The Ultra-Multilayer FC-BGA Substrates Manufacturer specializes in crafting intricate circuitry for cutting-edge electronics. With unparalleled precision, they engineer substrates that defy complexity, enabling seamless integration of components. Their advanced processes ensure optimal performance, reliability, and efficiency in every substrate produced. Through innovative techniques and state-of-the-art facilities, they meet the demands of diverse industries, from telecommunications to aerospace. With a commitment to quality and innovation, this manufacturer stands at the forefront of technological advancement, driving progress and shaping the future of electronic devices worldwide.
As the backbone of the electronics industry, PCBs play a key role in modern technology. Among the many PCB types, Ultra-Multilayer FC-BGA substrate stands out for its unique design and multi-layer structure. This highly complex PCB not only features multiple layers of stacked insulating materials and conductive layers, but also uses finely arranged solder balls to achieve high-density component connections, providing excellent electrical performance and stability for high-performance electronic devices. The emergence of Ultra-Multilayer FC-BGA substrate has brought new solutions to the electronics industry and will play an increasingly important role in future technology development.
What are Ultra-Multilayer FC-BGA Substrates?
Ultra-Multilayer FC-BGA substrate (Ultra-Multilayer Fine-pitch Ball Grid Array Substrates) is a highly complex printed circuit board (PCB) type that has attracted much attention in the modern electronics industry. Its unique feature is the use of a multi-layer structure and fine-pitch ball grid array (FC-BGA), which is designed to achieve high-density wiring and large-scale integrated circuit connections while providing excellent electrical performance and stability. sex.
First of all, the Ultra-Multilayer FC-BGA substrate stands out for its multi-layer structure. Compared with traditional single-layer or double-layer PCBs, Ultra-Multilayer FC-BGA substrates have multiple layers of stacked insulating materials and conductive layers, providing greater space and connectivity for complex circuits. This multi-layer structure allows more circuit functions and component arrangements to be implemented in a limited space, thereby meeting the needs of modern electronic equipment for high integration and functional density.
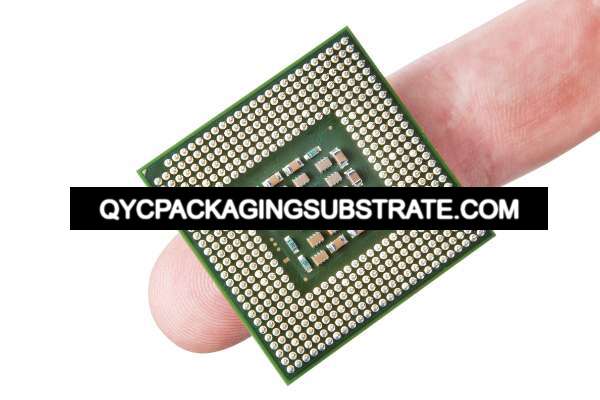
Ultra-Multilayer FC-BGA Substrates Manufacturer
Secondly, the solder ball array (FC-BGA) is another major feature of the Ultra-Multilayer FC-BGA substrate. Solder ball array is a connection technology that arranges solder balls at a small pitch and is used to connect to device pins. Through finely arranged solder balls, Ultra-Multilayer FC-BGA substrate achieves high-density component connection, which not only improves the efficiency of circuit wiring, but also allows the size of the entire PCB to be smaller, thereby achieving more functions in a limited space integration.
Taken together, the Ultra-Multilayer FC-BGA substrate is designed to overcome the limitations of traditional PCBs in high-density wiring and large-scale integrated circuit connections, providing a new solution for the design and manufacturing of modern electronic equipment. Its multi-layer structure and solder ball array technology make circuit design more flexible and performance more stable. It is suitable for various application scenarios, including communication equipment, computers and servers, industrial control, medical equipment, aerospace and other fields. With the continuous development and advancement of technology, it is believed that Ultra-Multilayer FC-BGA substrate will continue to play an important role in the electronics industry and provide strong support for future technological innovation.
Ultra-Multilayer FC-BGA Substrates design Reference Guide.
Ultra-Multilayer FC-BGA substrate is an important part of today’s electronic equipment design. Its complexity and high performance place strict requirements on designers. This design reference guide is designed to help engineers better understand and apply Ultra-Multilayer FC-BGA substrate to achieve excellent circuit design and performance.
Design planning
Before starting the design, clarify the overall requirements and functionality of the circuit. Consider factors such as signal transmission speed, power consumption, thermal management, etc., and fully communicate with the customer or team.
Schematic design
Use CAD software to draw the schematic diagram of the circuit. Make sure all components are connected correctly and tightly to avoid signal interference and power supply noise.
Component selection
Select appropriate components according to design requirements, including chips, capacitors, resistors, etc. Consider factors such as size, operating temperature range, electrical characteristics, and more.
Stacked structure design
Determine the hierarchical structure and interlayer connection method of the Ultra-Multilayer FC-BGA substrate. Consider factors such as signal integrity, thermal management, and EMI/EMC, and use appropriate interlayer copper layout and power distribution.
Wiring plan
Use micro-wiring technology to rationally arrange signal lines, power lines and ground wires. Differential signal transmission and impedance matching technology are used to ensure stable transmission of high-speed signals.
Solder ball design
Precisely determine the layout and arrangement of solder balls to ensure accurate alignment and connection to device pins. Consider the welding process and reliability requirements, and select appropriate welding materials and process parameters.
Test and verify
After the design is completed, electrical testing and reliability verification are performed. Use simulation tools and real test equipment to evaluate circuit performance and stability.
Through the above design reference guide, designers can design Ultra-Multilayer FC-BGA substrates more systematically to ensure that customer needs are met and excellent circuit performance is achieved. At the same time, continuing to learn and understand the latest PCB technology developments, continuously optimizing the design process and improving professional standards will bring more innovation and progress to the design and manufacturing of electronic equipment in the future.
What material is used in Ultra-Multilayer FC-BGA Substrates?
The manufacturing of Ultra-Multilayer FC-BGA substrate requires the selection of a series of high-quality materials to ensure its reliability and stability in high-performance electronic equipment. These materials not only need to have good electrical properties, but also need to meet the requirements of high-density wiring and fine structures. The following are the key materials commonly used in Ultra-Multilayer FC-BGA substrates:
Substrate material
The substrate of Ultra-Multilayer FC-BGA substrate is usually made of high-temperature and high-performance materials to meet the thermal stability and mechanical strength requirements of complex circuits. Common substrate materials include FR4 (fiberglass reinforced epoxy) and polyimide (PI), etc., which have good heat resistance and insulation properties.
Conductive layer material
The conductive layer is the core part of the Ultra-Multilayer FC-BGA substrate, and high-purity copper foil is usually used as the conductive layer material. Copper foil has excellent electrical conductivity and processability, and can meet the requirements of high-density wiring and fine structures.
Solder ball material
Solder balls are a key part of connecting device pins and PCB. High-quality soldering materials are usually used, such as tin-lead alloy, tin-copper alloy or lead-free solder. These materials have good welding performance and reliability, ensuring the stability and durability of the connection.
Solder mask material
The solder mask is used to cover the PCB surface, protect the conductive layer and solder joints, and prevent oxidation and short circuits. Common solder mask materials include epoxy and polyurethane, which have good adhesion and chemical resistance.
Silk screen printing materials
The silk screen layer is used to mark the location and logo of components on the PCB. Wear-resistant and corrosion-resistant ink or adhesive is usually used as the screen printing material to ensure clear and durable markings.
To sum up, the material selection of Ultra-Multilayer FC-BGA substrate is crucial, and factors such as electrical performance, thermal performance, mechanical strength and cost need to be comprehensively considered to ensure the quality and reliability of the final product.
What size are Ultra-Multilayer FC-BGA Substrates?
Ultra-Multilayer FC-BGA substrate sizes vary depending on application and design needs, allowing a certain degree of flexibility and customizability. Generally speaking, the size of this substrate is usually affected by the following factors:
First, the size of the Ultra-Multilayer FC-BGA substrate is limited by the required wiring and component density. In the case of high-density wiring and large-scale integrated circuits, larger substrate sizes are usually required to accommodate more circuits and components. Therefore, in high-performance applications, the size of the Ultra-Multilayer FC-BGA substrate may be larger.
Secondly, the size of Ultra-Multilayer FC-BGA substrate is also affected by the manufacturing process and cost. Larger substrate sizes may require more materials and processing steps, increasing manufacturing costs. Therefore, in practical applications, designers usually find a balance between performance and cost to choose the appropriate size.
In addition, the size of Ultra-Multilayer FC-BGA substrates is limited by available materials and manufacturing equipment. Certain specialty materials may have size limitations, and the processing capabilities of manufacturing equipment may also impose limitations on substrate size.
Overall, the size of Ultra-Multilayer FC-BGA substrates typically ranges from a few millimeters to tens of centimeters, depending on design requirements, performance needs and manufacturing technology limitations. In practical applications, designers need to consider various factors and select the appropriate size to achieve optimal performance and cost-effectiveness.
The Manufacturer Process of Ultra-Multilayer FC-BGA Substrates.
The process of manufacturing Ultra-Multilayer FC-BGA substrate is a complex and precise project that requires a series of rigorous steps to ensure its quality and performance. The following is a detailed analysis of the process:
First, design planning is the starting point of the manufacturing process. Based on the customer’s application needs and performance requirements, the engineering team performs circuit design and layout planning. At this stage, they take into account aspects such as circuit function, size, electrical characteristics, and thermal management to ensure that the final design meets the expected requirements.
Next is schematic design. Engineers use CAD software to draw circuit schematics and perform necessary simulation and verification. This step is key to ensuring the accuracy and reliability of the circuit design. Through simulation and verification, potential problems can be discovered and solved, laying a solid foundation for subsequent manufacturing work.
Next comes the stacking structure design, where the engineering team determines the stacking sequence and inter-layer connection method of the multi-layer PCB. At this stage, they consider factors such as signal integrity, thermal management, and overall structural stability to ensure the design is reasonable and feasible.
Microwiring is one of the key links in the manufacturing process. Engineers use high-precision wiring technology to connect circuits and components between various layers. They need to consider issues such as wiring density, trace length, circuit paths, and impedance matching to ensure the stability and reliability of signal transmission.
Next comes the solder ball production, where engineers precisely arrange the solder balls to ensure accurate alignment and connection with the device pins. The production quality of solder balls directly affects the quality and reliability of the connection between PCB and other components, so highly precise operations and strict quality control are required.
Finally, there is the testing and verification phase, where engineers conduct electrical testing and reliability verification to ensure that the PCB meets design specifications and performance requirements. They use a variety of testing equipment and tools to conduct comprehensive inspection and evaluation of PCBs to ensure that their quality and performance meet expected levels.
Through the above carefully designed and strictly executed manufacturing process, Ultra-Multilayer FC-BGA substrates can be produced efficiently and reliably, providing stable and reliable basic support for various high-performance electronic devices.
The Application area of Ultra-Multilayer FC-BGA Substrates.
As a highly complex and advanced PCB technology, Ultra-Multilayer FC-BGA substrate has a wide range of applications, covering all types of high-performance electronic equipment and systems. The following are the applications of Ultra-Multilayer FC-BGA substrates in different fields:
Communication device
In the field of communications, Ultra-Multilayer FC-BGA substrate is widely used in various base station equipment and optical fiber communication equipment. Based on its high-density wiring and excellent signal transmission performance, it can support complex communication protocols and data transmission requirements, providing reliable support for the stable operation of modern communication networks.
Computers and servers
In the field of computing, Ultra-Multilayer FC-BGA substrates are commonly used in high-performance computers and server systems. Due to its high degree of integration and excellent electrical performance, it can support high-speed data processing and large-scale storage, meeting application scenarios that require extremely high computing performance and data throughput.
Industrial control
In the field of industrial automation, Ultra-Multilayer FC-BGA substrates are widely used in various automation equipment and robotic systems. Its stable electrical performance and high reliability enable it to adapt to various harsh conditions in industrial environments, providing key support for the intelligence and automation of industrial control systems.
Medical equipment
In the medical field, Ultra-Multilayer FC-BGA substrates are commonly used in high-end medical equipment such as various medical imaging equipment and laser therapy equipment. Its high integration and high reliability can support the high requirements of medical equipment for data processing and image transmission, and provide accurate and reliable technical support for medical diagnosis and treatment.
Aerospace
In the aerospace field, Ultra-Multilayer FC-BGA substrates are widely used in avionics systems and satellite communication equipment. Its lightweight design and excellent vibration resistance enable it to adapt to extreme conditions in the aerospace environment, providing important support for the development and application of aerospace technology.
Overall, the wide application of Ultra-Multilayer FC-BGA substrates plays a key role in various fields, promoting the continuous innovation and development of high-performance electronic devices and systems. With the continuous advancement of technology and the continuous expansion of application scenarios, it will continue to play an important role and bring more possibilities and opportunities to various fields.
What are the advantages of Ultra-Multilayer FC-BGA Substrates?
Ultra-Multilayer FC-BGA substrate has attracted much attention in the electronics industry for its excellent characteristics. It has many advantages, including but not limited to the following aspects:
Highly integrated
Ultra-Multilayer FC-BGA substrates are designed to achieve high circuit integration and functional density. Through multi-layer stacking of insulating materials and conductive layers, more electronic components and functional modules can be accommodated in a limited space, thereby achieving compact layout and high integration of complex circuits.
Excellent signal transmission performance
This substrate provides stable signal transmission and anti-interference capabilities through precise wiring and design. The application of fine lines and fine apertures makes signal transmission more reliable, reducing the possibility of signal distortion and crosstalk, thus ensuring the stability and performance of the circuit.
High reliability
Ultra-Multilayer FC-BGA substrate has stable electrical performance and mechanical strength, and is suitable for various harsh environments. Its material selection and manufacturing process have been carefully designed and verified to maintain stable operation under harsh conditions such as high temperature, high humidity, and vibration, ensuring that the equipment works stably for a long time.
High flexibility
This kind of substrate has high flexibility and can be customized and designed according to different application needs to meet customer-specific requirements. Whether it is layout design, layer stacking or solder ball arrangement, it can be customized according to customer needs to provide the most suitable solution.
High productivity
Ultra-Multilayer FC-BGA substrate utilizes advanced manufacturing technology and processes to achieve high-efficiency production and cost control. The use of automated production lines and precision processing equipment has greatly improved production efficiency and reduced manufacturing costs, giving the substrate a competitive advantage in the market.
In short, Ultra-Multilayer FC-BGA substrate has an irreplaceable position in the design and manufacturing of high-performance electronic equipment. Its excellent performance and flexible design solutions will bring more possibilities to the development of future electronic technology.
FAQ
How many layers does the Ultra-Multilayer FC-BGA substrate have?
The number of layers of Ultra-Multilayer FC-BGA substrate can be determined according to specific design requirements, and can usually reach dozens of layers or even more. This depends on factors such as circuit complexity, signal transmission requirements, and space constraints. Multi-layer designs can provide more wiring space and signal layers to meet the dense wiring and signal transmission needs of high-performance electronic devices.
How long is the manufacturing cycle of Ultra-Multilayer FC-BGA substrate?
The manufacturing cycle of Ultra-Multilayer FC-BGA substrates depends on multiple factors, including design complexity, number of layers, quantity, and manufacturer’s production capabilities. Generally speaking, manufacturing lead time can range from a few days to a few weeks. Complex designs and customization needs may take longer, while simple designs may be completed in a shorter time.
How to choose a suitable Ultra-Multilayer FC-BGA substrate material?
Selecting the appropriate Ultra-Multilayer FC-BGA substrate material is a key factor in ensuring circuit performance and reliability. Common substrate materials include FR4, high-frequency materials (such as PTFE), aluminum substrates, etc. Factors such as the operating frequency of the circuit, thermal management needs, mechanical strength and cost need to be considered when selecting materials to ensure that design requirements are met.
What are the characteristics of the solder ball arrangement density of Ultra-Multilayer FC-BGA substrate?
The solder ball arrangement density of Ultra-Multilayer FC-BGA substrate is usually very high, and the spacing between solder balls can reach the micron level. This high-density arrangement enables more pin connections and provides more wiring space, making it suitable for electronic devices that require a high degree of integration and high performance.
How to ensure the reliability and stability of Ultra-Multilayer FC-BGA substrate?
Ensuring the reliability and stability of Ultra-Multilayer FC-BGA substrate requires strict control of the entire process from design to manufacturing. This includes simulation and verification in the design phase, material selection, manufacturing process control, quality inspection and testing, etc. By strictly implementing design specifications, using high-quality materials, following standard manufacturing processes and conducting comprehensive testing, the stability and reliability of Ultra-Multilayer FC-BGA substrates can be ensured to meet various application needs.