The Thinnest PCB Manufacturer.Introducing “NanoCircuits,” the unrivaled pioneer in PCB manufacturing. Renowned for its precision engineering and cutting-edge technology, NanoCircuits stands as the epitome of excellence in crafting the thinnest PCBs known to industry. With a relentless commitment to innovation and quality, each board produced by NanoCircuits showcases unparalleled slimness without compromising durability or performance. Seamlessly blending advanced materials and meticulous craftsmanship, NanoCircuits caters to the most demanding applications where space is at a premium. Elevate your projects with PCBs engineered to perfection by the unparalleled expertise of NanoCircuits, the unequivocal leader in thin PCB manufacturing.
With the continuous advancement of technology, electronic devices are developing in a direction that is smaller and lighter. As one of the core components of electronic equipment, PCB (Printed Circuit Board) is also constantly evolving. In recent years, a new PCB technology that has attracted much attention has emerged, that is, the “thinnest PCB”. This kind of PCB is extremely thin, not only lightweight and flexible, but also suitable for various complex electronic device designs. The advent of the thinnest PCB will further promote the innovative development of electronic equipment and bring more possibilities to future smart products.
What is The Thinnest PCB?
The thinnest PCB, the thinnest printed circuit board, is an extremely thin electronic component substrate. Typically, its thickness is less than 1 millimeter, and can even be as thin as tens of microns. Compared with traditional PCB, the thinnest PCB is lighter, which makes it an innovative choice in the design and application of electronic equipment.
Traditional PCBs are usually made of materials such as fiberglass-reinforced epoxy (FR4), whose relatively thick sheets limit the flexibility and portability of the device. The thinnest PCB uses high-performance flexible substrates, such as polyimide (PI) or polyester film. These materials not only have excellent electrical properties, but also have excellent flexibility and high temperature resistance.
The emergence of the thinnest PCB has brought new possibilities to the design and application of electronic devices. First, its thin nature allows it to easily adapt to complex device design requirements, such as curved or curled shapes. This flexibility enables the thinnest PCBs to be widely used in small electronic products such as smartphones, tablets, wearable devices, etc.
Secondly, the lightweight design of the thinnest PCB helps reduce the overall weight of the electronic device, thereby improving the product’s portability and comfort. This means lighter portability and a more comfortable experience for users, especially in the field of mobile devices. This advantage is particularly significant.
In addition, the thinnest PCB also has excellent high-frequency performance and electromagnetic shielding properties, which makes it excellent in some applications that require higher electrical signal transmission and interference suppression. Therefore, in addition to consumer electronics, the thinnest PCB is also widely used in medical equipment, aerospace devices, portable communication equipment and other fields.
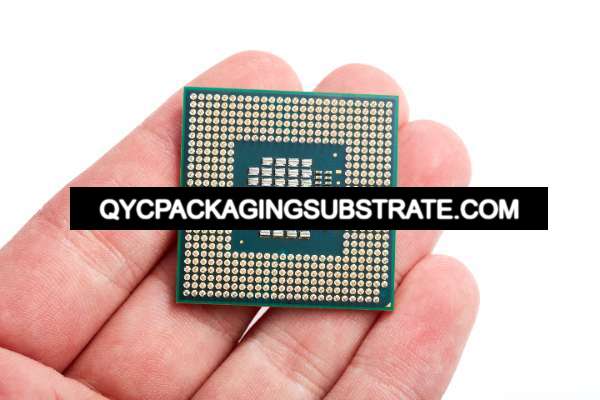
The Thinnest PCB Manufacturer
In general, the emergence of the thinnest PCB not only provides more flexibility and innovation space for the design of electronic devices, but also brings a lighter and more convenient use experience to users. With the continuous development of technology, it is believed that the thinnest PCB will play an increasingly important role in the field of electronic equipment in the future and become an important force in promoting the progress of the electronic industry.
The Thinnest PCB design Reference Guide.
With the continuous advancement of technology, electronic devices are developing in a direction that is thinner, lighter, and more portable, and the emergence of the thinnest PCB (Printed Circuit Board, printed circuit board) provides important support for this trend. As one of the core components of electronic equipment, the design of the thinnest PCB is crucial. Below is a reference guide for the thinnest PCB design to help you better understand and apply this innovative technology.
The thinnest PCBs usually use flexible substrates such as polyimide (PI) or polyester film. When selecting materials, consider their electrical properties, flexibility, high temperature resistance, and compatibility with other components to ensure the performance and reliability of the final product.
When designing the thinnest PCB, factors such as the size, shape, and usage environment of the device must be taken into consideration. Flexible PCB design tools can help you implement complex circuit layouts and line connections, ensuring the tight integration of the PCB with other components and improving the performance and stability of the overall device.
Carefully designed layout and wiring can maximize the use of PCB space, reduce the board area, and reduce the weight and thickness of the product. Reasonably plan the location and connection methods of circuit components to avoid signal interference and electromagnetic radiation, and improve the stability and anti-interference ability of the circuit.
Although the thinnest PCB has high flexibility, its structural strength and stability still need to be considered in practical applications. During the design stage, the structure of the PCB can be strengthened by adding support structures or choosing more durable materials to ensure that it will not deform or be damaged during use.
Quality control is crucial during the manufacturing process of the thinnest PCBs. Strictly control the selection of materials, processing technology and production process to ensure that the quality of PCB meets the design requirements, and ensure that its performance and reliability reach the expected level through strict testing and verification processes.
Through the above reference guide, you can better understand and apply the thinnest PCB technology, providing more possibilities and flexibility for the design and manufacturing of electronic devices. The emergence of the thinnest PCB will promote innovation and progress in the field of electronic equipment manufacturing, bring users a thinner and more portable product experience, and help technological development reach new heights.
What material is used in The Thinnest PCB?
The thinnest PCBs usually use high-performance flexible substrates such as polyimide (PI) or polyester film. These materials were selected as the manufacturing materials for the thinnest PCBs mainly because they offer multiple advantages and are able to meet the high requirements of today’s electronic device designs.
First, polyimide (PI) and polyester films have excellent electrical properties. They have good insulation properties and can effectively prevent the unintended conduction of current on the PCB surface, thereby ensuring the stability and reliability of the circuit. This is particularly important for electronic equipment that requires high-frequency, high-speed transmission, such as communication equipment and computer systems.
Secondly, these flexible substrates have excellent flexibility. Compared with traditional rigid PCB substrates, polyimide and polyester films are more flexible and can be bent, folded and curved to adapt to various complex-shaped device designs. This provides greater flexibility for the compact design of electronic devices, allowing the thinnest PCB to be easily integrated into various small spaces, such as smart wearable devices, medical equipment and automotive electronic systems.
In addition, polyimide and polyester films have excellent high temperature resistance. They can operate stably for a long time in high temperature environments and are not prone to deformation or thermal aging, ensuring the reliability and durability of electronic equipment under extreme conditions. This makes the thinnest PCBs important in high-temperature applications such as aerospace and industrial automation.
To sum up, polyimide and polyester films, as the thinnest PCB manufacturing materials, not only have excellent electrical properties, but also have excellent flexibility and high temperature resistance, making them suitable for various complex electronic device designs. With the continuous development of technology and the advancement of material science, it is believed that the thinnest PCB will play an increasingly important role in the field of electronic equipment manufacturing in the future, bringing more convenience and innovation to people’s lives and work.
What size are The Thinnest PCB?
The thinnest PCB sizes vary due to their flexibility and customization. Typically, the size of the thinnest PCB depends on the requirements of the specific application and the space constraints required by the design. Due to its design flexibility, the thinnest PCB can be customized into various shapes and sizes to suit the needs of different electronic devices.
For smartphones, tablets, and other portable electronic devices, the thinnest PCBs are often very small in size. They may be only a few centimeters long and wide, and may be only tens to hundreds of microns thick. This small size PCB can be easily embedded into ultra-thin devices, making them more compact and lightweight.
On the other hand, the thinnest PCBs can also be used in larger devices such as medical equipment and aerospace devices. Although these devices may require larger PCB sizes to accommodate more electronic components and connections, the thinnest PCBs can still achieve high integration and space optimization through their flexible and low-profile designs.
Overall, the thinnest PCBs come in a wide range of sizes, ranging from a few millimeters to tens of centimeters, depending on specific application needs and design requirements. This flexibility makes the thinnest PCB ideal for a variety of electronic devices, from small portable devices to large industrial applications, able to meet different size and performance requirements.
The Manufacturer Process of The Thinnest PCB.
The manufacturing process of the thinnest PCB is a complex and precise process involving multiple steps and delicate operations to ensure that the quality and performance of the final product meet the expected standards.
First, the key to making the thinnest PCB is choosing the right base material. Usually, polyimide (PI) or polyester film are the most commonly used substrates. They have excellent flexibility and high temperature resistance and can meet the thinnest PCB’s requirements for lightness and flexibility. During the manufacturing process, the substrate is precisely cut to the required dimensions in preparation for the following process steps.
Next, a thin film of copper (or other metal) is applied to the surface of the substrate to form a conductive layer. This step usually uses chemical deposition or physical plating to ensure the uniformity and sealing of the conductive layer to improve the electrical performance and stability of the PCB.
Then, photolithography technology is used to cover the conductive layer with a photoresist layer, and through the exposure and development process, the required circuit pattern is formed. These patterns will guide subsequent etching or removal steps to create wires and connections.
Next, chemical etching or mechanical removal is used to remove parts of the metal layer that are not protected by photolithography, thereby forming circuit connections and wires. This step requires high-precision control to ensure the accuracy and reliability of the circuit.
After completing the circuit pattern, multiple cleaning and processing steps are required to remove residual photoresist and etchant, as well as improve surface roughness and adhesion, providing a good foundation for subsequent assembly and packaging.
Finally, the final processing and assembly of the thinnest PCB is carried out, including drilling, metallization, solder paste coating, component mounting and other steps to finally form the finished PCB. During this process, temperature, humidity and other environmental factors need to be strictly controlled to ensure product quality and stability.
In general, manufacturing the thinnest PCB is a technology-intensive process that requires precision equipment and strict operational control. However, through continuous innovation and improvement, we will be able to produce the thinnest PCB that is thinner, more flexible, and has stable performance. products to promote the continuous development and progress of electronic equipment.
The Application area of The Thinnest PCB.
The thinnest PCB has an extremely wide range of applications, and its flexibility and lightness make it ideal for many small electronic products and high-end technical equipment.
First of all, the thinnest PCB has a wide range of applications in the field of consumer electronics. Portable electronic devices such as smartphones and tablets usually require thin and light designs to meet users’ needs for portability and appearance. The lightweight design and flexibility of the thinnest PCB make it one of the core components in these devices, providing them with reliable electrical connections and stable performance.
Secondly, the thinnest PCB also plays an important role in the field of medical equipment. As medical technology continues to advance, more and more medical devices need to be portable and flexible to adapt to different clinical environments and patient needs. The flexibility and high performance of the thinnest PCB make it a key component of products such as portable medical monitoring equipment and remote diagnostic tools, providing medical staff with more convenient and efficient medical services.
In addition, the thinnest PCB is also widely used in aerospace devices. The aerospace field has very strict requirements for electronic equipment, which require lightweight, high strength and reliability. The thinnest PCB’s lightweight design and excellent performance make it an ideal choice for aerospace devices, including spacecraft control systems, satellite communication equipment, etc.
Overall, the thinnest PCB not only plays an important role in the field of consumer electronics, but also shows great potential in high-end technology applications such as medical equipment and aerospace fields. With the continuous development of technology and changing market demands, it is believed that the thinnest PCB will play an important role in more fields and promote the innovation and progress of electronic equipment.
What are the advantages of The Thinnest PCB?
The advantage of the thinnest PCB lies in its unique design and performance characteristics, which make it an important innovation in the field of modern electronic equipment manufacturing. Compared with traditional PCBs, the thinnest PCBs have higher flexibility and bendability, which is determined by their use of high-performance flexible substrates. This flexible substrate, usually polyimide (PI) or polyester film, has excellent electrical properties and high temperature resistance, allowing the thinnest PCB to be flexibly used in complex device designs. This flexibility and bendability allow the thinnest PCB to easily adapt to the needs of various curved surfaces and small-sized devices, providing designers with greater creative space, thus promoting the diversified and personalized development of electronic devices.
In addition to flexibility and bendability, the lightweight design of the thinnest PCB is also one of its advantages. Traditional PCBs usually use hard substrates, so they are greatly restricted in design, while the flexible substrates used in the thinnest PCBs make them lighter. Since weight is an important factor affecting the portability and comfort of electronic devices, the lightweight design of the thinnest PCB helps reduce the overall weight of electronic devices, making the device more portable and comfortable, and providing users with a better experience.
To sum up, the thinnest PCB has higher flexibility and bendability, can adapt to more complex device design needs, and has the advantage of lightweight design, which helps to reduce the overall weight of electronic devices and improve the portability of products. and comfort. With the continuous advancement of technology and changing market demands, the thinnest PCB will become an important development direction in the field of electronic equipment manufacturing in the future, bringing more convenience and fun to people’s lives and work.
FAQ
What are the advantages of the thinnest PCB compared to traditional PCB?
The thinnest PCB has higher flexibility and bendability, is more adaptable, and can meet the design needs of more complex devices. Its lightweight design also helps reduce the overall weight of electronic devices and improve portability and comfort.
What materials are the thinnest PCBs made of?
The thinnest PCBs usually use high-performance flexible substrates such as polyimide (PI) or polyester film. These materials have excellent electrical properties, flexibility and high temperature resistance, making them suitable for a variety of complex electronic device designs.
What application fields is the thinnest PCB suitable for?
The thinnest PCB is widely used in small electronic products such as smartphones, tablets, and wearable devices. In addition, due to its flexibility and lightness, the thinnest PCB is also widely used in medical equipment, aerospace devices, and portable consumer electronics.
What is the difference in the manufacturing process of the thinnest PCB?
Compared with traditional PCBs, the manufacturing process of the thinnest PCBs is more complex and requires higher-precision processing equipment and process control. In particular, stricter control is required during material selection, lamination process and molding process to ensure the quality and reliability of the final product.
How reliable is the thinnest PCB?
Despite the advantages of the thinnest PCBs in terms of flexibility and lightweight, their reliability remains a critical issue. Manufacturers usually conduct rigorous reliability tests, including bending tests, temperature cycle tests, etc., to ensure that the thinnest PCBs can maintain stable performance under various environmental conditions.