Substrate Packaging Manufacturer. the Package Substrate will be made with FR4, BT, Rogers, Isola, Showa Denko and Ajinomoto High speed materials.
In the context of PCB engineering, Substrate Packaging plays a vital role. It is not only a basic material that supports and connects electronic components, but also a key component to ensure the reliability and performance of electronic equipment.
Substrate Packaging can be understood as the basic support structure of electronic components, similar to the foundation of a building. It provides a platform that allows various electronic components, such as chips, resistors, capacitors, etc., to be reliably mounted and connected to each other. This connection is not only physical, but also involves the transmission of electrical signals and the dissipation of heat. Therefore, the design and quality of Substrate Packaging directly affects the performance and reliability of the entire electronic device.
In Substrate Packaging, material selection is crucial. It must have good thermal conductivity to effectively disperse the heat generated by electronic devices to avoid overheating and damaging components. At the same time, the material must have sufficient mechanical strength to support and protect electronic components from the impact and damage of the external environment. In addition, good electrical performance is also necessary to ensure the stability and reliability of signal transmission.
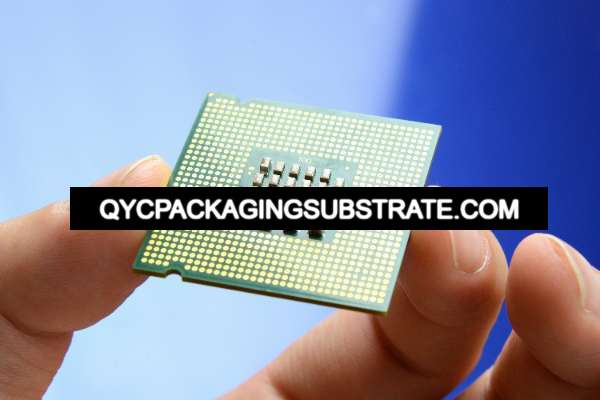
Substrate Packaging Manufacturer
In addition to material selection, the design and manufacturing process of Substrate Packaging are also crucial. It must accurately comply with the size and layout requirements of electronic components to ensure accurate and reliable connections between components. Every step in the manufacturing process, from substrate preparation to layer stacking to surface treatment, must be refined to ensure that the final Substrate Packaging output meets strict quality standards.
In general, Substrate Packaging is not just a simple material or structure, it is the core support and guarantee of electronic equipment. Through careful design and manufacturing, Substrate Packaging ensures excellent reliability and performance of electronic devices to meet evolving technology needs and user expectations.
What types of Substrate Packaging are there?
In PCB engineering, Substrate Packaging plays a key role, and different types of Substrate Packaging provide customized solutions for different needs. Let’s take a deeper look at the various types of Substrate Packaging and their suitability:
Organic substrates are a common type of Substrate Packaging, which is known for its cost-effectiveness and flexibility. For applications that require affordability and adaptability, organic substrates are ideal.
Ceramic substrates are favored for their excellent thermal conductivity and reliability. They play an important role in applications that require efficient heat dissipation and are sensitive to temperature changes, such as high-performance electronic devices and packaging.
Metal core substrates are another common type of substrate packaging and are particularly suitable for applications that require efficient heat dissipation. They have excellent thermal conductivity properties that help effectively transfer heat to the surrounding environment and maintain stable performance of the device.
Flexible substrates provide flexibility and moldability for applications with complex designs. Their ability to bend and twist makes them particularly suitable for devices that need to be mounted on curved or curved surfaces, such as flexible electronics and wearables.
These different types of Substrate Packaging have their own characteristics and can meet various needs and application scenarios. Choosing the right type of Substrate Packaging is critical to ensuring the performance and reliability of your electronic devices.
What are the advantages of Substrate Packaging?
Substrate Packaging offers multiple advantages in modern PCB engineering that make it the first choice for electronic design. The following are five major advantages of adopting Substrate Packaging:
Substrate Packaging effectively enhances the thermal management capabilities of electronic devices through its excellent thermal conductivity. This is essential to prevent electronic devices from overheating. By effectively transferring heat to the surrounding environment, Substrate Packaging ensures the stability and reliability of equipment during high-load operation.
Using Substrate Packaging can significantly improve the electrical performance of electronic devices and ensure high efficiency of signal transmission. By optimizing electrical connections and reducing signal attenuation, Substrate Packaging ensures stable signal transmission, thereby improving the overall performance and responsiveness of the device.
Substrate Packaging’s flexibility and high level of integration provide critical support for the development of compact and lightweight devices. Its miniaturized design makes electronic devices lighter and more portable, and can achieve more functions and performance in a limited space, meeting the urgent need for miniaturization of modern electronic products.
Substrate Packaging’s design and material selection are designed to increase the overall durability and longevity of electronic products. By using high-quality materials and advanced manufacturing processes, Substrate Packaging ensures reliable operation of equipment under various environmental conditions, thereby reducing failure rates and maintenance costs.
Compared to traditional electronic packaging methods, Substrate Packaging offers significant economic benefits without compromising quality. Its efficient manufacturing process and material utilization reduce manufacturing costs, while optimized thermal management and electrical performance reduce equipment operating costs, making Substrate Packaging an affordable choice.
In summary, Substrate Packaging, with its enhanced thermal management, improved electrical performance, miniaturization capabilities, higher reliability and cost-effectiveness, has become an ideal solution for modern electronic design and promotes the innovation and development of electronic products.
Why choose Substrate Packaging over other boards?
In modern electronic design, there are many obvious advantages to choosing Substrate Packaging instead of traditional PCB boards. First, Substrate Packaging excels in thermal efficiency. As electronic devices continue to shrink in size and power density increases, thermal management becomes a key challenge. Substrate Packaging effectively solves this problem through its excellent thermal conductivity and heat dissipation performance. In contrast, traditional PCB boards often cannot effectively handle high-temperature environments and can easily cause equipment to overheat, thus affecting its performance and lifespan.
Secondly, Substrate Packaging also performs well in terms of reliability. Because Substrate Packaging uses stronger and more durable materials, such as ceramic or metal core substrates, it has higher resistance to shock and shock, and can maintain stability in harsh working environments. This reliability is particularly important in critical applications such as aerospace and medical equipment. Traditional PCB boards may have high failure rates and maintenance costs in these areas.
Finally, Substrate Packaging also has clear advantages in terms of cost-effectiveness. Although Substrate Packaging may cost slightly more in terms of materials and manufacturing processes, its long-term performance and reliability often save users significant maintenance and replacement costs. In addition, Substrate Packaging enables higher integration and smaller size, saving space and material costs. Therefore, choosing Substrate Packaging is a wise choice for electronic designs that pursue long-term benefits and overall performance.
To sum up, compared with traditional PCB boards, Substrate Packaging has significant advantages in thermal efficiency, reliability and cost-effectiveness, making it the first choice for modern electronic design. By choosing Substrate Packaging, electronic equipment manufacturers can better meet market demand, improve product competitiveness, and provide users with a better user experience.
What is the manufacturing process of Substrate Packaging?
Substrate Packaging’s manufacturing process is a complex and delicate process designed to ensure the production of high-quality substrates that meet strict industry standards. Below we’ll dive into each of the key steps of this process.
The first step in manufacturing Substrate Packaging is substrate preparation. This includes selecting an appropriate substrate material, typically an organic, ceramic or metal core substrate. Substrates must undergo rigorous inspection and cleaning to ensure that the surface is free of impurities or defects, thus ensuring the quality and reliability of the final product.
Next comes the process of layer stacking, which is one of the key steps in the Substrate Packaging manufacturing process. At this stage, layers of different materials are stacked together to form the complete substrate structure. These layers can include conductive layers, insulating layers, and other functional layers, and each layer must be precisely positioned and stacked to ensure ultimate electrical performance and reliability.
After the layer stacking is complete, the substrate needs to undergo a precise surface treatment. This includes applying metallization layers, printed circuit patterns, machined hole locations, etc. The quality of the surface treatment is critical to the performance and reliability of the final product, so it must be very precise and meticulous.
Quality control is a vital part of the entire manufacturing process. From substrate preparation to layer stacking to surface treatment, each step must undergo rigorous inspection and testing to ensure compliance with industry standards and customer requirements. Any substandard products must be promptly discovered and reprocessed to ensure the quality and reliability of the final product.
Once Substrate Packaging manufacturing is complete, the final step is to conduct final inspection. At this stage, the product is thoroughly tested and inspected to ensure it meets design specifications and performance requirements. Only products that pass the final inspection can be considered qualified and can be delivered to customers for use.
Overall, the manufacturing process of Substrate Packaging is a complex and precise process that requires a high degree of professional knowledge and technology. Through strict quality control and precise manufacturing processes, high-quality Substrate Packaging products that meet industry standards can be produced.
What are the applications of Substrate Packaging?
Substrate Packaging, as a key electronic packaging technology, plays an important role in various industries. Its versatility makes it the first choice for innovative electronic designs. Here are the applications of Substrate Packaging in different industries:
In the field of consumer electronics, such as smartphones, tablets, smart home devices and other products, Substrate Packaging is widely used. Its high performance and compact design enable consumer electronics products to be smaller and lighter while maintaining excellent performance and reliability.
In the automotive industry, Substrate Packaging is used in vehicle electronic systems and in-car entertainment equipment. Since the automotive environment has extremely high requirements on the stability and durability of electronic devices, Substrate Packaging’s high reliability and high temperature resistance make it an ideal choice for the automotive electronics field.
In the aerospace field, Substrate Packaging’s lightweight and high-performance characteristics make it the first choice for aerospace electronic equipment. In the fields of spacecraft, satellites, navigation systems and other fields, Substrate Packaging can meet stringent environmental requirements and ensure reliable operation of equipment.
In the field of national defense, Substrate Packaging is widely used in key equipment such as military communication equipment, radar systems, and missile control systems. Its high reliability, interference resistance and durability make Substrate Packaging an indispensable part of the defense field.
In the field of medical equipment, Substrate Packaging is used in various medical diagnostic equipment, treatment equipment and implantable medical devices. Its high precision and reliability ensure the accuracy and stability of medical equipment, thereby providing more advanced technical support for the medical industry.
In the telecommunications industry, Substrate Packaging is used in key equipment such as communication base stations, optical fiber network equipment, and wireless routers. Its high-speed transmission and signal processing capabilities enable telecommunications equipment to achieve faster and more stable data transmission, meeting the needs of the modern communications field.
In general, Substrate Packaging’s wide range of applications spans various industry sectors, and its high performance, reliability and versatility make it a key driving force in promoting the innovation and development of electronic technology.
Where can I find Substrate Packaging manufacturers?
When looking for a reliable Substrate Packaging manufacturer, supplier selection is crucial. Our company is a well-known Substrate Packaging manufacturer that provides customers with customized and standard solutions to meet the unique needs of various electronic designs.
As a trustworthy supplier, we focus on quality and reliability. Our Substrate Packaging products undergo strict quality control and testing to ensure compliance with industry standards and customer requirements. No matter what Substrate Packaging you need, we can provide a customized solution to meet your specific needs.
Our company has rich experience and expertise and is a leader in the field of Substrate Packaging manufacturing. Our team consists of experienced engineers and technicians who can provide customers with professional consulting and technical support. Whether you need low-volume customization or high-volume standard products, we can meet your needs and ensure timely delivery.
In addition to providing high-quality Substrate Packaging products, we are also committed to providing excellent services to our customers. Our customer service team is here to answer any questions you have and provide you with timely support and assistance. Our goal is to provide customers with the best Substrate Packaging solutions to help them achieve their project goals.
In short, as a trustworthy Substrate Packaging manufacturer, we will wholeheartedly provide customers with high-quality products and services. Whatever your needs are, we have the capabilities and resources to meet your requirements. Choose us and you will get the best Substrate Packaging solutions to help you succeed.
What are the quotes from Substrate Packaging manufacturers?
In the electronic equipment manufacturing process, cost estimation of Substrate Packaging is a crucial step. Understanding Substrate Packaging manufacturer quotes involves considerations for specific substrate types and quantities, so contact a trusted manufacturer for a custom quote.
First, the manufacturer will conduct a preliminary assessment based on the detailed requirements provided by the customer, including the type and specifications of Substrate Packaging required. Different types of Substrate Packaging, such as organic substrates, ceramic substrates, metal core substrates or flexible substrates, have different cost structures and therefore need to be analyzed in a targeted manner.
Secondly, manufacturers also take into account the number of substrates required. Generally speaking, mass production can bring certain cost advantages, so customers who order in large quantities may receive more competitive prices.
In addition, customized quotations may also be affected by other factors, such as production cycle, delivery time, technical requirements, etc. Therefore, it is important to fully communicate and negotiate with the manufacturer to ensure that the final quote meets the customer’s needs and budget.
In order to obtain an accurate quotation, customers can contact the manufacturer via email, phone or online inquiry platform. When communicating with manufacturers, providing as detailed a project description and technical requirements as possible will help expedite the quoting process and ensure that the quote obtained meets expectations.
Overall, getting in touch with a trusted Substrate Packaging manufacturer and getting a customized quote is a critical step in ensuring the success of your project. By fully understanding project requirements, effective communication and negotiation with manufacturers, customers can obtain the most competitive quotations and ensure the smooth progress of the project.
Frequently Asked Questions (FAQs)
What is Substrate Packaging, and why is it important?
Substrate Packaging refers to the fundamental material supporting and connecting electronic components in PCB engineering. It is crucial for ensuring the reliability and performance of electronic devices by providing a stable platform for component placement and interconnection.
What are the main types of Substrate Packaging available?
There are several types of Substrate Packaging, including Organic Substrates, Ceramic Substrates, Metal Core Substrates, and Flex Substrates. Each type offers unique characteristics suitable for various applications, ranging from cost-effectiveness to enhanced thermal management.
What are the advantages of using Substrate Packaging?
Substrate Packaging offers numerous advantages, including improved thermal management, enhanced electrical performance, miniaturization capabilities, higher reliability, and cost-effectiveness. These benefits contribute to the overall efficiency and longevity of electronic devices.
How does Substrate Packaging differ from traditional PCBs?
Unlike traditional PCBs, which primarily consist of rigid substrates like FR4, Substrate Packaging utilizes diverse materials such as organic, ceramic, or metal core substrates. This allows for better thermal dissipation, flexibility, and reliability, making Substrate Packaging ideal for modern electronic designs.
What is the manufacturing process involved in producing Substrate Packaging?
The manufacturing process of Substrate Packaging involves substrate preparation, layer buildup, and surface finishing. It requires precise techniques to ensure the quality and integrity of the substrate, meeting stringent industry standards for electronic packaging.
What are the common applications of Substrate Packaging?
Substrate Packaging finds applications across various industries, including consumer electronics, automotive, aerospace, defense, medical devices, and telecommunications. Its versatility makes it suitable for diverse electronic designs requiring reliability and performance.