SHDBU Substrates Manufacturer. High speed and high frequency material packaging substrate manufacturing. Advanced packaging substrate company.
Packaging substrates are essential elements within the contemporary electronics sector, serving as fundamental materials that facilitate the connection between chips and external circuits. They bear the dual responsibilities of structural support and signal transmission. Essentially, these substrates provide a platform for tightly integrating chips with circuit boards or other external components, enabling signal transmission and electrical connectivity.
In electronic devices, packaging substrates play a pivotal role, not only providing physical support but also serving as a vital medium for circuit functionality realization. Through these substrates, chips can interact with the external environment, enabling various functions such as data processing, signal amplification, and power conversion. Consequently, the quality and performance of packaging substrates directly impact the stability and functionality of entire electronic systems.
Analogous to a bridge, packaging substrates bridge the significant gaps between the chip’s minute size and high integration level, and the complex layout of the circuit board. They ensure effective signal transmission and reliable electrical connections while also managing thermal concerns by dissipating heat to maintain optimal chip operating temperatures.
Overall, packaging substrates are indispensable in electronic products, serving as crucial components that connect chips and circuit boards. They provide a robust foundation for electronic device performance, stability, and functionality. Therefore, comprehending the definition and role of packaging substrates is vital for understanding the development trends and technological advancements in the modern electronics industry.
What are the types of packaging substrates?
Packaging substrates are vital components in the electronics industry, offering tailored options for various applications. One common type is FR-4, made of fiberglass and epoxy resin, prized for its resilience to high temperatures, mechanical strength, and favorable electrical properties. Due to its affordability and easy processing, FR-4 is extensively used in general electronic equipment and consumer electronics.
High-frequency RF substrates, such as those crafted from PTFE or PTFE glass fiber composites, are highly valued for their reduced dielectric constant, minimal signal attenuation, and consistent signal propagation. These characteristics make them particularly well-suited for applications like wireless communications, radar, and satellite systems.
Ceramic substrates, employing materials like alumina or boron nitride, exhibit exceptional stability at elevated temperatures and superior thermal conductivity. Their appropriateness for power amplifiers, sensors, and high-frequency circuits arises from their capabilities in high-frequency environments, power handling, and material density.
Thin film substrates, composed of stacked layers of thin film materials, possess thin, lightweight, and flexible properties. Tailored for compact and lightweight electronic devices such as smartphones, tablets, and wearables, they facilitate highly integrated and miniaturized applications.
What are the advantages of packaging substrates?
Packaging substrates offer numerous advantages over traditional circuit boards, driving their increasing popularity in the modern electronics industry. They enable higher levels of integration for multiple chips and electronic components, optimizing circuit system performance and efficiency in compact spaces, particularly crucial for high-density electronic devices. Additionally, these substrates utilize materials with superior thermal conductivity, like ceramic or metal substrates, effectively dissipating chip-generated heat to enhance system reliability and lifespan.
Their flexible design and manufacturing processes cater to specific application needs, employing advanced technologies for intricate circuit layouts and component integration, ensuring customized solutions for diverse customer requirements. Furthermore, packaging substrates employ high-quality materials and precise manufacturing techniques for stable and reliable signal transmission, minimizing attenuation and interference, making them suitable for demanding applications such as communications and high-frequency RF fields.
The high integration level and customizable design of packaging substrates streamline system costs and development cycles. Simplifying product design and manufacturing through component reduction and streamlined connections improves production efficiency, ultimately saving time and expenses. In essence, packaging substrates have become indispensable in the electronics industry, offering integrated solutions, superior thermal management, flexible design options, reliable signal transmission, and cost-effective manufacturing processes for various electronic equipment designs.
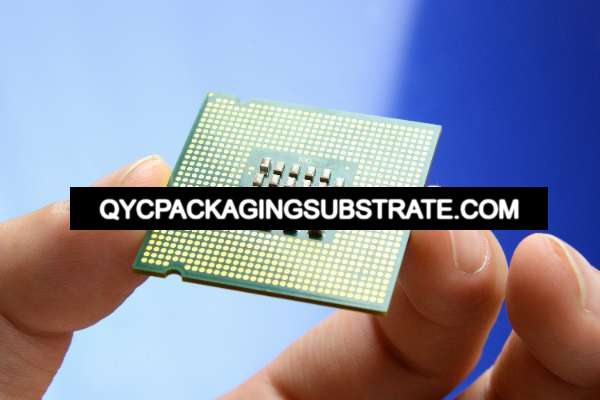
SHDBU Substrates
Why choose package substrate instead of other boards?
Packaging substrates offer several distinct advantages over traditional circuit boards, making them increasingly favored in modern electronics manufacturing. Firstly, they boast enhanced integration and performance, packing more functions into a smaller footprint compared to conventional boards. This compact design not only boosts device performance but also meets the rising demands for technical sophistication.
Secondly, packaging substrates excel in thermal management. With electronic devices becoming more densely packed and powerful, efficient heat dissipation is crucial. By optimizing designs and materials, packaging substrates effectively dissipate heat, enhancing device stability and reliability.
Moreover, their smaller size and weight align with the trend towards sleeker, lighter electronic products. This not only reduces overall device dimensions but also enhances portability.
Furthermore, packaging substrates offer superior signal integrity. Their precise design and shorter signal transmission paths minimize interference and signal degradation, ensuring stability and reliability.
In summary, packaging substrates outshine traditional circuit boards in integration, thermal management, size, weight, and signal integrity. Given the current trajectory of electronic products favoring high performance, slim profiles, and miniaturization, packaging substrates emerge as the superior choice for various applications.
How to manufacture packaging substrates?
The manufacturing process of packaging substrates is a multifaceted and precise endeavor involving several crucial steps to ensure the quality and functionality of the end product. Firstly, the substrate must undergo meticulous design and planning, accounting for factors like size, shape, internal wiring, and intended usage. Material selection is paramount, with options including FR-4, ceramics, and metals, each catering to specific applications and environmental conditions.
Pre-treatment precedes formal manufacturing, focusing on surface flatness and cleanliness through methods like chemical cleaning and surface treatment to enhance adhesion and solderability. Printing plays a vital role, applying a conductive layer to form circuit patterns using techniques like screen printing or inkjet printing. Electroplating follows to boost conductivity and corrosion resistance by depositing metal (typically copper) onto the substrate surface via electrolysis.
The process involves shaping and cutting to achieve the desired shape and size, utilizing mechanical or laser cutting methods for precision. Soldering and assembly follow, with components like chips soldered onto the substrate. Thorough testing and quality control measures culminate the process. Meticulous technical oversight and process control are essential to meet quality standards in packaging substrate manufacturing. Dependable substrates are crafted through meticulous design and rigorous manufacturing protocols to meet diverse industrial needs.
What are the application areas of packaging substrates?
Packaging substrates are indispensable components in the contemporary electronics sector, finding extensive applications across various industries and domains. They fulfill crucial roles in different fields:
Communications Industry: Packaging substrates are pivotal in the manufacturing of diverse communication equipment like wireless base stations, communication satellites, routers, and switches. They facilitate high-speed data transmission, ensure consistent signal stability, and optimize circuit layout to uphold the reliability and efficacy of communication networks.
Automotive Sector: Within automotive manufacturing, packaging substrates are integral to crafting vehicle electronic systems such as engine control units (ECUs), in-car entertainment setups, and navigation systems. These systems demand operation under severe environmental conditions and mandate exceedingly high standards for stability and endurance. Packaging substrates provide steadfast electrical connections and signal transmission, coupled with exceptional temperature resistance, thereby enabling dependable performance of in-vehicle electronic systems.
Medical Field: Packaging substrates find extensive usage in fabricating medical equipment and devices such as medical imaging machinery, pacemakers, and blood glucose monitors. These devices necessitate precise electronic control and signal processing to ensure accurate diagnosis and treatment. Packaging substrates offer steadfast and dependable circuit connections and signal transmission in medical equipment, concurrently adhering to the stringent safety and reliability requirements of the medical industry.
Industrial Control Domain: Packaging substrates are employed in manufacturing diverse industrial automation equipment and control systems like PLCs (programmable logic controllers), sensors, and actuators. These devices are required to operate reliably in harsh industrial environments and achieve precise control and monitoring functionalities. Packaging substrates furnish reliable circuit connections and signal transmission in industrial control equipment, while possessing robust anti-interference capabilities and durability to cater to the demands of the industrial automation sector.
In summary, packaging substrates assume critical roles across various domains including communications, automotive, medical, and industrial control. They not only ensure stable and dependable circuit connections and signal transmission but also underpin the operation of numerous high-performance and high-reliability electronic equipment and systems.
Where can I find the packaging substrate?
When sourcing packaging substrates, it’s imperative to secure a dependable supplier. When in the market for a packaging substrate provider, SHDBU Substrates Manufacturer stands out as the top choice.
As a crucial link between the chip and external circuits, the packaging substrate’s quality and dependability significantly impact the overall performance of electronic devices. When selecting a supplier, consider these compelling reasons why SHDBU is the optimal choice:
Extensive Manufacturing Expertise: SHDBU possesses significant experience in manufacturing packaging substrates. We not only adhere to industry standards but also prioritize innovation to meet evolving market needs.
Dedication to Quality: We are committed to delivering high-quality packaging substrate products by employing advanced materials and manufacturing methods, surpassing industry standards for performance and reliability.
Competitive Pricing with Uncompromised Quality: While prioritizing product excellence, SHDBU remains committed to offering competitive prices. Understanding the significance of cost-effectiveness to your business, we diligently strive to present appealing pricing without compromising on quality.
When seeking a packaging substrate supplier, entrust SHDBU Substrates Manufacturer as your reliable partner. Our wealth of professional manufacturing experience, commitment to high-quality products, bespoke solutions, technical expertise, and competitive pricing ensure you receive the expected packaging substrate, precisely tailored to your project’s requirements. Get in touch with us, and let’s collaborate to propel your project to success.
How do I contact SHDBU to get a package substrate quote?
Obtaining a quote for packaging substrate is crucial, and reaching out to SHDBU is the initial step towards securing an accurate quotation. Here are convenient ways to get in touch with us:
Visit our official website and navigate to the contact page. Fill in your name, email address, contact number, along with your requirements and inquiries. Our dedicated customer service team will promptly reach out to furnish you with a comprehensive quotation and technical assistance.
You have two options to get in touch with our sales team. Firstly, you can email your inquiry to our official sales address for a swift response with quotation details. Alternatively, feel free to call our customer service hotline to speak directly with one of our experienced representatives. They will provide personalized consultation services and competitive quotations regarding packaging substrates.
SHDBU also has official accounts on some social media platforms. You can send us messages or messages through these platforms, and our team will respond promptly and provide the quotation information you need.
SHDBU actively engages in electronics industry exhibitions and events, providing direct channels for clients to connect with our team, discuss their requirements, and receive on-the-spot quotations. Whether through exhibition interactions or other means of contact, we are committed to delivering professional and top-quality services. Our dedicated team will offer comprehensive quotation details tailored to your specific needs, crafting packaging substrate solutions that align perfectly with your requirements. Thank you for choosing SHDBU, and we eagerly anticipate the opportunity to collaborate with you!
What are the common problems with packaging substrates?
How does warping affect package substrates, and what causes it?
Warping, or bowing, can occur due to thermal stress during manufacturing or operation. This issue may lead to misalignment and affect the overall integrity of the electronic assembly.
Are there specific challenges related to high-frequency package substrates?
Yes, high-frequency package substrates may encounter signal integrity issues, such as impedance mismatches or signal loss. Design considerations and the use of specialized materials can address these challenges.
What are the advantages of Package Substrates over traditional boards?
Package substrates offer several advantages over traditional boards, including higher integration and performance, better thermal management, smaller size and weight, and improved signal integrity. These factors make them an ideal choice for a wide range of electronic applications.
Where can one find reliable Package Substrates?
For reliable Package Substrates, it’s essential to partner with reputable manufacturers like SHDBU. They offer high-quality products and customized solutions tailored to specific requirements.
How can I contact SHDBU for Package Substrate quotes and inquiries?
To inquire about Package Substrate quotes or for any other inquiries, you can reach out to SHDBU through their official website or contact their customer service team directly.
What are some common issues associated with Package Substrates?
Common issues related to Package Substrates may include manufacturing defects, thermal management challenges, signal integrity issues, and compatibility concerns. Addressing these issues often requires collaboration between manufacturers and customers to find suitable solutions.