We are a professional Substrate materials for optical packaging. we mainly produce ultra-small bump pitch substrate, ultra-small trace and spacing packaging substrate and PCBs.
Substrate materials for optical packaging encompass the fundamental elements utilized in the production and integration of optical components. These materials play a pivotal role in determining the performance, stability, and reliability of optical devices. The search for suitable substrate materials involves a thorough consideration of various factors, including optical performance, thermal characteristics, mechanical attributes, and manufacturing cost requirements. Several crucial considerations come into play when identifying substrate materials for optical packaging.
Foremost, optical performance stands as a primary criterion. The selected substrate materials must exhibit excellent transparency to facilitate unimpeded light propagation. Transparency, often contingent on wavelength, necessitates a careful assessment aligned with the specific optical application. Moreover, optical properties such as refractive index, scattering loss, and dispersion of the substrate material must be meticulously scrutinized to ensure alignment with the requirements of the optical element design.
During the operation of optical components, significant amounts of heat may be generated or absorbed. Therefore, choosing a substrate material with good thermal conductivity is critical to maintaining a stable temperature of the component. Matching of thermal expansion and contraction coefficients is also an important consideration to prevent deformation or damage of optical components due to temperature changes.
The mechanical properties of substrate materials play a crucial role in determining the longevity and stability of optical devices. It is imperative for these materials to possess adequate mechanical strength and hardness, capable of withstanding the diverse mechanical stresses encountered during manufacturing, assembly, and usage. Furthermore, the surface flatness and parallelism of the substrate material significantly impact the optical element’s performance, necessitating meticulous evaluation.
Beyond mechanical considerations, factors such as chemical stability, corrosion resistance, and manufacturing cost come into play. The substrate material must demonstrate resilience against chemical attacks to ensure the prolonged stability of the optical element. Simultaneously, manufacturing costs are pivotal economic considerations, particularly in large-scale production. Opting for substrate materials that strike a balance between cost-effectiveness and ease of processing becomes essential in this regard.
Through reasonable selection, we can ensure that optical components can work stably and reliably in various environments, while reducing costs during the manufacturing process and promoting the continuous development of optical packaging technology.
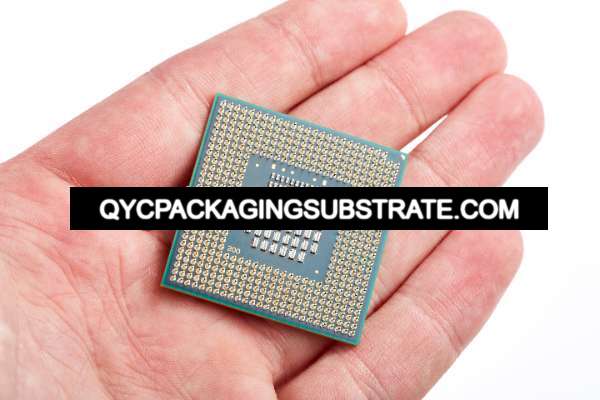
Substrate materials for optical packaging
What are the Materials Used in a Substrate materials for optical packaging?
In modern optoelectronic technology, the substrate material in optical packaging is a linchpin, exerting a direct influence on the performance, stability, and reliability of optical devices. Meticulous material selection for optical packaging substrates is paramount in attaining optical devices with high performance and efficiency. Several commonly employed materials for optical packaging substrates include:
Silicon Nitride
Silicon nitride stands out as an exceptional material for optical packaging substrates due to its commendable optical transparency and chemical stability. This substrate exhibits high transparency to both UV and visible light, coupled with outstanding mechanical strength and thermal stability. Given these qualities, silicon nitride finds extensive application in the packaging of various devices, including laser diodes (LD), laser diode arrays (LDA), and similar components.
Aluminum Nitride
Aluminum nitride stands out as a material boasting exceptional thermal conductivity, making it well-suited for effectively addressing the heat dissipation needs of high-power optoelectronic devices. With its impressive thermal conductivity and light transparency, aluminum nitride is a preferred choice for packaging applications in lasers, high-power LEDs, and other optical devices where efficient heat dissipation is crucial.
Glass base board
Optical glass stands out as a ubiquitous substrate material renowned for its exceptional transparency, especially within the visible light range. This material finds extensive application in packaging optical sensors, camera modules, and various devices, thanks to its superior clarity. Choosing from a range of glass types, such as borosilicate glass or soda-lime glass, is possible based on the specific needs of the application at hand.
Polymer substrate
Polymer substrates, exemplified by polyimide (PI) and polyetheretherketone (PEEK), offer notable advantages such as lightweight composition, high mechanical strength, and effective insulation properties. These materials find frequent application in flexible optical packaging scenarios, including the production of flexible displays, sensors, and similar devices.
Lithium niobate (LiNbO3)
on the other hand, stands out as a crystal material possessing nonlinear optical properties. Widely utilized in the realm of optical communications, lithium niobate serves as a key component in the manufacturing of optical modulators, wavelength converters, and other essential devices. Its outstanding optical characteristics establish it as a crucial substrate material in optical packaging applications.
Quartz substrate
Quartz has excellent optical transparency and chemical stability, and is also very transparent to ultraviolet light. Therefore, quartz substrates are often used in the packaging of some optical devices that require high wavelength stability, such as optical fiber coupling devices.
In the realm of optical packaging, the selection of substrate materials is a critical decision, requiring careful consideration of factors like transparency, thermal conductivity, mechanical strength, and chemical stability. This thoughtful selection is essential to ensure the stability and reliability of optical devices across diverse environmental conditions. Given that different materials offer distinct advantages, the process of choosing the appropriate substrate material becomes crucial in the design and manufacturing of optoelectronic devices.
What are the types of Substrate materials for optical packaging?
There are many types of substrate materials for optical packaging, and their selection is critical to the performance and stability of the optical device. Here are some common optical packaging substrate material types:
Silicon substrate
Silicon substrate is a common optical packaging substrate material with excellent optical properties and thermal conductivity. Silicon substrates are suitable for manufacturing micro-optical devices such as chip-scale packaging and integrated optical systems. Advantages include low cost, high reliability and good resistance to thermal expansion.
Silicon nitride substrate
Silicon nitride substrates exhibit exceptional thermal and chemical stability, making them ideal for optical packaging in elevated temperature environments. This substrate material plays a crucial role in the production of high-performance lasers, optoelectronic devices, and high-temperature sensors, among other applications.
Glass base board
Glass substrates are often used to manufacture optical lenses and windows, with good transparency and optical transmission properties. In some optical sensors and camera systems, glass substrates are widely used to protect and encapsulate optical components.
Quartz substrate
Quartz substrates have excellent optical transparency and chemical stability, which are crucial for manufacturing high-precision optical devices. Quartz substrates are commonly found in laser systems, fiber optic communications equipment, and other applications that require extremely high optical performance.
Polymer substrate
Polymer substrates are widely used in some optical packaging applications due to their lightweight, flexibility, and low cost. However, due to its relatively poor stability under high temperatures and strong light illumination, alternative materials may need to be considered in some high-performance optical systems.
Aluminum oxide substrate
Aluminum oxide substrates are mainly used in high-frequency and microwave devices in optical packaging. It has excellent thermal conductivity and electrical insulation properties, making it suitable for some optical components that are sensitive to temperature and frequency.
Niobium oxide substrate
Niobium oxide substrate is a special material used in the manufacture of optical filters and thin film optics. It has excellent transparency and transmission performance in the optical frequency range and is suitable for applications in some special wave bands.
In the design and manufacturing of optical packages, selecting the appropriate substrate material is critical, balancing factors such as optical performance, mechanical performance, thermal performance, and cost based on the requirements of the specific application. Various substrate materials play important roles in different optical applications and provide a solid foundation for the performance of optical devices.
When is It Ideal to Use Substrate materials for optical packaging?
In the field of optical packaging, selecting appropriate substrate materials is a key factor in ensuring the performance and reliability of optoelectronic devices. Suitable substrate materials are critical for transmission, scattering, thermal conductivity and mechanical stability of optical components. Here are some ideal times to use substrate materials in optical packaging:
First, when excellent optical transparency is required, the substrate material is critical. Optical transparency refers to the degree of transparency of a material to light wavelengths. For optoelectronic devices, this is the key to ensuring signal transmission efficiency. Some optical applications, such as lasers, optical communications and sensors, require substrates with good transparency to ensure high-quality transmission of optical signals.
Furthermore, the selection of an appropriate substrate material becomes crucial when exceptional thermal conductivity is a requirement. Optoelectronic devices often generate substantial heat during operation, and the inability to effectively dissipate this heat can lead to performance degradation or even device damage. Hence, choosing a substrate material with robust thermal conductivity properties becomes paramount to ensure reliable operation in high-temperature environments.
Additionally, under special environmental conditions, the substrate material selection gains heightened significance. Optical devices may be required to function in extreme conditions such as high or low temperatures, high humidity, etc. In such scenarios, opting for substrate materials with commendable chemical stability and mechanical strength is critical to guarantee the long-term stability and reliability of the device.
Moreover, in cases demanding micro- and nanoscale dimensional processing and manufacturing, the choice of substrate materials takes on added importance. Advanced optical devices, particularly micro-nano optical devices, impose stringent requirements on substrate surface flatness and process compatibility. Therefore, selecting substrate materials suited for micro-nano processing becomes indispensable to ensure the success of the manufacturing process and the stability of device performance.
In summary, the decision on which substrate material to use hinges on the specific application and operational environment of the optoelectronic device. In optical packaging, comprehensive consideration of factors such as optical performance, thermal performance, chemical stability, mechanical strength, and processing technology is essential to guarantee the stable and reliable functioning of the device in practical applications.
How is a Substrate materials for optical packaging Manufactured?
The manufacturing of substrate materials for optical packaging is a process involving complex processes designed to meet the high requirements for optical performance, mechanical properties and stability of optoelectronic devices. The following is a brief description of the manufacturing process of optical packaging substrate materials:
The initial and crucial phase in the production of optoelectronic devices involves the careful selection of substrate material. Commonly utilized substrate materials encompass silicon, glass, aluminum gallium nitride (Aluminum Nitride), and alumina (Alumina), each possessing unique properties tailored for specific optoelectronic applications. For instance, silicon substrates find widespread use in integrated optical devices, while aluminum gallium nitride stands out for its exceptional thermal conductivity properties, making it a preferred choice for high-power laser devices.
Subsequently, the manufacturing process commences with the meticulous preparation and cleansing of materials. This entails a thorough inspection of the original material, followed by cleaning procedures to eliminate impurities that might compromise performance. Manufacturers employ an array of chemical cleaning agents and high-purity solvents during this process to ensure the pristine purity of the substrate surface.
Next comes the formation and preparation of the substrate. This typically involves the process of applying, spin-coating, or spraying a coating to create the initial shape of the substrate. At this stage, for glass substrates, fusion or float can be used, while silicon substrates may need to be cut or polished.
Once the substrate is formed, the next steps may involve patterning and photolithography. This is a process of exposure to photoresist, masks, and UV light to define specific structures and patterns on a substrate. These structures may include optical waveguides, gratings, electrodes, etc.
After photolithography, an etching or etching step is usually required to remove the unwanted parts, leaving the designed structure. This may involve techniques such as dry etching, wet etching or ion beam etching.
Next comes the metallization step, where some areas are metalized to form conductive paths or connections. This usually involves metal deposition techniques such as evaporation, sputtering or electroplating.
Finally, encapsulation or coating is often required to protect the fabricated structure. This can be done using various methods such as chemical vapor deposition (CVD), physical vapor deposition (PVD) or coating with liquid encapsulation materials.
Strict quality control and testing are indispensable throughout the entire manufacturing process. By using a variety of instruments and techniques, manufacturers can inspect substrates for optical properties, mechanical strength, surface flatness, and more to ensure the final product meets design and specification requirements.
Overall, the manufacturing of optical packaging substrates is a complex, multi-step process that requires a high level of technology and sophisticated equipment. Different types of optoelectronic devices require different materials and manufacturing processes to meet their specific performance requirements.
Where to Find substrate materials for optical packaging?
Finding substrate materials in the field of optical packaging often requires consideration of multiple factors, including optical properties, thermal properties, mechanical properties, etc. The following is a comprehensive introduction to optical packaging substrate materials, including some common materials and their main characteristics.
First, the substrate material of the optical package should have good transparency to ensure the transmission effect of optical signals. Common transparent substrate materials include glass, quartz and transparent ceramics. Glass generally has good optical clarity, but may suffer from lower transmittance in certain wavelength ranges. Quartz is widely used in optical packaging in some high-temperature environments due to its excellent transparency and high temperature resistance. Transparent ceramics combine the characteristics of quartz and ceramics and have better optical and mechanical properties.
Secondly, the optical packaging substrate material should also have good thermal conductivity to ensure that the device can effectively dissipate heat when working. Metal substrates are a common choice, especially aluminum and copper substrates. Aluminum substrates have better thermal conductivity, while copper substrates have better thermal conductivity. This makes metal substrates widely used in the packaging of high-power optical devices.
In addition, for some special applications, substrate materials with special properties can also be considered. For example, some optical devices require electrical insulation properties, in which case a polymer substrate (such as polyimide PI) may be a suitable choice. Polyimide PI not only has excellent electrical insulation properties, but also has good high temperature resistance and is suitable for some high-demand optical packaging environments.
When looking for optical packaging substrate materials, consider working with a professional material supplier or manufacturer. We are professional suppliers, we usually provide various types of substrate materials, and we are also able to provide customized solutions according to the specific needs of our customers. When selecting materials, in addition to considering their optical, thermal and mechanical properties, cost, processing feasibility and manufacturing process requirements also need to be considered.
Overall, the selection of optical packaging substrate materials requires comprehensive consideration of multiple factors to ensure that the final optical device meets the application requirements in all aspects. By working with professional suppliers, more detailed consultation and customized solutions can be obtained to meet the needs of different optical packaging applications.