Ultra High Density Wiring Substrates Manufacturer.A leading innovator in cutting-edge technology, our company specializes in the production of Ultra High Density Wiring Substrates. Renowned for our precision engineering and advanced manufacturing techniques, we cater to the demands of industries requiring intricate circuitry solutions. With a commitment to excellence, we deliver substrates that surpass industry standards in density and performance. Our state-of-the-art facilities, coupled with a dedicated team of experts, ensure seamless production processes from design to delivery. Trust us as your partner for next-generation wiring substrates, where reliability meets innovation.
Ultra High Density Wiring Substrates (UHDWS) is a key technology in today’s electronic field. It realizes the wiring of a large number of electronic components in a limited space and provides high performance and miniaturization of modern electronic equipment. basic support. This article will delve into the definition, design, manufacturing process, application areas, advantages and FAQs of UHDWS, aiming to help readers fully understand this technology and further promote innovation and development in the electronics field.
What are Ultra High Density Wiring Substrates?
UHDWS is a special type of Printed Circuit Board (PCB) with extremely high circuit density and micro size. In the field of modern electronics, as electronic devices become increasingly miniaturized and their functions become more complex, the importance of UHDWS has become increasingly prominent. They use advanced manufacturing processes to realize the wiring of a large number of electronic components in a limited space, thereby providing basic support for the high performance and miniaturization of various types of equipment.
Traditional PCB wiring density is limited by space, making it difficult to meet the miniaturization and high-performance requirements of modern electronic equipment. By adopting miniaturized circuit design and high-density circuit layout, UHDWS integrates more functions into a smaller space, making it possible to improve the performance and reduce the size of the equipment.
The manufacturing process of UHDWS requires the use of advanced manufacturing equipment and processes, such as laser etching technology, multi-layer stacking technology, and micro-welding technology. The use of these technologies enables UHDWS to implement complex line layouts in a very small space while ensuring electrical isolation and signal integrity between lines, thereby ensuring the stability and reliability of the equipment.
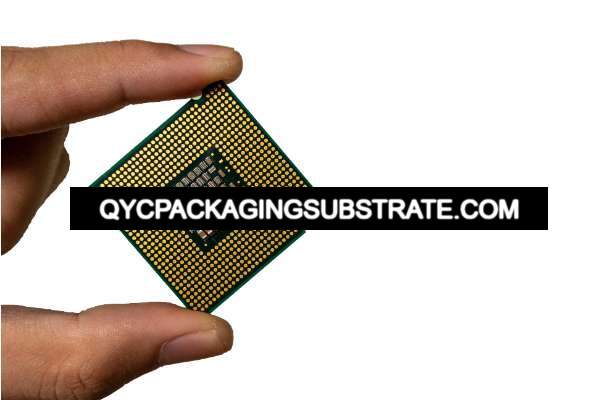
Ultra High Density Wiring Substrates Manufacturer
In terms of application, UHDWS is widely used in various high-end electronic devices, such as smartphones, tablets, portable medical equipment, drones, industrial automation equipment, etc. These devices often have strict requirements on volume and weight, and UHDWS’s miniaturization and high-density wiring can meet these requirements while providing excellent performance and stability.
In general, UHDWS, as a key electronic technology, provides important support for the development of modern electronic equipment. With the continuous advancement of manufacturing processes and technologies, UHDWS will continue to play an important role in promoting innovation and progress in the electronic field and bringing more scientific and technological achievements and convenience to human society.
Ultra High Density Wiring Substrates design Reference Guide.
The design of Ultra High Density Wiring Substrates (UHDWS) is a crucial part of the development of modern electronic products. It involves the planning of the layout of electronic components and wiring connections to ensure that the final product functions and performs as expected. When designing UHDWS, engineers need to consider multiple factors to ensure the effectiveness and reliability of the design.
First, one of the important design considerations is how components are placed. Reasonable component layout can optimize the structure of the circuit to the greatest extent, reduce the length of the signal transmission path, and reduce signal delay, thereby improving the performance and response speed of the system. At the same time, a reasonable layout can also reduce crosstalk and noise interference in the circuit and ensure signal stability and reliability.
Secondly, signal integrity is an aspect that requires special attention in UHDWS design. Due to the extremely high circuit density and micro size of UHDWS, the signal transmission path on the circuit board may be affected by various factors, such as impedance matching, signal coupling and reflection. Therefore, design engineers need to ensure signal integrity and stability to the greatest extent through reasonable wiring planning and signal adjustment technology.
In addition, thermal management is also one of the important factors to be considered in UHDWS design. Because electronic components generate heat during operation, excessive temperatures may affect circuit performance and reliability. Therefore, when designing UHDWS, engineers need to reasonably plan the heat dissipation structure and use appropriate heat dissipation materials and technologies to ensure that the circuit can operate within a stable temperature range.
Finally, manufacturability is another important aspect to consider in UHDWS design. Due to the extremely high circuit density and micro size of UHDWS, the manufacturing process may face many challenges, such as circuit etching accuracy, aperture control, and pad coating. Therefore, design engineers need to fully consider the feasibility of manufacturing during the design stage and select appropriate manufacturing processes and technologies to ensure the quality and reliability of the final product.
To sum up, the design of UHDWS involves multiple considerations, including component placement, signal integrity, thermal management, and manufacturability. By comprehensively considering these factors, design engineers can effectively optimize the circuit structure and improve the performance and reliability of the system, thereby achieving efficient design and production of electronic products.
What material is used in Ultra High Density Wiring Substrates?
Ultra High Density Wiring Substrates (UHDWS), as a key technology, usually use advanced materials, such as polyimide (Polyimide) or ceramic substrates. These materials have excellent properties and can achieve higher circuit density and better performance, providing reliable support for various complex electronic application scenarios.
Polyimide is a high-performance engineering plastic with excellent heat resistance, chemical resistance and mechanical strength. It maintains stable performance under extreme temperatures and environmental conditions, making it suitable for demanding electronic devices and systems. Due to its high plasticity and corrosion resistance, polyimide substrates can implement fine circuit layouts in complex circuit designs, thereby achieving ultra-high-density wiring and meeting the space utilization and performance requirements of modern electronic equipment.
Ceramic substrates have higher thermal conductivity and better dimensional stability than polyimide. Ceramic substrates are able to maintain stable electrical properties across extreme temperature ranges, while possessing excellent mechanical strength and wear resistance. This makes ceramic substrates ideal for some special applications, such as high-power electronic equipment, high-frequency communication systems, and electronic equipment in the military field.
In general, the advanced materials used in UHDWS have many advantages, including high temperature resistance, corrosion resistance, and high mechanical strength, making them widely used in the field of modern electronics. With the continuous development and innovation of technology, it is believed that UHDWS will continue to play an important role in promoting the continuous improvement of the performance and functions of electronic devices.
What size are Ultra High Density Wiring Substrates?
The size of Ultra High Density Wiring Substrates (UHDWS) changes with the advancement of technology and the continuous evolution of application requirements. Generally speaking, the size of UHDWS can range from a few millimeters to tens of centimeters, depending on the specific application scenarios and the size requirements of the equipment.
For small electronic devices, such as smartphones, wearable devices, and portable medical devices, extremely small-sized UHDWS are usually required to meet the compact design requirements of the device. These UHDWS may only be a few millimeters to centimeters in size, but still need to maintain a high-density circuit layout to support complex circuits and functions.
For large electronic systems, such as industrial automation equipment, communication base stations and medical imaging equipment, larger UHDWS are required to accommodate more electronic components and complex circuit layouts. These UHDWS may be tens of centimeters or even larger to meet the functional and performance needs of the system.
With the continuous development of technology, the size range of UHDWS is gradually expanding, so that it can be applied to an increasingly wider range of fields and scenarios. In the future, as the demand for the volume and performance of electronic devices continues to increase, the size and density of UHDWS will continue to develop in a smaller and higher direction to meet the growing market demand and application challenges.
The Manufacturer Process of Ultra High Density Wiring Substrates.
The manufacturing process of UHDWS is a complex and precise project, which usually includes multiple key steps. Each step is crucial and directly affects the quality and performance of the final product. The following are the main steps in the UHDWS manufacturing process:
Substrate preparation
The first step in fabricating UHDWS is to prepare the substrate material. Advanced materials such as polyimide or ceramics are usually used as substrates. These materials have good heat resistance and mechanical properties and can meet the needs of high-density wiring. In this step, the substrate is cut to size and surface treated to ensure good adhesion.
Alignment between layers
UHDWS are usually multi-layer structures, with each layer containing complex wiring and electrical connections. During the inter-layer alignment process, each layer of substrate must be accurately aligned to ensure the accuracy and stability of electrical connections. This step is usually accomplished with the help of optical microscopes and precision positioning equipment.
Line etching or printing
Once the substrate layer alignment is complete, the next step is to etch or print circuit traces on the substrate surface. This step involves printing metal foil or conductive ink onto the surface of the substrate and forming the desired circuit pattern through chemical etching or photolithography techniques. Precise circuit preparation is key to ensuring the performance and reliability of electronic equipment.
Hole drill
After the circuit etching or printing is completed, the next step is to drill holes in the substrate. These holes are used to mount electronic components and make electrical connections between different layers. The hole drilling process requires highly precise equipment and process control to ensure the location and size of the holes are accurate.
Pad coating
After completing the preparation of the traces and holes, the next step is to coat the pads on the substrate. Solder pads are used to connect pins or terminals of electronic components and provide a secure soldering connection. The pad coating process requires precise control of coating thickness and uniformity to ensure good soldering quality.
Component assembly
After the pad coating is completed, the electronic components can be mounted to the substrate. This involves precisely positioning components such as chips, resistors, capacitors, etc. on the substrate and connecting them to the circuits through soldering or other connection techniques. The component assembly process requires highly sophisticated automated equipment and process controls to ensure correct installation and connection of components.
Test
The final step is to test the fabricated UHDWS. This includes electrical testing, reliability testing, functional testing, etc. to ensure that the performance of UHDWS meets design requirements and meets customer needs. The testing process requires strict testing standards and advanced testing equipment to ensure product quality and reliability.
In general, the manufacturing process of UHDWS is a complex and precise process that requires highly professional technology and equipment support. Through precise process control and strict quality management, high-density circuits and micro-sized UHDWS products can be realized, providing strong support and driving force for the development of modern electronic equipment.
The Application area of Ultra High Density Wiring Substrates.
UHDWS is widely used in various fields, and its high-density wiring and miniature size make it ideal for modern electronic device design. The consumer electronics industry is one of the main areas for UHDWS applications. High-end consumer electronics products such as smartphones, tablets, and wearable devices all use UHDWS technology to achieve smaller, thinner and lighter designs and provide more powerful performance and functionality.
In the automotive industry, UHDWS is widely used in automotive electronic systems, including engine control units, in-car entertainment systems, body electronics, driving assistance systems, etc. Its high-density wiring and reliability can meet the requirements of automotive electronic equipment for miniaturization, high performance and durability, providing important support for the development of intelligence and electrification in the automotive industry.
The aerospace field is also one of the important application fields of UHDWS. Aerospace equipment has extremely high requirements for lightweight and high performance. The miniature size and high-density wiring of UHDWS make it a key component of complex electronic equipment such as spacecraft, satellites, and navigation systems.
In the field of medical equipment, UHDWS is used in various medical imaging equipment, implantable medical devices, health monitoring equipment, etc. Its high-density wiring and reliability can meet the needs of medical equipment for precise control and data transmission, providing reliable support for medical diagnosis and treatment.
The communication field is another major application field of UHDWS. Communication equipment such as base stations, optical fiber network equipment, satellite communication systems, etc. all use UHDWS technology to achieve high-speed data transmission and stable communication connections, meeting the communication industry’s requirements for high performance and high reliability.
Industrial automation is one of the important application areas of UHDWS. Industrial control systems, robots, automated production lines, etc. all require high-density wiring to achieve precise control and data transmission. The reliability and stability of UHDWS make it an ideal choice in the field of industrial automation.
In general, UHDWS plays an important role in various fields. Its high-density wiring and micro size provide key support for the performance improvement and size reduction of modern electronic equipment, and promote technological innovation and progress in various industries.
What are the advantages of Ultra High Density Wiring Substrates?
The advantages of UHDWS occupy an important position in the design of today’s electronic equipment. Compared with traditional wiring methods, it has many outstanding advantages and provides strong support for development and innovation in the electronic field.
First, UHDWS has higher line density. Its advanced manufacturing processes and materials make it possible to route more electronic components in a limited space. This means that more functional modules can be accommodated on the same size substrate, thereby improving the performance and functionality of the device.
Secondly, UHDWS has a smaller size. Because the circuits are more compact, electronic devices made by UHDWS are smaller and lighter, making them more suitable for portable devices or applications with limited space. This brings great convenience to the portability and portability of electronic products.
In addition, UHDWS also has higher reliability. Its precision manufacturing process and high-quality materials ensure the stability and long-term reliability of the circuit. UHDWS maintains stable performance under harsh environmental conditions, extending equipment life and reducing the need for maintenance and repairs.
In addition, UHDWS has better signal integrity. Because the circuit layout is more compact and the signal transmission path is shorter, electronic signals are transmitted faster and with less interference, thereby improving the performance and response speed of the device. This is especially important for application scenarios that require high-speed data transmission or low latency.
Finally, UHDWS has superior thermal performance. Its materials and design allow the heat generated by electronic equipment during operation to be effectively dissipated, thereby reducing the temperature of the equipment and improving stability and reliability. This is especially important for high-performance equipment or equipment that operates continuously for long periods of time.
To sum up, UHDWS, as an advanced electronic wiring technology, has many advantages such as high circuit density, small size, high reliability, good signal integrity and superior thermal performance. These advantages make UHDWS an indispensable part of the design of modern electronic equipment, promoting continuous innovation and progress in the electronic field.
FAQ
What are the advantages of UHDWS compared to traditional PCB?
UHDWS has higher circuit density and smaller size, and can accommodate more electronic components in a limited space to achieve more complex functions. In addition, UHDWS has superior signal integrity and thermal performance, as well as higher reliability, making it suitable for a variety of demanding electronic applications.
Are UHDWS more complex to design and manufacture?
Yes, due to the higher circuit density and smaller size of UHDWS, its design and manufacturing process may be more complex and sophisticated. It is necessary to use advanced design software and manufacturing technology and strictly control every link to ensure the performance and reliability of the final product.
What are the considerations for material selection for UHDWS?
When selecting materials for UHDWS, factors such as thermal resistance, chemical resistance, mechanical strength, and compatibility with other components need to be considered. Commonly used materials include polyimide and ceramic substrates, which can meet the high-performance requirements of UHDWS.
In what fields is UHDWS widely used?
UHDWS is widely used in consumer electronics, automobiles, aerospace, medical equipment, communications and industrial automation and other fields. For example, UHDWS can be found in smartphones, computers, automotive control systems, medical imaging equipment, and communication equipment.
What are the key steps in the UHDWS manufacturing process?
The manufacturing process of UHDWS includes steps such as substrate preparation, interlayer alignment, line etching or printing, hole drilling, pad coating, component assembly and testing. Every step is critical and requires precision equipment and strict process control to ensure product quality and performance.