Showa Denko MCL-E-700G package substrate Manufacturer. FC BGA package substrates and ABF base package substrates supplier, we have made the FC BGA substrates with 22 Layers with microtrace and microgap.
As technology continues to advance, electronic devices are becoming smaller and more powerful. In this rapidly growing field, the Showa Denko MCL-E-700G Kit Baseboard plays a vital role. This article will delve into the key features of this advanced technology and its importance in the future of electronics. MCL-E-700G substrate provides key support for the design and manufacturing of modern electronic equipment with its high reliability, excellent performance and flexibility, and promotes continuous innovation and development in the electronic field.
Is this Showa Denko MCL-E-700G package substrate?
When it comes to modern electronic manufacturing and packaging technology, Showa Denko MCL-E-700G packaging substrate is undoubtedly a high-profile innovative product. As an advanced technology from Showa Denko, the MCL-E-700G packaging substrate is not just an ordinary printed circuit board (PCB), but a precision-engineered substrate that exhibits excellent performance and reliability.
The uniqueness of the MCL-E-700G packaging substrate is that it adopts Showa Denko’s advanced technology, combining precision craftsmanship and high-quality materials, making it one of the first choices in the electronics field. In modern electronic devices, packaging substrates carry electronic components and provide electrical connections and mechanical support, so their performance and reliability are critical.
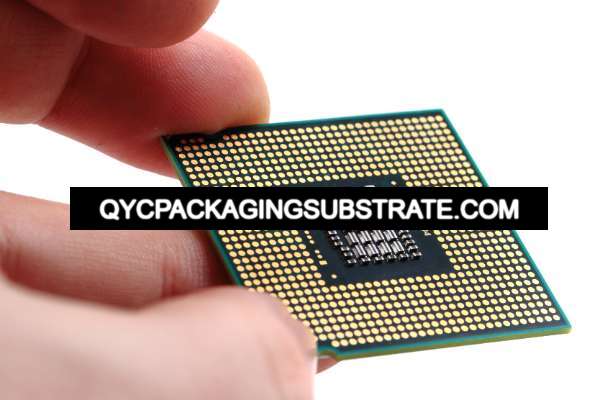
Showa Denko MCL-E-700G package substrate Manufacturer
The MCL-E-700G package substrate has excellent characteristics, including high reliability, good thermal stability and excellent electrical performance. This is due to the high-quality materials and precision manufacturing processes used, allowing the MCL-E-700G packaging substrate to perform well in a variety of environments and application conditions.
In addition, the MCL-E-700G packaging substrate also has flexible design features and can be customized according to the requirements of specific applications to meet customer needs. Whether in consumer electronics, automotive electronics, aerospace or medical equipment and other industries, MCL-E-700G packaging substrate has demonstrated its excellent applicability and stability.
Overall, the MCL-E-700G packaging substrate is not only an excellent electronic substrate, but also a strong testament to Showa Denko’s continued innovation in the electronics field. Its emergence provides new possibilities for modern electronic manufacturing, provides key support for the performance and reliability of various electronic devices, and will surely play an important role in future development.
Showa Denko MCL-E-700G package substrate design Reference Guide.
In the field of modern electronics, MCL-E-700G packaging substrate has become a core component of many high-end electronic products. To fully realize its benefits and ensure optimal performance and reliability, engineers need to follow a series of key design principles and considerations. Here are some important takeaways from the MCL-E-700G package substrate design reference guide:
Material selection
First of all, pay attention to selecting suitable materials, including high-performance fiberglass substrates, high thermal conductivity copper foil, and high-temperature resistant pad materials. The choice of these materials will directly affect the stability and durability of the substrate.
Hierarchical design
Reasonable hierarchical structure design is the key to ensuring the stability of signal transmission. Engineers need to consider the layout and distribution of signal layers, power layers, ground layers, etc. to minimize signal interference and electromagnetic radiation.
Wiring plan
When designing wiring, you need to follow the principle of signal integrity, ensure that the signal transmission path is as short and straight as possible, and avoid cross-coupling and crosstalk.
Thermal management
For high-power electronic devices, thermal management is critical. Engineers need to design effective heat dissipation structures to ensure that devices operate within a safe temperature range and avoid overheating damage.
Package design
Package selection and design have a significant impact on the performance and reliability of the entire circuit. Engineers need to choose the appropriate packaging form based on actual needs and consider the connection and fixation methods.
Mechanical strength
During the design process, the mechanical strength of the substrate also needs to be taken into consideration to ensure that it can withstand the shock and vibration of the external environment while protecting the internal circuitry from damage.
Testing and Validation
Finally, after the design is completed, strict testing and verification are required to ensure that the performance of the substrate meets the design requirements, and at the same time, potential problems are discovered and solved in a timely manner.
By following the above design principles and considerations, engineers can better take advantage of the MCL-E-700G packaging substrate to achieve optimal performance and reliability of electronic products. At the same time, continuous practice and experience accumulation will also provide valuable lessons for design work and promote the continuous progress and innovation of electronic technology.
What material is used in Showa Denko MCL-E-700G package substrate?
The MCL-E-700G packaging substrate is an innovative technological achievement that Showa Denko is proud of. Its excellent performance is due to the use of a series of high-quality materials.
First of all, the MCL-E-700G packaging substrate uses high-performance glass fiber as the base material. Glass fiber has excellent mechanical strength and insulation properties, can maintain stability in high temperature and high pressure environments, and provides reliable support and protection for electronic equipment.
Secondly, the packaging substrate uses high-quality copper as the conductive layer material. Copper has good electrical and thermal conductivity and can effectively transmit current and dissipate heat, ensuring stable operation and efficient work of the circuit.
In terms of pad layer, the MCL-E-700G package substrate uses carefully designed soldering materials. These pad layers can ensure a solid connection between the electronic components and the packaging substrate, while also having good corrosion resistance and heat resistance, making the welding process more reliable and stable.
In addition, the MCL-E-700G packaging substrate also uses a silk screen layer for marking and protection. This layer covers the surface of the substrate and can print identification information or patterns. It also protects the surface of the substrate from mechanical damage and chemical corrosion.
To sum up, the high-quality materials used in the MCL-E-700G packaging substrate include high-performance glass fiber, high-quality copper, carefully designed pad layers and silk screen layers. The selection and application of these materials ensure the stability of the packaging substrate Robustness and durability provide reliable guarantee for the efficient operation of modern electronic equipment.
What size are Showa Denko MCL-E-700G package substrate?
As an innovative product of Showa Denko, the MCL-E-700G packaging substrate has excellent flexibility in size and specifications, allowing it to adapt to a variety of different application scenarios. Whether it requires small, finely designed electronic equipment or large, complex applications, the MCL-E-700G packaging substrate can meet the needs.
In terms of small design, the MCL-E-700G packaging substrate can provide compact size and is suitable for applications that require compact space and high integration, such as smartphones, tablets, and wearable devices. Their sophisticated design and high reliability enable these devices to implement complex functions in a limited space and maintain stable performance.
For large and complex applications, MCL-E-700G packaging substrate is also capable. The various specifications and size options it provides can meet the needs for high-performance and high-reliability substrates in industrial control systems, medical imaging equipment, aerospace equipment and other fields. Whether it is high-speed data transmission or complex signal processing, the MCL-E-700G packaging substrate can provide reliable support.
In addition, the MCL-E-700G packaging substrate can also be customized in size and specification according to customer needs to meet the needs of specific applications. This customization flexibility makes the MCL-E-700G packaging substrate an ideal choice for a variety of electronic devices, whether it is mass production products or customized solutions.
To sum up, MCL-E-700G packaging substrates have diverse sizes and specifications and can be flexibly adapted to different application scenarios, providing a reliable foundation for the design and manufacturing of modern electronic equipment.
The Manufacturer Process of Showa Denko MCL-E-700G package substrate.
The manufacturing process of Showa Denko MCL-E-700G package substrate has been carefully designed and strictly executed to ensure the best level of quality and performance of the final product. Below are the detailed steps of the manufacturing process of this substrate:
Design
The first step in the manufacturing process is the design phase. At this stage, engineers use advanced computer-aided design (CAD) software to create design drawings of the MCL-E-700G package substrate. These design drawings take into account factors such as circuit layout, component location, signal transmission paths, etc. to ensure the performance and reliability of the final product.
Prototyping
Once the design is complete, the manufacturing team creates one or more prototype samples. These samples are used to test the effectiveness of the design and make necessary modifications and optimizations. The prototyping phase usually involves using rapid prototyping techniques such as 3D printing to quickly produce samples and conduct functional and reliability testing.
Etching
Once the prototype has been tested and confirmed to meet requirements, the next step is etching, the first step in series production. Etching is the removal of excess parts on the substrate through chemical etching or mechanical processing to form the outline and circuit pattern of the circuit board. The etching process of the MCL-E-700G package substrate requires highly precise control to ensure the accuracy and stability of the wires and connection points on the circuit board.
Drilling
After etching is complete, the next step is to drill holes. Drilling is done to create attachment points and mounting holes in the base plate. MCL-E-700G package substrates usually have complex wiring and multiple components, so the location and size of drill holes need to be precisely controlled to ensure accurate installation and reliable connection of components.
Assemble
The final step is assembly, which involves mounting the electronic components onto the MCL-E-700G package substrate and connecting them to form a complete circuit. The assembly process requires highly technical and precise operations to ensure that each component is installed correctly and connected correctly. Once assembly is complete, a series of tests may also be required to verify that the board functions and performs as expected.
Through these carefully designed and strictly executed manufacturing steps, Showa Denko MCL-E-700G packaging substrate ensures the best level of quality and performance of the final product, providing reliable solutions for a variety of applications.
The Application area of Showa Denko MCL-E-700G package substrate.
MCL-E-700G packaging substrate is widely used in various industries, mainly due to its excellent performance and multi-functional design. The following are application examples of MCL-E-700G packaging substrates in different fields:
Consumer Electronics
MCL-E-700G packaging substrate plays a key role in consumer electronics products, such as smartphones, tablets, home appliances, etc. Its high reliability and excellent electrical performance ensure the stable operation and long-term use of the equipment.
Car
Automotive electronic systems have extremely high requirements for reliability and performance. MCL-E-700G packaging substrates are widely used in the field of automotive electronics, covering engine control, in-vehicle entertainment, body control, etc. Its high temperature resistance, vibration resistance and corrosion resistance ensure reliability in harsh environments.
Aerospace
In the aerospace field, MCL-E-700G packaging substrates are widely used in control systems, communication systems and navigation systems for aircraft, satellites, missiles and other aerospace devices. Its lightweight design and reliability ensure the operation of aerospace devices under extreme conditions.
Medical equipment
Medical equipment has strict requirements on accuracy and reliability, and MCL-E-700G packaging substrates play a key role in medical imaging equipment, life support systems, implantable medical devices, etc. Its stable performance and low noise characteristics ensure the accuracy and safety of medical equipment.
Communication
Communication equipment has high requirements on the stability and speed of signal transmission. MCL-E-700G packaging substrate is widely used in base station equipment, optical fiber communication equipment, wireless network equipment, etc. in the communication industry. Its excellent high-frequency performance and anti-interference ability ensure stable connection and fast transmission of communication equipment.
Overall, the MCL-E-700G packaging substrate has demonstrated its excellent performance and versatility in different industries, making important contributions to the development of the modern electronics field.
What are the advantages of Showa Denko MCL-E-700G package substrate?
Showa Denko’s MCL-E-700G package substrate occupies an important position in modern electronic designs, offering advantages that extend far beyond traditional wiring methods. The advantages of the MCL-E-700G packaging substrate over other methods will be discussed in detail below:
First of all, the MCL-E-700G packaging substrate is compact. With the rapid development of electronic devices, the demand for smaller sizes is also increasing. The MCL-E-700G packaging substrate adopts advanced design and manufacturing technology, which can achieve a higher density circuit layout, thereby housing more functional modules in a smaller space, making it possible to make electronic products lightweight and portable. .
Secondly, the MCL-E-700G packaging substrate has high reliability. In many critical application fields, such as medical equipment, automotive electronics, etc., stable and reliable performance is crucial. The MCL-E-700G packaging substrate uses high-quality materials and precision manufacturing processes to ensure its stable operation under various environmental conditions, thereby effectively reducing product failure rates and maintenance costs.
Third, the MCL-E-700G packaging substrate is easy to mass produce. As market demand grows, fast and efficient production capabilities become critical. The MCL-E-700G packaging substrate adopts modern production technology, which can achieve large-scale mass production and ensure product supply stability and cost-effectiveness.
Finally, the MCL-E-700G packaging substrate offers flexible design features. In the design process of electronic products, flexibility is crucial. The MCL-E-700G packaging substrate can be customized and designed according to customer needs to meet the functional and performance requirements of different products. At the same time, it also supports multi-layer design, high-speed signal transmission and other features, providing engineers with greater design space and innovation possibilities.
In general, compared with other wiring methods, MCL-E-700G packaging substrate has significant advantages in volume, reliability, production and design, and is an important choice in modern electronic product design.
FAQ
What is the cost of the MCL-E-700G package substrate?
The cost of the MCL-E-700G package substrate depends on multiple factors, including size, material selection, production volume and design complexity. Typically, although the advanced performance and reliability of the MCL-E-700G packaging substrate will result in a relatively high initial cost, its long-term stability and excellent performance will bring you higher returns and value.
What is the environmental impact of the MCL-E-700G package substrate?
Showa Denko company is committed to sustainable development and environmentally friendly production. Environmentally friendly materials and production processes are used in the manufacturing process of the MCL-E-700G packaging substrate to reduce the impact on the environment. In addition, the efficient design and excellent performance of the MCL-E-700G packaging substrate help save energy and resources and reduce the generation of electronic waste.
How to recycle MCL-E-700G packaging substrate?
Because the MCL-E-700G package substrate uses a variety of materials, including fiberglass, copper, and pad layers, its recycling may require specialized processing methods. It is recommended to hand over the discarded MCL-E-700G packaging substrate to a professional electronic waste disposal agency, who will use appropriate methods to process and recycle it to minimize the impact on the environment.
What are the common faults when using MCL-E-700G packaging substrate?
Common MCL-E-700G package substrate failures may include poor welding, circuit short circuit, connection failure, etc. To avoid these problems, it is recommended to strictly follow the guidelines and conduct adequate testing and quality control during the design and manufacturing process. In addition, regular maintenance and inspection are also key to ensuring long-term stable operation of the MCL-E-700G package substrate.