Semiconductor Substrate Manufacturer.As a leading semiconductor substrate manufacturer, we specialize in producing high-performance substrates for advanced electronic applications. Our cutting-edge manufacturing processes and stringent quality control ensure that our substrates provide exceptional reliability, thermal management, and signal integrity, meeting the demands of the latest semiconductor technologies. We are committed to innovation and excellence, making us a trusted partner in the semiconductor industry.
Semiconductor substrates are the foundational materials upon which semiconductor devices are built. These substrates are crucial in the electronics industry, providing the platform for the integration of various electronic components and circuits. They play a vital role in the performance, reliability, and miniaturization of electronic devices, making them essential in modern technology.
What are Semiconductor Substrates?
Semiconductor substrates are wafers or layers of semiconductor materials that serve as the base for fabricating semiconductor devices. The most commonly used semiconductor material is silicon, but other materials such as gallium arsenide (GaAs), silicon carbide (SiC), and indium phosphide (InP) are also used, depending on the application and desired properties.
High electron mobility and high-frequency performance.
Used in applications such as RF (radio frequency) and microwave devices, optoelectronics, and high-speed digital circuits.
High thermal conductivity and high breakdown voltage.
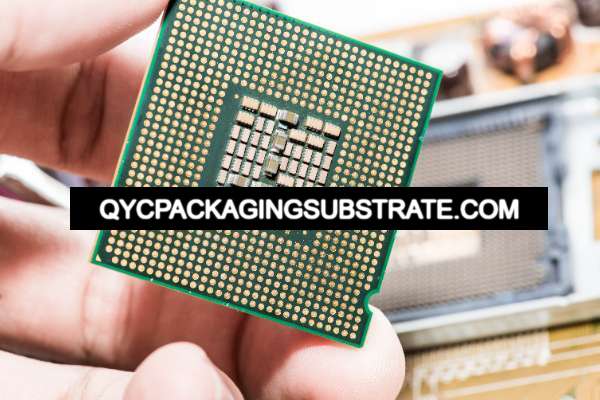
Semiconductor Substrate Manufacturer
Ideal for high-power and high-temperature applications, such as power electronics and LED lighting.
Excellent electron mobility and high-frequency characteristics.
Used in high-speed and high-frequency applications, including telecommunications and photonics.
Design Reference Guide for Semiconductor Substrates
Designing semiconductor substrates involves several critical considerations to ensure optimal performance and reliability. The following sections outline the key aspects of designing these advanced substrates:
The quality of the substrate material is determined by the crystal growth process:
Czochralski Process: A common method for growing large, single-crystal silicon ingots. This process ensures high purity and defect-free crystals.
Bridgman-Stockbarger Technique: Used for growing compound semiconductors like GaAs. It involves melting the material and then slowly cooling it to form a single crystal.
Hydride Vapor Phase Epitaxy (HVPE): Used for growing thick GaN (gallium nitride) layers, essential for high-power and high-frequency devices.
After crystal growth, the substrate material is processed into wafers:
Cutting and Slicing: Large ingots are sliced into thin wafers using precision saws.
Polishing: Wafers are polished to achieve a smooth, defect-free surface, essential for subsequent device fabrication.
Cleaning: Wafers are cleaned to remove any contaminants that could affect device performance.
What Materials are Used in Semiconductor Substrates?
Materials used in semiconductor substrates are selected for their specific properties and suitability for various applications:
Silicon (Si): Most commonly used due to its abundance, cost-effectiveness, and versatile properties.
Gallium Arsenide (GaAs): Used for high-speed and high-frequency applications due to its superior electron mobility.
Silicon Carbide (SiC): Preferred for high-power and high-temperature applications because of its excellent thermal and electrical properties.
Indium Phosphide (InP): Ideal for high-frequency and optoelectronic applications due to its excellent electron mobility and direct bandgap properties.
What Size are Semiconductor Substrates?
The size of semiconductor substrates varies depending on the application and manufacturing process:
Diameter: Common wafer diameters include 100mm, 150mm, 200mm, and 300mm. Larger diameters allow for more devices to be fabricated on a single wafer, improving cost efficiency.
Thickness: Wafer thickness typically ranges from 200 micrometers to 1 millimeter, depending on the material and intended use.
The Manufacturing Process of Semiconductor Substrates
The manufacturing process of semiconductor substrates involves several precise and controlled steps to ensure the highest quality and reliability:
The initial step involves growing high-purity single crystals of the desired semiconductor material. This is achieved using techniques like the Czochralski process for silicon and the Bridgman-Stockbarger technique for compound semiconductors.
The grown crystals are sliced into thin wafers using precision saws. The slicing process must be controlled to produce wafers of uniform thickness and minimal surface damage.
Wafers are polished to achieve a mirror-like surface finish, essential for high-quality device fabrication. After polishing, wafers are thoroughly cleaned to remove any residual contaminants.
To tailor the electrical properties of the substrate, doping may be introduced. Doping involves adding small amounts of impurities to the semiconductor material to control its electrical conductivity.
Wafers undergo rigorous testing and inspection to ensure they meet stringent quality standards. This includes measuring thickness, flatness, and electrical properties, as well as inspecting for any defects.
The Application Area of Semiconductor Substrates
Semiconductor substrates are used in a wide range of high-performance electronic applications:
The most common application of semiconductor substrates is in the fabrication of integrated circuits. Silicon wafers serve as the foundation for building complex ICs used in computers, smartphones, and countless other electronic devices.
Silicon carbide (SiC) substrates are used in power electronics for applications requiring high efficiency, high voltage, and high temperature. These substrates are used in electric vehicles, renewable energy systems, and industrial power supplies.
Gallium arsenide (GaAs) and indium phosphide (InP) substrates are used in RF and microwave devices for applications such as satellite communications, radar systems, and wireless networks. These materials offer superior performance at high frequencies.
Semiconductor substrates are essential in optoelectronics, where they are used to fabricate devices such as LEDs, laser diodes, and photodetectors. Materials like GaAs and InP are commonly used due to their direct bandgap properties, which are ideal for light emission and detection.
Silicon substrates are widely used in MEMS devices, which integrate mechanical and electrical components at the microscale. Applications include sensors, actuators, and microfluidic devices.
What are the Advantages of Semiconductor Substrates?
Semiconductor substrates offer several advantages that make them indispensable in high-performance electronic applications:
High Purity and Quality: Advanced crystal growth techniques ensure high purity and defect-free substrates, essential for reliable device performance.
Tailored Electrical Properties: Doping and material selection allow for precise control over electrical properties, enabling the design of specialized devices.
Thermal Management: Materials like SiC offer excellent thermal conductivity, critical for high-power and high-temperature applications.
Versatility: Semiconductor substrates can be used in a wide range of applications, from consumer electronics to industrial and aerospace systems.
Scalability: The ability to produce large-diameter wafers improves manufacturing efficiency and reduces costs for high-volume production.
FAQ
What are the key considerations in selecting a semiconductor substrate material?
Key considerations include the material’s electrical, thermal, and mechanical properties, compatibility with the intended device fabrication process, cost, and availability. The application requirements, such as operating frequency, power levels, and environmental conditions, also play a crucial role in material selection.
How does the doping process affect the properties of semiconductor substrates?
Doping involves adding impurities to the semiconductor material to control its electrical conductivity. This process allows for the creation of n-type or p-type regions, which are essential for the operation of semiconductor devices. The concentration and type of dopants determine the material’s electrical characteristics, such as carrier concentration and mobility.
What are the typical applications of silicon carbide (SiC) substrates?
Silicon carbide (SiC) substrates are commonly used in power electronics for applications requiring high efficiency, high voltage, and high temperature. Examples include electric vehicle powertrains, renewable energy inverters, industrial power supplies, and high-frequency RF devices.
How do semiconductor substrates contribute to the performance of optoelectronic devices?
Semiconductor substrates, particularly those with direct bandgap properties like GaAs and InP, are critical for optoelectronic devices. These materials allow for efficient light emission and detection, making them ideal for applications such as LEDs, laser diodes, and photodetectors. The substrate’s quality and properties directly impact the performance, efficiency, and reliability of these devices.