Professional Semiconductor IC substrate Manufacturer, we mainly produce ultra-small bump pitch IC/BGA substrate, ultra-small trace and ultra-small spacing are 9um/um. we do the the IC/BGA substrates from 2 layer to 20 layers.
Semiconductor IC substrate, referred to as IC substrate, is a key component used to assemble and connect integrated circuit (IC) chips. It provides support and a conductive path that allows various electronic components to connect to each other and ensures the proper operation of the entire circuit. The IC substrate plays the role of a bridge in the integrated circuit, connecting the chip with external circuits and providing the required power and signal transmission for the chip. Substrates are usually made of materials with good electrical conductivity, such as organic materials, ceramics or metal substrates, to ensure good electrical performance and thermal management capabilities.
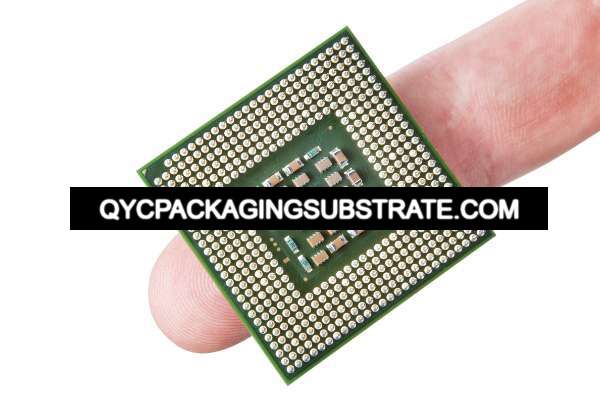
Semiconductor IC substrate Manufacturer
In integrated circuits, IC substrates perform multiple key functions. First, it provides physical support and protection for the chip to ensure that the chip is not damaged during use. Secondly, the IC substrate provides power and ground connections for the chip so that the chip can supply power normally. In addition, the substrate also carries signal transmission and data exchange between chips, promoting the coordinated work of the entire circuit system. In general, the semiconductor IC substrate is a key component of the integrated circuit, and its role covers the functions of supporting, connecting and managing various components in the circuit.
What are the different types of semiconductor IC substrates?
In modern PCB engineering, semiconductor IC substrates play a vital role. Their different types provide diverse solutions for various application needs. The following are several common semiconductor IC substrate types, their characteristics and application areas:
Organic substrates are a type that use organic materials as substrates. They are often flexible and cost-effective, making them ideal for many consumer electronics products. Organic substrates are widely used in portable electronic devices such as mobile phones, tablets, and smart wearable devices.
Ceramic substrates are known for their high thermal conductivity and reliability. They are often used in automotive electronics, aerospace and military applications due to their ability to provide stable performance in extreme environments. Ceramic substrates are also commonly used in circuit designs that require high-frequency operation and low losses.
Metal core substrates have excellent thermal conductivity properties and are ideal for high power applications. They are typically made from aluminum- or copper-based materials to efficiently conduct heat from the integrated circuit to the external environment. Metal core substrates are commonly used in LED lighting, power modules, automotive electronics and other fields.
Flexible substrates are a flexible substrate type that can be bent or curled to fit specific design requirements. They are usually made from flexible polymer materials, common materials include polyimide (PI) and polyester film. Flexible substrates play an important role in fields such as medical devices, wearable technology, and aerospace.
Each type of semiconductor IC substrate has unique characteristics and advantages and is suitable for different application scenarios. Selecting the appropriate substrate type is critical to ensuring the performance and reliability of electronic devices.
What are the advantages of semiconductor IC substrates?
Semiconductor IC substrates play a vital role in modern electronic devices, and their adoption brings many advantages and effectively improves the performance and reliability of electronic devices. Here are a few key advantages of semiconductor IC substrates:
First, semiconductor IC substrates have excellent thermal management capabilities. As electronic devices continue to shrink in size and improve performance, thermal management has become an increasingly prominent issue. The semiconductor IC substrate effectively disperses and conducts the heat generated by the device through good heat dissipation design and material selection, keeping the device within the normal operating temperature range, thus improving the stability and reliability of electronic devices.
Second, semiconductor IC substrates provide excellent electrical performance. The selection of substrate materials and the optimization of the manufacturing process enable the semiconductor IC substrate to have lower signal loss and electromagnetic interference, thus ensuring the stable operation of electronic devices and high-quality signal transmission. In addition, the semiconductor IC substrate can also provide good electrical isolation, effectively reduce crosstalk and interference between devices, and improve the anti-interference ability of the entire circuit system.
In addition, the use of semiconductor IC substrates contributes to the miniaturization and weight reduction of electronic devices. Compared with traditional PCB boards, semiconductor IC substrates usually have higher integration and more compact designs, allowing electronic devices to accommodate more functions and components without increasing volume and weight, satisfying the needs of modern electronic products. The need for miniaturization and lightweighting.
In addition, semiconductor IC substrates offer higher reliability and long-term stability. High-quality substrate materials and precise manufacturing processes ensure that semiconductor IC substrates have a low failure rate and a long service life, reduce the maintenance cost and failure rate of electronic equipment, and improve the market competitiveness of the entire product.
To sum up, semiconductor IC substrates have significant advantages in thermal management, electrical performance, miniaturization and reliability, providing a solid foundation for performance improvement and product innovation of electronic devices. With the continuous advancement of technology and changing market demands, semiconductor IC substrates will play a more important role in the future electronics field.
Why are semiconductor IC substrates superior to other boards?
In today’s fast-paced electronics world, semiconductor IC substrates have increasingly become an indispensable key component in electronic design. Compared with traditional PCB boards, semiconductor IC substrates have many unique advantages, making them the first choice in many applications. Here are a few of the main reasons why semiconductor IC substrates outperform other boards:
Semiconductor IC substrates enable higher integration and component density. Its compact structure allows it to accommodate more components in a smaller space through miniaturization and multi-layer stacking, thereby enabling more complex circuit designs.
Compared with traditional PCB boards, semiconductor IC substrates have better performance and reliability. Its material selection, manufacturing process and structural design have been carefully optimized, with lower signal loss, higher signal transmission rate and better electrical characteristics, ensuring stable operation and long-term reliability of the circuit.
Semiconductor IC substrates effectively manage and conduct heat, preventing damage to integrated circuits due to overheating. Its excellent thermal conductivity and heat dissipation design make it perform well in high-power applications, such as high-performance computers, automotive electronics and communication equipment.
Semiconductor IC substrates are highly adaptable and customizable and can meet the specific needs of different application scenarios. Manufacturers can customize designs according to customer requirements, including material selection, layer thickness, aperture size and circuit board shape, to provide customers with personalized solutions.
Although semiconductor IC substrates may be more expensive to manufacture, their overall overall cost-effectiveness is often higher given their performance advantages and long-term stability. In applications requiring high performance, high reliability and long life, it is often a wiser choice to choose semiconductor IC substrates.
In general, semiconductor IC substrates have become an indispensable and important part of modern electronic design through their advantages such as high integration, excellent performance, good thermal management capabilities, degree of customization, and cost-effectiveness. With the continuous development and innovation of technology, it is believed that semiconductor IC substrates will continue to play an important role in the future and bring more breakthroughs and progress to the electronic field.
What is the manufacturing process of semiconductor IC substrates?
The manufacturing process of semiconductor IC substrates is a complex and precise process involving multiple critical steps to ensure high quality, reliability and performance of the final product. The manufacturing process of semiconductor IC substrates and its key steps will be introduced below.
The first step in manufacturing a semiconductor IC substrate is to prepare the substrate material. Common substrate materials include fiberglass reinforced resin (FR-4), ceramics and metals. These materials require precision processing and processing to ensure smooth surfaces, accurate dimensions, and compliance with subsequent process requirements.
After the substrate preparation is completed, the next step is to build the stack. This step involves stacking layers of different materials together to build the structure of the substrate. These layers include conductive layers, insulating layers, and other functional layers such as pads, connecting lines, etc. Layer build-up is typically accomplished through layer-by-layer stacking, lamination, and hot pressing processes.
Once the layup is established, the base plate is formed and drilled. The forming process cuts the substrate into the required shape and size and drills holes where necessary for subsequent component installation and connection.
After forming and drilling, the substrate needs to be metallized. This step involves coating the surface of the substrate with a layer of metal, usually copper, to form conductive layers and connecting lines. Metallization can be achieved by techniques such as chemical deposition, vacuum coating or electroplating.
After metallization is complete, patterning follows. This step uses photolithography and etching processes to define patterns and connection lines on the metallization layer to form the final circuit pattern. Patterning is one of the key steps in semiconductor IC substrate manufacturing, determining the shape and connections of the final circuit.
After patterning is completed, the substrate requires surface treatment to improve its soldering performance and corrosion resistance. Common surface treatment methods include hot-dip tin, spray tin, chemical gold plating, etc. These treatments can provide good soldering performance during the soldering process and protect the substrate surface from corrosion and oxidation.
The final step is to inspect and test the manufactured semiconductor IC substrate. Through visual inspection, electrical performance testing and functional testing, we ensure that the substrate meets the specifications and can work properly. This step is key to ensuring product quality and reliability and is the final hurdle in the manufacturing process.
Through the above key steps, semiconductor IC substrates can be manufactured throughout the entire process from raw materials to final products, providing a reliable foundation and guarantee for the manufacturing of electronic products.
What are the applications of semiconductor IC substrates?
As a key component of electronic components, semiconductor IC substrates are widely used in various industries and play an irreplaceable role. The following are the main applications and roles of semiconductor IC substrates in different fields:
In the field of consumer electronics products, such as smartphones, tablets, smart watches, etc., semiconductor IC substrates play a vital role. They provide these devices with powerful data processing capabilities and efficient circuit connections, allowing the devices to have faster response times and more stable performance.
In the automotive industry, semiconductor IC substrates are widely used in vehicle electronic systems, such as engine control units, vehicle entertainment systems, driving assistance systems, etc. These substrates can ensure the reliability and stability of automotive electronic equipment and improve the intelligence and safety performance of automobiles.
In the aerospace and defense fields, semiconductor IC substrates play key tasks and are used in high-end equipment such as navigation systems, communication equipment, and radar systems. They have properties such as radiation resistance and high temperature resistance, and can operate stably in extreme environments, ensuring the reliability and safety of the equipment.
The medical device industry also has growing demand for semiconductor IC substrates. These substrates are used in medical imaging equipment, life monitoring equipment, treatment equipment, etc., providing the medical industry with high-precision data processing and signal transmission capabilities, helping medical personnel diagnose and treat diseases more accurately.
In the field of communication, semiconductor IC substrates are widely used in key equipment such as communication base stations, optical fiber communication equipment, and network routers. They provide high-speed data transmission and stable network connections, supporting the development and popularization of modern communication technology.
As a core component of modern electronic technology, semiconductor IC substrate plays a vital role in various industries. They not only improve the performance and reliability of electronic equipment, but also promote technological innovation and development in various industries. With the continuous advancement of technology, the application prospects of semiconductor IC substrates will be broader, making greater contributions to the development of human society.
Where can I find semiconductor IC substrates?
When looking for reliable semiconductor IC substrates, you can consider a variety of sourcing channels to ensure you meet your project needs and get a high-quality product. Here are some ways for you to consider:
The preferred choice is to purchase products directly from semiconductor IC substrate manufacturers. This ensures access to proven and reliable products, as well as the opportunity to work with manufacturers to customize specific needs. As our supplier, we offer various types and specifications of semiconductor IC substrates to meet your project requirements.
Electronic component distributors typically have extensive supply chain networks that offer multiple brands and models of semiconductor IC substrates. By working with a reputable distributor, you gain access to diverse choices and flexible delivery services.
Online marketplaces and platforms such as Alibaba, Amazon, eBay, etc. provide a wide selection of electronic component suppliers and products. You can browse and compare products from different suppliers on these platforms to find the semiconductor IC substrate that meets your needs.
Attending professional trade shows and events in the electronics industry is a great way to learn about the latest product and technology trends. By exhibiting at an exhibition or conference, you can communicate directly with various semiconductor IC substrate manufacturers and suppliers, establish cooperative relationships, and obtain the product information you need.
You can find reliable semiconductor IC substrate suppliers with recommendations from peers, partners, or professionals. This way you can get direct recommendations and reviews, which helps reduce risk in the selection process.
Choosing the right purchasing channel is crucial to obtain high-quality semiconductor IC substrates. By working directly with manufacturers, leveraging electronic component distributors and online marketplaces, attending industry events, and more, you can find the products that best fit your project needs and ensure your project runs smoothly. As a supplier of our company, we are committed to providing high-quality semiconductor IC substrate products and excellent customer service, and you are welcome to contact us for more information.
What is the quote for semiconductor IC substrate?
In the semiconductor IC substrate market, price is an important consideration, and it is usually affected by multiple factors. Let’s take a closer look at the semiconductor IC substrate quotes and the factors behind the prices.
The price of semiconductor IC substrates is typically determined based on a range of factors. First of all, the type of substrate will directly affect its price. For example, organic substrates, ceramic substrates, metal core substrates and flexible substrates have different costs. In addition, the specification and size of the substrate will also have an impact on the price. Large, complex substrates tend to be more expensive than small, simple substrates.
In addition to the characteristics of the substrate itself, the manufacturing process is also one of the important factors in price. Advanced manufacturing processes may increase production costs, thereby raising the price of the substrate. In addition, customized designs and special requests will also affect the price. If a customized manufacturing process or special materials are required, this often results in a price increase.
Substrate type: Different types of substrates have different cost structures. For example, ceramic substrates are generally more expensive than organic substrates because they have higher thermal conductivity and better electrical properties.
Specifications and dimensions: The specifications and dimensions of the substrate directly affect the usage of raw materials and manufacturing costs. Larger, more complex substrates tend to be more expensive.
Manufacturing processes: Advanced manufacturing processes such as precision machining, multi-layer stacking and special surface treatments may increase production costs.
Customized requirements: If customers require customized designs or special requirements, such as special materials or special processes, this will usually result in a price increase.
To sum up, the quotation of semiconductor IC substrates is affected by many factors, including substrate type, specification size, manufacturing process, and customization requirements. For customers, choosing the right substrate type and specification, and fully considering cost factors during the manufacturing process, will help to obtain a product that fits the budget and meets the needs.
Frequently Asked Questions
Are semiconductor IC substrates compatible with different types of integrated circuits?
Yes, semiconductor IC substrates are designed to be compatible with various types of integrated circuits. They provide a versatile platform for mounting and interconnecting components, accommodating diverse circuit designs and configurations.
What environmental considerations should be taken into account during substrate selection?
When selecting semiconductor IC substrates, it’s essential to consider environmental factors such as temperature, humidity, and exposure to chemicals or contaminants. Substrates with appropriate thermal conductivity, moisture resistance, and corrosion protection should be chosen to ensure reliability in different operating conditions.
How long can semiconductor IC substrates be expected to last in typical operating conditions?
The longevity of semiconductor IC substrates depends on factors such as material quality, manufacturing processes, and operating conditions. High-quality substrates manufactured using robust techniques can endure prolonged use in typical operating environments, contributing to the overall reliability and lifespan of electronic devices. Regular maintenance and proper handling also play a role in extending substrate lifespan.
What are the common failure modes associated with semiconductor IC substrates?
Common failure modes related to semiconductor IC substrates include thermal stress-induced cracking, delamination, solder joint failures, and electrical connectivity issues. These failures can occur due to factors such as improper design, manufacturing defects, excessive heat generation, mechanical stress, or environmental degradation. Implementing proper design practices, material selection, and quality control measures can mitigate these failure risks.
Can semiconductor IC substrates be customized to specific design requirements?
Yes, semiconductor IC substrates can be customized to meet specific design requirements, such as size, shape, material properties, and electrical characteristics. Manufacturers offer customization options to accommodate diverse application needs and optimize performance, ensuring compatibility with different circuit layouts and integration techniques.