Ultra-Multilayer BGA Substrates Manufacturer.”Ultra-Multilayer BGA Substrates Manufacturer” refers to a company specialized in producing advanced BGA substrates with multiple layers, catering to high-density interconnection needs in modern electronic devices.
Ultra-multilayer BGA (Ball Grid Array) substrates are at the forefront of electronic packaging technology, driving advancements in high-performance computing, telecommunications, and consumer electronics. These substrates feature multiple layers of circuitry within a compact form, enabling complex electrical interconnections and efficient thermal management. Their development is pivotal for supporting the increasing demand for miniaturization and enhanced functionality in modern electronic devices.
What are Ultra-Multilayer BGA Substrates?
Ultra-multilayer BGA substrates are sophisticated circuit boards designed to support high-density electronic assemblies, primarily used in advanced microprocessors and integrated circuits. These substrates consist of numerous thin layers of conductive materials, often separated by insulating layers, which are meticulously fabricated to create a compact and efficient interconnection platform. The BGA format, characterized by an array of solder balls on the substrate’s underside, facilitates robust electrical and mechanical connections between the substrate and the device’s PCB.
The multilayer aspect allows for intricate routing of electrical signals, power distribution, and ground planes within a limited space. This is crucial for high-speed and high-frequency applications where signal integrity and minimization of electrical interference are paramount. Moreover, the ability to stack multiple layers enables the integration of more functionality within a smaller footprint, which is essential for the continued miniaturization of electronic devices.
Design Reference Guide for Ultra-Multilayer BGA Substrates
Designing ultra-multilayer BGA substrates involves several critical considerations to ensure performance and reliability. Engineers must meticulously plan the layer stack-up, which includes determining the number and types of layers, such as signal layers, power layers, and ground planes. The layer arrangement directly impacts the substrate’s electrical performance, thermal management, and mechanical stability.
Signal integrity is a primary concern, particularly for high-frequency applications. Designers use advanced simulation tools to model and optimize signal paths, minimizing issues like crosstalk, signal reflection, and electromagnetic interference (EMI). Techniques such as differential pair routing and controlled impedance lines are commonly employed to maintain signal quality.
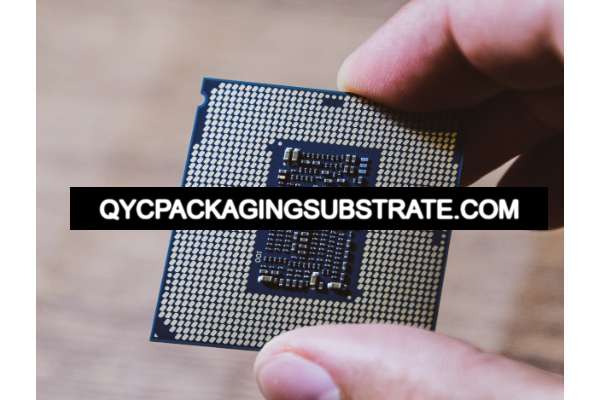
Ultra-Multilayer BGA Substrates Manufacturer
Thermal management is another crucial aspect, as multilayer substrates can generate significant heat. Effective thermal vias, heat sinks, and the strategic placement of thermal pads are essential to dissipate heat and prevent thermal runaway conditions. Additionally, careful consideration of the substrate material’s thermal conductivity and coefficient of thermal expansion (CTE) is vital to ensure longevity and reliability.
Mechanical design considerations include ensuring that the substrate can withstand the stresses of manufacturing, such as soldering and reflow processes, as well as operational stresses from thermal cycling and mechanical vibrations. This often involves selecting materials with suitable mechanical properties and designing robust via structures to ensure interlayer connectivity.
Materials Used in Ultra-Multilayer BGA Substrates
The materials used in ultra-multilayer BGA substrates are critical to their performance. These substrates typically incorporate advanced laminates, high-purity copper, and specialized dielectric materials.
High-performance laminates, such as FR-4 or BT (Bismaleimide-Triazine) resin, provide the necessary structural integrity and electrical insulation. For higher frequency and thermal requirements, materials like PTFE (Polytetrafluoroethylene) and ceramic-filled laminates are used due to their superior dielectric properties and thermal conductivity.
Copper is the primary conductive material, chosen for its excellent electrical conductivity and thermal properties. The copper layers are precisely etched to form the intricate circuitry patterns required for complex electronic devices. The thickness of these copper layers can vary depending on the current-carrying requirements and the need for effective heat dissipation.
Dielectric materials play a vital role in isolating the conductive layers and ensuring signal integrity. These materials must exhibit low dielectric constants and low loss tangents to support high-speed signal transmission. Advanced dielectric materials with high thermal stability and low CTE are preferred to maintain structural integrity and electrical performance across a wide temperature range.
Additionally, solder mask materials are used to protect the underlying circuitry from environmental factors and mechanical damage. These masks are typically made from epoxy-based polymers that provide good adhesion and resistance to thermal and chemical stresses encountered during manufacturing and operation.
What Size are Ultra-Multilayer BGA Substrates?
Ultra-multilayer BGA substrates come in various dimensions tailored to specific application requirements. The dimensions depend on the complexity of the device, the number of layers, and the intended use.
Typically, these substrates can range from a few millimeters to several centimeters in size. For example, substrates for smartphone processors might be only a few millimeters across, whereas those used in server processors could be significantly larger to accommodate more circuitry and connections.
The thickness of ultra-multilayer BGA substrates is also a critical dimension. They are generally thicker than single-layer substrates due to the multiple stacked layers. The thickness can range from 0.5 mm to over 2 mm, depending on the number of layers and the specific design requirements. Thicker substrates provide more space for routing and power distribution but must be carefully designed to manage thermal expansion and mechanical stress.
Aspect ratios, defined as the ratio of the substrate’s thickness to its smallest lateral dimension, are carefully controlled to ensure mechanical stability and manufacturability. Higher aspect ratios can lead to warping and mechanical failures, so designers aim to balance layer count with overall thickness to maintain reliability.
The Manufacturing Process of Ultra-Multilayer BGA Substrates
The manufacturing process of ultra-multilayer BGA substrates is complex and requires high precision to ensure the integrity and functionality of the final product. The process involves several stages:
Material Preparation:The process begins with the preparation of the base materials, including laminates, copper foils, and dielectric layers. These materials are carefully selected and inspected for quality and consistency.
Layer Stacking:The multiple layers of the substrate are stacked in a specific order, with dielectric layers separating the copper circuitry layers. This stack-up is designed to meet the electrical and thermal requirements of the final product.
Lamination:The stacked layers are laminated together under high pressure and temperature, bonding them into a single cohesive structure. This process ensures that the layers are securely attached and the dielectric material fills any gaps between the copper layers.
Drilling and Plating:Holes (vias) are drilled through the substrate to connect the various layers electrically. These holes are then plated with copper to create conductive pathways between the layers. Advanced techniques such as laser drilling and microvia formation are often used for high-density designs.
Circuit Patterning:The copper layers are patterned using photolithography and etching processes to form the intricate circuitry. This involves applying a photosensitive resist, exposing it to a pattern, developing the pattern, and etching away unwanted copper.
Solder Mask Application:A solder mask is applied to protect the circuitry from oxidation and short circuits. This mask is typically an epoxy-based polymer that is applied, exposed to a pattern, and cured.
Surface Finishing:Various surface finishes, such as ENIG (Electroless Nickel Immersion Gold) or HASL (Hot Air Solder Leveling), are applied to the exposed copper pads to ensure good solderability and corrosion resistance.
Testing and Inspection:The finished substrates undergo rigorous testing and inspection to ensure they meet electrical, thermal, and mechanical specifications. This includes electrical testing for continuity and isolation, X-ray inspection for internal defects, and mechanical tests for strength and durability.
Applications of Ultra-Multilayer BGA Substrates
Ultra-multilayer BGA substrates are used in a wide range of high-performance applications where space efficiency and reliability are paramount. These include:
Consumer Electronics:Smartphones, tablets, and laptops utilize these substrates to achieve compact designs with powerful processing capabilities. The integration of multiple layers allows for advanced features such as high-resolution displays, fast processors, and extended battery life.
Telecommunications:Network infrastructure equipment, such as servers, routers, and switches, relies on ultra-multilayer BGA substrates for high-speed data processing and transmission. These substrates support the dense circuitry and high bandwidths required for modern communication networks.
Automotive Electronics:Advanced driver-assistance systems (ADAS), infotainment systems, and electric vehicle power management systems use these substrates to handle the complex electronics involved. The ability to manage high temperatures and provide reliable performance under harsh conditions is crucial for automotive applications.
Medical Devices:Medical imaging equipment, diagnostic tools, and portable medical devices benefit from the miniaturization and reliability of ultra-multilayer BGA substrates. These substrates enable the integration of sophisticated electronics into compact and portable devices, enhancing patient care and diagnostic accuracy.
Aerospace and Defense:The aerospace and defense sectors require highly reliable and durable electronics for applications such as satellite communications, radar systems, and avionics. Ultra-multilayer BGA substrates provide the necessary performance and robustness for these demanding environments.
What are the Advantages of Ultra-Multilayer BGA Substrates?
The use of ultra-multilayer BGA substrates offers numerous advantages:
High Density and Miniaturization:The ability to stack multiple layers allows for more complex circuitry within a smaller footprint, enabling the miniaturization of electronic devices without compromising functionality.
Enhanced Thermal Management:The multiple layers provide better thermal dissipation paths, which is critical for high-power applications. Advanced thermal via structures and heat spreading techniques help manage heat effectively.
Improved Electrical Performance:The precise control of layer stack-up and use of high-quality materials ensure excellent signal integrity and reduced electromagnetic interference. This is essential for high-speed and high-frequency applications.
Mechanical Strength and Reliability:The robust construction of these substrates ensures they can withstand the stresses of manufacturing and operation, including thermal cycling and mechanical vibrations. This leads to longer device lifespans and improved reliability.
Versatility in Design:The flexibility in layer configuration and material selection allows designers to tailor the substrates to specific application requirements, whether for consumer electronics, telecommunications, automotive, medical, or aerospace applications.
FAQ
What are the key challenges in designing ultra-multilayer BGA substrates?
Designing ultra-multilayer BGA substrates involves addressing challenges such as managing thermal dissipation, ensuring signal integrity, and maintaining mechanical stability. Advanced simulation tools and careful material selection are crucial in overcoming these challenges.
How do ultra-multilayer BGA substrates enhance device performance?
These substrates enhance device performance by enabling high-density circuitry within a compact space, providing better thermal management, and ensuring reliable electrical connections. This allows for faster processing speeds, improved signal quality, and greater overall device reliability.
What industries benefit the most from ultra-multilayer BGA substrates?
Industries that benefit the most include consumer electronics, telecommunications, automotive, medical devices, and aerospace. These substrates support advanced features and high performance in applications ranging from smartphones to satellite communications.
What future trends can be expected in ultra-multilayer BGA substrate technology?
Future trends may include further miniaturization of substrates, integration of new materials with higher thermal and electrical performance, and the development of advanced manufacturing techniques to support even more complex and high-density designs