings and layers may be applied to the glass substrate to enhance its properties. This includes anti-reflective coatings, conductive layers, and protective coatings. These layers are deposited using techniques such as sputtering, chemical vapor deposition (CVD), and atomic layer deposition (ALD).
The final step involves rigorous quality control and testing to ensure the substrates meet the required specifications. Optical inspection, electrical testing, and thermal cycling tests are performed to verify the performance and reliability of the substrates. Defective units are identified and discarded to ensure only high-quality substrates are used in semiconductor devices.
The Application Area of Semiconductor Glass Substrates
Semiconductor glass substrates have a wide range of applications across various industries. Their unique properties make them suitable for advanced and innovative semiconductor devices. The following are some key application areas:
Glass substrates are commonly used in the fabrication of thin-film transistors (TFTs) for displays and other electronic devices. The optical clarity and thermal stability of glass make it an ideal material for supporting the thin films and circuits required for TFT technology.
In MEMS devices, glass substrates provide a stable and inert platform for the fabrication of microstructures and components. The chemical resistance and mechanical strength of glass are crucial for the reliable operation of MEMS devices in various environments.
Glass substrates are widely used in photovoltaic cells for solar energy applications. The transparency and durability of glass make it an ideal material for supporting the semiconductor layers that convert sunlight into electrical energy.
In optoelectronic devices, such as LEDs and photodetectors, glass substrates provide the necessary optical clarity and electrical insulation to support the semiconductor materials and ensure efficient light transmission and detection.
Glass substrates are used in advanced electronic devices that require high-performance and reliable substrates. This includes high-frequency RF devices, sensors, and other semiconductor components that benefit from the unique properties of glass.
What are the Advantages of Semiconductor Glass Substrates?
Semiconductor glass substrates offer several significant advantages, making them a preferred choice in various advanced semiconductor applications. The following are the key advantages:
High Thermal Stability: Glass substrates provide excellent thermal stability, allowing them to withstand high temperatures and thermal cycling without degradation. This is crucial for the reliable operation of semiconductor devices in demanding environments.
Excellent Electrical Insulation: The high electrical insulation properties of glass substrates prevent electrical interference and ensure the integrity of semiconductor circuits. This is essential for high-frequency and high-voltage applications.
Superior Optical Clarity: Glass substrates offer superior optical clarity, making them ideal for optoelectronic and display applications. The transparency of glass allows for efficient light transmission and minimal optical distortion.
Chemical Resistance: Glass substrates exhibit excellent chemical resistance, making them suitable for applications involving harsh chemical environments. This property ensures the longevity and reliability of semiconductor devices.
Mechanical Strength and Durability: Glass substrates provide high mechanical strength and durability, allowing them to withstand mechanical stresses and impacts. This is important for robust and reliable semiconductor devices.
Cost Efficiency: The availability of various types of glass materials and advancements in manufacturing technologies have made the production of semiconductor glass substrates more cost-effective. This allows manufacturers to produce high-performance substrates at a lower cost.
FAQ
What is the typical thickness of a semiconductor glass substrate?
The typical thickness of a semiconductor glass substrate can range from a few micrometers to several millimeters, depending on the application and design requirements. Thinner substrates are used for applications requiring flexibility and lightweight, while thicker substrates provide additional mechanical strength and thermal stability.
What materials are commonly used in semiconductor glass substrates?
Common materials used in semiconductor glass substrates include borosilicate glass, fused silica, aluminosilicate glass, and soda-lime glass. Each material offers unique properties suitable for specific semiconductor applications.
What are the main applications of semiconductor glass substrates?
Semiconductor glass substrates are used in various applications, including thin-film transistors (TFTs), microelectromechanical systems (MEMS), photovoltaic cells, optoelectronic devices, and advanced electronics. Their unique properties make them suitable for advanced and innovative semiconductor devices.
How are semiconductor glass substrates manufactured?
The manufacturing process of semiconductor glass substrates involves material preparation, cutting and shaping, surface treatment, patterning and etching, coating and layer deposition, and rigorous quality control and testing. Each step requires precise control and advanced technology to ensure the quality and performance of the substrates.