Semiconductor substrate Manufacturer.High speed and high frequency material packaging substrate manufacturing. We have more than 100 engineers and 20,000 employees, using the world’s advanced production equipment, can produce 20 layers of semiconductor packaging substrate, fast time, reasonable price.
Semiconductor substrates form an integral foundation in the field of electronic engineering, providing essential support for a diverse array of chips and electronic components. Possessing a distinctive structure and multifunctional capabilities, these substrates have evolved into indispensable elements within modern electronic devices. Their pivotal role lies in facilitating circuit connections and optimizing overall performance.
Nature of Semiconductor Substrates
A semiconductor substrate serves as a foundational structure designed to bear electronic components, typically crafted from semiconductor materials like silicon. Functioning as both the skeletal framework and circuit carrier, these substrates form an essential part of the electronic landscape.
Importance of Semiconductor Substrates
Support for Electronic Components:These substrates furnish a stable platform for mounting electronic components, delivering fixed positions and structural support for chips, transistors, and more.
Facilitating Electronic Connectivity: Wires and interconnected layers on the substrate intricately link individual electronic components, culminating in the creation of a comprehensive circuit—a fundamental necessity for the proper functioning of electronic devices.
Facilitating Electrical Flow: The conductive layers intricately woven into semiconductor substrates facilitate the seamless movement of electrical current throughout a circuit, fostering unobstructed communication and cooperation among electronic components.
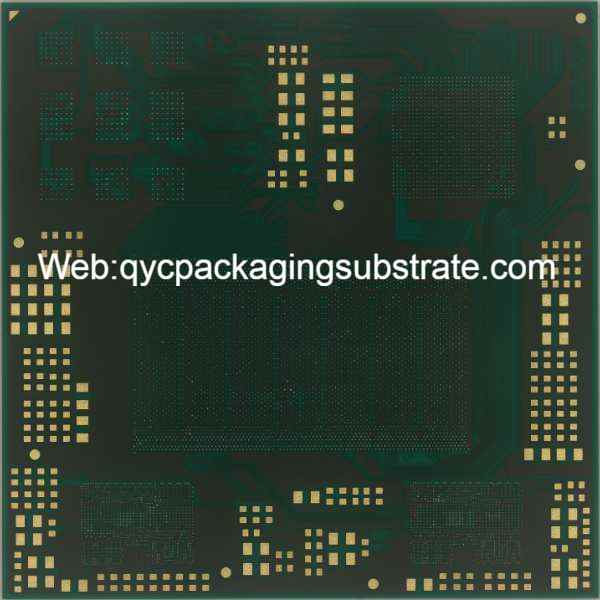
Semiconductor substrate manufacturer
In the dynamic landscape of modern electronics, semiconductor substrates emerge as a vital cornerstone, providing steadfast support to the technological ecosystem that permeates our daily existence. By delving into the intricacies of their composition, diverse types, and manufacturing methodologies, we glean a heightened appreciation for their pivotal role in electronic engineering. Whether applied in the realms of computing, communication systems, or medical apparatus, these substrates assert themselves as indispensable contributors to our technological trajectory, fortifying a resilient foundation for continual innovation.
What types of semiconductor substrates are there?
The versatility of semiconductor substrates is instrumental in modern electronics, prominently featuring rigid, flexible, and hybrid rigid-flexible substrates. Each variant offers distinct advantages and characteristics tailored to specific application scenarios, addressing diverse needs for electronic components across various fields.
Rigid Substrate
Comprising robust materials like fiberglass-reinforced epoxy (FR-4) or metal substrates, rigid substrates excel in applications demanding high mechanical strength and stability. Examples include computer motherboards, servers, and certain industrial equipment. The rigid structure enhances reliability in mounting electronic components, exhibiting adaptability to varying environmental conditions.
Flexible Substrate
Flexible substrates utilize materials with pliability, such as polyester film or polyimide. Ideal for scenarios requiring bending, curling, or limited space, these substrates find applications in mobile devices, curved displays, and medical sensors. Their thin, lightweight, and highly flexible nature enable electronic products to adeptly conform to intricate design requirements, enhancing overall system performance.
Hybrid Rigid-Flexible Substrate
Hybrid rigid-flexible substrates leverage the combined advantages of both rigid and flexible substrate types, offering designers increased versatility. This substrate category plays a crucial role in situations requiring the seamless integration of rigid and flexible components, notably in applications such as camera modules, foldable electronics, and specific military applications. Its adaptability in design and multi-level structure enable the realization of complex circuit configurations within constrained spatial environments.
Each semiconductor substrate type presents its unique value in different application areas. Rigid substrates stand out in terms of stability and mechanical strength, while flexible substrates offer great potential in bending and lightweight design. As a combination of the two, hybrid rigid-flexible substrates have become an ideal choice for some special needs. During the evolution of semiconductor substrates, these diverse choices provide electronic engineers with a wider range of solutions and promote continuous innovation in electronic product design.
What are the advantages of semiconductor substrates over other circuit boards?
Semiconductor substrates have become indispensable in the design of contemporary electronic devices, distinguished by their notable advantages over traditional circuit boards. Notably, they offer high integration, superior electrical performance, and exceptional reliability, making semiconductor substrates the preferred choice in today’s dynamic electronics landscape.
The standout characteristic of high integration is a key feature that distinguishes semiconductor substrates from conventional circuit boards. Unlike their counterparts, semiconductor substrates can accommodate a greater number of components and circuits within a smaller space. This heightened integration capability facilitates the creation of more compact and lightweight designs in modern electronic products, providing an ideal solution for the miniaturization and weight reduction requirements across various equipment types.
Secondly, semiconductor substrates excel in electrical properties. Leveraging unique materials and manufacturing processes, they provide outstanding electrical conductivity and signal transmission efficiency. This is particularly crucial for contemporary high-speed, high-frequency electronic devices such as communication equipment and computer systems. The electrical properties of semiconductor substrates ensure not only the stable operation of equipment but also robust support for the implementation of advanced functions.
Reliability stands as another prominent advantage of semiconductor substrates. In intricate electronic systems, equipment often contends with diverse environmental and usage conditions. With a robust structure and meticulous material selection, semiconductor substrates enhance the circuit’s resilience to factors like vibration, shock, and environmental variations. Consequently, they elevate the reliability and stability of the entire system, a critical consideration for fields demanding exceptionally stable equipment, such as medical devices and aerospace systems.
In conclusion, semiconductor substrates present cutting-edge solutions for the design and production of contemporary electronic devices, capitalizing on their benefits of high integration, superior electrical performance, and remarkable reliability. In a time characterized by the quest for smaller, lighter, and more potent electronic products, the incorporation of semiconductor substrates furnishes electronic engineers with adaptable and efficient design choices, propelling the ongoing advancement of electronic technology.
Why Choose a Semiconductor Substrate Manufacturer?
In the contemporary landscape of electronic design, the selection of a semiconductor substrate manufacturer holds pivotal importance, directly influencing the performance, reliability, and overall quality of the end product. Professional semiconductor substrate manufacturers stand out with distinct advantages, primarily characterized by their commitment to high quality, tailored solutions, and cutting-edge technology and processes.
First and foremost, products from professional semiconductor substrate manufacturers consistently exhibit excellent quality. Given the critical role of quality in electronic equipment, these manufacturers adhere to stringent quality control processes and employ advanced production equipment at every manufacturing stage. This comprehensive approach encompasses material selection, processing, process optimization, and final product testing. Compared to other circuit board options, professional manufacturers enjoy greater credibility in delivering high-quality, reliable electronic solutions.
Secondly, semiconductor substrate manufacturers possess the capability to offer customized solutions, addressing specific needs of individual customers. The diversity in electronic device designs necessitates tailored substrates. Leveraging extensive experience and flexible production capabilities, professional manufacturers adeptly customize designs and production according to customer requirements. This customization spans beyond adjusting appearance sizes, extending to circuit layouts, hierarchical structures, and material selections. Through this personalized approach, customers can better align with their unique design requirements, ultimately enhancing product performance and competitiveness.
To sum up, the meticulous choice of a professional semiconductor substrate manufacturer stands as a crucial stride in ensuring the success of electronic products. The amalgamation of high quality, tailored solutions, and advanced technologies and processes equips customers with a steadfast and innovative foundation to thrive in the dynamic and ever-evolving electronics market.
What is the manufacturing process of semiconductor substrates?
Layering (Cascading)
Following material selection, the layering stage commences. This critical step involves stacking different layers of materials in accordance with the design specifications. The stack-up design considers the circuit structure, interlayer connections, and the final product’s shape. The layering process is pivotal for ensuring both the structural integrity and functionality of the semiconductor substrate.
Chemical treatment
After lamination is complete, the substrate undergoes a series of chemical treatments to form circuit patterns and connections. This includes processes such as chemical etching and metallization. The goal of chemical treatment is to form precise circuit patterns on the surface of the substrate to ensure accurate and reliable connections between circuits.
Metalization
Metalization stands as a critical stage in semiconductor substrate manufacturing, involving the deposition of metal onto the circuit pattern through methods like evaporation or electroplating. Beyond merely connecting circuits, metallization enhances conductivity and ensures the stability of signal transmission. Maintaining precise process control during metallization is imperative to achieve uniformity and secure the adhesion of the metal layer.
Emphasizing the importance of process control, it serves as the linchpin throughout the semiconductor substrate manufacturing journey. Rigorous adherence to control standards at each stage is essential to guarantee product performance and reliability. Any deviation in the process could result in incorrect circuit connections, performance degradation, or even product failure.
Through meticulous design and unwavering process control, semiconductor substrates have become ubiquitous in modern electronics, furnishing a steadfast and reliable foundation for a diverse array of electronic devices.
In what fields are semiconductor substrates used?
Semiconductor substrates, as a crucial component in modern electronic products, have demonstrated exceptional utility across diverse fields. Their flexibility and high integration features position them as indispensable technical support in the realms of communications, medical, automotive, military, and beyond.
In the communication sector, semiconductor substrates play a pivotal role, offering reliable electrical connections and highly integrated circuits for various devices, ranging from smartphones to communication base stations. This not only enhances equipment performance but also facilitates more compact and lightweight designs.
In the medical field, semiconductor substrates are instrumental in providing highly integrated circuit solutions for medical monitoring equipment, imaging systems, and implantable medical devices. Their reliability and precision contribute to the fulfillment of the medical industry’s requirements for real-time monitoring and accurate control.
The automotive manufacturing industry is witnessing an increasing application of semiconductor substrates, spanning from engine control units to entertainment systems. These substrates enable smarter and more efficient automotive designs by incorporating highly integrated features. This, in turn, contributes to the reduction of automotive electronic system sizes, overall performance enhancement, and support for advanced driver assistance systems.
In the realm of military technology, semiconductor substrates stand as the linchpin for a myriad of sophisticated electronic devices. Renowned for their reliability and remarkable customizability, these substrates find ideal application in crucial military systems such as radar arrays, missile control units, and communications equipment. The utilization of semiconductor substrates not only facilitates ongoing innovation but also propels the constant enhancement of military technology.
In a broader context, semiconductor substrates play an extensive role across various facets of contemporary society. Their flexibility and highly integrated features not only drive the continual evolution of electronic products but also establish a robust foundation for the technological progress across diverse industries. For electronics engineers, possessing a profound understanding of the characteristics and application domains of semiconductor substrates is indispensable for steering innovation and addressing real-world challenges.
Where to find semiconductor substrates?
A common avenue for locating semiconductor substrate suppliers involves leveraging specialized electronic component marketplaces. These platforms convene suppliers from across the globe, presenting a diverse array of semiconductor substrates. Through these marketplaces, users can effortlessly peruse products from various suppliers, compare prices, and delve into information about their quality certifications. This approach provides a spectrum of options to align with specific project requirements.
An alternative and effective strategy involve directly engaging with the semiconductor substrate manufacturer. Cultivating a direct relationship with the manufacturer opens avenues to more extensive and customized services, offering heightened technical support. Manufacturers typically possess the capability to deliver flexible solutions, tailoring designs to precise project specifications and ensuring the product attains the utmost standards of quality and performance. This direct collaborative approach has the potential to reduce errors in information transmission and enhance overall communication efficiency.
In addition, online platforms are also a convenient way to find semiconductor substrates. Many suppliers publish their product information on online platforms, which allows you to easily search, compare and purchase the required semiconductor substrates through the Internet. Online platforms often provide detailed product specifications, technical parameters and user reviews to help you make an informed choice.
For our company, it is advisable to prioritize establishing direct collaborations with reputable and seasoned semiconductor substrate manufacturers.
A comprehensive consideration of these elements will safeguard the reliability of semiconductor substrates, laying a robust foundation for our company’s projects. Through a meticulous procurement process, companies can foster enduring relationships, contributing collaboratively to the successful realization of projects.
How to obtain quotations for semiconductor substrates?
In the realm of contemporary electronic engineering, the pricing dynamics of semiconductor substrates emerge as a pivotal consideration. This phase not only intertwines with the financial dimensions of a project but also wields a direct influence on the overall implementation strategy. Therefore, engineers and project leaders must possess an in-depth understanding of the elements that shape semiconductor substrate quotations and skillfully navigate the quoting process to facilitate effective project planning.
Several factors contribute to these quotations, encompassing elements such as material costs, the intricacy of the manufacturing process, customization requirements, project scale, and the prevailing dynamics of market supply and demand. A nuanced understanding of these factors is instrumental in accurately gauging the true cost of a project and establishing a reasonable budget early in the design phase. For instance, the adoption of highly intricate manufacturing processes or the utilization of specialized materials may escalate costs, while the advantages of cost-effectiveness may be realized through mass production.
Securing quotations for semiconductor substrates entails establishing robust communication channels with reputable manufacturers or suppliers. When selecting a partner, considerations extend beyond price, encompassing factors such as the manufacturer’s experience, technical prowess, delivery timelines, and after-sales support. Opting for a reliable manufacturer not only ensures product quality but also facilitates the smooth progression of the entire project.
Securing quotes efficiently involves a strategic process. Firstly, it is essential to thoroughly articulate project requirements and specifications, encompassing details such as materials, processes, quantities, and other relevant specifics. This precision enables suppliers to furnish more accurate estimates. Secondly, maintaining open and responsive communication with the manufacturer is crucial. Addressing queries promptly and making adjustments based on feedback ensures a smoother quoting process. Additionally, consulting multiple manufacturers for quotes facilitates effective comparison, aiding in the identification of the most cost-effective option.
Notably, when seeking a quotation for semiconductor substrates, the focus should extend beyond the price alone. A comprehensive evaluation of overall costs, quality assurances, and production cycles is imperative. In practical terms, a supplier offering a lower price but with inconsistent quality or unpredictable delivery times may pose substantial risks to the success of the project.
Frequently Asked Questions (FAQs) for Conductor Substrate Manufacturers
Semiconductor substrates, as key components in modern electronics, can raise a number of questions when choosing a manufacturer. Below are answers to some frequently asked questions to help you better understand the features and services of semiconductor substrate manufacturers.
What are the common types of semiconductor substrates?
Semiconductor substrates come in several common types, including rigid, flexible, and hybrid rigid-flexible substrates. Rigid substrates are ideal for applications demanding heightened mechanical strength, ensuring robust performance in such scenarios. On the other hand, flexible substrates are well-suited for environments requiring bending and flexibility, offering adaptability to accommodate various form factors and applications.
What are the key factors in selecting a semiconductor substrate manufacturer?
Critical considerations for selecting a manufacturer encompass their expertise, technical proficiency, stringent quality control measures, delivery timeliness, and the provision of robust after-sales services. Opting for a manufacturer that prioritizes these factors is instrumental in ensuring the success of a project.
What performance parameters of semiconductor substrates need attention?
Performance parameters encompass factors such as dielectric constant, interlayer withstand voltage, and conductive properties, among others. These parameters wield a direct impact on the functionality of semiconductor substrates within specific applications.
How to ensure that semiconductor substrate manufacturing meets quality standards?
Manufacturers are advised to obtain ISO quality management certification and implement a rigorous quality control system. Regular inspections and testing protocols are essential to guarantee that semiconductor substrates adhere to international quality standards.
What are the differences between rigid and flexible semiconductor substrates in applications?
Rigid substrates excel in applications demanding substantial mechanical strength, making them ideal for scenarios where robust structural support is essential. On the other hand, flexible substrates are well-suited for designs involving curved surfaces and bending requirements, commonly found in mobile devices and various other fields.
How to deal with thermal management issues in semiconductor substrate design?
Addressing thermal management challenges typically involves optimizing the design of heat dissipation structures and selecting materials with excellent thermal conductivity. Manufacturers frequently offer tailored cooling solutions to effectively manage and mitigate heat-related issues.
What are the customization options for semiconductor substrates?
Manufacturers commonly provide an array of customization options for semiconductor packaging substrates, encompassing considerations such as the number of layers, materials, stacking methods, surface treatments, and more. These options are designed to cater to the unique requirements of diverse projects, allowing for tailored solutions that align precisely with the specifications of each individual undertaking.