Semiconductor Load Board Manufacturer.A Semiconductor Load Board Manufacturer specializes in producing high-quality load boards used for testing semiconductor devices. These boards are essential for ensuring the performance and reliability of integrated circuits (ICs) by providing accurate electrical connections during testing processes. The manufacturer designs, fabricates, and tests load boards to meet stringent industry standards, catering to various applications such as consumer electronics, automotive, and telecommunications. Their expertise ensures precise and reliable testing, contributing to the advancement of semiconductor technology.
Semiconductor load boards are crucial components in the testing and validation of semiconductor devices. They serve as interfaces between the device under test (DUT) and the test equipment, ensuring accurate and efficient measurement of the device’s electrical characteristics. This article delves into the structure, materials, manufacturing process, applications, and advantages of semiconductor load boards, emphasizing their importance in the semiconductor industry.
What is a Semiconductor Load Board?
A semiconductor load board is a specialized printed circuit board (PCB) designed to connect semiconductor devices to automated test equipment (ATE) for testing and validation purposes. These boards are tailored to accommodate the specific pin configurations and signal requirements of the DUT, enabling thorough and precise testing of various parameters such as voltage, current, frequency, and timing.
Structure of Semiconductor Load Boards
The structure of semiconductor load boards is meticulously engineered to ensure optimal performance and reliability during testing. Key structural elements include:
Semiconductor load boards often feature HDI designs to support high pin counts and fine-pitch components. This ensures accurate signal routing and minimal signal loss.
These boards typically have multiple layers to facilitate complex signal routing and power distribution. The number of layers can vary depending on the complexity of the DUT and the testing requirements.
The traces on semiconductor load boards are designed with precision to maintain signal integrity and minimize crosstalk. This is especially important for high-frequency signals.
The boards are equipped with test sockets and connectors that match the pin configurations of the DUT. These components ensure secure and reliable connections during testing.
Dedicated power and ground planes are incorporated into the design to provide stable power delivery and reduce electromagnetic interference (EMI).
Effective thermal management is essential to prevent overheating during testing. Semiconductor load boards may include thermal vias, heat sinks, and other cooling mechanisms.
Materials Used in Semiconductor Load Boards
The choice of materials for semiconductor load boards is critical to ensure performance, reliability, and durability:
High-quality FR4, Rogers, and other advanced laminates are commonly used as substrate materials. These materials offer excellent electrical insulation, mechanical strength, and thermal stability.
Copper is the primary conductive material used for traces and pads due to its superior electrical conductivity. In some cases, additional surface finishes like gold or silver are applied to enhance performance and reliability.
Advanced dielectric materials are used to provide insulation between conductive layers while maintaining low signal loss.
Solder mask is applied to protect the traces from oxidation and short circuits, while the silkscreen layer is used for labeling and identification purposes.
Manufacturing Process of Semiconductor Load Boards
The manufacturing process of semiconductor load boards involves several precise steps to ensure high quality and performance:
The design phase involves creating detailed schematics and layouts using computer-aided design (CAD) software. Signal integrity and thermal simulations are performed to optimize the board design.
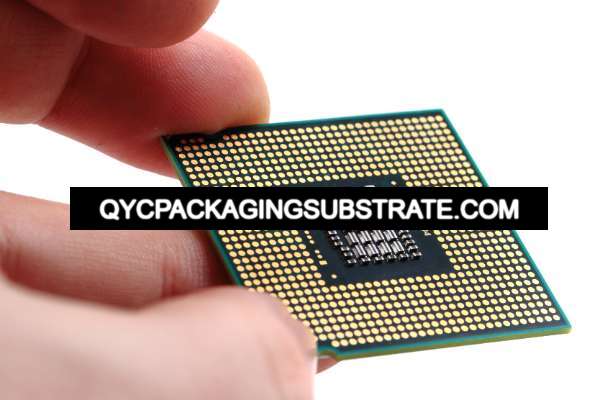
Semiconductor Load Board Manufacturer
Appropriate substrate and conductive materials are selected based on the design requirements and performance specifications.
Multiple layers of substrate and conductive materials are laminated together to form a multilayer structure. Precise alignment and control are essential to ensure the layers are properly bonded and aligned.
The circuit patterns are created using photolithographic processes. A photosensitive film (photoresist) is applied to the copper surface, exposed to ultraviolet (UV) light through a mask, and developed to reveal the desired circuit patterns. The PCB is then etched to remove the unwanted copper, leaving behind the traces and pads.
Vias are drilled into the PCB to create vertical electrical connections between different layers. These holes are then plated with copper to establish conductive pathways.
Surface finishes such as ENIG (Electroless Nickel Immersion Gold) or immersion silver are applied to the contact pads to enhance solderability and protect the conductive traces from oxidation and corrosion.
The final PCBs undergo assembly, where test sockets, connectors, and other components are added. Rigorous testing, including signal integrity tests, impedance matching tests, and environmental stress tests, are conducted to ensure the PCBs meet the required performance standards.
Applications of Semiconductor Load Boards
Semiconductor load boards are used in various applications across the semiconductor industry:
Load boards are used to characterize the electrical properties of semiconductor devices, including voltage, current, frequency, and timing parameters. This helps in understanding the device’s performance and identifying any potential issues.
During the production process, semiconductor load boards are used for automated testing of devices to ensure they meet the required specifications. This includes functional testing, parametric testing, and reliability testing.
Load boards are used in failure analysis to diagnose and identify the root causes of device failures. This helps in improving the design and manufacturing processes.
Semiconductor load boards are essential for quality control and assurance, ensuring that only devices that meet the required standards are shipped to customers.
In research and development, load boards are used to test and validate new semiconductor designs and technologies, enabling innovation and advancement in the field.
Advantages of Semiconductor Load Boards
Semiconductor load boards offer several advantages that make them indispensable in the semiconductor industry:
The precise design and high-quality materials used in semiconductor load boards ensure accurate and reliable testing of semiconductor devices.
Load boards can be customized to accommodate a wide range of device configurations and testing requirements, making them suitable for various applications.
Automated testing using load boards enhances testing efficiency, reducing the time and effort required for device validation.
The robust construction and advanced materials used in load boards ensure long-term reliability and durability, even in demanding testing environments.
By enabling thorough and accurate testing, load boards help in identifying and addressing issues early in the production process, reducing the risk of costly recalls and failures.
FAQ
What materials are commonly used in semiconductor load boards?
Common materials used in semiconductor load boards include high-quality FR4, Rogers, and other advanced laminates for substrates, copper for conductive traces, and additional surface finishes like gold or silver to enhance performance and reliability.
How do semiconductor load boards improve testing efficiency?
Semiconductor load boards improve testing efficiency by providing a reliable and accurate interface between the device under test (DUT) and automated test equipment (ATE). This enables thorough and precise testing, reducing the time and effort required for device validation.
Can semiconductor load boards be customized for different devices?
Yes, semiconductor load boards can be customized to accommodate different device configurations and testing requirements. This includes designing the board layout, selecting appropriate materials, and adding specific components such as test sockets and connectors.
What are the common applications of semiconductor load boards in the industry?
Semiconductor load boards are commonly used for device characterization, production testing, failure analysis, quality control, and research and development. They play a critical role in ensuring the performance, reliability, and quality of semiconductor devices.